3D printing with metal powders is transforming manufacturing across industries from aerospace to medical. This guide provides a comprehensive overview of metal powders for 3D printing including alloy types, powder production methods, key properties, applications, specifications, process considerations, supplier landscape, costs, and FAQs. It serves as a technical reference for engineers exploring adoption of metal powder-based additive manufacturing.
Introduction to Bột kim loại cho in 3D
3D printing, also known as additive manufacturing (AM), builds up components layer-by-layer from digital models. Using metal powder feedstock enables industrial-scale 3D printing in engineering-grade materials.
Benefits of metal powder-based AM include:
- Complex geometries not possible with machining
- Customized designs with mass customization potential
- Reduced waste compared to subtractive methods
- Shorter development times for prototyping
- Consolidation of assemblies into single printed parts
- High strength and thermal stability results
- Just-in-time manufacturing potential
Metal powders uniquely enable 3D printing of dense, high performance metal components across aerospace, medical, automotive, and industrial applications.
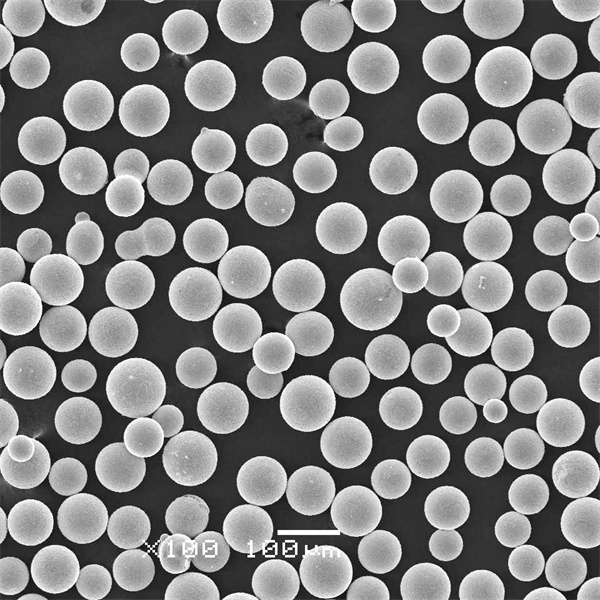
metal powder for 3d printing Types for AM
A range of metals and alloys are used as powder feedstock for 3D printing. Common options include:
Vật liệu | Key Properties |
---|---|
Thép không gỉ | Corrosion resistance, high strength |
Tool Steel | Extreme hardness, wear resistance |
Titan | Tỷ lệ sức mạnh trên trọng lượng cao |
Nhôm | Lightweight, high conductivity |
Nickel Alloys | Heat resistance, toughness |
Cobalt chrome | Biocompatibility, hardness |
By selecting optimized alloys, material properties like hardness, strength, ductility, and wear resistance can be tailored for printed parts.
Phương pháp sản xuất bột kim loại
Common production methods for 3D printing powders include:
- nguyên tử hóa khí – Inert gas turns molten alloy into spherical droplets. High purity and flowability.
- Nguyên tử plasma – Very high heat plasma melts alloy into fine spheres. Clean internal structure.
- Hợp kim cơ học – Ball milling synthesizes alloys from elemental blends. Nanostructured particles.
Gas atomization is the dominant method, allowing economic high volume production of spherical powders ideal for most AM processes.
How Metal Powders Enable 3D Printing
In powder bed fusion 3D printing, metal powder is selectively melted by a heat source layer-by-layer:
Powder Bed Fusion AM
- Powder spread into thin layer
- Laser or electron beam melts powder pattern
- Next layer powder spread over previous
- Repeated layer-by-layer until complete
- Unfused powder supports part
- Excellent dimensional accuracy and surface finishes
Fine spherical powder allows dense packing for high resolution printing. Particle size distribution must be matched to printer requirements.
