mim additive manufacturing refers to an industrial process to produce small, complex metal parts at high volumes. A composite metal powder feedstock is molded into a green-state shape using injection molding equipment, debound, and then sintered to achieve full density.
MIM leverages the geometric flexibility of polymer injection molding and green-forming with the performance capability of metal alloys. With additive manufacturing processes expanding options, this guide covers MIM compositions, properties, applications, specifications, process flows, suppliers, tradeoffs, and FAQs.
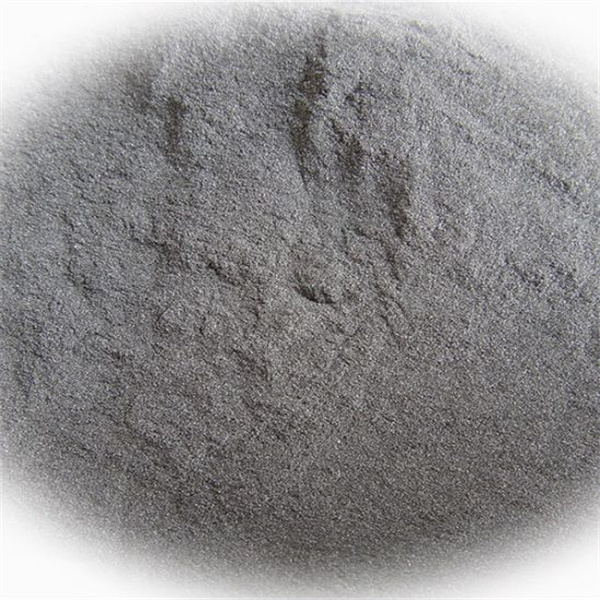
Composition of MIM Alloys
Many compositions are available as MIM feedstocks:
Vật liệu | Common Alloys | Tổng quan |
---|---|---|
Thép không gỉ | 316L, 17-4PH, 420 | Corrosion resistant, high hardness, for medical uses |
Thép công cụ | H13, P20 | High strength, heat resistance, for molded tooling |
Aluminum alloy | 2024, 6061, 7075 | Lightweight, high strength-to-weight ratio |
Titanium alloy | Bạn-shal-hv | Lightweight with corrosion resistance and high strength for aerospace uses |
Nickel alloy | Inconel 625 and 718 | Heat/corrosion resistance suited for turbo machinery |
Vonfram | WHA, WC | Extremely high density perfect for balancing applications |
Both standard and custom formulations are available depending on needs.
Properties of mim additive manufacturing
In addition to composition tailored to performance requirements, key resulting properties include:
Tài sản | Sự miêu tả |
---|---|
Tỉ trọng | Ranges from near pure metal density to greater than 95% theoretical density |
Sức căng | 250 MPa to over 1300 MPa depending on reinforcement strategies |
Độ cứng | Up to 70 HRC achieved based on alloy choice |
Chống ăn mòn | Varying resistance levels possible based on compositions selected |
Độ nhám bề mặt | As molded <6 μm Ra up to <0.2 μm Ra after plating/polishing |
Complex geometry | Molding allows intricate shapes unachievable with other processes |
Feature resolution | Small slots, holes, threads down to ~100 μm » achievable |
Wall thickness | As low as ~0.25 mm walls molded based on geometry |
Tolerances | Tighter tolerances than metal AM, typical ±0.3% of dimensions |
These capabilities make MIM suitable for end-use precision components.
Applications of MIM Additive Manufacturing
MIM’s geometric flexibility and tailored composition suit various industries:
Ngành công nghiệp | Component Examples |
---|---|
Ô tô | Gears, rocker arms, turbocharger components |
Không gian vũ trụ | Turbine blades, impellers, nozzle guide vanes |
Firearms | Triggers, safeties, slides, ejectors, muzzles |
Medical/Dental | Scalpel handles, forceps, skull plates, crowns |
Dầu và khí | Valve parts including bodies, stems, actuators |
Micro Electronics | Shields, connectors, pins, spacers, actuators |
MIM also helps create tooling inserts capable of mass production molding/forming operations.
