电子束增材制造 (EBAM) 是一种金属三维打印工艺,使用电子束能量源熔融材料。本指南介绍了 EBAM 系统、工艺、材料、应用、优势以及采用该技术的注意事项。
电子束增材制造简介
电子束增材制造(EBAM)是一种金属三维打印技术,它使用高功率电子束作为能源,直接根据 CAD 数据将金属原料逐层熔融成完全致密的部件。
EBAM 技术的关键属性:
- 使用电子束电源熔化材料
- 通过逐层添加金属粉末来制造零件
- 创建高密度的近网状零件
- 典型的材料包括钛、镍合金和钢
- 与其他金属 AM 工艺相比,制造量更大
- 沉积率高,可加快构建速度
- 平均零件精度为 ±0.3 毫米
- 与激光加工相比,残余应力低
- 大型复杂金属零件的理想选择
- 与减法技术相比,可减少浪费
EBAM 可实现传统制造无法实现的创新设计。然而,与任何快速成型工艺一样,在设计和应用方面也有独特的考虑因素。
如何 电子束快速成型制造 作品
EBAM 流程包括
- 沉积和平整金属粉末薄层
- 扫描电子束选择性熔化区域
- 降低构建板并重复分层/熔化
- 将完成的部件从粉末床中取出
- 根据需要进行后期处理
电子束枪在真空条件下产生聚焦光束。电子束的功率、速度、模式和其他参数都经过精确控制,以熔化材料。
EBAM 系统需要真空室、粉末处理、电子枪、控制器和其他子系统。
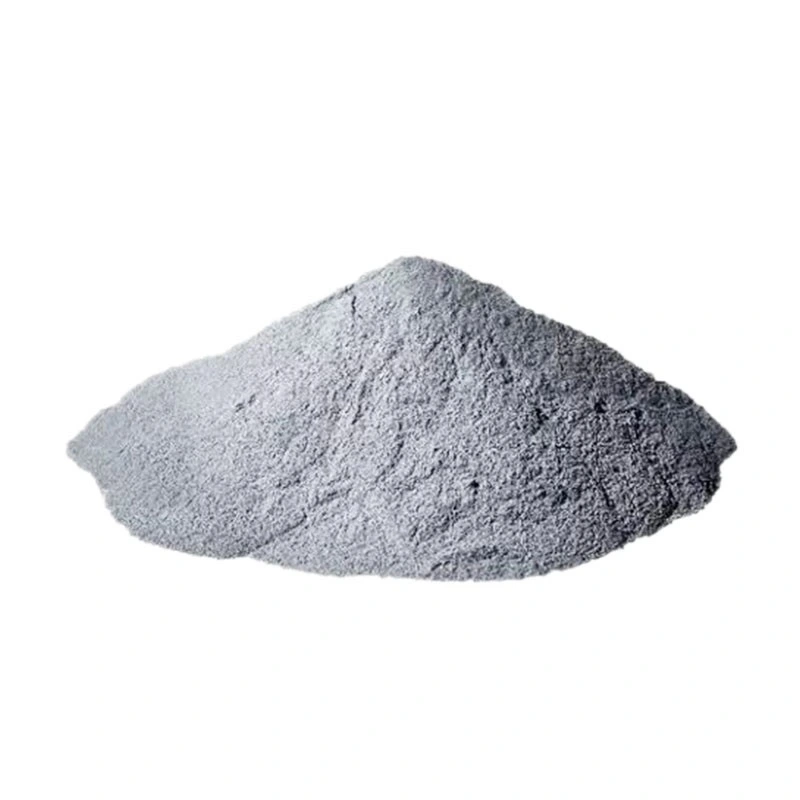
EBAM 设备制造商
全球领先的工业 EBAM 系统供应商包括
制造商 | 模型 | 建筑尺寸 | 材料 | 价格范围 |
---|---|---|---|---|
通用电气添加剂 | Arcam EBM Spectra H | 1000 x 600 x 500 毫米 | 钛、镍、钴铬、铝、铜、钢 | $1.5m - $2m |
Sciaky | EBAM 300 | 1830 x 1220 x 910 毫米 | 钛、铬镍铁合金、不锈钢 | $1.5m - $3m |
Velo3D | 蓝宝石 | 680 x 380 x 380 毫米 | 钛、铬镍铁合金 | $1m - $2m |
纳米尺寸 | DragonFly LDM | 330 x 330 x 330 毫米 | 铜 | $0.5m - $1m |
系统选择取决于生产需求、材料、精度要求和预算。与经验丰富的服务供应商合作是直接购买设备的另一种选择。
EBAM 流程特点
EBAM 涉及复杂的热、机械和材料相互作用。主要工艺特征包括
电子束 - 功率、光束直径、电流、扫描速度、聚焦
粉末 - 材料、形状、尺寸分布、层厚度
真空 - 所需的压力水平、气体杂质
温度 - 预热、熔池动力学、冷却速率
元数据 - 模板、耙系统、屏蔽
扫描策略 - 熔池模式、光束振荡
后期处理 - 热处理、HIP、机加工、精加工
要实现高质量的 EBAM 零件,了解参数之间的关系至关重要。
EBAM 设计指南
正确的 EBAM 零件设计实践包括
- 设计时考虑增材制造原理
- 使用薄壁和晶格结构减轻重量
- 尽量减少需要支撑的无支撑悬臂
- 调整部件方向,避免应力导致翘曲
- 考虑特征中的热收缩效应
