Additive manufacturing (AM), also known as 3D printing, is revolutionizing production across industries. This guide provides an in-depth look at AM technologies for titanium parts, including processes, materials, applications, post-processing, quality control, and more.
Overview of Sản xuất phụ gia Titan
Titanium is a strong, lightweight metal ideal for high-performance applications like aerospace and medical. Additive manufacturing unlocks new design freedoms and customization potential with titanium.
Những lợi ích | Details |
---|---|
Complex geometries | Intricate shapes not possible with machining |
Nhẹ | Lattice structures and topology optimization |
Part consolidation | Reduce assembly parts |
Customization | Patient-specific medical devices |
Shorter lead times | Rapid production directly from design |
With falling costs and quality improvements, titanium AM adoption is accelerating.
Titanium Materials for AM
Various titanium alloys are used for additive manufacturing:
Hợp kim | Đặc trưng |
---|---|
Ti-6Al-4V (Grade 5) | Most common. Balance of strength, ductility and corrosion resistance. |
Ti-6Al-4V ELI | Extra low interstitial. Improved ductility and fracture toughness. |
Ti-5553 | High strength for aerospace components. |
Ti-1023 | Good cold formability for fasteners. |
Ti-13V-11Cr-3Al | Corrosion resistant alloy for medical use. |
Powder characteristics like particle size distribution, morphology and purity are optimized for AM processing.
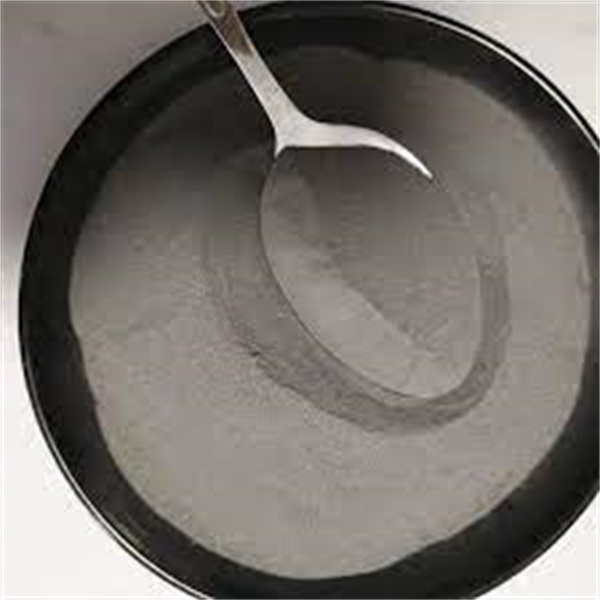
titanium additive manufacturing Process Methods
Popular titanium AM techniques:
Phương pháp | Sự miêu tả |
---|---|
Powder Bed Fusion | Laser or electron beam melts powder layers |
Directed Energy Deposition | Focused heat source melts metal powder or wire |
Binder Jetting | Liquid bonding agent selectively joins powder particles |
Each process has specific advantages depending on the part application and requirements.
Metal Powder Bed Fusion
A powder bed is selectively melted by a heat source layer-by-layer:
Kiểu | Details |
---|---|
Laser Powder Bed Fusion (L-PBF) | Uses laser for melting. Higher resolution. |
Tia điện tử tan chảy (EBM) | Electron beam heat source. Faster build rates. |
L-PBF allows finer features while EBM enables higher productivity. Both produce near-full density parts.
Directed Energy Deposition
Focused thermal energy is used to melt metal powder/wire to deposit material layer-by-layer:
Phương pháp | Nguồn nhiệt |
---|---|
Laser Metal Deposition | Laser beam |
Sản xuất phụ gia chùm tia điện tử | Chùm tia điện tử |
Laser Engineered Net Shaping | Laser beam |
DED is often used to repair or add features to existing components.
Binder Jetting Process
Liquid bonding agent selectively joins layers of metal powder:
- Powder spreading – New layer of powder spread over build platform
- Binder jetting – Printhead deposits binder in desired pattern
- Bonding – Binders bonds powder particles together
- Additional drying, curing and infiltration steps are used to achieve full density
Binder jetting produces porous “green” parts that require sintering and infiltration to densify. It offers high-speed printing.
