Quá trình điện cực xoay plasma (PREP) là một công nghệ xử lý vật liệu tiên tiến, sử dụng các vòng cung huyết tương và lực ly tâm để sản xuất vật liệu hiệu suất cao. Phương pháp sáng tạo này kết hợp các lợi ích của việc tan chảy hồ quang plasma và đúc ly tâm, cho phép sản xuất vật liệu với các đặc tính vượt trội so với các tuyến xử lý thông thường.
Overview of the Plasma Rotating Electrode Process
The plasma rotating electrode process utilizes a rotating graphite electrode that is surrounded by a plasma arc. As the electrode rotates, feed-stock material is continuously melted by the plasma arc and flung off the tip of the electrode due to centrifugal forces. The molten material solidifies and is collected, producing a finished part or ingot.
Some of the key benefits of PREP technology include:
- Rapid melting and solidification rates, enabling refined microstructures
- Production of alloys difficult or impossible to make with conventional methods
- Ability to process reactive materials without contamination
- In-situ alloying and microstructure control
- Near net shape capabilities, minimizing machining
Compared to other plasma melting methods, the rotating electrode provides additional control over the thermal conditions during processing. This enables tailored solidification conditions to optimize the microstructure and properties of the finished material.
The plasma source provides extremely high temperature capabilities exceeding 10,000°C, enabling melting of any material. By adjusting the plasma power and other parameters, the thermal conditions can be precisely controlled. This allows for flexibility in designing alloys and processing conditions.
plasma rotating electrode process (PREP) technology for 3D printing applications:
- Bạn-shal-hv, Ti-6Al-7Nb – Excellent strength-to-weight ratio and biocompatibility
- Very fine powders with controlled particle size distribution
- ALSI10MG, AlSi12 – Low density with good strength and corrosion resistance
- Spherical morphology with high powder flowability
- Inconel 718, Inconel 625 – Outstanding high temperature properties
- Dense 3D printed parts with fine microstructure
Thép công cụ
- H13, P20, 420 stainless – High hardness, wear and corrosion resistance
- Capable of complex geometries for mold and die components
- Vonfram, tantalum, molybdenum – Extremely high melting points
- High density powders suitable for radiation shielding
Copper alloys
- CuCrZr, CuNi2SiCr – Excellent thermal and electrical conductivity
- Used for thermal management applications
Hợp kim coban-chrom
- CoCrMo, CoCrW – Biocompatibility and high strength
- Low internal porosity with optimized parameters
The spherical powders produced via PREP enable high density 3D printed parts with excellent mechanical properties suitable for demanding applications in aerospace, medical, tooling, and more.
Hệ thống hợp kim | Example Alloys | Key Properties | Các ứng dụng |
---|---|---|---|
Hợp kim Titan | Ti-6Al-4V, Ti-6Al-7Nb | High strength-to-weight ratio, biocompatibility | Không gian vũ trụ, y tế |
Hợp kim nhôm | AlSi10Mg, AlSi12 | Low density, good strength and corrosion resistance | Automotive, consumer products |
Superalloys niken | Inconel 718, Inconel 625 | Excellent high temperature properties | Turbine blades, rocket nozzles |
