Best in718 powder for 3D printing
IN718 powder is a nickel-based superalloy powder widely used in additive manufacturing processes such as powder bed fusion and direct energy deposition. It is composed primarily of nickel, with additions of chromium, iron, niobium, molybdenum, and other elements. The combination of these elements imparts exceptional mechanical strength, corrosion resistance, and high-temperature capabilities to the final printed parts.
Low MOQ
Provide low minimum order quantity to meet different needs.
OEM & ODM
Provide customized products and design services to meet unique customer needs.
Adequate Stock
Ensure fast order processing and provide reliable and efficient service.
Customer Satisfaction
Provide high quality products with customer satisfaction at the core.
share this product
Table of Contents
Overview of IN718 Powder
IN718 is a precipitation hardenable nickel-based superalloy powder widely used for additive manufacturing, owing to its good strength, corrosion resistance, weldability and processability. This article provides a detailed guide to IN718 powder.
Key aspects covered include composition, properties, AM print parameters, applications, specifications, suppliers, handling, inspection methods, comparisons to alternatives, pros and cons, and FAQs. Tables are used to present quantitative data in an easy-to-reference format.
Composition of IN718 Powder
The composition of IN718 is:
Element | Weight % | Purpose |
---|---|---|
Nickel | 50 – 55 | Principal matrix element |
Chromium | 17 – 21 | Oxidation resistance |
Iron | Balance | Solid solution strengthener |
Niobium | 4.75 – 5.5 | Precipitation hardening |
Molybdenum | 2.8 – 3.3 | Solid solution strengthening |
Titanium | 0.65 – 1.15 | Carbide former |
Aluminum | 0.2 – 0.8 | Precipitation hardening |
Carbon | 0.08 max | Carbide former |
Trace amounts of cobalt, boron, copper and magnesium are also added.
Properties of IN718 Powder
Key properties of IN718 include:
Property | Description |
---|---|
High strength | Tensile strength 1050 – 1350 MPa |
Phase stability | Retains properties after prolonged use up to 700°C |
Corrosion resistance | Resistant to aqueous corrosion and oxidation |
Weldability | Excellent weldability using matching filler material |
Fabricability | Easy to form and machine |
Creep resistance | High stress rupture strength at high temperatures |
The properties make IN718 suitable for the most demanding applications.
3D Printing Parameters for IN718 Powder
Typical parameters for printing IN718 powder include:
Parameter | Typical value | Purpose |
---|---|---|
Layer height | 20 – 50 μm | Balance speed and resolution |
Laser power | 195 – 350 W | Sufficient melting without evaporation |
Scan speed | 700 – 1300 mm/s | Density versus build rate |
Hatch spacing | 80 – 160 μm | Mechanical properties |
Support structure | Minimal | Easy removal |
Hot isostatic pressing | 1120°C, 100 MPa, 3h | Eliminate internal voids |
The parameters depend on factors like build geometry, temperature management and post-processing requirements.
Applications of 3D Printed IN718 Parts
IN718 parts made by AM are used in:
Industry | Components |
---|---|
Aerospace | Engine components like turbine blades, discs |
Power generation | Combustion cans, transition ducts |
Oil and gas | Downhole tools, valves, pumps |
Automotive | Turbocharger wheels, exhaust valves |
Medical | Orthopedic implants, surgical tools |
Benefits over wrought IN718 include complex geometries, reduced lead times and buy-to-fly ratios.
Specifications of IN718 Powder for AM
IN718 powder must meet the following specifications for 3D printing:
Parameter | Specification |
---|---|
Particle size range | 10 – 45 μm |
Particle shape | Spherical morphology |
Apparent density | Typically > 4 g/cc |
Tap density | > 6 g/cc |
Hall flow rate | > 23 sec for 50 g |
Purity | >99.9% |
Oxygen content | <100 ppm |
Custom size distributions and tightly controlled composition available.
Suppliers of IN718 Powder
Prominent suppliers include:
Supplier | Location |
---|---|
Praxair | USA |
Carpenter Powder Products | USA |
Sandvik Osprey | UK |
LPW Technology | UK |
Erasteel | France |
AP&C | Canada |
Prices range from $50/kg to $150/kg, influenced by quality considerations and order volumes.
