Electron beam additive manufacturing (EBAM) is a metal 3D printing process that uses an electron beam energy source to fuse materials. This guide examines EBAM systems, processes, materials, applications, benefits, and considerations for adopting this technology.
Introduction to Electron Beam Additive Manufacturing
Electron beam additive manufacturing (EBAM) is a type of metal 3D printing that uses a high power electron beam as the energy source to fuse metallic feedstock into fully dense parts layer by layer directly from CAD data.
Key attributes of EBAM technology:
- Uses electron beam power source to melt materials
- Builds parts by adding metal powder layer-by-layer
- Creates near-net shape parts with high density
- Typical materials are titanium, nickel alloys, steel
- Larger build volumes than other metal AM processes
- High deposition rate for faster builds
- Average part accuracy of ±0.3mm
- Low residual stress compared to laser processes
- Ideal for large, complex metal parts
- Reduces waste versus subtractive techniques
EBAM enables innovative designs not possible with conventional manufacturing. However, as with any additive process, there are distinct design and application considerations.
How Sản xuất phụ gia chùm tia điện tử Works
The EBAM process consists of:
- Depositing and leveling thin layer of metal powder
- Scanning electron beam to selectively melt areas
- Lowering build plate and repeating layering/melting
- Removal of completed parts from powder bed
- Post-processing as needed
An electron beam gun generates a focused beam under vacuum conditions. Beam power, speed, pattern and other parameters are precisely controlled to fuse material.
EBAM systems require a vacuum chamber, powder handling, electron gun, controls, and other subsystems.
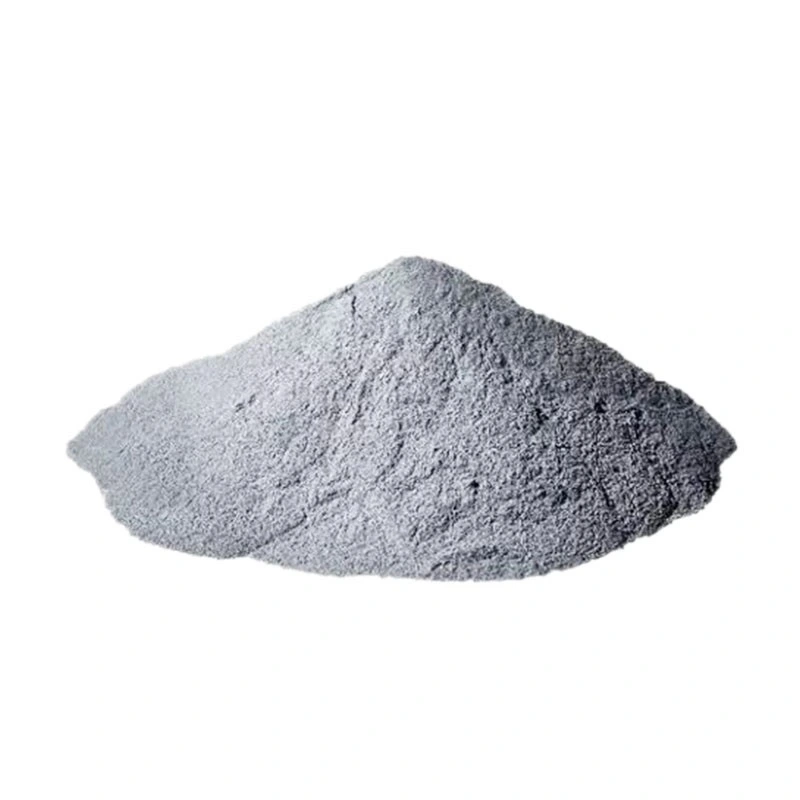
EBAM Equipment Manufacturers
Leading global suppliers of industrial EBAM systems include:
nhà chế tạo | Model | Build Size | Nguyên vật liệu | Phạm vi giá |
---|---|---|---|---|
Phụ gia GE | Arcam EBM Spectra H | 1000 x 600 x 500 mm | Ti, Ni, CoCr, Al, Cu, Steels | $1.5M – $2M |
Sciaky | EBAM 300 | 1830 x 1220 x 910 mm | Ti, Inconel, stainless | $1.5M – $3M |
Velo3D | Sapphire | 680 x 380 x 380 mm | Ti, Inconel | $1M – $2M |
Nano Dimension | DragonFly LDM | 330 x 330 x 330 mm | Đồng | $0.5M – $1M |
System selection depends on production needs, materials, accuracy requirements, and budget. Partnering with an experienced service provider is an alternative to purchasing equipment directly.