Thép công cụ | H13, P20, 420 stainless | Độ cứng cao, hao mòn và chống ăn mòn | Injection molds, dies |
Refractory alloys | Tungsten, tantalum, molybdenum | Extremely high melting points | Radiation shielding, high temp furnace parts |
Copper alloys | CuCrZr, CuNi2SiCr | Độ dẫn điện và điện cao | Electronics cooling, connectors |
Hợp kim coban-chrom | CoCrMo, CoCrW | Biocompatibility, high strength | Medical implants, dental crowns |
Equipment Used in Plasma Rotating Electrode Processing
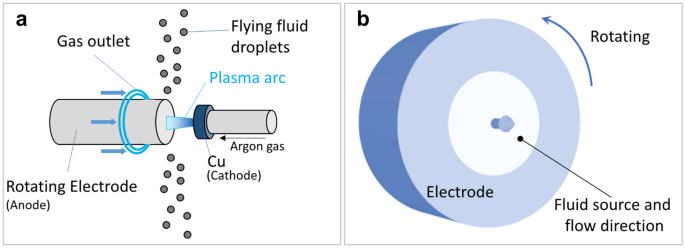
The main components used in the plasma rotating electrode process include:
Plasma Torches
- Typically transferred arc torches delivering 10-100 kW of power
- Provides the high temperature plasma arc to melt the feed material
- Various plasma gases can be used – argon, nitrogen, hydrogen, helium
Rotating Electrode
- Usually made of graphite for high temperature capabilities
- Diameter and length depends on part size
- Rotates at speeds up to 3000 rpm
- Water-cooled to handle high thermal load
Mold
- Graphite or copper mold to shape the depositing material
- Water-cooled to rapidly solidify the molten material
- Centrifugal forces project the material to the mold walls
Power Supplies
- DC power supply to operate the plasma torch
- Can be operated in hot or cold cathode mode
- Currents ranging from 100-1000 A depending on plasma torch
Vacuum Chamber
- Provides controlled atmosphere for plasma arc
- Vacuum or inert gas environment
Control System
- Computerized control of plasma parameters
- Rotation speed
- Material feed rate
- Automated production
How the Plasma Rotating Electrode Process Works
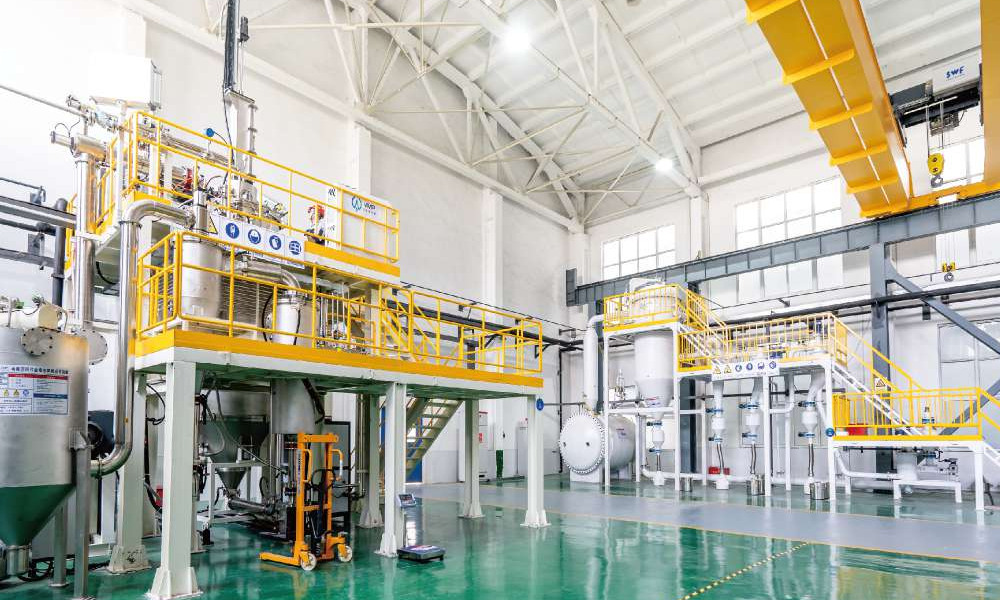
The plasma rotating electrode process combines centrifugal casting and plasma arc melting into one integrated system. Here is an overview of how PREP works:
- Feedstock insertion – The electrode is rotated at a high speed up to 3000 rpm. Feedstock material such as alloy powder is injected into the molten pool on the rotating electrode tip.
- Melting – The plasma arc from the surrounding plasma torch(es) melts the inserted feedstock and areas of the rotating electrode surface. Temperatures exceed 10,000°C ensuring rapid melting.
- Molten material ejection – The centrifugal forces generated by the fast rotation cause the molten material to be flung off the electrode tip. This forms droplets that travel outwards.
- Deposit formation – The ejected molten material impacts the water-cooled copper mold placed around the electrode. The droplets rapidly solidify to gradually form a deposit.
- Tailored solidification – The high heat transfer rate provided by the mold enables controlled directional solidification. This allows optimizing the deposit structure.
- Deposit collection – Once fully formed, the molded deposit is removed from the chamber. This may be an ingot, near net shape part, or other product morphology.
- Automated operation – The PREP system is fully automated with computer control. It can run unattended to build up substantial quantities of material.
- Parameter flexibility – Variables like plasma power, electrode rotation speed, and material feed rate can be adjusted to tailor the deposit characteristics.
