Nhôm là một lựa chọn vật liệu kim loại phổ biến cho sản xuất phụ gia, được đánh giá cao về tỷ lệ sức mạnh trên trọng lượng cao, khả năng chống ăn mòn tuyệt vời, tính chất nhiệt và hiệu suất cơ học. BẰNG Sản xuất phụ gia nhôm quality and printer capabilities advance, new high-value applications across aerospace, automotive, consumer products and architecture can benefit from complex aluminum part production.
This overview covers the advantages of common aluminum alloys used in AM processes like laser powder bed fusion (PBF-LB) and direct energy deposition (DED), along with their corresponding properties, post-processing procedures, applications, and leading suppliers. Comparison tables highlight the tradeoffs between different aluminum materials and AM methods.
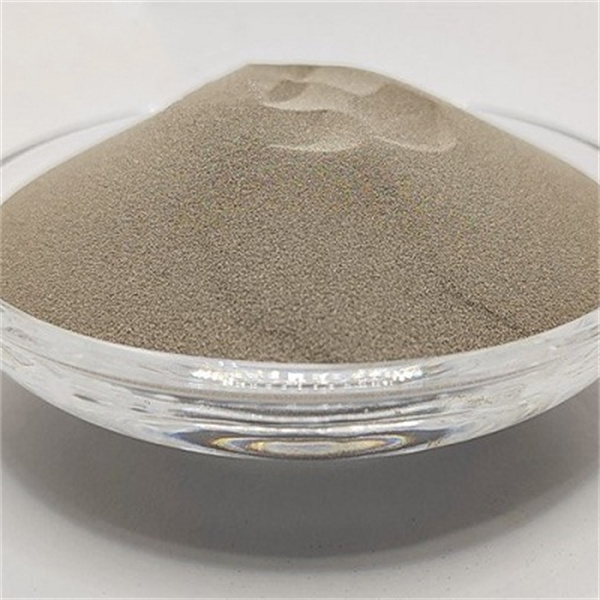
Overview of additive manufacturing aluminum
Key benefits aluminum offers for AM applications:
- Lightweight – low density helps reduce printed part weight
- High Strength – many aluminum alloys have yield strengths exceeding 500 MPa
- Excellent Corrosion Resistance – protective oxide outer layer
- High Thermal Conductivity – heat dissipation potential
- Good Elevated Temperature Properties – up to 300-400°C
- Electrically Conductive – useful for electronics applications
- Low Cost – less expensive than titanium or nickel alloys
- Recyclability – powders can be reused reducing material costs
Combined with the design freedom of AM, aluminum enables lighter, better performing components across industries. Refinements in aluminum powder production allow expanded capabilities to fabricate dense parts rivaling cast and wrought metallurgy.
Aluminum Alloy Powder Materials for AM
Aluminum alloys optimized for additive manufacturing utilize controlled powder particle production paired with intelligent alloying additions to enhance properties.
Common Aluminum AM Alloy Compositions
Hợp kim | Si% | Fe% | Cu% | Mn% | Mg% | Khác |
---|---|---|---|---|---|---|
ALSI10MG | 9-11 | & lt; 1 | <0.5 | <0.45 | 0.2-0.45 | – |
AlSi7Mg0.6 | 6-8 | & lt; 1 | <0.5 | <0.45 | 0.55-0.6 | – |
Scalmalloy® | 4-6 | 0.1-0.3 | & lt; 0.1 | & lt; 0.1 | 0.4-0.7 | Zr Sc |
C35A | 3-5 | 0.6 | 3.0-4.0 | 0.2-0.7 | 0.25-0.8 | – |
A20X | 3-5 | 0.6 | 3.5-4.5 | 0.2-0.8 | 0.05-0.5 | – |
Silicon is a common strengthener. Trace elements like Fe, Cu, Mg optimize properties. Unique alloys like Scalmalloy® use scandium-zirconium precipitate nanoparticles to achieve ultrahigh strengths exceeding wrought alloys.
Key Characteristics of Aluminum AM Alloys
Hợp kim | Sức căng | Tỉ trọng | Layer Penetration Depth |
---|---|---|---|
ALSI10MG | 400-440 MPa | 2,67 g/cc | 70-100 μm |
AlSi7Mg0.6 | 420-500 MPa | 2.66 g/cc | 60-80 μm |
Scalmalloy® | Over 550 MPa | 2.68 g/cc | 50-70 μm |
Higher strengths limit achievable single layer depth before requiring remelting cycles.
Specifications for Sản xuất phụ gia nhôm
Critical powder characteristics like flowability, particle shape and chemistry purity dictate aluminum AM processing quality.
Size Distribution Standards for Al Powder
Measurement | Typical Specification |
---|---|
Phạm vi kích thước | 15 – 45 μm |
Hình dạng hạt | Mostly spherical |
Median Size (D50) | 25-35 μm |
Tight control over particle size distribution, morphology and contamination levels ensures dense defect-free printed parts.
Chemistry Standards for Aluminum Print Powders
Yếu tố | Composition Limit |
---|---|
Oxygen (O2) | Tối đa 0,15% |
Nitrogen (N2) | Tối đa 0,25% |
Hydrogen (H2) | Tối đa 0,05% |
Limits on gaseous impurities prevent extensive porosity or internal voids in printed aluminum components.
