Titanium Ti-64 cho kim loại in 3D, abbreviated as Ti-64, is an aerospace grade titanium alloy widely used for critical additive manufacturing applications across aerospace, medical, automotive and general engineering. This guide provides a technical overview of Ti-64 powder metallurgy including composition, mechanical properties data, AM processing details, post-treatments, applications, cost analysis, product specifications, and comparisons against alternative titanium grades.
Overview of titanium ti-64 for 3d printing metal
Ti-6Al-4V (Grade 5) titanium alloy delivers an optimal balance of strength, fracture toughness and corrosion resistance combined with proven biocompatibility – making it the most ubiquitous material choice for mission-critical 3D printed metal components across industries.
As AM scales from prototyping to series production for flight-ready aerospace components plus patient-specific implants, Ti-64 has become the benchmark powder against which new materials are compared.
It offers:
- Tỷ lệ sức mạnh trên trọng lượng tuyệt vời
- High hardness and fracture toughness up to 550 MPa
- Ductility for complex geometries
- Biocompatibility and non-toxicity
- Tested pedigree spanning decades
- Available supply chain and cost-efficiencies
Continue reading for in-depth technical information on powder metallurgy approaches for fabricating 3D printed titanium Ti-64 parts.
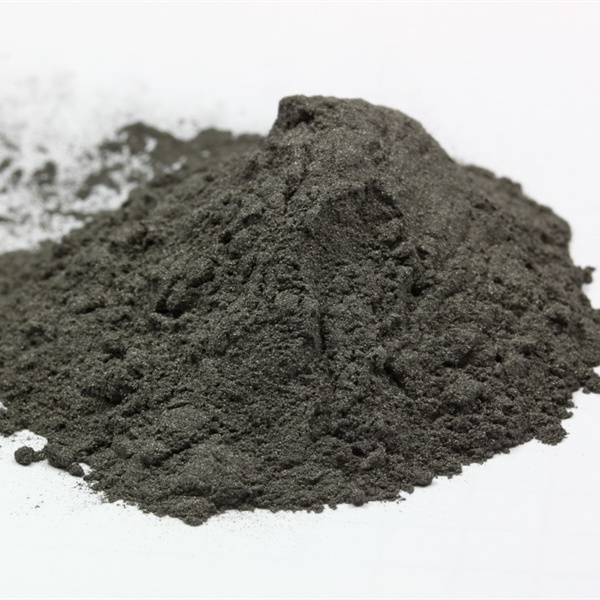
Composition and Alloy Design
The titanium Ti-64 alloy comprises predominantly titanium with aluminum and vanadium blending additions:
Yếu tố | Cân nặng % | Vai trò |
---|---|---|
Titanium (TI) | Balance, ~90% | Corrosion resistance, biocompatibility |
Nhôm (AL) | 5.5-6.75% | Sức mạnh dung dịch rắn |
Vanadi (V) | 3.5-4.5% | Phase stabilizer |
Sắt (Fe) | & lt; 0,3% | Contaminant |
Oxy (O) | & lt; 0,2% | Contaminant |
Trace elements like carbon, nitrogen and hydrogen are minimized as they degrade mechanical properties. Iron and oxygen concentrations also kept low.
The aluminium stabilizes the alpha phase while vanadium forms strengthening beta precipitates upon appropriate heat treatment. This dual phaseborgenixation imparts excellent performance.
Key Properties of Ti-64
- Yield Strength: 880 MPa
- Tensile Strength: 950 MPa
- Elongation: 14%
- Hardness: 350 Brinell
- Fatigue limit: 500 MPa
- Fracture Toughness: 75 MPa√m
- Shear Strength: 690 MPa
- Young’s Modulus: 115 GPa
- Tỉ trọng 4,43 g/cc
- Độ nóng chảy: 1604°C
These properties depend strongly on proper heat treatment discussed later. Values also vary slightly between wire-fed vs powder bed AM processes needing parameter adjustments.
