Metal powder atomization is a particle size reduction technique used to produce fine metal powders with optimized characteristics for industrial applications. This process involves forcing molten metal through a nozzle to disintegrate it into uniform droplets that rapidly solidify into powder particles.
Atomization allows control over powder particle size distribution, morphology, purity, and other properties critical for high performance in metal 3D printing, powder metallurgy parts manufacturing, metallic coating processes, and more. This article provides a comprehensive overview of various types of atomization equipment, working principles, design considerations, applications, advantages, and limitations.
Overview of Metal Powder Atomization Process
Metal powder atomization converts bulk liquid metal into fine spherical powders with controlled characteristics. This is achieved by breaking up a molten metal stream into fine droplets using gas or liquid jet impact. The droplets rapidly solidify into powder particles as they cool.
The key steps involved in this process are:
- Metal Melting – The raw metal charge is melted using induction furnace, arc melting, or other techniques. Common metals atomized include aluminum, titanium, nickel, iron, cobalt, copper etc.
- Molten Metal Supply – The liquid metal is maintained at optimal temperature and channeled to the atomization zone using tundish, crucibles, or pumps.
- Nguyên tử hóa – The molten metal stream is disintegrated into droplets by interaction with high velocity gas or liquid. Various atomization methods are used.
- Powder Collection – The atomized metallic powder is cooled and collected for downstream operations. Sieving, magnetic separation, annealing processes may be utilized.
- Powder Characterization – The particle size distribution, morphology, density, flowability, and microstructure of the powder is analyzed.
Proper control over process parameters like metal composition, temperature, atomizing fluid velocity, atomizer design is critical to achieve desired powder characteristics.
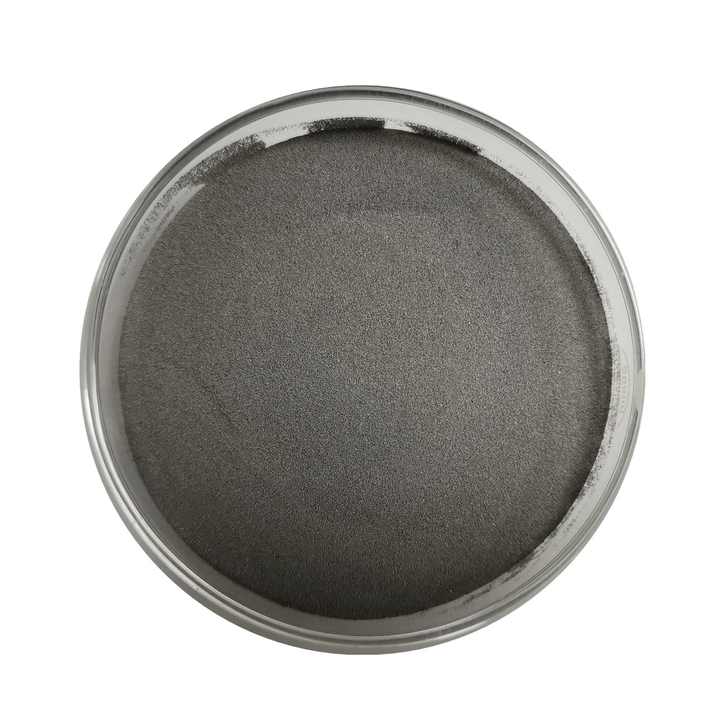
Types of Atomization Equipment
Atomization systems can be categorized based on the medium used to disintegrate the molten metal into droplets:
nguyên tử hóa khí
In gas atomization, kinetic energy of high pressure gas rapidly accelerates and disperses the liquid metal stream into fine droplets. Based on the gas delivery design, it can be further classified into:
- Pressure Gas Atomization – Uses close-coupled nozzles to deliver compressed air or inert gas sideways onto the liquid metal stream.
- Two-Fluid Nozzle Gas Atomization – Coaxial nozzles introduce the high velocity atomization gas around an inner metal delivery tube.
- Multiple Nozzle Gas Atomization – Uses an array of convergent-divergent nozzles to deliver supersonic gas jets onto the melt stream.
Gas atomized powders have lower particle size, more uniform morphology, higher purity compared to water atomized powders. But the process is energy intensive and expensive.
Nguyên tử nước
In water atomization, the molten metal stream is disintegrated by its impact with high pressure water jets. Droplets with broader size distribution are formed. Water atomization has lower capital and operating costs compared to gas atomization.
Based on design, water atomization can use:
- Close-Coupled Water Atomization – Water jets impinge directly on the liquid metal exiting the tundish.
