Metal atomization is a process used to produce fine metal powders for various applications. It involves melting metal and then breaking it into fine droplets using gas or centrifugal force. The droplets rapidly solidify into powder particles. Metal atomization systems are the equipment used to carry out this process efficiently on an industrial scale.
Overview of Metal Atomization Systems
Metal atomization systems consist of a metal melting unit, an atomization mechanism, and a powder collection system. The main components are:
Metal Melting Unit
- Melting crucible
- Induction coils or electrodes
- Temperature sensors
- Inert gas sealing
Atomization Mechanism
- Nozzles for gas atomization
- Rotating disk or cup for centrifugal atomization
Powder Collection System
- Cyclone separators
- Bag house filters
- Scrubbers and condensers
The metal charge is first melted in the crucible using induction heating or electrical resistance heating. The molten metal is then guided into the atomization section.
In gas atomization, high pressure gas jets hit the metal stream and break it up into fine droplets. In centrifugal atomization, the molten metal is poured on a spinning disk/cup that ejects it radially into droplets due to centrifugal force.
The droplets solidify rapidly as they fall through the cooling chamber due to the high surface area to volume ratio. The inert gas prevents oxidation. The solidified powder particles are collected in the separators, filters and condensers.
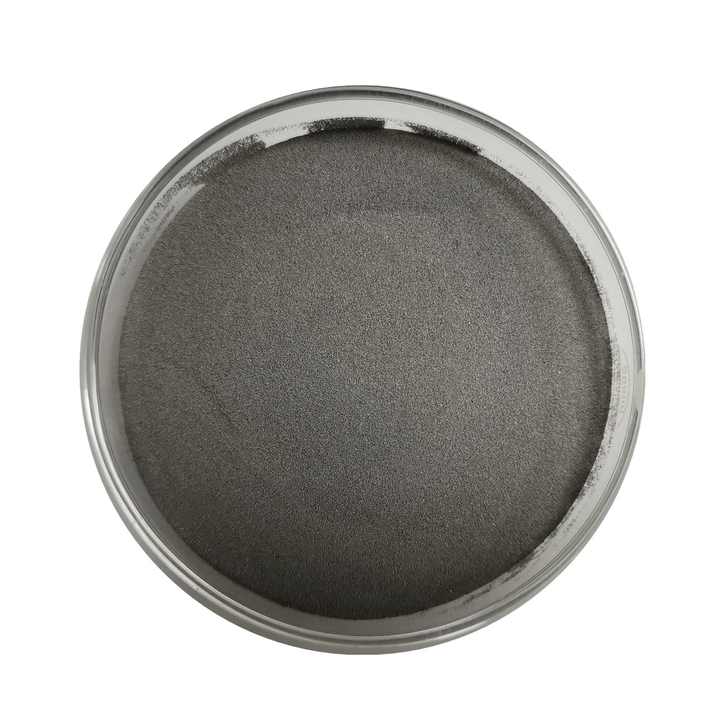
Types of Metal Atomization Systems
There are two main types of atomization mechanisms used:
nguyên tử hóa khí
- Uses high pressure inert gas jets
- Can make finer powders down to 10 microns
- Nitrogen, argon used as atomizing gases
Centrifugal Atomization
- Uses rotating cup or disk
- Makes coarser powders over 20 microns
- Simple design, no gas handling needed
Vacuum Atomization
- Carried out under vacuum instead of inert gas
- Reduces gas absorption by powders
Ultrasonic Atomization
- Uses ultrasonic vibrations to make droplets
- For research scale production
Electrostatic Atomization
- Uses electric field to disintegrate metal stream
- Experimental technique
Metal Atomization System Design
The major components of a typical gas atomization system are:
Table 1: Gas Atomization System Design
Thành phần | Details |
---|---|
Melting Unit | Induction melting crucible, capacity 50-2000 kg |
Nozzle Assembly | Multiple close-coupled nozzles, 2-5 mm diameter |
Melt Superheating | Nitrogen/argon injected to superheat melt |
Atomization Chamber | Water-cooled, 3-5 m height |
Gas Supply | Nitrogen/Argon, 50-100 bar pressure |
Cyclone Separators | Multiple cyclones in series for powder collection |
Final Filters | Baghouse, cartridge filters |
The nozzle design and number is important for achieving the desired fine powder particle size distribution. The height of the atomization chamber allows time for the droplets to solidify before collection.
High grade industrial gases like nitrogen or argon are supplied from compressed gas cylinders or on-site generators. Their pressure and flowrate determines the droplet size.
