Overview of molybdenum alloy power
Molybdenum alloy powder is an important material for industrial metal 3D printing applications such as tooling, aerospace, oil and gas, and optics.
Key characteristics of molybdenum alloy powder:
Thuộc tính | Sự miêu tả |
---|---|
Cường độ nhiệt độ cao | Retains strength up to 1300°C |
Dẫn nhiệt | On par with steel, 2-3X that of titanium |
Chống ăn mòn | Excellent resistance to acids and chlorides |
Common alloys | Mo-Ti, Mo-TiB2, Mo-La2O3, Mo-ZrO2 |
Các ứng dụng | Tooling, aerospace, optics, nuclear |
Molybdenum’s high melting point, strength, and thermal properties make it highly valued for printed parts working under extreme temperatures. It offers new design possibilities over traditional molybdenum processing.
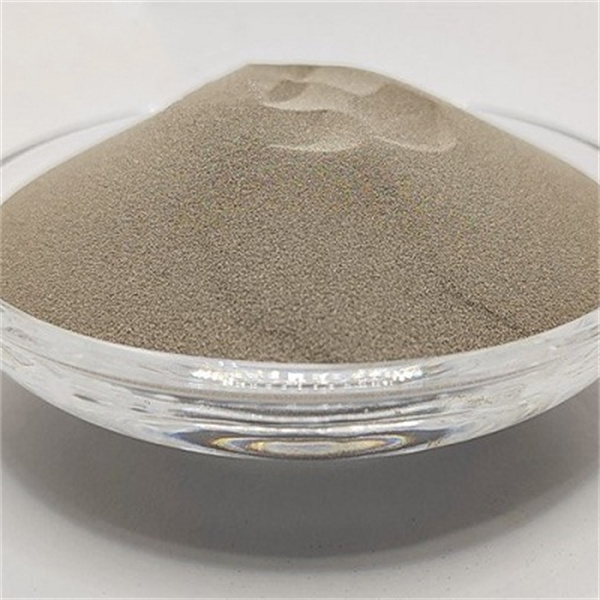
Applications of molybdenum alloy power
The unique properties of molybdenum alloys make them suitable for:
Ngành công nghiệp | Các ứng dụng |
---|---|
Dụng cụ | Plastic injection molds, extrusion dies, forming tools |
Không gian vũ trụ | Leading edges, thrust nozzles, engine components |
Quang học | Mirrors, precision optics, substrates |
Hạt nhân | Plasma facing components, heat shields |
Dầu và khí | Downhole tools, valves, wellhead parts |
3D printing facilitates complex molybdenum-based components with conformal cooling channels and lightweight lattices not possible with conventional methods.
Some specific applications taking advantage of molybdenum alloys include:
- Injection molds with conformal cooling to reduce cycle times
- Leading edges on hypersonic vehicles to withstand intense heating
- Mirror substrates that resist thermal distortion
- Aerospace thruster nozzles with integrated cooling channels
- Downhole drilling components needing strength and corrosion resistance
Molybdenum alloys enable lighter, higher performance metal parts across industries.
Popular molybdenum alloy power for Metal AM
Common molybdenum alloys used for metal powder bed fusion 3D printing include:
Hợp kim | Đặc trưng | Các ứng dụng |
---|---|---|
Mo-Ti | High strength, 1200°C use | Không gian vũ trụ, hạt nhân |
Mo-La2O3 | Khả năng chống leo tuyệt vời | Aerospace, optics |
Mo-ZrO2 | Fracture toughness, ductility | Industrial, tooling |
Mo-TiB2 | Hardness, wear resistance | Tooling, optics |
Mo-Re | Cường độ nhiệt độ cao | Nuclear, aerospace |
The high melting point of molybdenum allows a wide range of alloying additions to tailor properties like hardness, strength, ductility, and corrosion resistance as needed.
molybdenum alloy power Characteristics
Molybdenum alloy powder for metal AM has the following characteristics:
Tham số | Details |
---|---|
Hình dạng hạt | Spherical, some satellites allowed |
Kích thước hạt | 15-45 microns typical |
Phân bố kích thước | D10, D50, D90 within tight ranges |
Khả năng chảy | Excellent flow, not agglomerated |
Mật độ rõ ràng | Over 4 g/cc |
Sự thuần khiết | High purity, low oxygen preferred |
Gas atomization is commonly used to produce the spherical molybdenum alloy powder ideal for powder bed fusion printing.