- Free Fall Water Atomization – Falling molten metal stream is intercepted by water jets below the tundish.
Water atomized powders have more irregular particle shapes and broader distribution ideal for pressing and sintering. But water introduces contamination.
Centrifugal Atomization
In centrifugal atomization, molten metal is poured or pumped into a high speed spinning disk or cup. The metal forms a thin film on the perimeter which disintegrates into fine droplets due to centrifugal forces.
Advantages include simple design, low gas consumption, easy scale up. But size range is relatively higher than gas atomization. Used to produce spherical powders from low melting point metals like tin, lead, zinc etc.
Ultrasonic Gas Atomization
Combines gas atomization with an ultrasonic generator coupled to the nozzle. The high frequency vibrations enhance disintegration and dispersion of metal into finer droplets, achieving submicron powder.
Very effective to generate nanocrystalline and amorphous powder morphologies. But expensive and maintenance intensive. Used for specialized applications.
Spark Erosion Atomization
In this electrical atomization technique, a pulsed high current spark discharge is applied between the molten metal and an electrode tip, creating plasma that disintegrates the metal into ultrafine spherical powder.
Enables very fine, highly spherical metallic powder production. But low output rate and high cost. Mostly used for precious metals like gold, platinum, palladium.
Atomizer Components and Design
Atomizers consist of a variety of components engineered to melt, pour, atomize, cool, and collect the metallic powder effectively.
Metal Melting And Pouring System
- Induction Furnace – Most commonly used for melting metals like steel. Allows good temperature control and low melt contamination.
- Crucibles – Refractory ceramic pots used to contain metal charge. Can be heated in separate furnace and manually poured or directly incorporated into atomization system.
- Tundish – Intermediate molten metal reservoir that controls pour rate into the atomization section.
- Downspout – Precisely directs flow of molten metal into atomization zone. Made of refractory metal like tungsten to withstand high temperatures.
- Pumps – Used to control pressure-fed molten metal delivery in certain atomizer configurations.
Atomization Section
- Atomizing Nozzle – Specialized high pressure and temperature resistant nozzles used to create gas or water jets for atomization.
- Nozzle Arrays – Multiple specialized nozzles strategically positioned to optimize droplet formation.
- Spinning Components – Disks, cups used in centrifugal atomization rotate at very high speeds – 10,000 to 50,000 RPM driven by an electric motor.
- Ultrasonic Generator – Converts electrical signal into high frequency mechanical vibrations in nozzle region. Used in ultrasonic atomization.
- Power Supply – Provides the high current to generate an electrical arc for spark erosion atomization.
Powder Handling System
- Cyclones Separators – Separate fine powder from the process gas or water flows using centrifugal forces.
- Bag Filters – Collect very fine powder not separated in cyclones. Need frequent replacement.
- Screen Classifiers – Size classification of powder into different fractions using mesh sieves.
- Magnetic Separators – Remove any tramp metal contaminants from the powder.
- Conveyors – Transports powder between equipment. Screw, belt, vibrating conveyors used.
- Hoppers – Stores powder for further processing or packaging.
- Vacuum Cleaning – Removes spilled powder from equipment and surfaces.Critical for reactive metal powders.
Instrumentation and Controls
- Temperature Sensors – Critical to monitor and control furnace/melt, nozzle temperature for optimal atomization.
- Pressure Sensors – Monitor gas and water pressure into nozzles to maintain proper atomization.
- Flow Meters – Measure and control flow rates of atomization fluid and melt.
- Tachometers – Monitors rotation speed of centrifugal atomization disks.
- Level Sensors – Maintain optimal melt levels in key vessels. Prevents overflow.
- Emergency Stop – Required for rapid and safe shutdown of machinery in case of any issues.
- Control System – Automated computer control optimizes coordination of parameters and improves repeatability.
Metal Powder Atomization Process Parameters
Proper selection of process parameters is key to achieving powders with desired characteristics. The table below summarizes the key variables and their influence on powder properties:
Tham số | Effect on Powder Properties |
---|---|
Temperature of Molten Metal | Higher temperature reduces viscosity, improves atomization. But can increase oxidation, evaporation loss. |
Atomizing Gas Pressure | Higher gas pressure improves particle size distribution, lowers average size. But increases gas consumption. |
Atomizing Gas Flow Rate | Higher flow rate improves particle size reduction. But increases gas usage. |
Atomizing Fluid Velocity | Higher velocity improves particle size reduction. Dependent on nozzle design. |
Nozzle Design | specialized nozzles create finer droplets and powder. |
Melt Pour Rate | Higher pour rates increase yield for continuous operation but can reduce particle size. |
Melt Superheat | Increases as pouring temperature rises above melting point. Improves fluidity. |
Melt Filtration | Removes inclusions and contaminants. Improves powder purity. |
Atomization Distance | Longer free-fall distance allows more time for droplet formation. Reduces satellite formation. |
Melt Composition | Alloying elements can change viscosity, surface tension, affecting atomization behavior and powder characteristics. |
Characterization of Atomized Metal Powder
The properties and quality of the atomized powder determines the performance in downstream applications. Key characteristics evaluated are:
Phân phối kích thước hạt
The distribution of powder particles across different size fractions, commonly represented as D10, D50, and D90 percentiles. Gas atomization can achieve under 20 microns while water atomization produces coarser powder.
