Nickel alloy powder for 3d printing
All You Need To Know About Nickel alloy powder for 3d printing
Product Category
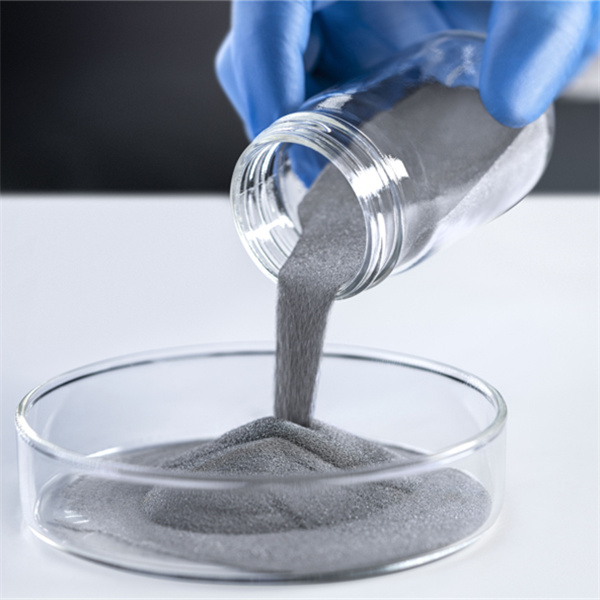
Overview of Nickel Alloy Powder for 3D Printing
3D printing, also known as additive manufacturing, has revolutionized product design and manufacturing across industries like aerospace, automotive, medical, and consumer goods. Unlike traditional subtractive manufacturing which removes material, 3D printing builds up components layer-by-layer based on a digital 3D model.
One of the most popular technologies for metals 3D printing is powder bed fusion, where a thermal energy source selectively fuses regions of a powder bed. The unmatched design freedom, buy-to-fly ratio, and economic production of complex parts has driven huge adoption of powder bed technologies like selective laser melting (SLM), direct metal laser sintering (DMLS), and electron beam melting (EBM).
Nickel alloys are a versatile class of materials with properties like high strength, corrosion resistance, and heat resistance that make them ideal candidates for 3D printing. The most common nickel alloy powders used in powder bed fusion include Inconel superalloys, stainless steels, Hastelloys, Nimonics, Kovar, Invar, Monel, nickel-titanium alloys, and nickel-based superalloys.
Composition of Nickel Alloy Powders
Nickel alloys derive their properties from their elemental composition and microstructure. The nickel content varies from 2% to 99% for different alloys. Nickel imparts properties like corrosion resistance, oxidation resistance, and high-temperature strength. The alloying elements are added to enhance specific characteristics depending on the application.
Nickel Alloy Powder Compositions
Alloy Family | Nickel Content | Alloying Elements |
---|---|---|
Inconel | 30-80% | Cr, Mo, Nb, Ta, Al, Ti, Fe |
Stainless steel | 2-20% | Cr, Mo, Mn, Si, C |
Hastelloy | 35-60% | Mo, Cr, W, Fe, Co |
Nimonic | Over 50% | Cr, Ti, Al, Mo |
Kovar | 17% | Fe, Co, Mn, Si |
Invar | 36% | Fe |
Monel | Over 67% | Cu, Fe, Mn, Si, C |
Nickel-titanium | 55% Ni, 45% Ti | – |
Nickel superalloys | Over 50% | Cr, Co, Mo, W, Ta, Al, Ti, Nb |
The chromium content in stainless steels and nickel superalloys improves oxidation and corrosion resistance. Molybdenum, tungsten, and tantalum enhance creep strength and high temperature mechanical properties. Iron in alloys like Kovar and Invar controls thermal expansion behavior. Aluminum, titanium, and niobium are added for precipitation hardening. Manganese improves hot ductility whereas carbon enhances strength and hardness. Silicon benefits fluidity and weldability.
Understanding how alloying influences microstructure formation and properties aids in selecting the optimal material for an application. Proper characterization and qualification of powder composition and quality is critical before printing mission-critical components.
Properties of Nickel Alloy Powders
The unique properties of nickel alloys printed from optimized powders enable their use across diverse applications and extreme environments. The table below summarizes the general properties for common alloy families.