- 设计几何形状,便于清除粉末
- 设计表面的功能而非外观
- 适应最小壁厚和特征尺寸
- 允许在表面对库存进行后处理
- 模拟复杂部件的构建和热效应
- 设计用于粉末床移除的夹具和接口
模拟和建模工具有助于预测残余应力和变形。
EBAM 材料
可使用以下设备加工各种金属 电子束增材制造:
类别 | 普通合金 |
---|---|
钛 | Ti-6Al-4V,Ti-6Al-4V ELI,商用纯钛 |
镍超合金 | 铬镍铁合金 718、铬镍铁合金 625、海恩 282 |
不锈钢 | 304、316、17-4ph、15-5ph |
工具钢 | H13,马氏体时效钢 |
铝质 | AlSi10Mg, Scalmalloy |
贵金属 | 黄金、白金 |
铜 | CuCrZr、铜、铜镍合金 |
钴铬合金 | 钴铬钼合金、人造卫星 |
材料性能在很大程度上取决于 EBAM 工艺参数和后处理。
EBAM 的主要应用
EBAM 可提高各行业的绩效:
行业 | 典型的 EBAM 应用 |
---|---|
航空航天 | 飞机结构、涡轮机、发射硬件 |
发电 | 热气通道组件、外壳 |
石油和天然气 | 阀门、泵、压缩机、工具 |
汽车 | 轻量化部件、热交换器 |
医疗 | 骨科植入物、手术器械 |
海事 | 叶轮、螺旋桨、复杂铸件 |
化学 | 热交换器、搅拌器、压力容器 |
与传统制造相比,其优势包括
- 购买与飞行的比例为 1:1,减少了浪费
- 通过数字化流程缩短交付周期
- 将组件组合成单一部件
- 不适合机加工的定制几何形状
- 提高复杂结构的性能
- 一旦获得认证,即可扩大生产量
EBAM 为其他方法无法实现的下一代产品设计创造了机会。
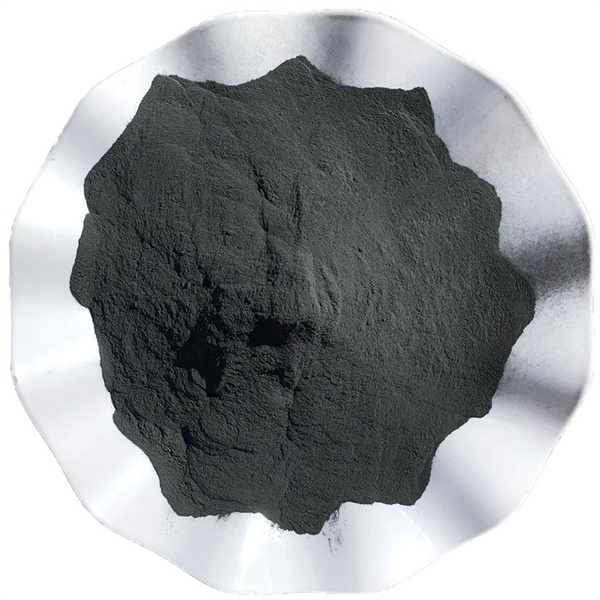
EBAM 的利弊
优势
- 大型复杂金属部件的单件加工
- 格状设计的部件强度高、重量轻
- 无需昂贵的模具或工具
- 与减法技术相比,减少了材料浪费
- 与其他 AM 工艺相比,制造速度相对较快
- 中等产量(100-10,000 件)时具有成本效益
- 通过快速凝固实现稳定的冶金效果
- 将组件组合成单一部件
- 按需生产和定制设计
- 超越加工限制的几何自由度
局限性:
- 设备成本高于聚合物三维打印
- 仅限于真空兼容材料
- 精度和表面光洁度低于机加工
- 通常需要进行后期处理才能实现特性
- 生产需要回收的废粉
- 需要进行工艺开发和试验
- 满足高功率需求的设施考虑因素
- 热应力可能导致部件变形
- 对悬挑和最小特征的限制
- 建造室围护结构的尺寸限制
在满足应用要求的情况下,EBAM 可实现高价值的产品改进。
实施 EBAM 技术
采用 EBAM 时的主要考虑因素包括
- 确定 EBAM 功能可提供优势的应用领域
- 为 EBAM 系统编制大量资本投资预算
- 制定严格的资格认证协议和标准
- 了解终端应用的监管要求
- 聘用具有粉床专业知识的人员或与服务提供商合作
- 为工艺试验和优化留出时间和资源
- 实施粉末处理程序和通风
- 提供合适的基础设施和供电能力
- 热处理等二次加工的预算