Controlling composition and minimizing impurities like oxygen are critical to achieve target material properties in the printed parts.
Metal 3D Printer Requirements
Printing molybdenum alloy parts requires robust industrial metal printers with:
System | Typical Specification |
---|---|
Năng lượng laser | 300-500W |
Build volume | 250 x 250 x 300 mm minimum |
Khí trơ | Argon preferred over nitrogen |
Precision optics | 50 micron minimum spot size |
Powder handling | Closed-loop metal powder system |
Operational software | Facilitates production rather than prototyping |
The high melting point of molybdenum alloys requires sufficient laser power density and gas protection. Automated powder handling systems improve productivity and powder recyclability.
Metal 3D Printing Process Parameters
Typical laser powder bed fusion process parameters for molybdenum alloys:
Tham số | Range |
---|---|
Năng lượng laser | 250-500 W. |
Tốc độ quét | 400-1200 mm/s |
Khoảng cách nở | 80-180 μm |
Độ dày lớp | 20-100 m |
Beam diameter | 50-100 μm |
Shielding gas | Argon, 0-5% hydrogen mixtures |
Lower porosity and higher densities are achieved with higher laser power density and finer hatch spacing.
Process optimization is needed to balance density against residual stresses and cracking tendencies for each molybdenum alloy.
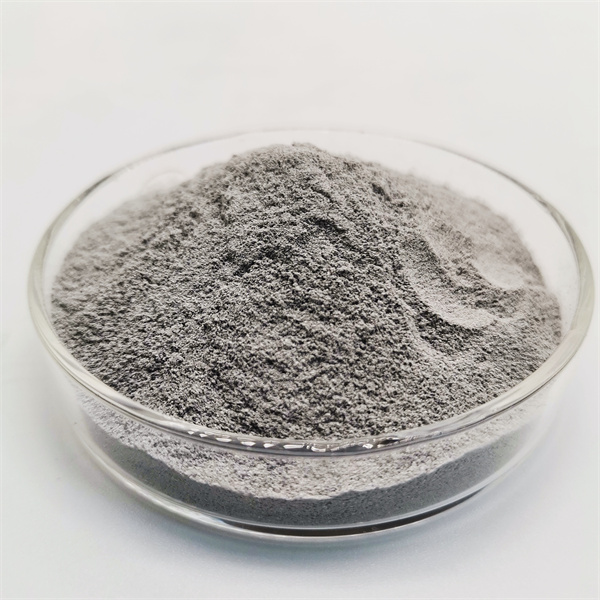
Metal 3D Printing Design Guidelines
Key design principles for molybdenum alloy parts:
Design Aspect | Hướng dẫn |
---|---|
Wall thickness | 1-2 mm minimum thickness |
Overhangs | 45-60° minimum without supports |
Surface finish | As-printed is rough, post-process if needed |
Residual stress | Careful scanning strategies and annealing |
Hỗ trợ | Careful design to minimize use of supports |
The high stiffness of molybdenum alloys makes residual stress management critical. Simulation software is needed to optimize scanning patterns and support structures.
