Molybdenum metal powder is a refractory material valued for its high temperature properties combining strength, thermal conductivity and corrosion resistance. This guide covers molybdenum powder manufacturing processes and characteristics plus molybdenum alloying and applications. It also details product specifications, pricing, suppliers, advantages versus alternatives along with expert recommendations for usage.
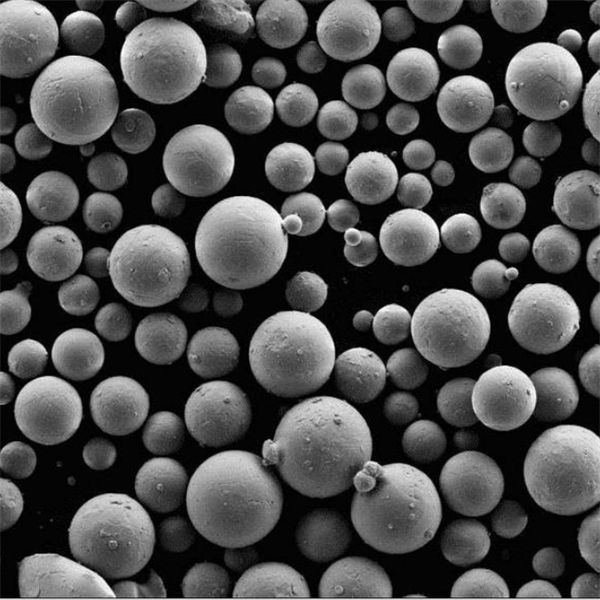
Tổng quan
Essential properties of pure metallic molybdenum powder include:
- Excellent high temperature strength up to 2100°C
- Retains tensile strength even at high heat
- Very low thermal expansion coefficient
- Thermal and electrical conductivity
- Resists erosion and corrosion
- Enables lightweight constructive materials
Molybdenum powders see demand growth for thermally loaded structures like heat shields, rocket nozzles, filaments and composite reinforcements where extreme conditions exceed traditional alloys. This report explores production methods, cost drivers, application areas and processing guidance around molybdenum powders.
Composition and Characteristics
Molybdenum metal powder comprises just the single pure metallic element:
Chemical Formula | MO |
---|---|
Atomic Number | 42 |
Atomic Weight | 95.95 g/mol |
Tỉ trọng | 10.28 g/cc |
Độ nóng chảy | 2623 ° C. |
Boiling Point | 4639°C |
Salient characteristics:
- Silver-white luster when freshly powdered
- Ductile with high thermal shock resistance
- Near-net-shape capable for manufacturing
- Can be alloyed with carbon, silicon or boron
- Resists acids and alkaline corrosion
- Retains mechanical strength across temperatures
These useful combinations of chemical, physical and mechanical properties spur applications. But availability was limited until the last decade by difficulties producing pure molybdenum metal powder affordably.
Phương pháp sản xuất
Advances now enable commercial production of molybdenum metal powders via:
Phương pháp | Sự miêu tả | Kích thước hạt | Sự thuần khiết |
---|---|---|---|
Điện phân | MoO3 dissolved in aqueous solution reduced at cathode | 50 μm | High 99.95%+ |
Giảm calciother | Reducing molybdenum trioxide using calcium | 150 μm | Moderate 98% |
Giảm hydro | Solid state reduction of MoO3 using dry hydrogen | Submicron | High 99.9% |
Hình cầu huyết tương | Spheroidize irregular molybdenum flakes | 15 to 150 μm | Moderate 98% |
- Electrolysis and hydrogen processes allow high purity
- Reduction methods offer lower cost for most applications
- Post-process plasma spheroidization improves powder properties
Ongoing initiatives target more efficient dry processes eliminating hydrometallurgy to improve economics for mainstream adoption.
Refractory Material Applications
Unique molybdenum metal powder properties suit extreme demands:
High Temperature Structural Components
- Rocket nozzles, missile parts
- Nuclear fusion reactor elements
- Furnace hearths and hardware
- Vacuum tube filaments
Thermal Management
- Heat dissipation plates with ceramic matrix
- Thermal spray coatings on pipes and tools
Composite Blends
- Dispersion strengthened alloy reinforcements
- Spark plasma sintered cermets
Electrical Contacts
- Vacuum switchgear electrodes
- Relay contacts resisting arc erosion
Metallization Pastes
- Conductive thick films printed circuits
- Joining agent in transient liquid phase Diffusion Bonding
Molybdenum powder thus punches above its niche weight class in value-added applications rather than pure commodity volumes.
Product Specifications
Molybdenum metal powder is commercially available in standardized or custom variations:
Tham số | Giá trị điển hình |
---|---|
Kích thước hạt | 1 μm to 150 μm |
Sự thuần khiết | 98% to 99.95% molybdenum |
Hình thái | Angular, spheroidal |
Mật độ rõ ràng | 4 to 6 gm/cc |
True Density | 10.2 gm/cc |
Diện tích bề mặt cụ thể | 0.2 to 2 m2/g |
Hàm lượng oxy | < 0.1 wt% |
Powder Flow Rate | Fair, improves with conditioning |
Oxit bề mặt | Present but thin native layer |
Phân phối kích thước hạt – Match client processing method, tensile strength vs ductility targets.
