Selective laser melting (SLM) is an additive manufacturing technique that uses a laser to selectively melt and fuse metallic powder into 3D objects. This guide provides an in-depth overview of SLM Printing, materials, process parameters, applications, benefits, and more.
What is SLM?
SLM is a powder bed fusion process that uses a high-powered laser to melt and solidify fine metallic powder layer-by-layer to build up fully dense 3D parts directly from CAD data.
Process | Sự miêu tả |
---|---|
Laser melting | A laser scans and melts powder in the shape of each layer |
Powder spreading | Fresh layer of powder spread over build area |
Lowering build platform | Build platform lowered before spreading new powder layer |
Repeating steps | Steps repeated layer-by-layer until part is completed |
SLM allows printing fully dense metal parts with complex geometries directly from 3D CAD data.
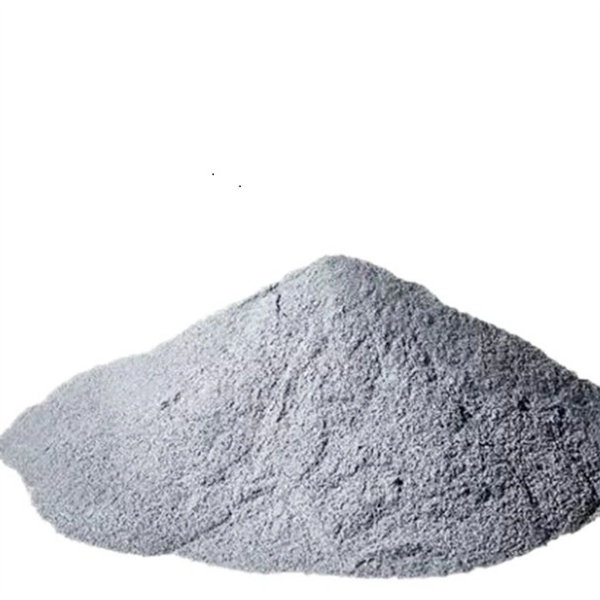
How SLM Printing Works
SLM printing involves the following key components and process:
Thành phần | Vai trò |
---|---|
Laser | Selectively melts powder in pattern of each layer |
Scanner system | Controls laser position and focusing |
Powder bed | Holds powder layers during printing |
Powder dispenser | Spreads fresh powder for each layer |
Build plate | Holds and lowers part during printing |
Inert gas system | Provides protective atmosphere to prevent oxidation |
The process is fully automated based on the imported 3D model geometry.
SLM vs Other 3D Printing Methods
SLM differs from other forms of 3D printing in key ways:
Phương pháp | Comparison |
---|---|
Fused Deposition Modeling (FDM) | FDM uses extruded thermoplastics, SLM uses metal powder |
Stereolithography (SLA) | SLA uses photopolymers, SLM uses metals |
Tia điện tử tan chảy (EBM) | EBM uses electron beam, SLM uses laser beam |
Binder Jetting | Binder jetting bonds powder particles, SLM fully melts powder |
SLM allows printing of fully dense metal parts suitable for end-use engineering applications.
Metals for SLM Printing
Common metals printed with SLM technology:
Vật liệu | Key Properties |
---|---|
Thép không gỉ | Corrosion resistance, high strength |
Hợp kim nhôm | Lightweight, ductile |
Hợp kim Titan | Lightweight, high strength |
Nickel alloys | Heat and corrosion resistance |
Cobalt-Chrome | Biocompatibility, wear resistance |
Thép công cụ | High hardness, thermal stability |
A range of metals are printed with SLM for different applications requiring specific material properties.
SLM Process Parameters
Critical SLM process parameters:
Tham số | Phạm vi điển hình |
---|---|
Năng lượng laser | 100-400 W |
Scanning speed | 100-5000 mm/s |
Khoảng cách nở | 50-200 m |
Độ dày lớp | 20-100 m |
Spot size | 50-100 μm |
Build chamber atmosphere | Argon or nitrogen |
These parameters are optimized depending on the material, part geometry, build speed and mechanical properties required.
