Hastelloy X is a nickel-based alloy powder with excellent high temperature strength, oxidation resistance, and fabricability. This guide provides a comprehensive overview of Hastelloy X powder including its properties, processing, applications, suppliers, costs, and more.
Tổng quan về Hastelloy X Powder
Hastelloy X is a patented nickel-chromium-iron-molybdenum alloy powder designed for outstanding performance in extreme environments up to 1300°F (704°C). Key features include:
- Sức mạnh nhiệt độ cao và khả năng chống leo
- Quá trình oxy hóa và chống ăn mòn tuyệt vời
- Good weldability and fabricability
- Resistance to stress-rupture cracking
- Can be aged hardened through heat treatment
It offers superior mechanical properties compared to other nickel alloys due to additions of chromium, molybdenum, and tungsten. This combination gives Hastelloy X excellent resistance to oxidation, carburization and chlorination attack.
Hastelloy X is most commonly used in powder form for additive manufacturing processes like laser powder bed fusion (L-PBF) and directed energy deposition (DED). The fine spherical powders provide smooth flowability, packing density, and spreadability needed for high quality 3D printed parts.
The alloy is also produced as wire, sheet, plate, pipe and casting. Powder metallurgy Hastelloy X parts can be easily post-processed through hot isostatic pressing (HIP) and heat treatment to further enhance properties.
Ứng dụng của Hastelloy X Powder
Hastelloy X’s outstanding high-temperature strength makes it well suited for extreme environment applications including:
- Aircraft and aerospace – Combustion cans, missile components, rocket nozzles
- Power generation – Gas turbine hot section parts
- Chemical processing – Reformer tubes, crackers, heat exchangers
- Automotive – Turbocharger parts, exhaust valves
Other uses include nuclear fuel element cladding, furnace parts, and glass molds. Hastelloy X’s good oxidation resistance allows it to replace more expensive refractory metals in many applications.
Composition and Specifications
Hastelloy X powder typically has a nominal composition (weight %) of:
- Nickel: 47%
- Chromium: 22%
- Iron: 18%
- Molybdenum: 9%
- Cobalt: 2.5%
- Tungsten: 1%
Key specifications for Hastelloy X powder include:
Tham số | Sự chỉ rõ |
---|---|
Kích thước hạt | 15-45 m |
Hàm lượng oxy | & lt; 1000 ppm |
Mật độ rõ ràng | ≥4 g/cc |
Lưu lượng dòng chảy | ≥25 s/50g |
Thành phần hóa học | Ni: Balance <br> Cr: 21-23% <br> Fe: 17-20% <br> Mo: 8-10% <br> Co: 2-3% <br> W: 0.6-1.2% |
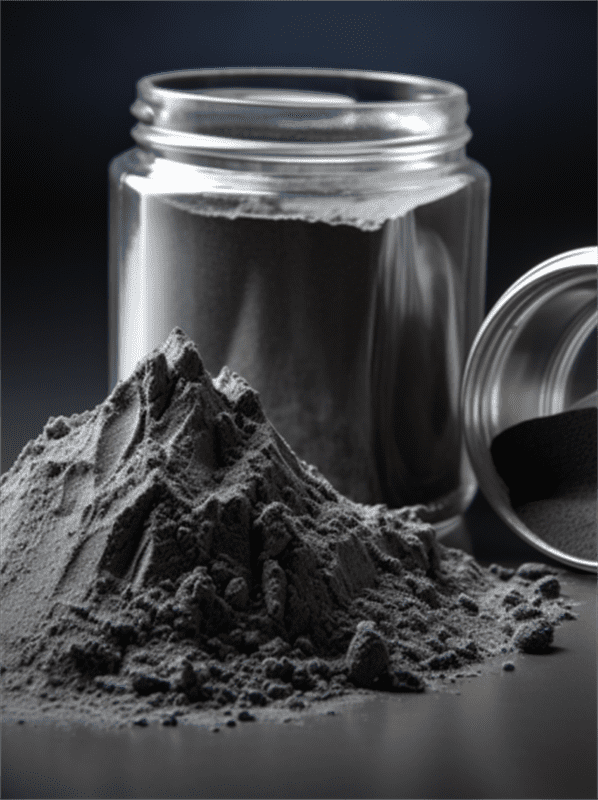
Manufacturing Processes for Hastelloy X Parts
Hastelloy X powder can be used to manufacture components through several additive and conventional manufacturing techniques.
Additive Manufacturing Processes
Laser Powder Bed Fusion (L-PBF)
L-PBF is one of the most common additive manufacturing processes for metals. A laser selectively melts and fuses powder layers based on a 3D model to build up a part layer-by-layer. Hastelloy X powder’s spherical morphology and optimized size distribution is ideal for this process.