MIM Feedstock Specifications
Feedstock properties require careful control for tolerance and feature capability:
Tham số | Typical Specification | Phương pháp kiểm tra |
---|---|---|
Powder particle size | 3 – 20 μm | Nhiễu xạ laser |
Powder loading | >55 vol% | Phân tích nhiệt lượng |
Powder apparent density | 2.5 – 4 g/cm3 | Hall Flowmeter |
Chạm vào mật độ | >4 g/cm3 | Tapping volumeter |
Viscosity curve | Shear rate dependent | Capillary rheometry |
Pellet size distribution | 2 – 4 g sensitive to shape | Sàng |
These specifications promote mold flow while ensuring green-body and sintered strength.
Overview of the MIM Manufacturing Process
- Develop composite feedstock with desired powder + binder system
- Pelletize feedstock for precision volumetric shot control
- Injection mold parts with tight tolerances and surface finish
- Chemically debind and remove polymer content
- Sinter pellets at >92% theoretical density
- Machine features as needed if geometry allows
- Apply supplementary plating, heat treating, coating, etc. if necessary
- Quality assurance testing and validation for production
This continues to be optimized for reliability at high volumes.
MIM Equipment and Feedstock Suppliers
Công ty | Nguyên vật liệu | Khả năng |
---|---|---|
BASF | Wide range of MIM alloys | Complete quality feedstocks |
Sandvik Osprey | 316L, 17-4PH, more | Atomization expertise transferred to MIM |
MPP | Tool steels, stainless steels, custom | Leading MIM equipment too |
CN Innovations | Custom alloys | Specialists in novel compositions |
Parmatech Corp | Ti alloys, tool steels, Fe alloys, exotics | Equipment and feedstocks |
Suppliers offer complementary equipment like molding machines and furnaces to enable turnkey production.
Tradeoffs When Considering MIM AM
Pros:
- Highly complex geometries and assemblies consolidated
- Excellent mechanical properties from uniform fine grains
- Great surface finish resolution as molded
- Proven mass production scalability once qualified
- Low wasted raw material relative to metal printing
- Leverages existing injection molding know-how
Cons:
- High up front costs for feedstock formulation and tooling
- Intensive qualification for new parts and applications
- Limited size range to under several pounds
- Restricted to alloys available as powders
- Generally lower ultimate strength than forgings
- Per-part cost higher than other processes until >10k volume
MIM hits the sweet spot for small complex metal components with its established track record.
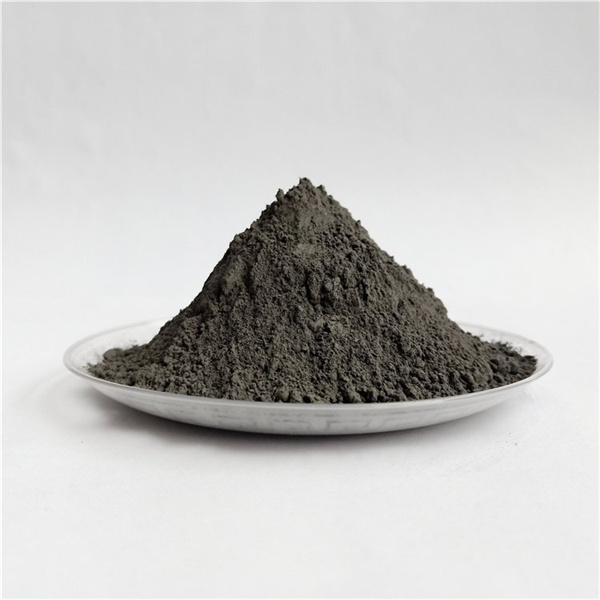
Các câu hỏi thường gặp
How small of features can MIM practically mold?
Typical lower range limits fall around 100-150 microns for hole diameter and mold wall thicknesses around 0.3 mm (~12 thou), thinner in certain geometries.
What determines the size range limits for MIM parts?
General difficulty handling thin-walled shapes over approximately 5” flow length without sagging or distortion. Maximum thickness typically under 0.5” and weights up to 5 pound range.
Does MIM allow functionally graded (FGM) composites?
Yes, advanced molding processes now support tailored porosities or spatially graded multi-powder feedstocks within a single molded component during manufacturing.
How many alloys are commercially available as MIM feedstocks?
Over 60+ base formulations exist – 300 series stainless steels comprise over 50% of the total market, followed by tool steels, titanium alloys, and nickel superalloys seeing growth.
What finishing processes typically follow MIM?
Common secondary operations include barrel finishing/vibratory deburring, surface grinding, shot peening, laser marking, passivation, plating, heat treating, joining, and inspection.