Unique Capabilities of Plasma Rotating Electrode Processing
The plasma rotating electrode process provides some unique capabilities that differentiate it from other materials processing methods:
Rapid Solidification Rates
- Solidification rates exceeding 100,000°C/s are possible
- Enables formation of non-equilibrium phases and metastable structures
- Refines grain sizes down to the nanoscale
Net Shape Fabrication
- Deposits can be molded to near net shape reducing machining
- Complex part geometries can be directly produced
- Eliminates additional processing steps
Reactive Material Processing
- The plasma arc confinement allows reactive materials to be processed without contamination
- Highly reactive alloys like titanium aluminides can be produced
Thermal Control
- The rotating electrode provides additional control over the thermal conditions
- Enables tailored non-equilibrium cooling rates for microstructure control
In-Situ Alloying
- Alloying additions can be fed into the molten pool during processing
- Enables flexibility in designing and producing new alloys
Clean Processing Environment
- Vacuum chamber provides controlled atmosphere
- No crucibles are needed reducing potential contamination
Alloy Systems Processed with PREP
Hệ thống hợp kim | Sự miêu tả |
---|---|
Titanium aluminides | Intermetallic alloys based on Ti and Al with high temperature properties |
Bulk metallic glasses | Amorphous alloys with high strength and hardness |
Metal matrix composites | Reinforced with particles for high strength and stiffness |
Superalloys | Ni, Fe, or Co based alloys with excellent creep resistance |
Thép công cụ | Iron based alloys with high hardness and wear resistance |
Refractory metals | Ultra-high melting point metals like W, Mo, Nb, Ta |
The plasma rotating electrode process is capable of producing a wide range of alloys systems including:
Titanium Aluminides
- Intermetallic alloys based on Ti and Al
- Excellent high temperature properties with low density
- Used for aerospace and automotive applications
Bulk Metallic Glasses
- Amorphous alloys with superior strength and hardness
- High cooling rates enable metallic glass formation
- Excellent engineering materials and coatings
Metal Matrix Composites
- Reinforced with carbides, oxides, or other particles
- Excellent specific strength and stiffness
- Used for aerospace, automotive, and semiconductor parts
Superalloys
- Nickel, iron, or cobalt based alloys with outstanding creep resistance
- Used for high temperature structures in turbines and engines
Thép công cụ
- Iron based alloys with high hardness and wear resistance
- Used for cutting tools, molds, dies, and other applications
Refractory Metals
- Ultra-high melting point metals like tungsten, molybdenum, niobium, tantalum
- Used for high temperature applications due to retention of strength
Microstructure and Property Enhancement
One of the main advantages of PREP is the ability to create advanced microstructures that impart enhanced properties. Some examples include:
Grain Refinement
- Extremely fine nanoscale grains can be produced
- Results in increased strength according to the Hall-Petch relationship
Extended Solid Solubility
- Solute trapping via rapid solidification expands solid solubility
- Alters alloying behavior allowing new compositions
Non-Equilibrium Phases
- Metastable phases can be retained at room temperature
- Provides precipitation strengthening and alters properties
Particle Reinforcement
- In-situ formation of nanoscale precipitates and particles
- Excellent strengtheners and refiners of grain size
Elimination of Segregation
- No chemical segregation due to rapid solidification
- Improves alloy homogeneity and eliminates defects
Improved Interfaces
- Rapid solidification enables interfaces free of contaminants
- Strengthens grain boundaries and interphase interfaces
Advantages of Plasma Rotating Electrode Processing
Some of the major advantages of PREP technology include:
- Versatility – Capable of processing virtually all alloy systems
- Superior microstructures – Achieves significant grain refinement and microalloying
- Near net shape – Complex geometries can be directly fabricated
- Efficiency – Automated hands-off operation with high productivity
- Chất lượng – Provides clean processing environment and eliminates defects
- Performance – Produces alloys with outstanding mechanical properties
- Novel alloys – Enables development of unique metastable compositions
- Cost effectiveness – Reduces raw materials waste and machining requirements
Compared to other processing methods, PREP enables new possibilities for alloy development and optimized materials performance.