Key benefits of L-PBF Hastelloy X parts:
- Complex geometries and lightweight structures
- Minimal material waste
- High density and mechanical properties
- Good surface finish
- Short lead times for prototypes and production
Directed Energy Deposition (DED)
DED uses a focused heat source like a laser, electron beam or plasma arc to melt metal powder or wire which is then deposited and built up layer-by-layer.
Advantages of DED with Hastelloy X include:
- Ability to repair and add features to existing parts
- Larger build volumes than powder bed processes
- Low porosity and residual stress
- Combination of different materials or gradients possible
Binder Jetting
In binder jetting, a liquid bonding agent is selectively printed onto metal powder beds to create a green part. Hastelloy X green parts are then sintered to fuse the particles together into a dense final part.
Benefits of binder jet Hastelloy X parts:
- Very high print speeds compared to laser processes
- No support structures needed
- Large build volumes possible
- Lower equipment costs than laser processes
Conventional Manufacturing Processes
Hastelloy X powder can also be processed into fully dense parts using:
- Metal injection molding (MIM) – Mixing fine powder with a binder, injection molding, then sintering
- Hot isostatic pressing (HIP) – Applying high temperature and isostatic gas pressure on powder to consolidate it
- Powder forging – Compacting and heating powder in a mold to shape and densify
These conventional powder metallurgy approaches allow complex net-shape parts to be produced with minimal machining. The isotropic properties give reliable performance.
How to Choose Hastelloy X Powder
Powder Characteristics
When selecting Hastelloy X powder, key characteristics to consider include:
Kích thước hạt – Affects powder flowability, surface finish, and density. Typical range is 15-45 μm. Finer is better for resolution but may have poor flow.
Hình thái – Spherical powders with smooth surfaces provide best flow and spreading. Irregular shapes make handling more difficult.
Mật độ rõ ràng – Higher density improves powder bed loading, thermal conductivity, and final part density. Values of ≥4 g/cc are recommended.
Lưu lượng dòng chảy – Important for smooth powder spreading on the build plate. Flow rates of 25-35 s/50g indicate good flowability.
Hàm lượng oxy – Lower oxygen leads to better density and mechanical properties. Should be <1000 ppm.
Thành phần hóa học – Must match the specified Hastelloy X composition range for properties.
Supplier Reputation and Quality Systems
Reputable suppliers with strong quality control are essential for reliable, consistent powder:
- Stringent chemical analysis and powder characterization testing
- Powder produced in controlled conditions
- Rigorous lot sampling and testing
- Process controls and SOPs for handling, storage, transportation
- Quality certifications like ISO 9001, ISO 13485
Trị giá
Hastelloy X powder costs between $60-100 USD/kg. Prices depend on order quantity, powder quality/characteristics, supplier brand, and geographical location. Larger orders typically have lower per-unit costs.
How to Choose a Hastelloy X Powder Supplier
Key factors in choosing a Hastelloy X powder supplier include:
Reputation – Experienced companies with proven success and satisfied customers. Look for testimonials and case studies.
Chất lượng – Stringent quality control, sampling, testing, certification, and documentation.
Expertise – Deep metallurgical and powder production knowledge. Ability to customize powders if needed.
Consistency – Robust processes ensure every batch meets specifications.
Inventory – Ready stock availability in small to large quantities avoids long lead times.
Customer service – Responsiveness to inquiries, technical support, and guidance.
Distribution network – Warehouses near you avoid long shipping times and delays.
Prices – Reasonable prices for required order volumes and powder characteristics.
Terms – Flexible payment terms, shipping costs/times, and purchase options.
Leading global suppliers of Hastelloy X powder include Sandvik, Carpenter Technology, Praxair, and AP&C. It helps to compare multiple suppliers using these criteria to find the best fit for your needs and budget.
Installing and Operating Hastelloy X Powder AM Systems
Installing and operating metal additive manufacturing systems capable of processing Hastelloy X powder requires attention to:
System requirements – Power, inert gas supplies, chiller, ventilation. L-PBF systems like EOS M400 need ~65 kW power.
Facility conditions – Temperature 20-25°C. Relative humidity 30-70%. Minimal temperature/humidity fluctuations.
Personnel – Trained system operators. Separate post-processing team. System maintenance support.
Feedstock handling – Gloveboxes, powder sieving equipment, powder recycling systems. Minimize powder contact with air and moisture.
Workflow – Parameter optimization, build setup, post-processing, quality control. Digital workflow from design to finished part.
