Aluminum is a popular metal powder for additive manufacturing thanks to its low density, good mechanical properties, machineability, corrosion resistance and conductivity. Optimizing aluminum powder characteristics enables reliable printing of strong, lightweight aluminum parts across aerospace, automotive and industrial applications.
This guide covers properties, specifications, atomization production, quality assurance considerations, applications and advice on sourcing aluminum powders for powder bed fusion or binder jet 3D printing.
Máy in 3D Bột nhôm Sáng tác
Common aluminum grades for AM include:
Hợp kim | Sự miêu tả | Thành phần điển hình |
---|---|---|
ALSI10MG | Cast alloy with silicon and magnesium additions for strength and corrosion resistance | Remainder Al, 9-11% Si, 0.25-0.45% Mg, 0.8% max Fe, 0.2% max Cu |
Què | Very similar to AlSi10Mg with slightly lower silicon content | Remainder Al, 6-8% Si, 0.25-0.45% Mg, 0.8% max Fe, 0.2% max Cu |
6061 | Very common heat treatable wrought alloy with magnesium and silicon | Remainder Al, 0.8-1.2% Mg, 0.4-0.8% Si, 0.7% max Fe, 0.15-0.4% Cu, 0.04-0.35% Cr |
Match composition to mechanical properties, corrosion resistance, weldability needs and alloy costs.
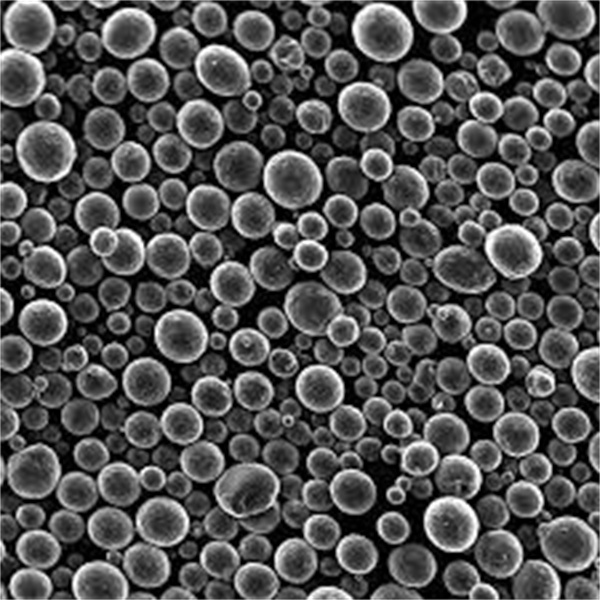
Specification Overview
Tham số | Details | Phương pháp kiểm tra |
---|---|---|
Sự thuần khiết | >98% Aluminum preferred | ICP analysis |
Hình dạng hạt | Spherical >90% desired | Microscopy |
Phân bố kích thước | D50: 25-45 μm typical | Nhiễu xạ laser |
Mật độ rõ ràng | 1.2-1.8 g/cc | Máy đo lưu lượng hội trường |
Khả năng chảy | Hall flow 25-50 sec for 50 g sample | Máy đo lưu lượng hội trường |
Oxides & Hydroxides | <3% by weight | TGA, XRD, Inert gas fusion |
Độ ẩm | <0.2% by weight | TGA analysis |
High powder quality and consistency required for defect minimized AM processing into high density, strong parts.
Atomization Methods
3d printer aluminum powder production via:
- Air Atomization – High pressure air disintegrates molten aluminium into fine spherical droplets preventing oxidation. Lower energy process results in larger particles suitable for binder jet printing.
- Nitrogen Atomization – Nitrogen ambient prevents surface oxidation during atomization enabling finer powder sizes, lower oxygen and higher flow characteristics preferred for SLM and EBM.
- Electrode Rotating Atomization – Rapidly spinning thin molten aluminium into nitrogen results in powder with very tight size distributions good packing density.
Controlling process atmospheres, cooling rates and gas dynamics optimizes aluminum particle sizes and morphologies for powder bed applications requiring good flow and shear response.
Tính chất cơ học
Hợp kim | Density (g/cc) | Yield Strength (MPa) | Tensile Strength (MPa) | Kéo dài |
---|---|---|---|---|
ALSI10MG | 2.68 | 228 | 398 | 7.9% |
Què | 2.74 | 261 | 372 | 8.1% |
6061 | 2.70 | 241 | 303 | 11% |
Meeting specified strengths requires optimized printing parameters and post-processing like aging. Part orientation also significantly impacts mechanical performance.