AM Parameters for Titanium
Key AM process parameters for titanium:
Tham số | Phạm vi điển hình |
---|---|
Độ dày lớp | 20-100 m |
Laser power (L-PBF) | 150-500 w |
Tốc độ quét | 600-1200 mm/s |
Beam size | 50-100 μm |
Khoảng cách nở | 60-200 μm |
Optimizing these parameters balances build speed, part quality, and material properties.
Post-Processing of Sản xuất phụ gia Titan Parts
Common post-processing steps:
Phương pháp | Mục đích |
---|---|
Support removal | Remove support structures |
Surface machining | Improve surface finish |
Drilling and tapping | Add screw holes and threads |
Nóng isostatic nhấn | Eliminate internal voids and porosity |
Surface treatments | Improve wear/corrosion resistance |
Post-processing tailors the parts to meet final application requirements.
Applications of titanium additive manufacturing
Key application areas for titanium AM parts:
Ngành công nghiệp | Sử dụng |
---|---|
Không gian vũ trụ | Structural brackets, engine parts, UAV components |
Thuộc về y học | Orthopedic implants, surgical instruments |
Ô tô | Lightweight auto parts, custom prototypes |
Hóa chất | Corrosion resistant fluid handling parts |
Dầu và khí | Valves, pumps for corrosive environments |
AM enables innovative titanium component designs across demanding industries.
Quality Control for titanium additive manufacturing Parts
Critical quality checks for titanium AM parts:
- Dimensional accuracy – Measure against design using CMMs and 3D scanners.
- Độ nhám bề mặt – Quantify surface texture using profilometers.
- Độ xốp – X-ray tomography to check for internal voids.
- Thành phần hóa học – Confirm alloy grade using spectrometry techniques.
- Tính chất cơ học – Conduct tensile, fatigue, fracture toughness testing.
- Non-destructive testing – X-ray, ultrasound, penetrant testing.
- Cấu trúc vi mô – Metallography and microscopy to check for defects.
Comprehensive testing validates part quality for functional performance.
Global Suppliers of Sản xuất phụ gia Titan
Leading suppliers of titanium AM services and systems:
Công ty | Vị trí |
---|---|
Phụ gia GE | Hoa Kỳ |
Velo3D | Hoa Kỳ |
3D Systems | Hoa Kỳ |
Trumpf | nước Đức |
EOS | nước Đức |
These companies offer a range of titanium AM equipment, materials, and part production services.
Phân tích chi phí
Titanium AM part costs depend on:
- Part size – Larger parts require more material and build time.
- Production volume – High volumes distribute costs over more parts.
- Vật liệu – Titanium alloys have higher material costs than steels.
- Post-processing – Additional processing steps increase costs.
- Buy vs outsource – AM system acquisition costs vs. contract manufacturing costs.
Titanium AM is economically viable for low volume complex parts. It competes against subtractive methods like CNC machining.
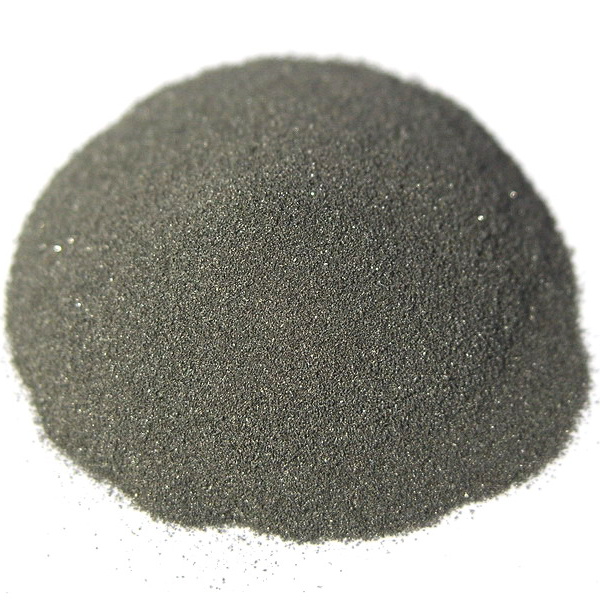
Challenges of titanium additive manufacturing
Some ongoing challenges with titanium AM include:
- High residual stresses can cause part distortions and defects.
- Achieving consistent mechanical properties comparable to wrought materials.
- Anisotropic material behavior depending on build orientation.