Particle Shape and Morphology
Gas atomized powder has highly spherical particles while water atomized powder is more irregular. Satellite particles indicate lack of optimal atomization. Rounded powder has better flow and packing density.
Thành phần hóa học
The elemental and phase composition from assays. Determines alloy grade. Gas atomization produces high purity while water can contaminate reactive metals like titanium, aluminum.
Apparent and Tap Density
Indicator of powder packing efficiency. Higher density improves product properties in pressing and sintering. But can affect powder flow. Values typically 40-65% of material density.
Đặc tính dòng chảy
Important for handling and downstream processing. Influenced by factors like particle shape, size distribution, surface structure. Improved by annealing, surface treatment.
Cấu trúc vi mô
Internal powder structure revealed by microscopy. Gas atomized powder has fine grains and defects from rapid solidification while water atomized is coarser. Determines sintering behavior.
Applications of Metal Powder Atomization
Atomized metallic powders find a wide range of uses in advanced manufacturing, improving product quality and performance versus conventional metal processing:
sản xuất phụ gia
- 3D Printing – Atomized spherical powders with controlled size distribution are ideal for powder bed fusion techniques. Aluminum, titanium, nickel superalloys are commonly used.
- Metal Injection Molding – Finer stainless steel, titanium, and aluminum powders improve sintering process and component density.
Luyện kim bột
- Press and Sinter – Irregular, coarser water atomized ferrous powder used for high production of P/M parts with good mechanical properties.
- Soft and Hard Magnets – Fine crystalline NdFeB, SmCo powders produce high performance bonded and hot pressed magnets.
- Friction Materials – Water atomized copper powder enhance performance of brake pads and clutch linings.
Surface Coatings
- Thermal Spray – Spherical, controlled size distribution powder important for uniform, dense coatings via plasma or HVOF spray. WC-Co, nickel alloy powder used.
- Vapor Deposition – Ultrafine superalloy powder feedstock used in electron beam physical vapor deposition for turbine coatings with enhanced protection.
Khác
- Metal Injection Molding – Fine stainless steel, titanium, and aluminum powder feedstocks can produce small, complex components.
- Brazing Pastes – Atomized silver, gold, copper alloy used in manufacturing high temperature braze joints.
- Spark Erosion – Ultrafine spherical powder used as dielectric medium improves precision and speed of EDM machining.
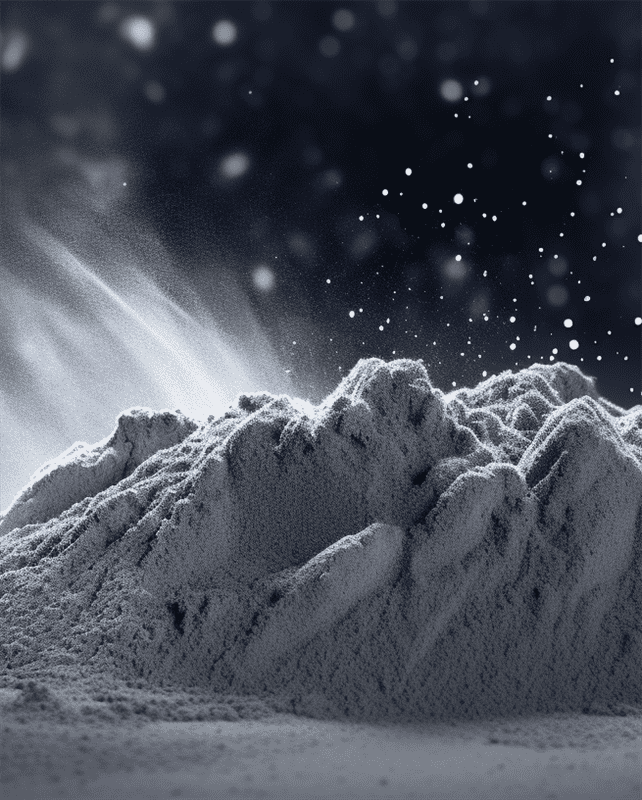
Advantages of Metal Powder Atomization
Compared to conventional metal processing routes, key benefits of using atomized powders include:
- Improved mechanical properties – Fine, homogeneous microstructure from rapid solidification increases yield strength, fatigue life, and ductility.