Properties of Nickel Alloy Powder Families
Alloy Family | Density | Melting Point | Tensile Strength | Thermal Conductivity | Thermal Expansion | Oxidation Resistance | Corrosion Resistance |
---|---|---|---|---|---|---|---|
Inconel | 8.2-8.4 g/cc | 1300-1450°C | 750-1380 MPa | 11-16 W/mK | 12-16 μm/m°C | Excellent | Excellent |
Stainless steel | 7.5-8.1 g/cc | 1375-1500°C | 450-1100 MPa | 15-30 W/mK | 10-18 μm/m°C | Good | Good-Excellent |
Hastelloy | 8.1-9.2 g/cc | 1260-1350°C | 550-1000 MPa | 6-22 W/mK | 12-16 μm/m°C | Good-Excellent | Excellent |
Nimonic | 8.1-8.7 g/cc | 1260-1400°C | 500-1200 MPa | 10-30 W/mK | 12-17 μm/m°C | Good | Good |
Kovar | 8.2 g/cc | 1450°C | 550 MPa | 17 W/mK | 5.9 μm/m°C | Poor | Poor |
Invar | 8 g/cc | 1427°C | 200-450 MPa | 10.5 W/mK | 1.2 μm/m°C | Fair | Fair |
Monel | 8.8 g/cc | 1350-1370°C | 550-950 MPa | 21-48 W/mK | 13-17 μm/m°C | Fair | Excellent |
Nickel-titanium | 6.4 g/cc | 1240-1310°C | 600-900 MPa | 8-18 W/mK | 11 μm/m°C | Fair | Excellent |
Nickel superalloys | 8-9 g/cc | 1260-1350°C | 750-1400 MPa | 11-61 W/mK | 12.5-17 μm/m°C | Good-Excellent | Fair-Good |
The high melting point of nickel alloys prevents part distortion or deformation during processing. Strength levels over a wide temperature range enable load-bearing structural applications. Controlled thermal expansion behavior allows precision components with tight tolerances. The excellent corrosion and oxidation resistance facilitates usage in harsh environments like marine, chemical, and oil and gas.
By tailoring the powder composition and process parameters, material properties can be optimized for the design requirements. However, the anisotropic nature of additive manufacturing can result in directionally dependent properties. Proper design and quality assurance is key to achieve desired performance.
Applications of Nickel Alloy Powders
The versatility of nickel alloys makes them suitable for diverse applications across aerospace, defense, automotive, marine, oil and gas, chemical processing, power generation, medical, tooling, and other general engineering areas.
Industry Applications of Nickel Alloy Powder Families
Alloy Family | Industry Applications |
---|---|
Inconel | Aerospace, defense, automotive, chemical processing, oil and gas, power generation, rocketry, missiles, nuclear |
Stainless steel | Aerospace, defense, automotive, medicine, marine, architecture, chemical, food processing, tooling, molds |
Hastelloy | Aerospace, defense, chemical processing, pollution control, power generation, oil and gas |
Nimonic | Aerospace, defense, power generation, chemical processing, tooling |
Kovar | Electronics, semiconductors, integrated circuits, packaging |
Invar | Electronics, optics, precision instruments, aerospace |
Monel | Marine, oil and gas, chemical processing, power generation, pulp and paper |
Nickel-titanium | Medical devices, actuators, sensors, aerospace, oil and gas |
Nickel superalloys | Aerospace, defense, power generation, oil and gas, automotive, tooling |
Some examples of nickel alloy parts produced by 3D printing include:
- Aerospace: Turbine blades, nozzles, combustors, valves, brackets, thermofluid components
- Automotive: Turbocharger rotors, manifolds, valves, drivetrain parts
- Medical: Implants, prosthetics, surgical instruments, patient-specific devices
- Oil and gas: Downhole tools, valves, wellhead components, pipe fittings
- Tooling: Injection molds, extrusion dies, jigs and fixtures, press tools
- General: Heat exchangers, fluid handling parts, fasteners, housings, enclosures
The excellent material properties, complex geometries, shorter lead times, reduced costs, and design flexibility enabled by 3D printing nickel alloys make them a very attractive option across many critical applications.
