Selective laser melting (SLM) is a metal additive manufacturing process that uses a laser to fuse metallic powder into fully dense components. This guide examines SLM technology, systems, materials, applications, benefits, and considerations when implementing additive manufacturing with SLM.
Introduction to Sản xuất phụ gia SLM
Selective laser melting (SLM) is a powder bed fusion additive manufacturing technique that utilizes a high-power laser to selectively melt and fuse metallic powder particles layer-by-layer to build up fully dense 3D parts directly from CAD data.
Key attributes of SLM technology:
- Uses focused laser beam to melt powdered metals
- Adds material only where required in each layer
- Allows complex geometries unachievable by casting or machining
- Creates near-net shape metal components with high density
- Materials include aluminum, titanium, stainless steel, alloys
- Small to medium part build volumes
- Ideal for complex, low-volume parts
- Eliminates need for hard tooling like molds or dies
- Significantly reduces waste compared to subtractive methods
- Enables lightweight designs and part consolidation
- Allows functional improvements with engineered structures
With its capabilities, SLM delivers game-changing benefits for innovative product design and lean manufacturing. However it requires expertise to master the process.
How SLM Additive Manufacturing Works
The SLM production process consists of:
- Spreading and leveling a thin layer of metal powder on a build plate
- Selectively scanning a focused laser beam to melt powder
- Lowering build platform and repeating layering and melting
- Removing completed parts from the powder bed
- Post-processing parts as needed – cleanup, heat treat etc.
Precisely controlling the laser, scan patterns, chamber atmosphere and other parameters is critical to achieve high quality, dense metal parts with SLM.
SLM systems feature a laser generator, beam delivery optics, powder delivery system, build chamber, inert gas handling, and central controls. Performance depends heavily on system engineering and tuning build parameters.
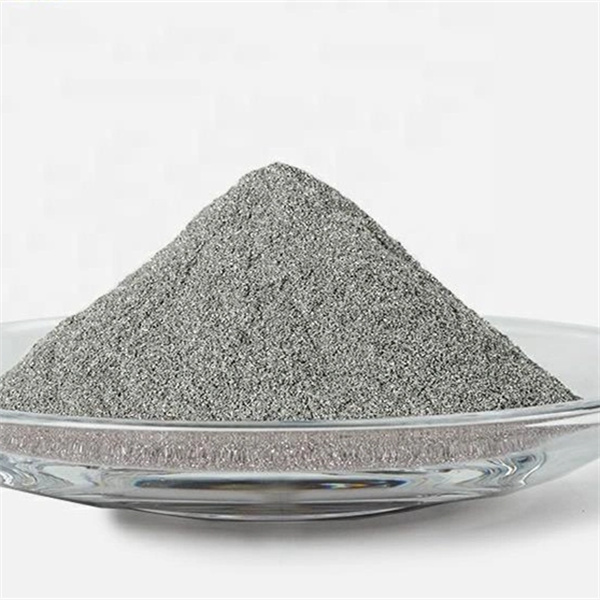
SLM Equipment Manufacturers
Leading global suppliers of SLM additive manufacturing systems include:
Công ty | Models | Build Size Range | Nguyên vật liệu | Phạm vi giá |
---|---|---|---|---|
Giải pháp SLM | NextGen, NXG XII | 250 x 250 x 300 mm <br>500 x 280 x 365 mm | Ti, Al, Ni, Steels | $400k – $1.5M |
EOS | M 300, M 400 | 250 x 250 x 325 mm <br> 340 x 340 x 600 mm | Ti, Al, Ni, Cu, Steels, CoCr | $500k – $1.5M |
Trumpf | TruPrint 3000 | 250 x 250 x 300 mm <br> 500 x 280 x 365 mm | Ti, Al, Ni, Cu, Steels | $400k – $1M |
Concept Laser | X line 2000R | 800 x 400 x 500 mm | Ti, Al, Ni, Steels, CoCr | $1M+ |
Renishaw | AM400, AM500 | 250 x 250 x 350 mm <br>395 x 195 x 375 mm | Ti, Al, Steels, CoCr, Cu | $500k – $800k |
System selection depends on build size needs, materials, quality, cost, and service support. Partnering with an experienced SLM solutions provider is recommended to properly evaluate options.
