Refractory metal powders enable additive manufacturing of extremely heat resistant alloys unmatched by other materials. This guide covers refractory powder compositions, particle specifications, properties data, pricing, and comparisons to inform procurement decisions.
Introduction to Refractory Metal Powders
Key capabilities offered by refractory powders include:
- Withstand extremely high temperatures
- Retain high strength at temperature extremes
- Resist creep deformation and cracking
Common alloys used are:
- Tungsten heavy alloys like W-Ni-Cu
- Molybdenum TZM alloy
- Tantalum powders
This guide provides considerations when selecting refractory powders:
- Alloy Compositions and Production Methods
- Mechanical Properties Test Data
- Particle Size Distribution Recommendations
- Morphology, Density and Flow Characteristics
- Pricing Estimates Based on Order Volumes
- Oxidation and Corrosion Resistance Comparisons
- Pros vs Cons Relative to Solid Forms
- FAQs on Printing Parameter Optimization
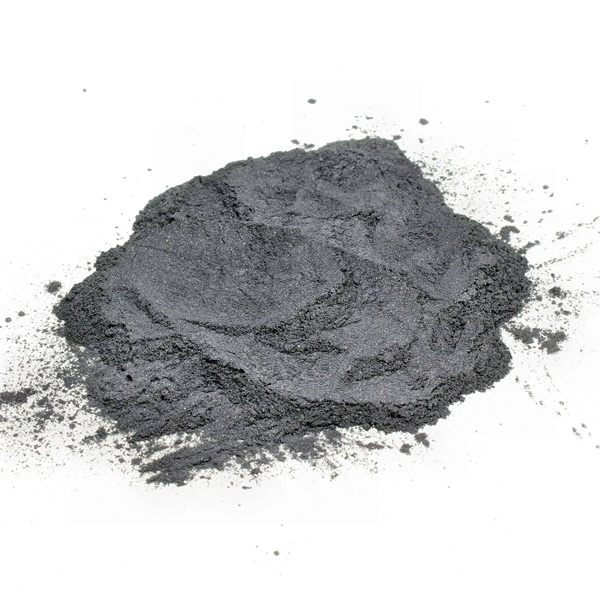
Refractory Metal Powder Compositions
Bảng 1 shows refractory metal powder compositions by primary elemental additions with some variation depending on alloy variant:
Hợp kim | Major Alloying Elements |
---|---|
Tungsten Heavy Alloy | W, Ni, Cu, Fe |
Molybdenum TZM | Mo, Ti, Zr |
Tantalum | Phải đối mặt |
Small additions of carbon, potassium, silicon and boron also stabilize microstructures and grain sizes tailored for high temperature creep resistance depending on operating conditions.
Mechanical Properties and Test Methods
ban 2 shows typical minimum mechanical properties met by refractory metal powder alloys, with actual values varying based on build geometry, post-processing, and heat treatment:
Hợp kim | Tỉ trọng | **Tensile Strength ** | Phương pháp kiểm tra |
---|---|---|---|
Tungsten Heavy Alloy | 18 g/cc | 550 MPa | ASTM E8 |
Molybdenum TZM | 10.2 g/cc | 485 MPa | ASTM E8 |
Tantalum | 16.6 g/cc | 207 MPa | ASTM E8 |
Carefully validate delivered powder lot properties against certifications through sampling to ensure consistency.
Refractory Metal Particle Size Recommendations
bàn số 3 shows common particle size distributions used for quality refractory powders:
Phạm vi kích thước | Typical Mesh | Common Printing Range |
---|---|---|
Khỏe | -325 mesh | 15-45 micron |
Tiêu chuẩn | -100 mesh | 149 microns |
Thô | -60 +100 mesh | 250 microns |
Other important powder characteristics:
- Spherical particle morphology
- Good flow rates exceeding 30s hall funnel time
- Apparent density within 5% of true density
- Low oxygen and moisture content
Balance high powder flowability against print resolution needs through particle size selection and distribution.
Powder Morphology, Density and Flow Properties
Bảng 4 compares powder characteristics between general quality levels that impact print process robustness:
Tham số | High Quality Powder | Entry-level Powder |
---|---|---|
Hình thái | Cao hình cầu | Jagged, irregular |
Lưu lượng dòng chảy | Hall flow > 35s for 50g | Hall flow < 25s for 50g |
Mật độ rõ ràng | > 90% true density | Often <80% true density |
Moisture Content | <0.01% | >0.02% |
Poor powder properties require extensive parameter adjustments to achieve print quality, reducing productivity.