Nickel Alloy Powder Specifications
Nickel alloy powders are commercially available in various size distributions, morphologies, and quality levels tailored to 3D printing requirements. Common specifications are given below:
Typical Nickel Alloy Powder Specifications
Property | Typical Values |
---|---|
Alloy composition | Custom alloys, grade per ASTM/ASME |
Particle shape | Spherical, near-spherical |
Particle size | 10-45 microns |
Particle size distribution | D10: 15-25 μm, D50: 25-35 μm, D90: 35-45 μm |
Apparent density | 2.5-5.5 g/cc |
Tap density | 4-8 g/cc |
Flowability | Excellent per Hall flowmeter |
Residual oxygen | 100-400 ppm |
Residual nitrogen | 50-150 ppm |
Residual carbon | 100-300 ppm |
Spherical morphology and narrow particle size distribution with D10, D50 and D90 values in ideal ranges for the specific print process help achieve good density and mechanical properties. High flowability prevents powder agglomeration and spreadability issues during recoating. Low residual oxygen, nitrogen and carbon minimize contamination and porosity.
Powder quality, size parameters and other characteristics significantly influence final part properties and must align with printer and application requirements. Most suppliers provide custom alloy compositions and particle optimization to meet user specifications.
Nickel Alloy Powder 3D Printing Methods
The most common additive manufacturing methods used to process nickel alloy powders include:
Nickel Alloy Powder Print Processes
Method | Description |
---|---|
Selective Laser Melting (SLM) | Powder bed fused by focused laser beam |
Direct Metal Laser Sintering (DMLS) | Similar to SLM but lower power laser |
Electron Beam Melting (EBM) | Powder bed fused by electron beam under vacuum |
Laser Metal Deposition (LMD) | Powder injected into molten pool created by laser |
Directed Energy Deposition (DED) | Similar to LMD with powder or wire feed |
Binder Jetting | Liquid bonding agent selectively printed on powder bed |
SLM and DMLS use a high power density laser to fully melt the metal powder into dense parts layerwise. EBM uses an electron beam as the power source to build parts under vacuum. Wire-fed LMD melts the incoming metal wire using a focused laser. Binder jetting prints a liquid binder to form the part followed by sintering.
The specific technique chosen depends on factors like part size, geometry complexity, surface finish, feature resolution, production rate, and cost. Each process requires optimization of printer settings and parameters tailored to the powder alloy composition.
Nickel Alloy Powder Process Parameters
Critical printer parameters for nickel alloys that require optimization for density, strength, precision, and surface finish include:
Typical SLM/DMLS Process Parameters
Parameter | Typical Range |
---|---|
Layer thickness | 20-60 μm |
Laser power | 100-400 W |
Scan speed | 400-1200 mm/s |
Hatch spacing | 80-200 μm |
Beam size | 50-200 μm |
Scanning strategy | Chess, stripe, contour |
Support structure | Regular, fragmented, hybrid |
Typical EBM Process Parameters
Parameter | Typical Range |
---|---|
Layer thickness | 50-200 μm |
Electron beam power | 3-15 kW |
Speed function | 20-200 mm/s |
Line offset | 0.1-0.3 mm |
Focus offset | 15-35 mA |
Scanning strategy | Uni-directional, bi-directional |
Support structure | Regular, heavy |
Lower layer thickness and beam size paired with higher scan speeds increase resolution, accuracy, and surface finish. Chess or strip scanning patterns are commonly used. Perimeter contours improve edge quality. Optimized support structures prevent deformation but are easier to remove. Preheating and powder recycling can aid density and material quality.
Advantages of 3D Printing Nickel Alloys
Additive manufacturing using optimized nickel alloy powders offers many benefits versus traditional manufacturing:
- Design freedom: Complex geometries not possible by machining
- Weight reduction: Lighter components by topology optimization
- Part consolidation: Reduced assembly by printed complex shapes
- Customization: Patient-matched medical devices, tooling
- Reduced waste: Only required volume of material used
- Shorter lead time: Weeks versus months for production tooling
- Process flexibility: Easy design iterations and optimization
- Performance benefits: Anisotropic strengths, embedded features
- Cost reduction: Eliminate tooling costs, low volume production
- Buy-to-fly ratio: Print only final part versus machining from block
3D printing expands the design envelope and enables novel nickel alloy parts not feasible or economical with conventional techniques. It is revolutionizing production across aerospace, medical, automotive, and other industries.