Metal Atomization System Specifications
Typical specifications for industrial scale gas atomization systems are:
Table 2: Metal Atomization System Specifications
Thông số | Thông số kỹ thuật |
---|---|
Khả năng sản xuất | 10 kg/hr to 5000 kg/hr |
Kích thước hạt | 10 – 150 micron |
Metal Types | Nickel, iron, cobalt, copper alloys |
Melting Temperature | 1600 °C max |
Gas Pressure | 10 – 100 bar |
Cooling Rate | 104 – 106 K/s |
Powder Purity | 99.5% |
Nozzle Design | Annular slit, discrete jet |
Atomization Gas | Nitrogen, Argon |
The capacity depends on the crucible size and varies from lab/pilot scale 10 kg/hr to large scale 5000 kg/hr systems. Mostly nickel, iron, and cobalt alloys are atomized but other metals like aluminum, copper alloys are also processed.
High gas pressure and fast cooling rates ensure fine microscopic powder particles in the 10-150 micron size range. Powders with 99.5% purity can be obtained.
Metal Atomizer System Applications
Some major applications of metal powder produced from atomization include:
Table 3: Metal Powder Applications
Ngành công nghiệp | Các ứng dụng |
---|---|
Không gian vũ trụ | Turbine blades, discs |
Ô tô | Sintered parts, filters |
Thiết bị điện tử | Chip resistors, conductors |
sản xuất phụ gia | Bột in 3D |
Hóa chất | Catalysts, pigments |
Y sinh | Implants, prosthetics |
In the aerospace industry, nickel and titanium alloy powders are used to produce turbine blades and discs with complex shapes by powder metallurgy. Automotive industry uses atomized iron and steel powders for sintered parts like gears.
Fine copper and silver powders serve as conductors and resistors in microelectronics applications. Metal powders are the feedstock for additive manufacturing methods like 3D printing.
Special alloy powders finds use as chemical catalysts and pigments. Porous stainless steel powder is used for orthopedic bone implants in the biomedical field.
Advantages of Metal Atomization Systems
Some benefits of using metal atomization for powder production:
Table 4: Advantages of Metal Atomization
Những lợi ích | Details |
---|---|
Finer powders | Micrometer to nanometer sizes |
Narrow size distribution | Precise control over particle size |
Độ tinh khiết cao | Avoid contamination from milling |
Chi phí thấp hơn | Cheaper than mechanical grinding |
Composition control | Alloying possible in melt |
Spherical particles | Good flowability |
Versatile | Wide range of alloys atomized |
Gas and centrifugal atomization can produce finer metal powders down to 10 microns compared to mechanical milling. The particle size distribution is narrower giving better control.
Since no grinding media is involved, the powder purity is higher. The capital and operating costs are lower than mechanical milling.
Alloying elements can be added in the crucible allowing flexibility in powder composition. Spherical powder particles provide good flowability important for die filling.
Almost any alloy from nitinol to inconel can be atomized with proper control over process parameters.
Limitations of Metal Atomization
Some drawbacks of metal atomization systems are:
Table 5: Limitations of Metal Atomization
Drawbacks | Details |
---|---|
Điểm nóng chảy cao | Limited to lower melting metals |
Reactive metals | Difficult to atomize reactive metals like titanium, aluminum |
Gas pickup | Absorbed gases affect powder quality |
Satellite particles | Some larger irregular particles formed |
High capital cost | Major investment needed for large system |
Metals with very high melting points over 1800°C like tungsten, molybdenum are difficult to atomize due to crucible limitations. Reactive metals like titanium, aluminum require vacuum or inert atmosphere.
Gases absorbed during atomization process affect powder characteristics. Some irregular shaped satellite particles are also formed during atomization along with spherical particles.
Large scale metal atomization systems require major capital investment of over $2 million. Operational costs are also relatively high.
Suppliers of Metal Atomization Systems
Some leading global suppliers of metal atomization equipment are:
Table 6: Metal Atomization System Suppliers
Công ty | Vị trí | Scale |
---|---|---|
Phoenix Khoa học | Rockwood, USA | Lab to industrial |
Makin Metal Powders | Manchester, UK | Lab to industrial |
Hỏi hóa chất | Hilden, Germany | Lab to industrial |
ZenniZ | Moscow, Russia | Công nghiệp |
ALD Vacuum | Hanau, Germany | Công nghiệp |
These companies offer gas, centrifugal, vacuum atomization systems ranging from lab/pilot scale 5 kg/hr to large scale 2000 kg/hr capacities. Turnkey systems with melting, atomization and powder handling units are provided.
Atomization systems are priced from $100,000 for lab units to over $2 million for industrial plants based on capacity and features. Location, taxes, transportation etc. also affect pricing.
Installing a Metal Atomization System
Key steps in installing a metal atomization system are:
Table 7: Metal Atomizer Installation
Stage | Actions |
---|---|
Site preparation | Level concrete floor, install utilities |
Assembly | Assemble sub-units like crucible, nozzle section |
Connections | Connect gas lines, cooling water, ducting |
Commissioning | Test run empty, leak checks, trial with low capacity |
Safety checks | Install emergency stop, fire suppression, alarms |
Personnel training | Train staff on system operation and maintenance |
The equipment is heavy so the site needs to have a level, vibration-free concrete floor. Utilities like cooling water, inert gas, and exhaust ducting need to be connected.