Handling and Storage of IN718 Powder
As a reactive material, IN718 powder requires controlled handling:
- Store sealed containers in a cool, dry inert atmosphere
- Prevent exposure to moisture, air, or temperature extremes
- Use properly grounded equipment during transfer
- Avoid dust accumulation and control ignition sources
- Local exhaust ventilation recommended
- Follow applicable safety guidelines
Correct storage and handling prevents composition changes or hazards.
Inspection and Testing of IN718 Powder
IN718 powder batches are validated using:
Method | Parameters Tested |
---|---|
Sieve analysis | Particle size distribution |
SEM imaging | Particle morphology |
EDX | Chemistry and composition |
XRD | Phases present |
Pycnometry | Density |
Hall flow rate | Powder flowability |
Testing per ASTM standards ensures batch-to-batch quality consistency.
Comparing IN718 to Alternative Superalloy Powders
IN718 compares with other alloys as:
Alloy | Cost | Printability | Weldability | Strength |
---|---|---|---|---|
IN718 | Low | Good | Excellent | Medium |
IN625 | Medium | Excellent | Excellent | Low |
IN792 | High | Fair | Good | Excellent |
IN939 | Very High | Good | Limited | Excellent |
For balanced properties at lower cost, IN718 supersedes other Ni-based superalloys for many applications.
Pros and Cons of IN718 Powder for 3D Printing
Pros | Cons |
---|---|
Proven material credentials in AM | Lower high temperature strength than some alloys |
Excellent weldability and machinability | Susceptible to solidification cracking during printing |
Easily fabricated into complex shapes | Requires controlled atmosphere handling |
Cost advantage over exotic superalloys | Significant post-processing often needed |
Readily available from range of suppliers | Relatively low hardness after printing |
IN718 enables high performance additive manufacturing at a reasonable cost.
Frequently Asked Questions about IN718 Powder
Q: What particle size range works best for 3D printing IN718 alloy?
A: A range of 15-45 microns provides the optimum blend of flowability, high resolution, and high density parts. Finer powders below 10 microns can also be used.
Q: What post processing is typically required for IN718 AM components?
A: Hot isostatic pressing, heat treatment, and machining are commonly needed to eliminate voids, optimize properties, and achieve dimensional accuracy.
Q: Is IN718 easier to 3D print compared to other Ni superalloys?
A: Yes, the excellent weldability and lower susceptibility to cracking make IN718 one of the easier to process Ni-based superalloys by powder bed fusion techniques.
Q: What industries use IN718 alloy for metal 3D printing?
A: Aerospace, power generation, oil and gas, automotive, and medical sectors are major application areas for additively manufactured IN718 components.
Q: What material has properties closest to IN718 for AM?
A: IN625 alloy powder has comparable weldability and corrosion resistance to IN718 but lower strength. IN792 trades weldability for higher strength.
Q: Is hot isostatic pressing mandatory for IN718 3D printed parts?
A: HIP eliminates internal voids and improves fatigue resistance. It may not be required for non-critical applications.
Q: Does IN718 require support structures during 3D printing?
A: Minimal supports are recommended on overhangs and bridged sections to prevent deformation and facilitate easy removal post-printing.
Q: What defects can occur when printing with IN718 powder?
A: Potential defects are cracking, porosity, distortion, incomplete fusion, and surface roughness. Most can be prevented with optimized parameters.
Q: What hardness can be expected with IN718 AM components?
A: Hardness after printing is typically 30-35 HRC. Post-processing like aging can increase it to 40-50 HRC for higher wear resistance.
Q: What precision can be obtained with IN718 printed parts?
A: After post-processing, IN718 printed components can achieve dimensional tolerances and surface finishes comparable to CNC machined parts.
About Met3DP
Product Category
HOT SALE
CONTACT US
Any questions? Send us message now! We’ll serve your request with a whole team after receiving your message.
Related products
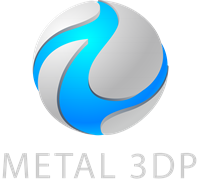
Leading provider of additive manufacturing solutions headquartered in Qingdao, China.
COMPANY
PRODUCT
cONTACT INFO
- Qingdao City, Shandong, China
- [email protected]
- [email protected]
- +86 19116340731