SLM Process Characteristics
SLM involves complex interactions between various process parameters. Here are key characteristics:
Laser – Power, wavelength, mode, scanning speed, hatch spacing, strategy
Powder – Material, particle size, shape, feeding rate, density, flowability, reuse
Nhiệt độ – Preheating, melting, cooling, thermal stresses
Bầu không khí – Inert gas type, oxygen content, flow rates
Build Plate – Material, temperature, coating
Scan Strategy – Hatch pattern, rotation, border outlines
Hỗ trợ – Minimizing, interface, removal
Post-processing – Heat treating, HIP, machining, finishing
Understanding relationships between these parameters is essential to achieve defect-free parts with optimized mechanical properties.
SLM Part Design Guidelines
Proper part design is critical for successful SLM additive manufacturing:
- Design with AM principles in mind vs conventional methods
- Optimize geometries to reduce weight, material use, improve performance
- Minimize need for supports using self-supporting angles
- Allow for support interface regions in design
- Orient parts to reduce stresses and avoid defects
- Account for thermal shrinkage effects in features
- Design interior channels for unmelted powder removal
- Address potential warpage in overhangs or thin sections
- Design surface finishes factoring in as-built roughness
- Consider effects of layer lines on fatigue performance
- Design fixturing interface for removing parts from powder bed
- Minimize trapped volumes of unsintered powder
Simulation software helps assess stresses and deformations in complex SLM parts before printing.
SLM Material Options
A range of alloys can be processed with SLM technology, with final material properties dependent on parameters:
Category | Common Alloys |
---|---|
Titan | Ti-6Al-4V, Ti 6242, TiAl, Ti-5553 |
Nhôm | AlSi10Mg, AlSi12, Scalmalloy |
Thép không gỉ | 316L, 17-4PH, 304L, 4140 |
Tool Steel | H13, Maraging Steel, Copper Tool Steel |
Nickel Alloys | Inconel 625, 718, Haynes 282 |
Cobalt chrome | CoCrMo, MP1, CoCrW |
Precious Metals | Gold, Silver |
Choosing compatible alloys and dialing in qualified build parameters are essential to achieve required material performance.
Key SLM Applications
SLM enables transformative capabilities across industries:
Ngành công nghiệp | Typical SLM Applications |
---|---|
Không gian vũ trụ | Turbine blades, impellers, UAV components |
Thuộc về y học | Orthopedic implants, surgical tools, patient-specific devices |
Ô tô | Lightweighting components, custom tooling |
Năng lượng | Complex oil/gas valves, heat exchangers |
Công nghiệp | Conformal cooling inserts, jigs, fixtures, guides |
Phòng thủ | Drones, firearms, vehicle & body armor components |
Benefits versus conventional manufacturing include:
- Mass customization capability
- Shorter development time
- Design freedom for performance gains
- Part consolidation and lightweighting
- Eliminating excessive material use
- Supply chain consolidation
Careful validation of mechanical performance is needed when applying SLM parts in critical applications.
Pros and Cons of SLM Sản xuất phụ gia
Advantages:
- Design freedom enabled through additive process
- Complexity achieved without increased costs
- Eliminates need for hard tooling like molds or dies
- Consolidates subassemblies into single components
- Lightweighting from organic, topology optimized structures
- Customization and low volume production
- Reduced development time versus casting/machining
- High strength-to-weight ratio from fine microstructures
- Greatly minimizes material waste versus subtractive processes
- Just-in-time and decentralized production
- Reduced part lead time and inventory
Limitations:
- Smaller build volumes than other metal AM processes
- Lower accuracy and surface finish than CNC machining
- Limited choice of qualified alloys compared to casting
- Significant trial-and-error to optimize build parameters
- Anisotropic material properties from layer-by-layer buildup
- Potential for residual stress and cracking defects
- Powder removal difficulties from complex internal geometries
- Often requires post-processing to achieve final properties
- Higher equipment cost than polymer 3D printing
- Special facilities and inert gas handling needed
When applied appropriately, SLM enables breakthrough performance impossible by other means.
Implementing SLM Additive Manufacturing
Key steps when adopting SLM technology include:
- Identifying suitable applications based on needs
- Confirming SLM feasibility for chosen designs
- Developing rigorous process qualification protocols
- Investing in suitable SLM equipment
- Securing expertise in metallic powder bed processes
- Establishing stringent material quality procedures
- Mastering parameter development and optimization
- Implementing robust post-processing methods
- Qualifying mechanical properties of finished components
A methodical introduction plan focused on low-risk applications minimizes pitfalls when adding SLM additive capabilities. Partnering with experienced SLM service bureaus or system OEMs provides access to expertise.