Post-Processing Procedures for Sản xuất phụ gia nhôm
Common post-processing methods for additive manufactured aluminum parts include:
Aluminum AM Post-Processing Techniques
Điều trị nhiệt
T6 heat treatment – Solution heating & aging cycles to improve strength, hardness & ductility. Essential for highest mechanical performance with many Al alloys.
Surface Finishing
Machining, bead blasting, or polishing exterior surfaces provides dimensional accuracy and smooth surface finish. Anodizing can colorize and protect aluminum surfaces.
HIP (Hot Isostatic Pressing)
High temperature + pressure minimizes internal voids and porosity. Useful for leak-critical applications but an added process step.
Machining
CNC machining features like precision bearing surfaces or threads into net shape AM parts. Up to 60% machining reductions achieved versus traditional manufacturing.
Additive Manufacturing Techniques for Aluminum
Modern metal 3D printers leverage selective laser melting, electron beams or binder jetting to construct complex aluminum components unattainable with conventional methods.
Comparison of Aluminum AM Processes
Phương pháp | Sự miêu tả | Những lợi ích | Giới hạn |
---|---|---|---|
Powder Bed Fusion – Laser | Laser selectively fuses regions of metal powder bed | Good accuracy, material properties and surface finish | Relatively slow build speeds |
Powder Bed Fusion – Electron Beam | Electron beam melting in high vacuum | Excellent consistency, high density | Limited material options, high equipment cost |
Direct Energy Deposition | Focused heat source melts metal powder spray | Larger components, repairs | Poorer surface finish, geometry constraints |
Binder Jetting | Binder jetted to join powder particles | Very fast build speeds, lower equipment cost | Weaker mechanical performance, secondary sintering needed |
Laser based powder bed approaches offer the best all-around capabilities for most functional aluminum components today.
Aluminum AM Part Applications
The lightweight, high strength and thermal characteristics aluminum AM enables suits the demands of:
Industries Using Additive Manufactured Aluminum Parts
Không gian vũ trụ – brackets, stiffeners, heat exchangers, UAV components
Ô tô – custom brackets, powertrain, chassis and drivetrain systems
Công nghiệp – lightweight robotics and tooling, prototyping
Architecture – ornamentation, custom metallic art
Người tiêu dùng – electronics, customized products
Aluminum AM unlocks new design possibilities perfect for complex mission critical applications.
Suppliers of Aluminum Print Powders
High purity aluminum alloy powders specifically optimized for additive manufacturing processes are offered by major metallic material suppliers:
Leading Aluminum Powder Companies
Công ty | Common Alloy Grades | Typical Pricing/Kg |
---|---|---|
Ap & amp; c | A20X, A205, custom alloys | $55 – $155 |
Sandvik Osprey | AlSi10Mg, AlSi7Mg0.6, Scalmalloy® | $45 – $220 |
Công nghệ LPW | AlSi10Mg, Scalmalloy® | $85 – $250 |
HOÀN TOÀN | Alsi10mg, alsi7mg0.6 | $50 – $120 |
Prices vary based on alloy choice, powder size specs, lot quantities and certifications required.
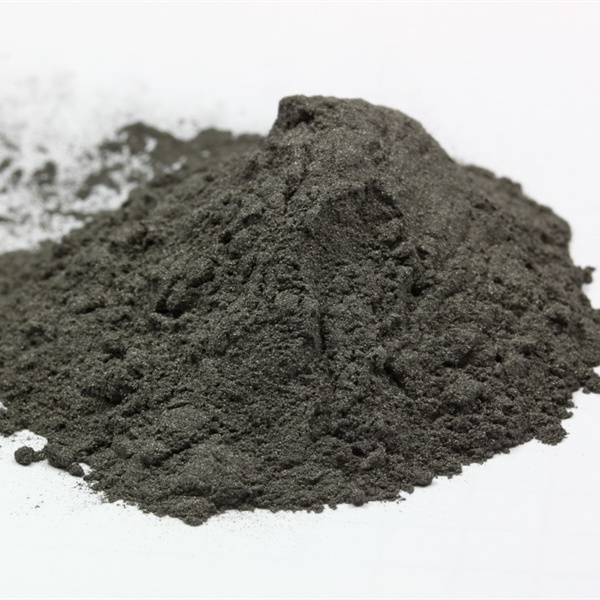
Câu hỏi thường gặp
What aluminum alloy is best suited for laser powder bed fusion AM?
AlSi10Mg offers the best all-around printability, mechanical properties and corrosion resistance for most applications with laser powder bed 3D printing of aluminum alloys.
What particle size distribution is recommended for aluminum AM powders?
A Gaussian curve with average size between 25-35 μm provides optimal powder bed density and uniform melting behavior with most common laser powder bed fusion machines.
Why is Scalmalloy considered an advanced aluminum alloy?
Scalmalloy leverages a uniform precipitation strengthened structure for unmatched strength while retaining decent elongation and fracture toughness through a novel scandium containing composition unattainable with conventional aluminum metallurgy.
Should heat treating be used post additive manufacturing with aluminum?
Yes, heat treatment improves the microstructure and enhances mechanical properties for many aluminum AM alloys. A typical T6 treatment involves solution heating followed by artificial aging resulting in significant property improvements from precipitation strengthening phenomena.
What surface finishes are possible with AM aluminum parts?
After some machining, grinding, sanding and/or polishing operations, surface roughness (Ra) values under 10 μm are attainable for additive manufactured aluminum components depending on the AM process used. More intensive finishing can provide optical grade mirror surfaces. Common finishes include anodizing as well for enhanced corrosion or wear properties combined with coloring options.