- Precise dimensional control – Consistent, spherical powder enables high density and precise net shape fabrication. Reduces machining.
- Higher Productivity – Components can be mass produced via metal powder processing faster than subtractive methods.
- Greater design freedom – Complex geometries can be manufactured that are impossible through casting or machining.
- Minimizes Waste – Near net shape capability reduces scrap loss versus ingot metallurgy. Unused powder can be recycled.
- Lower Energy Usage – Powder process requires lower temperature and energy than production from bulk metal.
- Hợp kim tùy chỉnh – Specialized compositions can be atomized that are difficult to produce via ingots.
- Độ tinh khiết cao – Reactive elements like titanium can be atomized with lower contamination than conventional practices.
Limitations of Metal Powder Atomization
- High capital investment required for atomization equipment and powder handling systems compared to bulk metal processing.
- Additional downstream processes like compaction, sintering etc. are needed to make products from powders. Overall production route is complex.
- Achieving ultrafine nano-scale powder can be challenging and expensive with lower throughputs.
- Potential for contamination when using water atomization, especially for reactive metals.
- Powder can adsorb oxygen and moisture, requiring protective storage and handling.
- Safety issues exist related to dust explosions, fire hazards, and toxicity for certain powder compositions and morphologies.
- Variability in final component properties compared to wrought products. Defects related to powder can manifest after consolidation.
- Recycling and reuse of metal powder is limited compared to bulk metal forms. Material is discarded after 1-2 reuse cycles.
- Lack of industry standards for novel metal powders on characteristics, testing methodology, quality control, and certification creates barriers for adoption.
Selecting a Metal Powder Atomization System
Choosing the right atomization equipment for an application depends on factors such as:
Production Volume
- Low production – Lab and pilot scale atomizers. Centrifugal or pressure gas atomization systems.
- Medium production – Continuous atomizers rated up to 3 tons/hour powder output.
- High production – Custom large scale systems with capacity exceeding 10 tons/hour.
Powder Material
- Non reactive metals like steel and nickel alloys can use water atomization.
- Water sensitive alloys like aluminum, titanium need inert gas atomization.
- Refractory metals like tungsten require specialized atomizing media and protection.
Powder Properties
- Gas atomization for finer powder below 30 microns with spherical morphology.
- Water atomization for coarser, irregular powder for pressing.
- Specialized atomization for nanocrystalline or amorphous metallic powder.
Product Application
- Additive manufacturing uses very fine, controlled particle distribution powder from gas atomization.
- Powder injection molding requires fine, spherical powder with good flow.
- Thermal spray coatings need dense, spherical powder that packs well.
Capital and Operating Costs
- Water atomization has lower equipment cost and operating cost but can compromise powder quality.
- Gas atomization has 10X higher capital cost but produces superior powder. Operating costs also higher.
- Centrifugal atomization is economical but has size and shape limitations.
Plant Integration
- Requires sufficient infrastructure for melt preparation, powder handling, storage and transport.
- Protective systems for reactive metals like inert gas atmosphere.
- Automated controls and data monitoring improve process stability.
Leading Metal Powder Atomizer Manufacturers
Several companies offer standardized and custom engineered metal powder atomization systems and components:
Gas Atomization Systems
- Praxair – market leader in high pressure gas atomization equipment. Offers lab, pilot and production scale systems.
- AP&C – Specializes in close-coupled nozzle gas atomizers for reactive and refractory metals. Used extensively for titanium and aluminum powders.
- ALD Vacuum Technologies – Designs multi-nozzle gas atomizers for medium to high production. Owned by Oerlikon Metco.
Nguyên tử nước
- Gasbarre – Offers close-coupled and free-fall water atomization for medium to high volumes.
- Sheffield Atomising Systems – Specialized in free fall water atomization technology for over 50 years.
Centrifugal Atomization
- ABB – Major global equipment provider. Offers lab to full production scale centrifugal atomization systems.
- Ferrum AG – Leading supplier of horizontal and vertical centrifugal atomizers based in Switzerland.