EBAM Process Characteristics
EBAM involves complex thermal, mechanical, and material interactions. Key process characteristics include:
Electron Beam – Power, beam diameter, current, scan speed, focus
Powder – Material, shape, size distribution, layer thickness
Vacuum – Required pressure levels, gas impurities
Nhiệt độ – Preheat, melt pool dynamics, cooling rate
Metadata – Build plate, rake system, shielding
Scan Strategy – Melt pool patterns, beam oscillations
Post-processing – Heat treat, HIP, machining, finishing
Understanding relationships between parameters is critical to achieve high quality EBAM parts.
EBAM Design Guidelines
Proper EBAM part design practices include:
- Design with additive manufacturing principles in mind
- Use thin walls and lattice structures for weight reduction
- Minimize unsupported overhangs which require supports
- Orient parts to avoid stresses leading to warpage
- Account for thermal shrinkage effects in features
- Design geometry to ease powder removal
- Engineer surfaces for functionality rather than appearance
- Accommodate minimum wall thickness and feature size
- Allow for post-processing stock on surfaces
- Simulate builds and thermal effects for complex parts
- Design fixturing and interfaces for powder bed removal
Simulation and modeling tools help predict residual stresses and deformation.
EBAM Materials
A range of metals can be processed with electron beam additive manufacturing:
Category | Common Alloys |
---|---|
Titan | Ti-6Al-4V, Ti-6Al-4V ELI, Commercially Pure Titanium |
Superalloys niken | Inconel 718, Inconel 625, Haynes 282 |
Thép không rỉ | 304, 316, 17-4PH, 15-5PH |
Thép công cụ | H13, Maraging Steels |
Nhôm | AlSi10Mg, Scalmalloy |
Precious Metals | Gold, Platinum |
Đồng | CuCrZr, Cu, Copper Nickel Alloys |
Cobalt chrome | CoCrMo, Stellite |
Material properties depend heavily on EBAM process parameters and post-treatment.
Key EBAM Applications
EBAM enables performance improvements across industries:
Ngành công nghiệp | Typical EBAM Applications |
---|---|
Không gian vũ trụ | Aircraft structures, turbines, launch hardware |
Sản xuất điện | Hot gas path components, housings |
Dầu & amp; khí ga | Valves, pumps, compressors, tooling |
Ô tô | Lightweighting parts, heat exchangers |
Thuộc về y học | Orthopedic implants, surgical instruments |
Hàng hải | Impellers, propellers, complex castings |
Hóa chất | Heat exchangers, stirrers, pressure vessels |
Benefits over conventional manufacturing include:
- Reduced waste from buy-to-fly ratio of 1:1
- Shorter lead time from digital process
- Combined assemblies into single parts
- Customized geometries unsuited for machining
- Improved performance from complex structures
- Scalable production volumes once qualified
EBAM creates opportunities for next-generation product designs not feasible by other means.
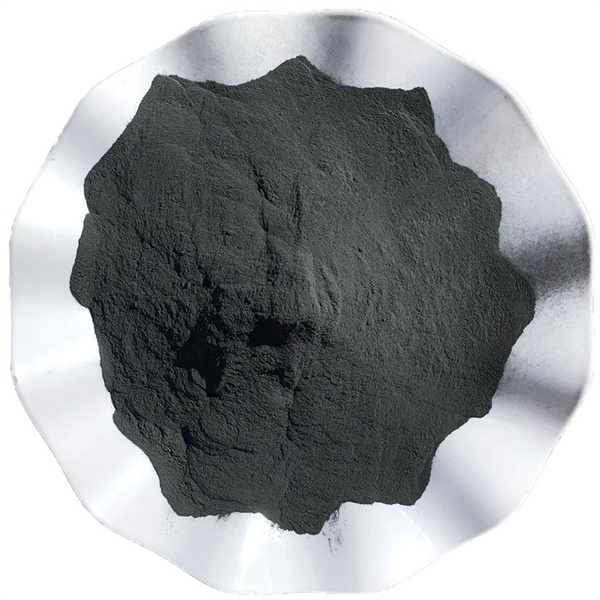
Pros and Cons of EBAM
Advantages:
- Large complex metal parts in a single piece
- Strong and light components from lattice designs
- Eliminates need for expensive dies or tooling
- Reduced material waste compared to subtractive techniques
- Relatively fast build rate compared to other AM processes
- Cost effective at medium volumes of 100-10,000 units
- Consistent metallurgy from rapid solidification
- Combines assemblies into single parts
- On demand production and customizable designs
- Geometry freedom beyond machining constraints
Limitations:
- Higher equipment cost than polymer 3D printing
- Restricted to vacuum compatible materials
- Lower accuracy and surface finish than machining
- Post-processing often required to achieve properties
- Production of scrap powder requiring recycling
- Process development and trials needed
- Facility considerations for high power needs
- Thermal stresses may cause part distortion
- Constraints on overhangs and minimum features
- Size limitations from build chamber envelope
When suitable for application requirements, EBAM enables high value product improvements.