- Limited size capability compared to other manufacturing methods.
- Process inconsistencies between AM machines and repeatability issues.
- High upfront system costs and material pricing.
- Lack of qualified operators and subject matter experts.
However, ongoing advances are helping overcome many of these limitations.
Future Outlook for titanium additive manufacturing
The future outlook for titanium AM is positive:
- Expanding range of alloys and material options specially formulated for AM.
- Larger build volumes enabling bigger parts and higher productivity.
- Improved quality, surface finish, material properties closer to wrought materials.
- Developments in in-situ inspection, process monitoring and control.
- Hybrid manufacturing combining AM with CNC machining and other methods.
- Growth across aerospace, medical, automotive, and industrial gas turbine sectors.
- Broader adoption as AM system costs decrease and expertise increases.
Titanium AM has huge potential to transform supply chains across multiple industries as the technology continues maturing.
Choosing a Titanium AM Service Bureau
Here are tips when selecting a titanium AM service provider:
- Review their specific experience and examples with titanium parts.
- Look for complete end-to-end capabilities including post-processing.
- Evaluate their quality systems and certifications like ISO and AS9100.
- Assess their engineering support and design for AM knowledge.
- Consider location and logistics for fast turnaround.
- Understand their AM equipment capabilities and capacity.
- Compare pricing models (per part, volume discounts etc.).
- Check lead times and on-time delivery track record.
- Review customer testimonials and satisfaction levels.
Choosing the right partner ensures high quality parts delivered on time and on budget.
Pros and Cons of Titanium AM
Advantages and limitations of titanium AM:
Ưu điểm
- Design freedom enables complex geometries.
- Lightweighting through lattices and topology optimization.
- Faster prototyping and limited production runs.
- Consolidate assemblies into single parts.
- Customized medical devices tailored to anatomy.
- Reduced material waste compared to machining.
Nhược điểm
- Relatively high production costs compared to other processes.
- Limitations on maximum part size.
- Post-processing often required to improve finish.
- Anisotropic material properties.
- Standards and codes still in development.
- Specialized expertise required for design and processing.
For low-to-medium volumes of complex titanium parts, AM is a game changing technology despite some persistent limitations as the technology matures.
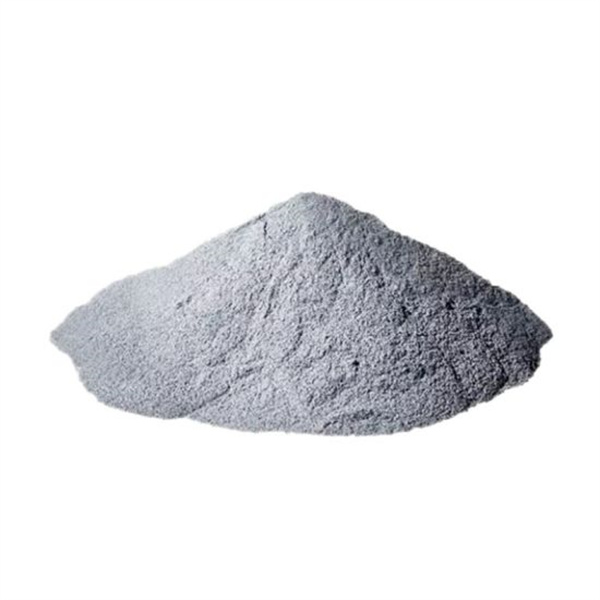
Câu hỏi thường gặp
Questions | Answers |
---|---|
Which AM process is best suited for titanium? | Powder bed fusion like DMLS and EBM allow full melting to achieve near wrought properties. |
Does titanium AM require any support structures? | Yes, most titanium AM processes require removable support structures. |
What post-processing is typically needed for titanium AM parts? | Most parts need support removal, machining, and often hot isostatic pressing. |
What industries use titanium AM the most? | Aerospace, medical, automotive, and oil and gas are leading adopters of titanium AM. |
What material properties can be expected with titanium AM? | With optimal parameters, properties approach 90-100% of wrought materials. |
Phần kết luận
Titanium additive manufacturing enables breakthrough designs and lightweight components across aerospace, medical, automotive, and other high-value sectors. As the technology continues to mature, broader titanium AM adoption can be expected across more industries to transform supply chains and enable next-generation products.