Benefits of SLM Printing
Key advantages of SLM printing:
- Ability to create complex geometries not possible with machining
- Significantly shorter lead times compared to machining
- Minimal material waste and lower buy-to-fly ratios
- Lightweighting potential with lattice structures
- Consolidate assemblies into single parts
- Customized products tailored to customer specs
- Just-in-time production and inventory reduction
- High dimensional accuracy and repeatability
- Good surface finish and fine resolution
SLM provides significant cost and time savings for low to medium volume production.
SLM Applications
Ngành công nghiệp | Các ứng dụng phổ biến |
---|---|
Không gian vũ trụ | Turbine blades, structural brackets, engine components |
Thuộc về y học | Dental copings, implants, surgical instruments |
Ô tô | Lightweight components, custom prototypes |
Công nghiệp | Lightweight robotic parts, jigs, fixtures, tooling |
SLM is used across industries to produce high-performance end-use metal parts with reduced lead times.
Post-Processing for SLM Parts
Typical SLM part post-processing steps:
- Support structure removal using EDM
- Surface machining to improve finish
- Drilling holes, tapping threads
- Heat treatment to enhance properties
- Hot isostatic pressing to eliminate internal voids
- Surface treatments like bead blasting, anodizing, coating
Post-processing tailors the parts to meet application requirements.
SLM Design Guidelines
Key SLM design considerations:
- Optimize geometries to reduce support structures
- Maintain minimum wall thickness for better heat dissipation
- Use fine lattice structures to reduce weight
- Design self-supporting geometries to avoid supports
- Allow for post-machining tolerances and surface finish
- Orient parts to minimize stair-step effect
- Consider effects of thermal stresses during printing
- Design-in features like tabs to ease support removal
Simulation tools help evaluate SLM printability during the design phase itself.
SLM Printing Equipment
Major SLM system manufacturers:
Công ty | Model |
---|---|
EOS | EOS M series |
3D Systems | ProX DMP series |
Renishaw | AM series |
Phụ gia GE | Concept Laser M2 |
Giải pháp SLM | SLM 500 |
These turnkey systems provide automated SLM printing capabilities in different build sizes.
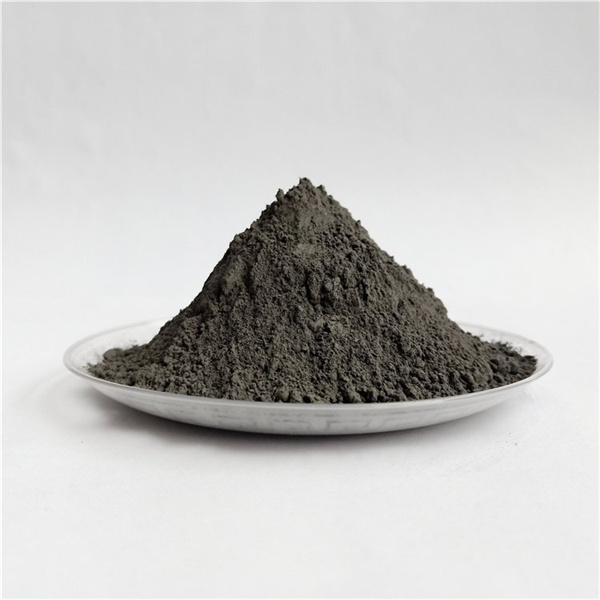
SLM Cost Economics
SLM printing costs vary based on:
- Machine purchase costs – $0.5M to $1.5M
- Material costs – $50-$150/kg for common metals
- Labor costs – machine operation, post-processing
- Build rates – 5-100 cm3/hr depending on parameters
- Economies of scale from higher production volumes
SLM is most cost-effective for complex low-to-medium volume production compared to other metals manufacturing processes.
Challenges of SLM Printing
Some challenges associated with SLM include:
- High residual stresses can cause part distortions
- Anisotropic material properties depending on build orientation
- Limitations on maximum part size
- Removing powder from internal channels
- Achieving surface finish comparable to machining
- Need for support structures on overhangs
- Specialized operator training required
- Powder handling risks require safety precautions
However, ongoing development is helping resolve many of these challenges.