Ultrasonic Atomization
- Tekna – Offers ultrasonic gas atomizer systems based on their patented coupled-twin-wire induction guide technology
- Ultramet – Provides specialty ultrasonic atomization equipment with high temperature liquefier technology
Spark Erosion Atomization
- PyroGenesis – Offers the Plasma Atomization System (PAS) for producing ultrafine spherical metallic powders.
- Plasma Innovations – Supplies the rotating electrode process (REP) spark erosion atomization systems.
Cost Analysis of Metal Powder Atomizers
Atomizer cost depends on scale, production rate, automation level and powder material being processed. Typical capital cost estimates:
Large Production Gas Atomizer | Custom building | 1000 | 10 million |
---|---|---|---|
Small Production Water Atomizer | Trailer/container system | 100 | 750,000 |
Medium Production Water Atomizer | Shelter system | 500 | 2 million |
Large Production Water Atomizer | Custom building | 2000 | 5 million |
Pilot Centrifugal Atomizer | Skid mounted | 50 | 400,000 |
Medium Centrifugal Atomizer | Shelter system | 500 | 1.5 million |
Lab Ultrasonic Atomizer | Benchtop | 5 | 250,000 |
Pilot Ultrasonic Atomizer | Skid mounted | 20 | 1 million |
Spark Erosion Atomizer | Container system | 10 | 2 million |
Operating Costs
- Main costs are energy, labor, maintenance, inert gas usage.
- Gas atomization power consumption is ~500-800 kWh per tonne powder. Gas usage 5-10 m3 per kg powder.
- Water atomization power usage lower at ~200-400 kWh per tonne powder. But higher labor and maintenance.
- Centrifugal atomization power consumption ~300-500 kWh per tonne powder. Lower inert gas usage.
- Consumable parts like nozzles, filters bags require frequent replacement.
Cost Reduction Opportunities
- Increasing production scale and powder output lowers capital cost per kg powder.
- Higher degree of automation and monitoring improves labor productivity.
- Recycling and reusing process gases, water, and waste heat reduces operating expenses.
- Preventive maintenance programs minimize downtime and maintenance costs.
- Local supply of energy, gases, water, and ancillary services lower logistics expenses.
- Buying rebuilt/used atomization systems reduces capital outlay for small producers.
Metal Powder Atomization Equipment – Frequently Asked Questions
Q: What is the typical particle size range achieved in gas atomization?
A: Gas atomization can produce powders from 1 micron to over 100 micron particle size. Typical D50 values are 10-45 microns for most alloys. Finer powder under 10 microns is possible with optimized nozzles and high gas velocities.
Q: How much can a small gas atomizer system produce annually?
A: A pilot scale gas atomizer with 10 kg/hr output running 5000 hours/year can produce ~50,000 kg of powder per year. A small production system with 50 kg/hr capacity can output ~250,000 kg annually under full production.
Q: What types of metals can be atomized into powder?
A: Most commercial alloy systems have been atomized, including stainless steel, tool steel, nickel alloys, titanium alloys, aluminum alloys, superalloys, cobalt alloys etc. Refractory metals like tungsten, molybdenum are challenging and require specialized atomization systems.
Q: What is the best atomization method for reactive metals like titanium?
A: Gas atomization with an inert gas like argon or nitrogen is preferred for reactive metals like titanium, aluminum. This prevents oxidation and contamination compared to water atomization.
Q: How fine can particle size be achieved with ultrasonic atomization?
A: Ultrasonic gas atomizers can generate submicron and nano-scale metallic powder with average size under 100 nanometers when optimized. But powder output rate is low.
Q: Can metal powder be recycled after use in additive manufacturing?
A: Yes, unused powder can be reused in AM processes. But the powder can only be recycled 1-2 times before properties degrade. The powder then needs to be re-atomized for continued reuse.
Q: What is the best way to handle fine reactive powder?
A: Using inert gloves boxes, sealing powder containers, avoiding exposure to air/moisture. Some reactive materials may require surface treatment. Water atomized aluminum powder is typically coated to prevent oxidation.
Q: Why is high purity inert gas important for gas atomization?
A: High purity minimizes contamination. Moisture and oxygen can oxidize reactive alloys during atomization. Tramp gases can get entrapped in powder, creating defects in final part properties.
Q: How easy is it to service and repair a gas atomizer?
A: Routine maintenance is straightforward. But major repairs like nozzle replacement can take days and require personnel with specialized training. Additional nozzle assemblies should be kept as spares for rapid changeover.
Q: What safety issues are present with metal powder production?
A: Fine powder handling always presents dust explosion risk. Other concerns are pressurized gas hazards, high voltage electricity, elevated temperatures, molten metal handling requiring protective equipment and training.