- 进行机械测试以验证性能
最适合初步试验的应用是关键性较低、风险较小的应用。
通过 EBAM 节省成本
EBAM 的商业案例取决于:
- 设备成本高,约为 $1 百万至 $3 百万美元
- 工艺开发和生产所需的劳动力
- 金属粉末原材料的成本
- 二次精加工作业
- 设施、粉末处理基础设施
- 与减法工艺相比,减少了浪费
- 将子组件合并为单一部件
- 与传统技术相比,开发时间更短
- 在产量约为 100-10,000 个零件时变得经济实惠
- 复杂几何形状的最高节约率,增加价值
制造商必须以生产效益来抵消较高的 AM 设备成本。
EBAM 与其他工艺的比较
过程 | 与 EBAM 的比较 |
---|---|
数控加工 | EBAM 可加工减法工艺无法加工的复杂几何形状。无需硬质工具。 |
金属注射成型 | EBAM 无需高昂的模具成本。材料性能优于 MIM。 |
压铸 | EBAM 的模具成本更低。没有尺寸限制。可实现非常复杂的几何形状。 |
板材层压 | 与层压复合材料相比,EBAM 可制造出完全致密的各向同性材料。 |
粘结剂喷射 | 与多孔粘合剂喷射的绿色部件相比,EBAM 可提供完全致密的最终部件。 |
SLM | SLM 的分辨率更精细,而 EBAM 的制造速度更快。两者都能制造出致密的金属零件。 |
根据应用、批量大小、精度需求和性能要求,每种工艺都具有特定的优势。
EBAM 的未来展望
在以下因素的推动下,扩大采用 EBAM 的前景一片光明:
- 生产级合金范围更广
- 更大的制造包络面可制造更大的部件
- 更快的构建速度,提高吞吐量
- 光洁度和尺寸精度得到提高
- 技术成熟,成本下降
- 前后处理进一步自动化
- 集成加工的混合系统
- 先进的过程监控系统
- 航空航天等高要求行业的资质
- 利用 EBAM 功能优化设计
随着技术的进步,EBAM 将改变各行各业的制造业。
常见问题
EBAM 使用哪些材料?
可加工钛、镍合金、工具钢、不锈钢、铝合金和贵金属。
EBAM 零件的精度和光洁度如何?
典型的尺寸精度为 ±0.3mm,表面粗糙度约为 25-125μm Ra。
EBAM 零件使用什么后处理?
可采用热处理、HIP 和机械加工。等离子喷涂也很常见。
EBAM 能生产多大的零件?
对于大型系统,常见的制造体积范围从 500mm x 500mm x 500mm 到 2m x 1m x 1m。
与减法相比,减法有哪些优势?
EBAM 可生成接近净形的零件,减少废料,并将组件合并为单一的复杂部件。
哪些行业使用 EBAM?
航空航天、能源、汽车、石油和天然气以及医疗行业是 EBAM 的早期采用者。
操作 EBAM 设备需要哪些专业知识?
需要在粉末床工艺、冶金和后处理方面经验丰富的熟练技术人员。
需要采取哪些安全预防措施?
通风、监控设备、人员防护设备和安全粉末处理至关重要。
与传统制造相比,成本如何?
对于复杂的设计,EBAM 在 100-10,000 个单位的中批量生产时才具有成本效益。
您能简要介绍一下 EBAM 流程吗?
EBAM 将金属粉末分层沉积,电子束根据 CAD 数据有选择地逐层熔化,从而制造出零件。