Monitoring requirements – Build monitoring cameras. Residual oxygen analyzers. Alerts if parameters exceed limits.
Safety – Enclosed systems. Operator PPE. Exposure limits for metal powders. Fire and explosion prevention measures.
Maintenance – Periodic maintenance as prescribed by manufacturer. Laser, optics, powder handling system, sensors.
Calibration – Regular calibration of laser power meter, powder layer thickness device, O2 sensors.
Parameter optimization – Achieve material properties by optimizing laser power, speed, hatch spacing, layer thickness, build orientation.
Close control and monitoring of these aspects is necessary for safe, repeatable production of high quality Hastelloy X parts.
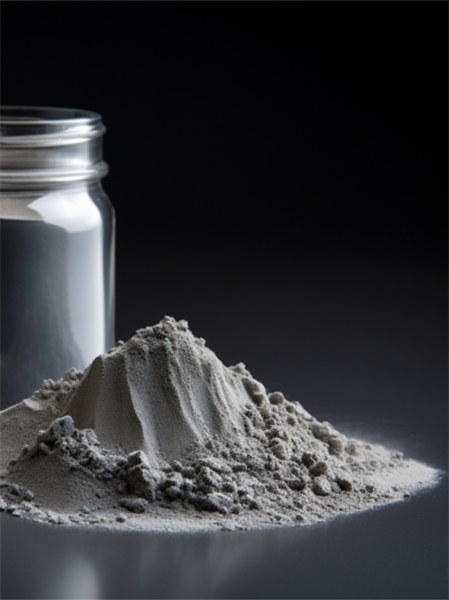
Post-Processing Methods for Hastelloy X AM Parts
As-built Hastelloy X parts from additive manufacturing require post-processing to achieve final properties and quality:
Support removal – For some processes like L-PBF, supports must be removed from internal cavities and overhangs, often using EDM wire cutting.
Giảm căng thẳng – Heat treating below solution annealing temperature to reduce residual stresses from the build process. 450-760°C range.
Nóng isostatic nhấn (hông) – Applying a high pressure inert gas atmosphere at high temperature to close internal voids and densify the microstructure.
Surface finishing – Machining, grinding, sandblasting, or polishing exterior surfaces to improve surface roughness, accuracy, and aesthetics.
Final part cleaning – Vibratory finishing, cleaning in alkaline solutions, or solvents removes loose powder particles and surface contaminants.
Solution treatment – Heating above the alloy’s solvus temperature then rapid cooling/quenching to dissolve secondary phases and enhance mechanical properties.
Aging/precipitation hardening – Heat treating to allow fine strengthening precipitates to form within the alloy microstructure.
Proper post-processing is key to achieve the material properties and performance required by the application. The methods used depend on the AM process, design geometry, and end-use functional requirements.
Quality Control and Testing of Hastelloy X Powder and Parts
Thorough quality control and testing is crucial when working with Hastelloy X powder feedstock and printed parts:
Powder testing – Chemical composition, particle size distribution, flow rate, apparent density, morphology, impurities. Ensures powder meets specifications.
Parameter monitoring – In-process monitoring of layer thickness, recoater blade speed, laser power, hatch spacing, scanning speed, etc. to ensure optimal build.
Kiểm tra trực quan – Check for surface defects, cracking, warpage, delamination between layers using dye penetrant if needed.
Dimensional inspection -Measure critical dimensions to check conformance with CAD model using CMMs or 3D scanners.
Đo mật độ – Verify≥99.5% theoretical density was achieved for mechanical integrity. Using Archimedes method or x-ray CT scanning.
Surface roughness testing – Quantify surface finish of as-built and post-processed parts. Optical profilometry or stylus instruments.
Mechanical testing – Tensile, fatigue, fracture toughness, hardness, Charpy impact testing per applicable ASTM standards.
Microstructure characterization – Optical, SEM and EBSD analysis checks for porosity, cracking, grain morphology, precipitates, dislocations.
Phân tích hóa học – ICP-OES or XRF spectroscopy verifies final alloy composition is correct.
Non-destructive testing – Ultrasonic, radiographic, eddy current, magnetic particle inspection of critical components.
Data from this extensive testing validates properties and quality. Parts that fail any check may require re-builds or further post-processing.