Cost Analysis of SLM Production
The economics of SLM production involve:
- High machine equipment cost
- Labor for build setup, post-processing, quality control
- Material costs of suitable metal powder feedstock
- Part finishing – machining, drilling, deburring etc.
- Overhead – facilities, inert gas, maintenance
- Initial trial-and-error process development
- Costs decline with production experience and volume
- Becomes economical at volumes around 1-500 units
- Provides highest cost advantage for complex geometries
Choosing qualified alloys from reputable suppliers is recommended to prevent defects. Partnering with a service provider offers a faster and lower risk adoption path.
SLM Compared to Other Processes
Process | Comparison to SLM |
---|---|
CNC Machining | SLM enables complex shapes unmachinable through subtractive process. No hard tooling required. |
Đúc kim loại | SLM has no high tooling costs. Better material properties than MIM. |
Die Casting | SLM has lower tooling costs. No size limitations. Very complex geometries achievable. |
Sheet Lamination | SLM creates fully dense and isotropic material versus laminated composites. |
Binder Jetting | SLM creates fully dense green parts versus porous binder jetted parts requiring sintering. |
DMLS | SLM provides higher accuracy and better material properties than polymer DMLS. |
EBM | Electron beam melting has higher build rates but lower resolution than SLM. |
Each process offers specific advantages based on the application requirements, batch size, materials, and performance needs.
Future Outlook for SLM Additive Manufacturing
SLM is poised for significant growth in coming years driven by:
- Ongoing material expansion with more alloy availability
- Larger build volumes enabling industrial scale production
- Improved surface finishes and tighter tolerances
- Increased system reliability and productivity
- New hybrid systems integrating CNC machining
- Declining costs improving business case viability
- Further optimization algorithms and simulation
- Automated support removal and post-processing
- Growth in qualified parts for regulated industries
- Continued advancement of high complexity designs
SLM will become mainstream for an expanding range of applications where its capabilities provide distinct competitive advantage.
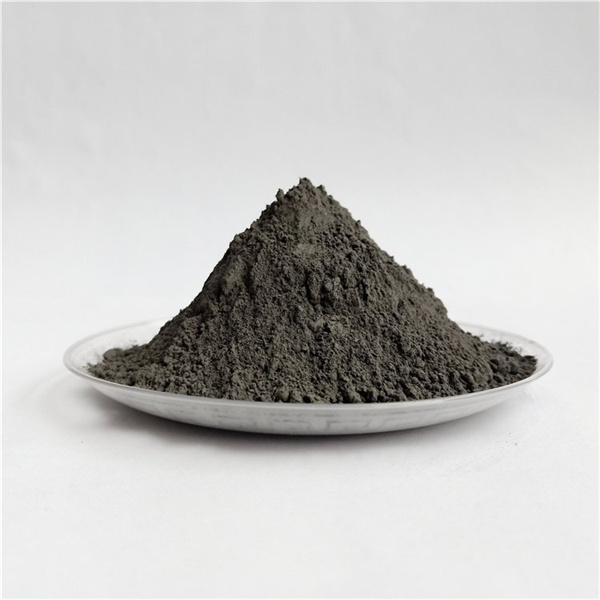
Câu hỏi thường gặp
What materials can you process with SLM technology?
Titanium, aluminum, stainless steels, tool steels, nickel alloys, and cobalt chrome are commonly processed.
How accurate is SLM?
Accuracy of around ±0.1-0.2% is typical, with minimum feature resolution of ~100 microns.
What is the cost of SLM systems?
SLM equipment ranges from $300,000 to $1,000,000+ depending on size, capabilities, and options.
What types of post-processing are required?
Heat treating, HIP, surface finishing, and/or machining may be utilized. Support removal is also needed.
What industries use SLM additive manufacturing?
Aerospace, medical, automotive, industrial, and defense sectors are early adopters of SLM.
What materials does SLM not work well for?
Highly reflective metals like copper or gold remain challenging. Material properties for some alloys are still emerging.
What surface finishes can be achieved?
As-built SLM surface roughness ranges from 5-15 microns Ra. Finishing can further improve this.
How big of parts can you make with SLM?
Standard build volumes range up to 500mm x 500mm x 500mm. Larger machines accommodate bigger components.
Is SLM suitable for end-use production parts?
Yes, SLM is being used increasingly for final production components, with examples in aerospace and medical industries.