Mechanical Properties of Printed molybdenum alloy power
Typical mechanical properties of printed molybdenum alloys:
Hợp kim | Density (g/cc) | Strength (MPa) | Hardness (HV) |
---|---|---|---|
Mo-Ti | 9.9 | 700-900 | 350-450 |
Mo-La2O3 | 10.1 | 850-1050 | 400-500 |
Mo-ZrO2 | 9.8 | 600-800 | 300-400 |
Mo-TiB2 | 9.5 | 650-850 | 400-600 |
Mo-Re | 10.5 | 900-1100 | 350-450 |
Property ranges depend on composition, process parameters, and heat treatment. Molybdenum alloys achieve exceptional performance at high temperatures.
Support Structures for Printing molybdenum alloy power
Support structures are often needed when printing molybdenum alloy parts:
- Overhangs greater than 45° typically require supports
- Dense support blocks or sparse support lattices can be used
- Low contact area supports recommended to minimize surface defects
- Careful orientation minimizes need for supports
- Soluble PVA or break-away plastic supports available
Minimizing use of supports reduces surface defects and post-processing time. The high stiffness of molybdenum leads to support structures detaching more easily.
Common Defects in Printed molybdenum alloy power
Potential defects when printing molybdenum alloys:
Defect | Cause | Prevention |
---|---|---|
Độ xốp | Low powder density, lack of fusion | Optimize process parameters |
Cracking | Residual stresses | Modify geometry, scanning, supports |
Warping | Thermal stresses | Preheat substrate, stress relieve |
Độ nhám bề mặt | Unmelted particles, balling | Adjust power, speed, focus |
Anisotropy | Directional microstructure | Optimize build orientation |
Defects can be minimized through careful parameter selection, powder spread, scan strategy, and orienting parts optimally on the build plate.
Post-Processing Methods
Typical post-processing steps for printed molybdenum alloy parts:
Phương pháp | Mục đích |
---|---|
Support removal | Removing support structures from part |
Surface finishing | Improving surface finish |
Nóng isostatic nhấn | Removing internal voids, improve density |
Heat treatment | Relieving residual stresses |
Joining | Welding multiple printed components |
The as-printed microstructure and mechanical properties of molybdenum alloys can also be tailored through heat treatment. This enhances properties like ductility and fracture toughness.
Qualification Testing
Thorough testing needed to qualify printed molybdenum components:
Phương pháp kiểm tra | Typical Requirements |
---|---|
Density analysis | > 99% of wrought material |
Tensile testing | Meet minimum strength and ductility specs |
Cấu trúc vi mô | Consistent, defect-free grain structure |
Hardness testing | As required for application |
Impact testing | Minimum impact energy for fractures |
Non-destructive evaluation like CT scanning helps identify any internal voids or defects present.
Selecting a molybdenum alloy power Nhà cung cấp
Key factors when selecting a molybdenum alloy power supplier:
Nhân tố | Criteria |
---|---|
Quality systems | ISO 9001 or AS9100 certified |
Powder characterization | Provides particle size distribution and morphology data |
Process control | Tight control of gas atomization process |
Specialization | Focus on gas atomized alloys tailored for AM |
Technical support | Application engineers to assist product development |
Customer references | Case studies for AM applications |
Choosing a supplier with powder specifically optimized for AM will provide the best printing results.
Cost Analysis of Printed Molybdenum Alloy Parts
Cost factors for molybdenum alloy printed parts:
- High cost of molybdenum powder – $350-700/kg
- Printer productivity affects cost per part
- Material utilization rates of 30-50%
- Labor for post-processing steps
- Additional costs for HIP, machining, heat treat
Cost model factors:
- Printer purchase investment – $500,000+
- Low-moderate build rates – 5-15 cm3/hr
- Moderate-high material
Cost Advantages vs. Traditional Processing
Benefits of printing molybdenum alloys vs. traditional methods:
sản xuất phụ gia | Traditional Processing | |
---|---|---|
Thời gian dẫn đầu | Days | Weeks |
Design freedom | Complex geometries, lattices | Design restrictions |
Customization | Easily adapted designs | Difficult process changes |
Consolidation | Integrated, printed assemblies | Multiple manufacturing steps |
Material waste | Near net shape, low waste | High material removal |
For low to medium volumes, AM is more cost-effective. Traditional methods have advantages for high volumes.