Refractory Metal Powder Pricing
Table 5 outlines rough refractory powder pricing under normal market conditions:
Khối lượng đặt hàng | Price Estimate |
---|---|
10 kg | $450+/kg |
100 kg | $275+/kg |
500+ kg | $200+/kg |
1000+ kg | Subkey discounts |
- Premium alloys command higher baseline pricing
- Bulk orders beyond 500 kg enable >40% price reductions
- Actual market prices tied to commodity indexes
- Carefully validate true yields vs usable fractions from suppliers
Oxidation and Corrosion Resistance Properties
Refractory metal powders offer extremely high melting points and stability in oxidizing environments:
Bảng 6
Hợp kim | Độ nóng chảy | Kháng oxy hóa |
---|---|---|
Tungsten Heavy Alloy | 1400°C | Xuất sắc |
Molybdenum TZM | 2600°C | Xuất sắc |
Tantalum | 2996 ° C. | Extreme |
Properties derive from high chromium, aluminum and silicon content creating tenacious oxide barriers preventing material loss even at extreme temperatures nearing melting points.
Pros vs Cons: Powder vs Solid Forms
Bảng 7
Thuận lợi | Bất lợi | |
---|---|---|
Bột kim loại chịu lửa | Complex geometries | Higher cost |
Sức mạnh nhiệt độ cao tuyệt vời | Post-processing | |
Weight reduction | Parameter optimization | |
Refractory Metal Solid | Chi phí thấp hơn | Shape limits |
khả dụng | Very heavy | |
Khả năng gia công | Material waste |
In general, refractory powders justify premiums for low volume complex components where thermal resistance is vital. Standard mill product forms offer affordability for simple shapes in high quantities.
Combining supply forms strategically reduces overall program costs.
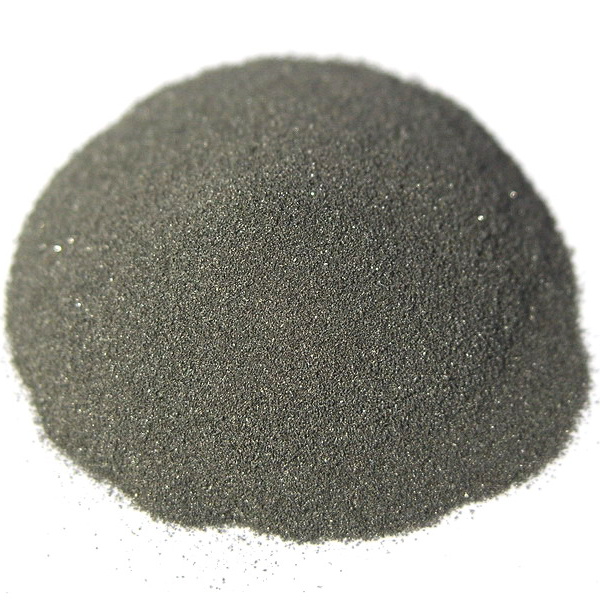
Câu hỏi thường gặp
Table 8 – Common questions:
Câu hỏi thường gặp | Answer |
---|---|
Should I review test reports? | Yes, validate certification data indicates powder quality |
What size powder particles should I use? | 15-45 microns balances resolution and flow |
What impacts consistency? | Production method affects variability – vacuum melted is best |
How much should I buy initially? | Start small, buy more once process is validated |
Table 9 – Application-focused advice:
Câu hỏi thường gặp | Answer |
---|---|
How do I optimize for rocket nozzle components? | Use extra fine <10 micron W or Mo powders to print sub 2mm channels |
Which post processing approach lowers porosity? | Hot isostatic pressing with inert atmosphere protects against oxidation |
Which refractory alloy maximizes creep resistance? | Consider additions of potassium, silicon and boron in tungsten heavy alloys based on operating temperatures |
How should I adjust parameters for ultra fine feature resolution? | Slow down scan speeds, increase hatch spacing, use smallest layer thicknesses machine allows |