Applications of Alloys Produced by PREP
The alloys fabricated using the plasma rotating electrode process have found usage in a diverse range of demanding applications:
Các thành phần hàng không vũ trụ
- Turbine blades, disks, casings from nickel and titanium alloys
- Requires high strength and creep resistance at elevated temperatures
Cutting Tools
- Drill bits, end mills, saw blades using tool steel alloys
- Must withstand wear, impact, and heat during machining
Biomedical Implants
- Titanium or stainless steel alloys for orthopedic implants
- Kháng ăn mòn tuyệt vời và khả năng tương thích sinh học
Phụ tùng ô tô
- Engine components, drivetrain from aluminum, magnesium, and titanium alloys
- Lightweighting and performance under extreme conditions
Sporting Goods
- Golf clubs, bicycles, and high-end gear using advanced alloys
- High strength-to-weight ratio required
Thiết bị điện tử
- Heat sinks cut from beryllium composites
- Requires thermal management capabilities
Nuclear Applications
- Reinforced materials used in nuclear reactors
- Must maintain performance under radiation
Applications of Alloys Produced by PREP
Ngành công nghiệp | Ứng dụng |
---|---|
Không gian vũ trụ | Turbine components |
Cutting tools | Drill bits, saw blades |
Y sinh | Cấy ghép |
Ô tô | Engine and drivetrain parts |
Đồ thể thao | Clubs, bicycles, gear |
Thiết bị điện tử | Heat sinks |
Hạt nhân | Components for reactors |
Current Research on Plasma Rotating Electrode Processing
There are a number of areas of research being conducted to further advance PREP technology:
- Modeling of the complex plasma-material interactions
- Incorporation of novel and recycled materials as feedstock
- Multi-electrode configurations for large part production
- Hybrid PREP processes combined with additive manufacturing
- Development of new measurement diagnostics
- Joining dissimilar alloys to create metal matrix composites
- Exploring carbon nanotube reinforcement
- Economic and life cycle analyses of the process
Continued research will enable further process improvements, a wider range of alloys, and new applications. Government agencies and private companies are actively invested in advancing plasma rotating electrode processing.
Future Outlook for PREP Technology
The plasma rotating electrode process represents an innovative leap in materials processing technology. Ongoing developments and adoption by industry will enable next generation high performance alloys.
Several trends point to a bright future for PREP:
- Demand for specialized advanced alloys in diverse industries is increasing. PREP allows alloy compositions unachievable by conventional methods.
- Net shape and additive manufacturing is gaining wider utilization. PREP has near net shape capabilities surpassing other methods in alloy flexibility and quality.
- High throughput automated production is essential for competitiveness. PREP achieves hands-off automated operation with high productivity.
- Quality requirements for critical components are becoming more stringent. PREP offers a high precision, clean, and controlled processing environment.
- Alloys with enhanced engineered microstructures have exceptional performance. PREP unlocks metastable structures with unique properties.
With these drivers, PREP is poised to become an essential technology for next generation alloy production across numerous sectors. Continued rapid growth is expected in this exciting field.
Frequently Asked Questions About Plasma Rotating Electrode Processing:
Here are some common FAQs about the plasma rotating electrode process:
What are the main advantages of PREP technology?
Some key advantages are rapid solidification rates enabling advanced microstructures, near net shape fabrication, flexible alloying capabilities, clean processing environment, and automated production.
What materials can be processed by PREP?
Virtually any alloy system can be processed including titanium, aluminum, magnesium, nickel, cobalt, iron, tool steel, and refractory alloys. Nanocomposites and amorphous alloys are also possible.
How does PREP compare to other additive manufacturing methods?
PREP enables higher temperature alloys, finer grain structures, and avoids some issues with porosity and anisotropy. But PREP has limited geometries compared to powder bed fusion processes. The two are complementary.
What industries utilize alloys made by PREP?
Aerospace, biomedical, automotive, sporting goods, electronics, and nuclear industries take advantage of alloys from PREP. The technology is also used to make cutting tools.
What are some limitations of PREP technology?
The size of parts made is restricted by the electrode diameter. Complexity of part geometry is also limited compared to some other additive methods. Initial system costs are relatively high.
What new advancements are being made in PREP?
Some current research areas include multi-electrode systems, hybrid processes with additive manufacturing, advanced modeling, new in-situ diagnostics, and alloy development.
How does PREP improve the microstructure and properties of alloys?
Grain refinement, retained metastable phases, solute trapping, elimination of segregation, improved interfaces, and tailored solidification conditions result in enhanced alloy performance.
What expertise is required to operate a PREP system?
Specialized training is recommended to learn how to properly run PREP equipment. Knowledge of metallurgy and plasma physics is also beneficial to getting the most out of the technology.