Titanium Ti-64 cho kim loại in 3D Production
Medical and aerospace applications require tight controls to achieve defect-free builds so powder manufacturing follows strict specifications:
Steps | Details |
---|---|
Ingot Casting | Triple arc-melted ingot cast with tight chemistry control |
Remelting | Optional VAR or ESR purification for critical uses |
nguyên tử hóa khí | High pressure inert argon gas blast forms fine droplets |
Sàng | Multiple classification stages as per particle size distribution (PSD) standards |
Conditioning | Desiccation, blending, flow additives |
Final Testing | PSD, Hall flow rate, chemical assays, SEM imagery |
Bao bì | Moisture-proof argon filled cans or bottles |
Salient characteristics:
- Spherical particle morphology with few satellites
- Flowable powder without clumping or caking
- Controlled PSD band with majority distribution between 15 microns to 45 microns
- Chemistries conforming to ASTM F2924 and F3001 grades
- Consistent batches with repeatability data across large production volumes
- Documents traceability to source ingot castings
Such rigorous production control ensures reliable defect-free prints after validated machine parameter adjustments.
Applications of titanium ti-64 for 3d printing metal
The alloy’s biocompatibility plus high strength-to-weight ratio suit numerous critical applications:
Không gian vũ trụ
- Structural brackets, bulkheads and landing gear parts
- Turbine blades and impellers
- Aircraft interior components
Medical & Dental
- Orthopedic implants like knee, hip joints and spinal cages
- Dental abutments and bridges
- Surgical instruments requiring sterilization
Ô tô
- Lightweight pistons, connecting rod
- Luxury and racing car components including valves
Xử lý hóa học
- Corrosion resistant fluid handling parts like pipes, valves
- Food/pharma compliant filters and housings
3D printed Ti-64 also sees increasing adoption for high value industries like robotics, sporting goods and electronics thermal management leveraging design freedoms.
We next dive deeper into popular powder bed fusion techniques used to process this versatile alloy powder for mission-critical finished components.
Metal 3D Printing Using Titanium Ti-64 Powder
Both laser and electron beam powder bed technologies fuse Ti-64 to full density across a build plate layer-by-layer:
Laser Powder Bed Fusion (L-PBF)
- Selective laser melting (SLM) and direct metal laser sintering (DMLS)
- Focused high power Yb or Nd:YAG fiber lasers
- Inert argon atmosphere with oxygen levels below 500 ppm
- Real time optical monitoring of melt pools
Electron Beam Powder Bed Fusion (E-PBF)
- Powerful 60kV to 150kV electron beam in vacuum
- Ultrafast beam scanning rates above 25,000 mm/sec
- High productivity for smaller components
- Deeper penetration welds titanium more easily
For bigger parts, wire-fed directed energy deposition (DED) methods allow adding material over base structures. Multiple AM approaches enable optimizing mechanicals and surface finish.
Những lợi ích
- Complex geometries unsupported in casting or machining
- Reduced lead times and lower costs vs subtractive steps
- Minimal material wastage and buy-to-fly ratios exceeding 90%
- Consistent results across long builds once dialed in
- Design freedom enables performance gains
However to reap these, meticulous pre and post-processing is vital.
Pre and Post Processing Steps
Achieving defect-free builds involves integrated protocols:
Pre-Processing
- Parameter optimization test matrices on dedicated machines
- Monitoring powder conditions and reuse blending ratios
- Initial heat treatments to ensure uniform particle characteristics
- Careful nesting and orienting parts on the build plate
Xử lý hậu kỳ
- Removing parts from plate via wire-EDM / band sawing
- Extensive downstream machining and finishing
- Hot isostatic pressing (HIP) to eliminate internal voids
- Solutionization, aging and stabilization heat treatments
- Final quality assurance validation testing
Such comprehensive processing controls enable tapping the full potential of additive manufacturing using Ti-64 beyond relying solely just on printers.
