Nickel-based K403 Powder
K403 powder is a nickel-chromium-iron-molybdenum alloy powder. It offers excellent resistance to oxidation, corrosion and thermal fatigue cracking. K403 has good phase stability at high temperatures. K403 powder is designed for protective coatings, thermal spray, welding, brazing, and other high temperature applications.
Low MOQ
Provide low minimum order quantity to meet different needs.
OEM & ODM
Provide customized products and design services to meet unique customer needs.
Adequate Stock
Ensure fast order processing and provide reliable and efficient service.
Customer Satisfaction
Provide high quality products with customer satisfaction at the core.
share this product
Table of Contents
Overview of Nickel-based K403 Powder
K403 powder is a nickel-chromium-iron-molybdenum alloy powder. It offers excellent resistance to oxidation, corrosion and thermal fatigue cracking. K403 has good phase stability at high temperatures.
Key features of K403 powder include:
- Outstanding high temperature strength and creep resistance
- Resists oxidation and hot corrosion up to 1150°C
- Retains properties under cyclic heating conditions
- Compatible coefficient of expansion with common alloys
- Available in various size ranges and morphologies
K403 powder is designed for protective coatings, thermal spray, welding, brazing, and other high temperature applications.
This article provides a detailed look at the composition, properties, applications, specifications, pricing, safety, and other essential information about nickel-based K403 powder.
Composition of Nickel-based K403 Powder
The typical composition of nickel-based K403 powder is:
Element | Composition |
---|---|
Nickel (Ni) | Balance |
Chromium (Cr) | 21-23% |
Iron (Fe) | 17-20% |
Molybdenum (Mo) | 8-10% |
Tungsten (W) | 1-2% |
Manganese (Mn) | ≤0.5% |
Silicon (Si) | ≤0.5% |
Carbon (C) | ≤0.1% |
Nickel gives corrosion resistance. Chromium and iron provide oxidation resistance. Molybdenum and tungsten impart strength at high temperatures.
The exact composition is tailored based on the powder production method and application requirements.
Properties of Nickel-based K403 Powder
K403 powder exhibits the following properties:
Property | Details |
---|---|
Density | 8.2 g/cm3 |
Melting Point | 1350-1400°C |
Thermal Conductivity | 11 W/m.K |
Electrical Resistivity | 94 microhm-cm |
Young’s Modulus | 207 GPa |
Poisson’s Ratio | 0.29-0.30 |
Tensile Strength | ≥ 550 MPa up to 1050°C |
Elongation | 15-25% |
Hardness | 30-35 HRC |
Oxidation Resistance | Excellent isothermal up to 1150°C |
The alloy maintains high strength and hardness at elevated temperatures. It has good ductility for deformation processing. The material resists thermal fatigue cracking.
Applications of Nickel-based K403 Powder
Nickel-based K403 powder is designed for use in high temperature environments. Typical applications include:
Thermal Spray Coatings: Used to apply thick coatings resistant to wear, corrosion and oxidation at high temperatures via wire/powder flame or electric arc spraying.
Welding: Used as filler material for joining high temperature alloys providing oxidation and corrosion resistance.
Brazing: Excellent filler alloy for brazing assemblies operating at over 1000°C like turbine components, heat exchangers etc.
Additive Manufacturing: Selective laser melting and other powder bed fusion processes can utilize K403 powder to fabricate parts.
Gas Turbines: Powder metallurgy turbine components exposed to hot gas paths like blades, vanes, seals.
Chemical Industry: K403 coated components in fluidized bed reactors, heat exchangers, cyclone separators.
Glass Industry: Powder sprayed rolls, guides, baffles used in glass melting furnaces and forehearths.
Heat Treatment: Fixtures, trays, baskets operating under high temperature applications.
Specifications and Grades of K403 Powder
K403 powder is available in various size ranges, morphologies and grades:
Particle Size: Ranging from 10-45 microns for AM methods, up to 150 microns for thermal spray processes.
Morphology: Spherical, irregular and dendritic particle shapes available. Spherical powders have better flowability.
Grades: Powder can be tailored as per AMS 7875, AMS 5887 or other high temperature alloy specifications.
Purity: High purity argon gas atomized powder available for critical applications.
Customization: Alloy chemistry and particle characteristics can be customized as per application requirements.
Global Suppliers of Nickel-based K403 Powder
Some of the major global suppliers of nickel-based K403 powder include:
Company | Country |
---|---|
Sandvik | Sweden |
Carpenter Technology | USA |
Hoganas | Sweden |
Praxair | USA |
CNPC Powder | China |
VDM Metals | Germany |
AMETEK | USA |
These companies produce K403 powder using various techniques like argon gas atomization, plasma atomization, and electrode induction melting to achieve desirable powder characteristics.