Implementing EBAM Technology
Key considerations when adopting EBAM include:
- Identifying applications where EBAM capabilities provide advantage
- Budgeting significant capital investment for EBAM system
- Developing rigorous qualification protocols and standards
- Understanding regulatory requirements for end use applications
- Hiring personnel with powder bed expertise or partnering with service providers
- Allowing time and resources for process trials and optimizations
- Implementing powder handling procedures and ventilation
- Providing suitable facilities infrastructure and power capabilities
- Budgeting for secondary processing like heat treating
- Performing mechanical testing to validate properties
Applications best suited for initial trials are less critical and lower risk.
Cost Savings with EBAM
The business case for EBAM depends on:
- High equipment cost around $1 million to $3 million
- Labor for process development and production
- Cost of raw metallic powder materials
- Secondary finishing operations
- Facilities, powder handling infrastructure
- Reduced waste relative to subtractive processes
- Consolidating subassemblies into single parts
- Shorter development timelines than conventional techniques
- Becoming economical at volumes around 100-10,000 parts
- Highest savings for complex geometries adding value
Manufacturers must outweigh higher AM equipment costs by manufacturing benefits.
EBAM Compared to Other Processes
Process | Comparison to EBAM |
---|---|
CNC Machining | EBAM enables complex geometries unmachinable through subtractive process. No hard tooling required. |
Đúc kim loại | EBAM eliminates high tooling costs. Better material properties than MIM. |
Die Casting | EBAM has lower tooling costs. No size limitations. Very complex geometries achievable. |
Sheet Lamination | EBAM creates fully dense isotropic material versus laminated composites. |
Binder Jetting | EBAM delivers fully dense final parts compared to porous binder jetted green parts. |
SLM | SLM has finer resolution while EBAM has faster build rates. Both create dense metal parts. |
Each process offers specific advantages based on the application, batch size, accuracy needs, and performance requirements.
Future Outlook for EBAM
The future is bright for expanded adoption of EBAM driven by:
- Broader range of production-grade alloys
- Larger build envelopes enabling bigger parts
- Faster build rates for increased throughput
- Improved finish and dimensional accuracy
- Declining costs as technology matures
- Further automation of pre/post processing
- Hybrid systems integrating machining
- Advanced in-process monitoring systems
- Qualification for demanding industries like aerospace
- Design optimization leveraging EBAM capabilities
As the technology progresses, EBAM will transform manufacturing across a widening range of industries.
Câu hỏi thường gặp
What materials are used in EBAM?
Titanium, nickel alloys, tool steels, stainless steels, aluminum alloys, and precious metals can be processed.
What is the accuracy and finish of EBAM parts?
Dimensional accuracy of ±0.3mm is typical, with surface roughness around 25-125μm Ra as-built.
What post-processing is used for EBAM parts?
Heat treating, HIP, and machining may be used. Plasma spray coating is also common.
How big of parts can EBAM produce?
Common build volumes range from 500mm x 500mm x 500mm up to 2m x 1m x 1m for large systems.
What are the benefits over subtractive methods?
EBAM generates near net-shape parts with reduced waste and consolidates assemblies into single complex components.
What industries use EBAM?
Aerospace, energy, automotive, oil and gas, and medical sectors are early adopters of EBAM.
What expertise is needed to operate EBAM equipment?
Skilled technicians experienced in powder bed processes, metallurgy, and post-processing are required.
What safety precautions are required?
Ventilation, monitoring equipment, personnel protective equipment, and safe powder handling are critical.
How does cost compare to conventional manufacturing?
EBAM becomes cost effective around mid-volume production of 100-10,000 units for complex designs.
Can you briefly explain the EBAM process?
EBAM deposits metallic powder in layers which an electron beam melts selectively layer-by-layer based on CAD data to build a part.