Metal AM Applications
AlSi10Mg aluminum sees wide use across industries for additively manufactured:
- Aerospace & Defense: Lightweight airframe, UAV components; conformal heat exchangers and cold plates; active lattice structures. Rapid tooling for composite layups.
- Automotive: Aluminum has 3X lower embodied energy than steel allowing greater fuel efficiency through weight reduction. Customized car body panels, fittings, chassis elements like control arms enable performance improvements. Heat exchanger parts like manifold housings add functionality gains. Jigs and fixtures for carbon fiber composites.
- Industrial: Customized series production for small to medium lot sizes. Heat sinks for electronics thermal management with optimized form factors. Fluid flow components like impellers, pumps, valves and housings. Jigs, fixtures, guides and gages offering lightweight durability.
- Architecture: Specialized custom parts made on-demand. Decorative elements using hybrid printing with bronze infill. Dimensionally accurate scale models for visualization.
Certification Standards
- ASTM B556 – Standard Specification for Powder Metallurgy (PM) Aluminum Alloy Structural Components Using Alloy 6061
- ASTM B925 – Standard Specification for Premium Quality Aluminum Alloy Powder for Processing via Powder Metallurgy Methods for Automotive, Aerospace, and Defense Applications
- ASTM E2926 – Standard Specification for Additive Manufacturing Aluminum Powders and Feedstock
Review statistically validated batch certificates showing compliance relative to target grade specifications and AM processing needs before purchase.
Common Defects
Key aluminum metal AM defects with root causes:
Defect | Cause | Giải pháp |
---|---|---|
Độ xốp | Moisture; Oxides; Metal vaporization | Lower humidity; minimize oxides; adapt energy density |
Cracking | Rapid cooling; Residual stresses; Impurities | Optimize build plate preheating; Hot isostatic pressing; High purity powder |
Delamination | Recoater blade forces; Poor layer fusion | Smooth powder size distribution; Optimize spread layer; Validate spreader settings |
Balling | High surface tension inhibits flow | Preheat plate for faster melting |
Surface Finish Issues | Spatter, unmelted particles fused in | Parameter optimization for a given powder |
Adapt printing parameters through trial builds to achieve fully dense parts prior to series production.
Pricing Factors
Tham số | Sự va chạm |
---|---|
Loại bột | Higher purity/sphericity comes at a premium |
Lot size | Economy of scale savings at 500+ kg |
Certification level | Full certification vs batch testing |
Atomization method | Nitrogen > Air due to higher consistency and lower oxides |
Regional logistics | Source locally if possible |
Expect pricing around $50-100/kg for lower size distribution aluminium AM powder delivered. Larger manufacturers offer economies of scale.
Buying Considerations
Tham số | Tầm quan trọng |
---|---|
Quality compliance | Cao |
Sampling availability | Cao |
Chuyên môn kỹ thuật | Trung bình |
Customer references | Trung bình |
Giá cả | Thấp |
Vendor Comparison
nhà chế tạo | Phạm vi kích thước | Chất lượng | Consistency | Lead Times | Giá cả |
---|---|---|---|---|---|
[Brand 1] | 10-45 m | Fully certified | Very consistent | 12-14 weeks | $$$ |
[Brand 2] | 15-65 μm | Batch testing | Minor variation | 3-4 weeks | $ |
[Brand 3] | 10-63 μm | Independent MPI | Meets minimum specs | 8-10 weeks | $$ |
Choose leading brand aligned to quality compliance needs of part application even if at a pricing premium to avoid defect and property deviation risks.

Câu hỏi thường gặp
Q: What particle size is optimal for aluminum laser powder bed fusion?
A: 25-45 μm aluminum powder size fractions facilitate dense packing with good shear and melt flow response ideal for spreading and high density fusion in powder bed applications.
Q: How should aluminum AM powder be stored properly?
A: Seal containers air-tight with moisture absorbing bags to prevent oxidation and stabilization limiting shelf life to 6-12 months if properly stored cool out of direct sunlight.
Q: Does aluminum powder for metal AM require special handling precautions?
A: Classified as non-hazardous but use powders in well ventilated areas with approved PPE as fine metallic particulate carries respiratory health and dust explosion risks requiring safety protocols be established.
Q: What post processing is typically done on additively manufactured aluminum parts?
A: Aluminum AM parts often undergo solution treatment, aging precipitation hardening, passivation and electropolishing to relieve residual stresses, enhance mechanical properties and surface finish. Protective coatings improve corrosion and wear resistance.