Nickel Alloy Powder Suppliers
Most major metal powder manufacturers now offer a range of nickel alloy powders optimized for additive manufacturing. Some leading suppliers include:
Key Nickel Alloy Powder Suppliers
Supplier | Key Alloy Grades |
---|---|
Met3DP | Inconel 625, 718, Hastelloy X, stainless steels |
Sandvik | Osprey stainless steels, superalloys, titanium alloys |
Praxair | Inconel 718, 625, Hastelloy X, stainless steels |
AP&C | Inconel 718, 625, stainless steels |
LPW Technology | Inconel 718, stainless steels, nickel superalloys |
SLM Solutions | Stainless steel 316L, 17-4PH, nickel superalloys |
GE Additive | Stainless steel 316L, Inconel 718, 625, Hastelloy |
Suppliers offer various size distributions, excellent powder flowability, low oxygen and moisture content, lot traceability, and custom alloys tailored to process and application requirements. Most provide specialized characterization to ensure consistent high quality powder.
Nickel Alloy Powder Cost
The average cost for common nickel alloy powders is summarized below:
Nickel Alloy Powder Costs
Material | Cost per kg |
---|---|
Inconel 718 | $75-150 |
Inconel 625 | $60-120 |
Stainless steel 316L | $35-70 |
Stainless steel 17-4PH | $45-90 |
Hastelloy X | $85-170 |
Nickel superalloys | $90-200 |
High performance alloys like Inconel 718 and Hastelloy X carry a premium while stainless steels tend to be the lowest cost option. However, material cost is only one component of total part cost. Value-add from design flexibility, performance benefits, and lead time reduction often offset higher powder prices for low volume production.
Buying powder in bulk quantities can reduce costs. Many suppliers also offer powder reuse and recycling services. Overall, the buyer must evaluate total cost including labor, post-processing, material utilization, mechanical properties, and other factors when selecting an appropriate nickel alloy powder.
Wholesale Price: $20/Kg-$200/Kg
Showing 1–15 of 17 results
-
GH3536 Alloy Powder
-
K465 Alloy Powder
-
GH3230 Powder
-
GH5188 Powder
-
GH3625 powder(Inconel 625 powder)
-
GH4169(Inconel 718)
-
GH3230 Powder
-
GH 3625 Powder
-
High temperature alloy series
-
GH4169 Powder
-
Nickel-based K403 Powder
-
Best IN939 Powder for 3D Printing in 2023
-
Best IN738 powder for 3D printing in 2023
-
Best in718 powder for 3D printing
-
Best Hastelloy X Powder丨High temperature alloy Powder for 3D Printing
FAQ About 3D Printing Metal Powder
How can I contact Metal3DP customer service?
We provide 24/7 customer support. You can find our contact details on the Contact Us page, including phone, email, and online chat.
What metal powder materials does Metal3DP offer?
We offer various high-quality metal powders including stainless steel, high-temperature alloys, suitable for processes like laser and electron beam powder bed fusion.
How does Metal3DP ensure the quality of 3D printing metal powder?
With extensive metal additive manufacturing expertise, we employ advanced processes and stringent quality control to ensure the mechanical properties and surface quality of parts.
In which industries are Metal3DP's 3D printing devices applied?
Our devices have a wide range of applications in industries like aerospace, medical, automotive, and more, providing solutions for high-performance metal components in manufacturing.
Does Metal3DP offer custom alloy options?
Yes, we provide custom alloy services to meet specific material requirements from clients.
What are the advantages of Metal3DP's SEBM systems?
Our SEBM systems excel in producing complex metal parts with exceptional mechanical properties. Key features include industry-leading build volume, precision, and reliability.
Can I find application cases on the Metal3DP website?
Yes, our website showcases a wide range of application cases demonstrating successful implementations of Metal3DP technology across various industries.
How can I start collaborating with Metal3DP?
Get in touch with us, and our team will provide you with tailored solutions and collaboration plans based on your needs.
What is the turnaround time for Metal3DP's custom services?
The turnaround time for custom services varies depending on project complexity. We will provide accurate delivery times based on your requirements.
What 3D printing technologies does Metal3DP offer?
We specialize in Selective Laser Sintering (SLS), Selective Laser Melting (SLM), and Selective Electron Beam Melting (SEBM) among other 3D printing technologies.
SEND US
Ask For Other Question?
If you cannot find the answer to your question in our FAQ, you can always leave us a message. We will answer to you shortly.
WAIT FOR US
Next step
01. We will prepare a proposal
Required scope, timeline and APR. Price will be included if you provide us with detail information about a project.
02. Discuss it together
Let’s get acquainted and discuss all the possible variants and options
03. Let’s start building
When the contract is signed, and all goals are set, we can start the first sprint.