Pros and Cons of Hastelloy X vs. Alternatives
Hastelloy x
Ưu điểm
- Excellent high temperature mechanical properties up to ~700°C
- Better oxidation resistance than stainless steels or Inconel 718
- Higher strength than Inconel 625 while resisting oxidation
- Good weldability relative to other Ni-based superalloys
- Lower cost than refractory alloys like tantalum or tungsten
Nhược điểm
- Inferior high temperature capabilities versus Inconel 718 above ~650°C
- Subject to embrittlement if exposed to sulfur or lead at high temperatures
- More difficult to machine than austenitic stainless steels
- Higher cost than stainless steels
Inconel 625
Ưu điểm
- Excellent corrosion resistance in wide range of environments
- High strength at room temperature and 600°C
- Good oxidation resistance up to 980°C
- Lower cost than Hastelloy X or Inconel 718
Nhược điểm
- Less high temperature strength than Hastelloy X
- Susceptible to pitting in some environments
- Subject to thermal fatigue cracking
Inconel 718
Ưu điểm
- Retains strength up to 704°C, better than Hastelloy X at very high temperatures
- High creep and fatigue resistance
- Khả năng chống ăn mòn tốt trong nhiều môi trường
Nhược điểm
- Poor oxidation resistance at temperatures above 600°C
- Susceptible to post-weld cracking
- More difficult to weld than Hastelloy X
316L Stainless Steel
Ưu điểm
- Excellent corrosion resistance in various environments
- Dễ hàn và có thể gia công
- Good bio-compatibility for medical uses
- Lower cost than nickel superalloys
Nhược điểm
- Limited high temperature capability, can’t exceed ~315°C
- Susceptible to pitting and crevice corrosion in some environments
- Lower hardness and wear resistance
For the best combination of fabricability, strength, and oxidation resistance up to 704°C, Hastelloy X provides advantages over these alternatives for many applications.
Uses and Applications of Hastelloy X Parts from AM
Additive manufacturing makes it feasible to produce complex Hastelloy X components customized for demanding applications:
Không gian vũ trụ
- Combustion cans and liners
- Aircraft engine blades and nozzles
- Rocket thrusters and propulsion components
- Spacecraft turbopumps and valves
Gas Turbines
- Combustors, transitions, and hot gas path parts
- Fuel nozzles
- Tấm giữ nhiệt
- Vanes, blades and shrouds
Xử lý hóa học
- Reformer furnace tubes
- Ethylene cracker tubes
- FGD process gas exchangers
- Fluidized catalytic cracker catalyst injection nozzle
Ô tô
- Exhaust system components
- Turbocharger wheels and housing
- Thermal shielding parts
Glass Molds
- Precision glass lens and prism molds
- Glass blowing molds
Hạt nhân
- Fuel element cladding and components
The unique strengths of Hastelloy X enable lighter, more capable components in these extreme environments compared to conventional materials and manufacturing.
Installing and Maintaining Hastelloy X AM Parts
Proper installation and maintenance is key to achieving the expected service life from Hastelloy X AM components in demanding applications:
Surface preparation – For parts like turbine blades, carefully polish surfaces and remove any powder remaining in crevices to prevent accelerated attack during service.
Dimensional inspection – Ensure critical interfaces and dimensions are within specifications after post-processing so parts fit correctly at assembly.
Handing precautions – Take care to avoid galling of threads and surfaces during assembly. Use proper torquing methods.
Corrosion protection – Apply appropriate protective coatings on mating surfaces as corrosion inhibitors. Mask cooling holes during coating.
Installation method – Follow manufacturer instructions during part installation. Account for thermal expansion differences from AM microstructure.
Operating conditions – Do not exceed temperature, pressure, flow, rotation speed, and load limits in service.
Monitoring – Utilize sensors, online monitoring to track part condition and identify problems early.
Maintenance – Periodic inspections for wear, cracks, corrosion damage, warping, oxidation. Replace as needed.
Cleaning procedures – Use proper techniques to clean parts during maintenance without damaging surfaces.
Proper installation combined with monitoring, maintenance and replacement when needed will achieve the full potential of AM Hastelloy X components for long term performance.
Frequently Asked Questions About Hastelloy X Powder
Q: What particle size range is best for AM processes like L-PBF?
A: A particle size range of 15-45 microns is recommended. Finer powders around 15 μm provide good resolution and surface finish while sizes up to 45 μm improve powder flow and packing density.
Q: Does Hastelloy X powder require drying or plasma treatment before AM?
A: Hastelloy X powder is usually spray atomized in inert gas so no additional drying or plasma treatment is required before printing. The powder should be handled properly to avoid absorbing excess moisture from air during storage/transport.
Q: What are common heat treatment procedures for Hastelloy X?
A: A typical heat treatment is 2 hours solution annealing at 1150°C followed by air cooling, then 20 hours precipitation hardening at 760°C and air cool. This strengthens Hastelloy X through gamma prime precipitation.