Metal Powder Specifications for AM
Key powder characteristics for 3D printing include:
Metal Powder Specifications for AM
Tham số | Giá trị điển hình |
---|---|
Kích thước hạt | 10-45 micron |
Hình dạng hạt | Hình cầu |
Phân bố kích thước | D10, D50, D90 |
Khả năng chảy | Measured in seconds/50g |
Mật độ rõ ràng | 2,5-4,5 g / cm3 |
Chạm vào mật độ | Up to 80% solid density |
Sự thuần khiết | 98-99% |
Surface Oxides | Less than 1% by weight |
These properties directly impact powder packing, spreading, laser absorption, powder reuse, and final part properties.
Metal Powder Size Distribution
Particle size range must match the printer requirements:
Particle Size Ranges for AM
Kiểu | Phạm vi kích thước |
---|---|
Fine Powder | 15-25 micron |
Medium Powder | 25-45 micron |
Coarse Powder | 45-75 micron |
- Finer powders allow higher resolution and surface finish
- Coarser powders have better flow and reduced dusting
Ideal size distribution depends on printer make and model. Custom distributions optimize performance.
How to Select Metal Powder for AM
Key considerations for metal powder include:
- 3D Printer – Compatible size range, ideal morphology
- Material Properties – Mechanical, physical, post-processing needs
- Tiêu chuẩn chất lượng – Powder analytics, consistency lot-to-lot
- Lead Time and Availability – Standard alloys vs custom orders
- Số lượng – Bulk discount pricing at higher volumes
- Supplier Capabilities – Range of materials and expertise
Work closely with reputable powder producers and printer OEMs to identify the optimal material for application needs.
Metal Powder Suppliers for AM
Leading global suppliers of quality metal powders for AM include:
Metal Powder Suppliers for AM Industry
Nhà cung cấp | Vật liệu chính |
---|---|
Ap & amp; c | Titanium, titanium aluminide, nickel alloys |
Phụ gia thợ mộc | Stainless steels, tool steels, cobalt alloys |
Sandvik Osprey | Stainless steels, nickel alloys, titanium |
HOÀN TOÀN | Titanium, Niken, Cobalt hợp kim |
Công nghệ LPW | Titanium, aluminum, steels |
AMG Superalloys UK | Titanium aluminide, nickel alloys |
These companies offer extensive technical expertise in both alloys and AM processes. Some are vertically integrated to produce, characterize, and even 3D print with their powders.
Metal Powder Pricing for 3D Printing
As a specialty material, metal printing powders are more costly than traditional metal powders. Pricing factors:
- Thành phần – More expensive alloys mean higher powder prices
- Sự thuần khiết – Tighter chemistry control raises costs
- Phương pháp sản xuât – Specialty methods cost more than atomization
- Phân bố kích thước – Finer grades are more expensive
- Số lượng – Bulk orders over 1000 kg offer discounted pricing
Typical Metal Powder Price Ranges for AM
Vật liệu | Giá mỗi kg |
---|---|
Thép không gỉ | $25-$100 |
Tool Steel | $50-$150 |
Titan | $100-$500 |
Nickel Alloys | $50-$500 |
Cobalt chrome | $100-$300 |
Get current pricing from shortlisted suppliers when sourcing materials for AM production.