Thông số kỹ thuật
Ti-64 alloy batches for medical or aerospace users require certification:
Tham số | Giá trị điển hình |
---|---|
Chemistry per AMS 4928 | Table above |
Phân phối kích thước hạt | D10 20μm, D50 35μm, D90 50μm |
Hình thái | Predominantly spherical + satellites |
Mật độ rõ ràng | 2.7 – 3.2 g/cc |
Chạm vào mật độ | 3.2 – 4.0 g/cc |
Lưu lượng dòng chảy | 30 – 35 sec for 50g, Hall funnel |
Surface oxygen analysis | < 2000 ppm |
Tạp chất | Fe < 3000 ppm, H< 100 ppm |
Custom sieving into tighter bands is possible but increases cost. Matching client AM machine parameters and approved quality checks ensures performance repeatability across production jobs.
Titanium Ti-64 cho kim loại in 3D Availability and Cost Analysis
Aerospace grade Ti-6Al-4V carries a cost premium over standard Ti grades thanks to specialized melting, rigorous QC testing and powder shape engineering:
SẢN PHẨM | Số lượng | Phạm vi giá |
---|---|---|
Ti-64 R&D powder | 0.5 kg | $500+ |
Ti-64 Prototyping powder | 10 kg | $150+ per kg |
Ti-64 Production powder | 1000+ kg | $50+ per kg |
Costs remain on the higher side but continue improving as AM scales up Ti-64 alloy usage allowing economy of scale manufacturing optimization. Small R&D samples can now be purchased without MOQs but production jobs require order forecasts.
Comparing Ti-64 vs Alternative Titanium Alloys
While Ti-64 has the widest adoption, other grades now vie as AM alternative options:
Hợp kim | Sức mạnh | Độ dẻo | Kháng oxy hóa | Trị giá |
---|---|---|---|---|
Ti-64 (Ti-6Al-4V) | Rất cao | Trung bình | Trung bình | $$$ |
Ti-5553 (Ti-5Al-5Mo-5V-3Cr) | Rất cao | Trung bình | Tốt hơn | $$$ |
Ti-1023 (Ti-10V-2Fe-3Al) | Cao | Cao hơn | Tốt | $$ |
Ti-48Al-2Cr-2Nb (Ti4822) | Trung bình | Brittle | Best | $$$$ |
Key Benefits of conventional Ti-64 are:
- Proven material pedigree over 30+ years
- Smoother surface finishes in AM builds
- Established heat treatment protocols
- Allowables data for design qualification
- Readily available with competitive supply
Ti-64 Limitations:
- Not the absolute highest strength titanium
- Susceptible to thermal oxidizing without controls
- Requires extensive Hot Isostatic Pressing (HIP)
Thus each exhibited tradeoffs described assist selecting optimized grades per application requirements.
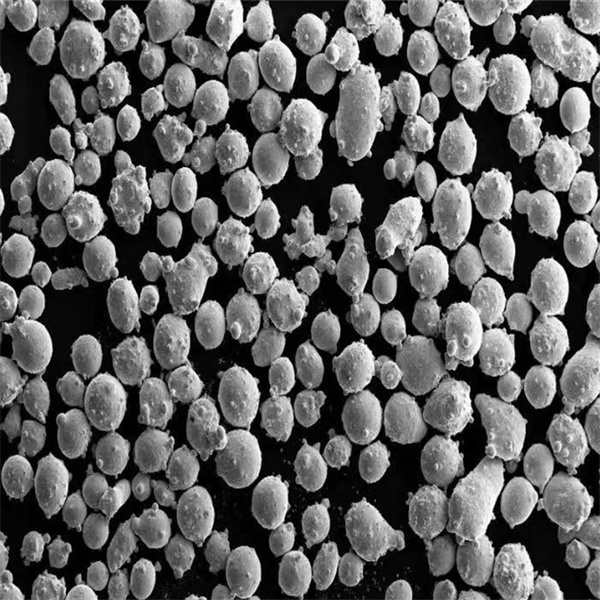
Summary
Additive manufacturing grants engineers unprecedented freedoms to design high performance titanium Ti-64 components unmatched by legacy techniques. By combining emerging digital capabilities with extensive material data validated over 30+ years aerospace and medical implementations, engineers can deploy innovative new 3D printed geometries leveraging Ti-64 benefits with reduced qualification risk. However meticulous controls still remain vital across powder manufacturing, storage handling, metal AM processing plus post-treatments to tap the full potential of this versatile high strength alloy.