Sustainability Benefits of Metal 3D Printing
Sustainability benefits of printing molybdenum alloys:
- Reduce material waste by only using required powder
- Enable lightweight, optimized designs through topology optimization
- Localized production reduces transportation emissions
- Powder recycling further improves sustainability
- On-demand production avoids over-production waste
- Consolidated parts decrease downstream processing
The technology promotes more sustainable approaches to engineering design and manufacturing.
Applications Taking Advantage of Molybdenum Alloys
Key applications benefiting from molybdenum alloy power:
Ứng dụng | Những lợi ích |
---|---|
Injection molds | High temperature strength, conformal cooling |
Aerospace thrusters | Withstands 2300°C exhaust temperatures |
Aircraft leading edges | High temperature capability during hypersonic flight |
Nuclear fusion reactors | Tolerates extreme neutron radiation |
Optical mirrors | Resists thermal distortion |
3D printing facilitates complex geometries not possible with wrought molybdenum parts.
Trends and Developments in molybdenum alloy power
Emerging trends in molybdenum alloy powders:
- New alloy compositions tailored for AM properties
- Larger batch sizes produced for economy of scale
- Tighter controls of powder characteristics and quality
- Improved recyclability of powders
- Declining costs through increased production volumes
- Wider range of available particle size distributions
- Increased competition among suppliers
- More supply chain localization outside China
The powders are becoming more optimized and economical as the AM market expands.
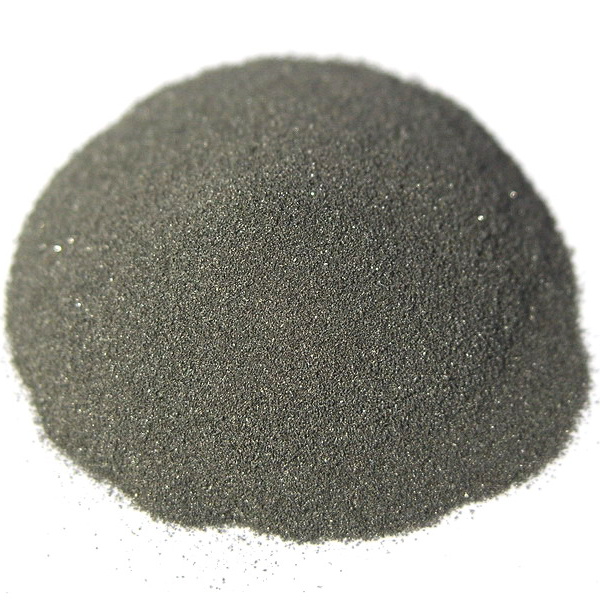
Summary of molybdenum alloy power for Metal AM
- Essential for high temperature, corrosion resistant printed parts
- Requires high power density printers with inert atmospheres
- Careful process control needed to minimize defects
- Provides performance improvements over conventional molybdenum
- Applications across tooling, aerospace, energy, optics
- High material costs but lower total part costs
- Improved powders and supply chain availability emerging
Molybdenum alloys will enable lighter, higher performance metal additively manufactured components across demanding industrial applications.
Câu hỏi thường gặp
Question | Answer |
---|---|
What particle size is recommended for molybdenum alloys? | 15-45 microns typically, depends on alloy and application. |
What printers can process molybdenum alloys? | High power systems from EOS, Concept Laser, Trumpf, GE Additive. |
What finish can be obtained on printed surfaces? | As-printed is rough at 10-15 μm Ra. Machining can achieve under 1 μm. |
What post-processing is typically required? | Support removal, stress relieving, hot isostatic pressing, machining. |
How recyclable are the powders? | Powders can generally be reused 5-10 times before refresh. |