Future Outlook for SLM
The future outlook for SLM printing is positive:
- Improved part quality with fewer defects
- Larger build volumes enable bigger parts
- Faster build speeds driven by higher laser powers
- New materials development expands applications
- Hybrid manufacturing combining SLM with machining
- Automated powder handling and post-processing
- Mainstream adoption across wider range of industries
- Declining costs make it economical for more applications
These advancements will enable SLM printed metal parts to compete with conventional manufacturing processes for an increasing number of applications.
Choosing an SLM Printing Service Provider
Here are important factors when selecting an SLM service provider:
- Experience specifically with SLM technology
- Range of equipment and build sizes offered
- Materials expertise with different metal alloys
- Secondary processing capabilities like heat treating
- Quality certifications like ISO 9001 and AS9100
- Design optimization and engineering support
- Lead time and on-time delivery track record
- Client references and testimonials
- Pricing structure – part vs volume pricing
Choosing a reliable SLM service partner ensures high quality parts produced efficiently.
Pros and Cons of SLM Printing
Ưu điểm
- Complex geometries not possible with machining
- Fast turnaround times from CAD to part
- Low material waste and buy-to-fly ratios
- Lightweighting through optimized designs
- Consolidate assemblies into single printed parts
- Customized, just-in-time production potential
- Eliminates costs of tooling, jigs, fixtures
Nhược điểm
- High machine capital investment
- Limited size based on build chamber dimensions
- Post-processing often required to finish parts
- Anisotropic properties depending on build orientation
- Lack of design standards for additive manufacturing
- Material options more limited than with machining
- Requires trained personnel to operate equipment
For low to medium volume production, SLM can provide significant advantages but it does have limitations to consider.
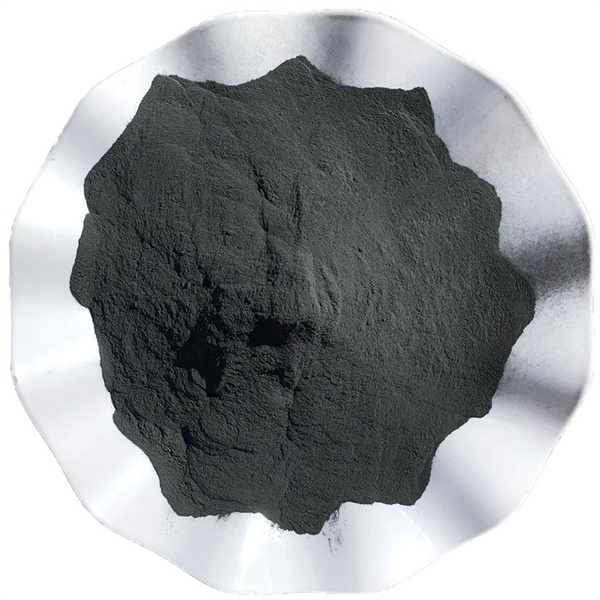
Câu hỏi thường gặp
Question | Answer |
---|---|
What materials are used in SLM? | Common SLM materials include stainless steel, aluminum, titanium, nickel alloys, tool steels, and cobalt-chrome. |
What industries use SLM printing? | Aerospace, medical, automotive, and industrial sectors are leading adopters of SLM. |
Can metal parts from SLM be used directly? | Most SLM parts need post-processing like surface finishing and heat treating before use as end-use components. |
Is SLM printing suitable for mass production? | No, SLM printing is better suited for small to medium batch sizes rather than mass production volumes. |
What precision and surface finish can SLM achieve? | Precision of +/- 0.1-0.2% is possible. Surface roughness ranges from 10-30 μm before finishing. |
Phần kết luận
SLM printing enables on-demand production of complex, high-performance metal parts with a digital manufacturing workflow. As the technology continues to mature, SLM will become viable for more mainstream applications across different industries. The unique capabilities of SLM printing will empower engineers and designers to create innovative next-generation products using additive manufacturing.