The system is then assembled, aligned,leak tested and initially run empty before actual hot commissioning. Safety systems for emergency shutdown, fire or melt leakage must be operational.
Thorough training of the operating personnel by the vendor is essential for smooth operations.
Operating and Maintaining a Metal Atomizer
Key aspects of operating a metal atomization system include:
Table 8: Metal Atomizer Operation
Activities | Details |
---|---|
Raw material handling | Use proper gloves, containers for metal charge |
Crucible cleaning | Remove residue, slag by grinding, acid pickling |
Crucible lining | Inspect lining, recoat/replace as needed |
Process parameters | Maintain proper temperature, pressure, flows |
Nozzle condition | Inspect nozzles for wear, blockages |
Powder handling | Ensure proper containers, transfer procedures |
Equipment inspection | Check seals, connectors, safety systems |
Maintenance | Schedule preventive maintenance, repairs |
Proper protective gear should be used when handling raw metal pieces to avoid contamination. The melting crucible needs regular cleaning and lining refractory maintenance.
Careful monitoring of process parameters like temperature, pressure and gas flow is important. Nozzles, especially for gas atomization, require inspection and replacement periodically.
The fine powder produced needs careful handling to prevent exposure risks. Regular inspections help spot leaks, damages and ensure all safety systems work. Preventive maintenance should be scheduled to avoid breakdowns.
Choosing a Metal Powder Atomizer Supplier
Key factors in selecting a metal atomization system supplier:
Table 9: Choosing a Metal Atomizer Supplier
Criteria | Considerations |
---|---|
Chuyên môn kỹ thuật | Experience, expert personnel |
Range of equipment | Lab, pilot, industrial scale systems |
Track record | Relevant case studies, client list |
Customization | Flexibility for specific requirements |
After-sales service | Installation support, maintenance contracts |
Giá | Quotes fitting budget |
Reliability | Build quality and proven performance |
Safety | Meets all industry safety norms |
Certification | ISO or other quality certification |
Look for an established company with expertise in thermal spray or powder metallurgy industries. They should offer the full range of atomizers from lab prototypes to large scale production.
Request client references and case studies relevant to your specific application. Seek customized solutions for your capacity needs and powder characteristics.
Evaluate after-sales service support like installation supervision, operator training, maintenance contracts etc. Consider pricing but give priority to performance, safety and reliability.
Phần kết luận
Metal atomization is an efficient process for producing clean, spherical fine metal powders from various alloys for advanced applications in aerospace, automotive, additive manufacturing and other industries.
Gas and centrifugal atomization systems consist of metal melting, droplet formation and powder collection sub-units. Careful design is required to obtain desired particle sizes and powder characteristics.
Leading vendors offer standard and customized atomization systems in small to large industrial capacities with suitable after-sales support. Choosing the right supplier and following good operating practices ensures smooth functioning and maximum powder production.
Câu hỏi thường gặp
Q: What is the typical capacity range of metal atomization systems?
A: Metal atomization systems are available in capacities from 10 kg/hr for lab/pilot scale to over 5000 kg/hr for high volume industrial production. Larger capacities up to 10,000 kg/hr are also possible.
Q: What industries commonly use metal atomization?
A: Key industries using metal atomization include aerospace, automotive, additive manufacturing, powder metallurgy, electronics, and chemical industries. The fine, spherical powders are used to manufacture critical components.
Q: How fine can the powder particle size be made?
A: In gas atomization, powder sizes down to 10 microns can be achieved by optimal design of nozzles, gas pressure and flow rates. Centrifugal atomization typically makes coarser powders over 20 microns in size.
Q: What metals can be atomized?
A: Most engineering metals with melting point below 1800°C can be atomized. Common examples are nickel, iron, cobalt and titanium alloys. Some reactive metals like aluminum and magnesium can also be atomized under controlled conditions.
Q: What gases are used in gas atomization?
A: Nitrogen and argon are most widely used due to their inertness and availability. In some cases oxygen or air is also used but can contaminate the powder.
Q: How are the operating costs of atomization systems?
A: Operating costs are higher than mechanical milling since continuous supply of high pressure gas is needed. Also electrical energy for induction heating and crucible/nozzle maintenance add to costs.
Q: What safety aspects need attention?
A: High temperature metal melts, inert gases under pressure, fine combustible powders require careful handling and safety systems for fire, explosion prevention. Proper operator training is a must.
Q: What maintenance is required for the equipment?
A: Nozzle inspection and replacement, crucible repair/relining, leak checks, cleaning air filters are typical maintenance tasks. Scheduled preventive maintenance minimizes breakdowns.
Q: Can metal alloys be atomized?
A: Yes, metal alloys can be readily atomized by adding the alloying elements like chromium, aluminum, titanium into the melting crucible in precise proportions to obtain the desired composition.
Q: Can metal atomization be done on a small scale?
A: Yes, lab scale atomizers with 1-5 kg capacity melting crucibles are available from suppliers for small batch powder production like R&D purposes. But operating costs per kg are higher.