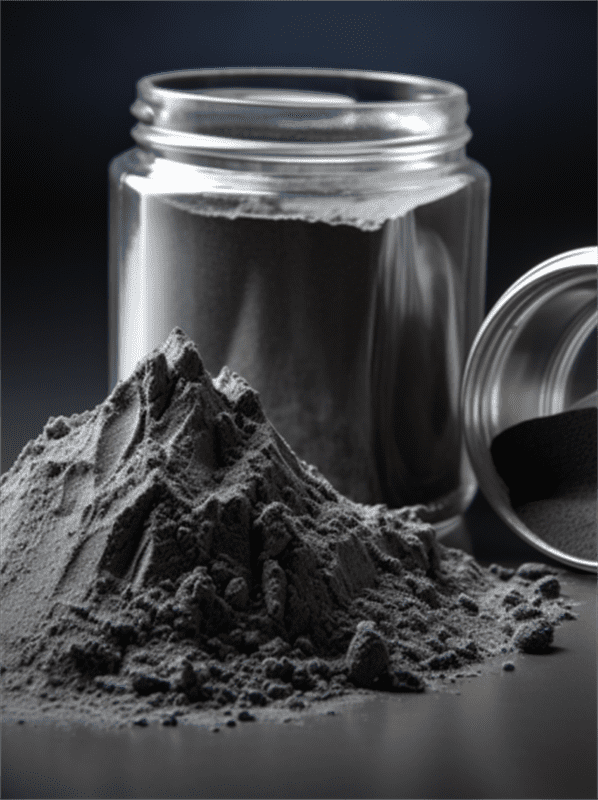
Process Considerations for Metal AM Powders
Success with metal 3D printing powders requires attention to:
- Moisture Control – Dry powder prevents hydrogen embrittlement
- Recycling – Reuse unmelted powder up to ~20 times if handled properly
- Sàng – Classify and sieve powder before reuse
- Fresh Powder Ratios – Blend with 10-30% fresh powder for reuse
- Handling – Inert environment, grounded containers
- Kho – Sealed containers, climate controlled space
- Safety – Explosion risks require mitigation controls
Follow all powder safety precautions and printer OEM recommended procedures.
The Future of Metal Powder AM
Emerging developments in metal powder 3D printing include:
- New alloys and composites for improved material properties
- Faster print times through multi-laser and higher power systems
- Larger print envelopes expanding part size capabilities
- Hybrid manufacturing combining AM with machining
- Automated post-processing like depowdering and heat treating
- Expanded adoption in regulated sectors like aerospace and medical
- Increased focus on process quality control and repeatability
As the technology advances, expect wider adoption of metal AM across more industries.
Câu hỏi thường gặp
Q: What is the most commonly used metal powder for AM?
A: Alloy 316L stainless steel is one of the most common materials with a good combination of printability, mechanical properties, and corrosion resistance.
Q: What is the typical average particle size range for metal AM powders?
A: Most metal AM powders range from 15-45 microns average size. Finer powders around 15-25 μm provide the best resolution.
Q: What safety precautions should be used with metal powders?
A: Conductive containers grounded to dissipate static charges. Argon or nitrogen atmosphere glove boxes. Dust explosion prevention systems. PPE.
Q: Does metal powder go bad or expire?
A: If stored properly in sealed containers, metal powder can last 1-5 years depending on the alloy. Moisture control is critical.
Q: What is the typical purity level of metal powders for AM?
A: 98-99% purity is typical for gas atomized AM powders. Higher purity reduces contaminants and improves final properties.
Q: Which alloys are compatible with biomedical implants?
A: Titanium and cobalt chrome are commonly used thanks to biocompatibility and ability to post-process to final implant requirements.
Q: What metal AM printing methods use powders?
A: Main methods are binder jetting, powder bed fusion via laser or electron beam, and directed energy deposition.
Q: How expensive are metal powders compared to bulk metals?
A: On a per-kilogram basis, metal powders are 10X to 100X more expensive than bulk forms depending on alloy and process.
Q: Can you print pure metals like silver and gold?
A: Yes, but alloyed versions are more common for better strength and printability. Pure precious metals are challenging.
Key Takeaways on Metal Powder for AM
- Gas atomized spherical powders support high resolution printing
- Match powder size distribution tightly to printer requirements
- Leading global suppliers provide qualified AM printing powders
- Handling atmosphere control prevents oxidation and moisture issues
- Powder can be reused up to 20x if sieved and blended properly
- More expensive than conventional metal powders but enables new geometries
- Continued progress expanding alloys, sizes, printers, and applications
Metal powder feedstock unlocks the potential for digitally-driven additive manufacturing across industrial sectors. Continued advances will drive greater adoption long-term.