Plasma Rotating Electrode Process Powder Overview
The plasma rotating electrode process (PREP) is a unique powder production technique that utilizes a rotating electrode to generate a plasma arc. This arc melts and atomizes the electrode material, creating spherical metal powder particles with exceptional properties. PREP powders are widely used in additive manufacturing, powder metallurgy, and thermal spraying applications.
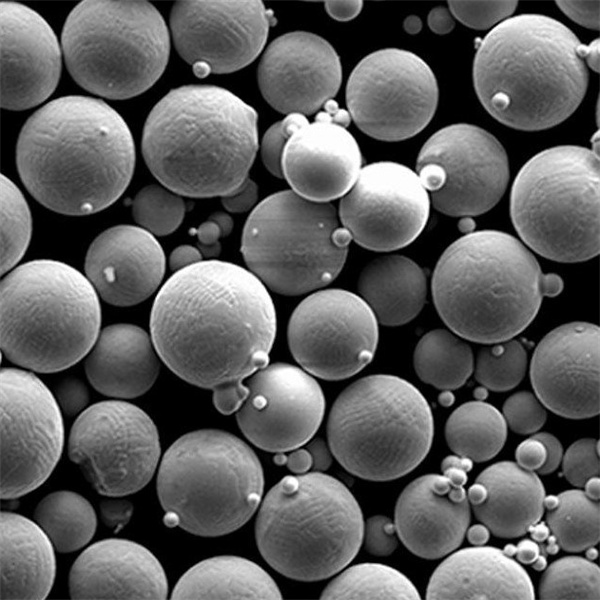
Types, Composition, and Properties of PREP Powders
Type | Composition | Properties |
---|---|---|
Titanium | Titanium, alloying elements | High strength, low density, and corrosion resistance |
Nickel-based | Nickel, chromium, cobalt, alloying elements | Corrosion resistance, high-temperature strength, and wear resistance |
Cobalt-based | Cobalt, chromium, tungsten, alloying elements | High hardness, wear resistance, and corrosion resistance |
Stainless steel | Iron, chromium, nickel, alloying elements | Corrosion resistance, high strength, and toughness |
Aluminum | Aluminum, alloying elements | Lightweight, high strength-to-weight ratio, and corrosion resistance |
Copper | Copper, alloying elements | High electrical and thermal conductivity, corrosion resistance |
Tungsten | Tungsten, alloying elements | High melting point, high density, and wear resistance |
Molybdenum | Molybdenum, alloying elements | High strength, high-temperature strength, and corrosion resistance |
Tantalum | Tantalum, alloying elements | High melting point, high density, and corrosion resistance |
Applications of PREP Powders
Application | Industry | Benefits |
---|---|---|
Additive manufacturing | Aerospace, automotive, medical | Complex geometries, lightweight components, rapid prototyping |
Powder metallurgy | Automotive, electronics, tooling | High precision, near-net-shape components, reduced waste |
Thermal spraying | Aerospace, automotive, energy | Protective coatings, wear resistance, corrosion resistance |
Friction stir welding | Aerospace, automotive, shipbuilding | High-strength welds, reduced distortion, improved fatigue life |
Metal injection molding | Electronics, medical, automotive | Complex geometries, high-volume production, near-net-shape components |
Specifications, Sizes, Grades, and Standards of PREP Powders
Specification | Description |
---|---|
Size | Particle diameter range (e.g., 10-100 microns) |
Grade | Purity level, alloy composition |
Standard | International or industry-specific standards (e.g., ASTM, ISO) |
Suppliers and Pricing of PREP Powders
Supplier | Location | Price Range |
---|---|---|
Höganäs | Sweden | $100-$350 per kilogram |
Sandvik | Sweden | $120-$360 per kilogram |
AP&C | United States | $150-$450 per kilogram |
GKN | United Kingdom | $125-$370 per kilogram |
Carpenter Technology | United States | $130-$380 per kilogram |
Met3DP | China | $80-$190 per kilogram |
Advantages and Disadvantages of PREP Powders
Advantages:
- High purity and consistency
- Spherical shape for optimal packing and flowability
- Wide range of materials and alloys available
- Excellent mechanical properties
- Reduced waste and environmental impact
Disadvantages:
- Can be more expensive than other powder production methods
- Requires specialized equipment and expertise
- May require post-processing to achieve desired properties
FAQ
Question | Answer |
---|---|
What is the difference between PREP powders and gas atomized powders? | PREP powders are typically finer and more spherical than gas atomized powders. |
What are the key factors to consider when selecting PREP powders? | Size, grade, composition, and supplier reliability. |
How can I ensure the quality of PREP powders? | By purchasing from reputable suppliers and conducting thorough testing. |
What are the emerging applications of PREP powders? | Additive manufacturing, advanced coatings, and lightweight materials. |
How can I learn more about PREP powders? | Attend industry conferences, read technical papers, and consult with experts. |