Pricing of Nickel-based K403 Powder
Nickel-based K403 powder is costlier than simple alloy powders due to the complex chemistry and processing:
- Quantity – Prices range from $80-120/kg for bulk orders above 1000 kg. Smaller quantities are priced higher.
- Quality – High purity, spherical morphology powder manufactured under controlled conditions using advanced processes demands premium pricing.
- Supplier – Major global suppliers tend to offer competitive pricing owing to higher volumes.
- Geography – Prices vary across regions with USA and Europe being higher priced markets compared to China and India.
For critical applications, buyers should focus on quality rather than lowest cost while procuring K403 powder. Sourcing powder that meets specifications is vital for performance.
Health and Safety Considerations for K403 Powder
As a metallic alloy powder, K403 poses some health and safety risks:
- Fine powders can be a dust explosion hazard. Prevent dust accumulation and ignition sources.
- May cause skin and eye irritation upon prolonged exposure. Use personal protective equipment.
- Inhalation must be avoided. Use respiratory protection while handling powder.
- Powder may catalyze reactions with oxidizers. Prevent contact between incompatible materials.
- Proper grounding of equipment, ventilation, hygiene practices essential when handling the powder.
- Refer to applicable safety data sheets from suppliers for complete health hazard information.
Safety procedures for metallic powders like inert gas gloveboxes, explosion suppression systems may be implemented for worker protection.
Inspection and Testing of K403 Powder
To ensure the K403 nickel alloy powder conforms to specifications, various tests and inspections should be performed:
- Chemical Composition – Verify composition of major alloying elements using optical emission or X-ray fluorescence spectroscopy.
- Particle Size Distribution – Assess particle size range as per ASTM B822 standard using laser diffraction.
- Morphology – Inspect particle shape and surface defects under SEM. Check for satellites, porosity.
- Flow Rate – Evaluate flowability and apparent density as per ASTM B213 using Hall flowmeter.
- Impurities – Measure oxygen and nitrogen content using inert gas fusion analysis. Minimize impurities.
- Microstructure – Check phases present using X-ray diffraction analysis.
- Mechanical Properties – Perform tensile and hardness testing for powder metallurgy parts.
Qualification and batch testing ensures consistent powder quality and performance.
Comparison of K403 Powder with IN738 Powder
K403 and IN738 are two alloy powders used for high temperature applications:
Parameter | K403 Powder | IN738 Powder |
---|---|---|
Composition | Ni-Cr-Fe-Mo | Ni-Cr-Co-Al-Ti |
Oxidation Resistance | Excellent up to 1150°C | Very Good up to 1100°C |
Cost | Higher | Lower |
Phase Stability | Very Good | Poor |
Mechanical Strength | High up to 1050°C | Good up to 750°C |
Fabrication | Medium | Easy |
Applications | Thermal spray, welding | Turbine components, AM parts |
Availability | Moderate | Readily available |
For extreme temperatures exceeding 1100°C requiring phase stability, K403 is preferred despite higher cost. IN738 offers easier fabrication and lower cost.
FAQs
Q: What is nickel-based K403 powder used for?
A: K403 powder is designed for high temperature applications like thermal spray coatings, brazing, welding, additive manufacturing where oxidation and corrosion resistance up to 1150°C is required.
Q: What particle size is used for thermal spraying K403 powder?
A: Coarser K403 powder up to 150 microns is commonly used for thermal spray processes like wire arc spraying to maximize deposition efficiency and coating thickness.
Q: Is K403 suitable for laser powder bed fusion additive manufacturing?
A: Yes, fine K403 powder can be used in selective laser melting machines to fabricate complex geometry parts that perform well in high temperature environments.
Q: How does K403 compare with Haynes 214 alloy?
A: K403 has slightly better high temperature strength and oxidation resistance than Haynes 214. But Haynes 214 offers excellent fabrication characteristics and lower cost.
Q: What are the main health hazards of K403 powder?
A: Fine K403 powder poses dust explosion risks. It can also irritate skin and eyes. Inhalation must be prevented. Use proper protective equipment when handling K403 powder.
Q: Where can I purchase K403 powder for high temperature brazing application?
A: Leading suppliers like Sandvik, Carpenter Powder Products, Praxair Supply carry K403 nickel alloy powder suitable for high temperature brazing. Consider recommended particle size and purity levels based on your specific application.
About Met3DP
Product Category
HOT SALE
CONTACT US
Any questions? Send us message now! We’ll serve your request with a whole team after receiving your message.
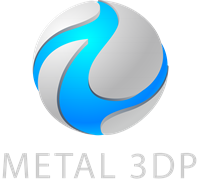
Leading provider of additive manufacturing solutions headquartered in Qingdao, China.
COMPANY
PRODUCT
cONTACT INFO
- Qingdao City, Shandong, China
- [email protected]
- [email protected]
- +86 19116340731