Purity grades – 99.9% sufficient for most applications. Higher purity adds cost.
Conditioning – Blending, dry lubing and desiccation improves powder packing and flow properties.
Application-specific customization of powder characteristics is possible but requires MOQs.
Molybdenum Metal Powder Pricing
As a specialized powder produced in small batches serving niche sectors, costs trend higher than mainstream metals:
Số lượng | Price ($ per lb) |
---|---|
1 lb | $50+ |
10 lbs | $35+ |
100 lbs | $25+ |
500 lbs+ (Mo ingot) | $5+ lb |
Research grade purities above 99.95% attract steep premiums for 1 gram packs priced ~$200+ per gram.
Material costs dominate for small sintered or AM printed parts – so applications must justify values. Allows lightweighting, insulation and conductivity combinations otherwise unachievable.
Comparison Versus Alternatives
Molybdenum competes against specialty metals and composites targeting high temperature properties:
Vật liệu | Dẫn nhiệt | Độ nóng chảy | Tỉ trọng | Trị giá |
---|---|---|---|---|
Molypden | 138 W/(m.K) | 2622°C | 10.28 g/cc | $$$ |
Vonfram | 173 W/(m.K) | 3422 ° C. | 19.35 g/cc | $$ |
Tantalum | 57 W/(m.K) | 2996 ° C. | 16.6 g/cc | $$$$ |
Molybdenum DiSilicide | N/A | 2035°C | N/A | $$ |
Tungsten Carbide | 66 W/(m.K) | 2870°C | 15.63 g/cc | $$ |
Than chì | Up to 1500 | 3652°C | 2.26 g/cc | $ |
Molybdenum Pros
- Unrivaled high temperature tensile strength up to 2100°C
- Lower density enables lightweight high temp structures
- Resists molten metal corrosion during extreme processing
Thách thức
- Difficult to fully densify powder to full shape
- Brittle intermetallics can emerge compromising ductility
- Very high melting point makes alloying and joining difficult
- Powder production economics need further improvement
With ongoing improvements in powder processes, molybdenum dominates extreme service niches. Blending with carbon/boron aids sintering and alloying additions customize properties across temperature requirements.
Research and Development Directions
Emerging molybdenum powder improvements include:
Production
- Electrolytic routes using molten salts
- Lower energy molybdenite roast/reduction
- Microwave plasma spheroidization
Alloy Design
- HEA composites with tungsten/tantalum
- Liquid phase sintering additions like Cu/Ni
- Rate dependent strengthening mechanisms
Consolidation
- Flash spark plasma sintering
- Lattice structures with topology optimization
- Binder jet printed green state debinding
Các ứng dụng
- Solid state battery electrolytic plate replacements
- 3D printed rocket thruster prototypes
- Creep resistant glass seal ferrule Bushings
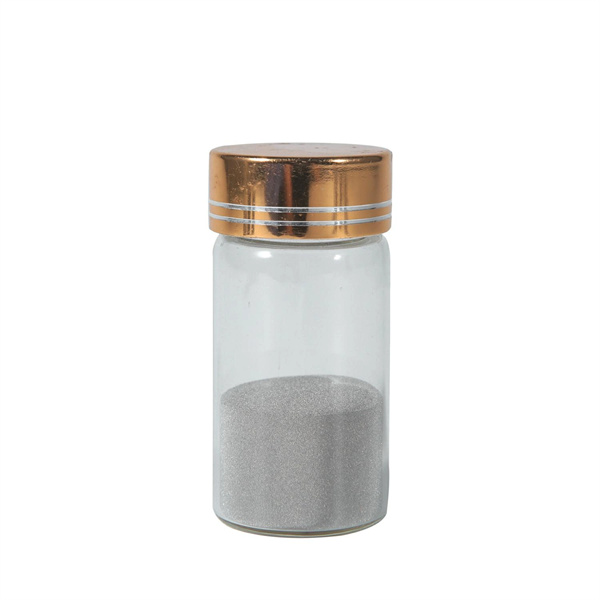
Summary
Molybdenum’s rare refractory properties including high temperature strength, thermal conduction, corrosion resistance and ductility enable innovative lightweight components and composites unlocking performance advancements across extreme thermal management applications in nuclear fusion, space travel and industrial processing. Recent powder metallurgy improvements now allow complementing traditional molybdenum mill forms with additive manufacturing methods. Matching particle size and morphology to desired densification approaches allows fabricating previously unviable shapes. Though relatively more expensive than conventional metals, molybdenum punches far above its niche weight class in specialized thermal niches outpacing alternatives.