Nóng isostatic nhấn (HIP) is a manufacturing process used to eliminate porosity and increase the density of metals, ceramics, and other materials. This article provides an overview of how HIP works, the main equipment involved, typical applications, and guidelines for selecting HIP services.
What is Hot Isostatic Pressing and How Does it Work?
Hot isostatic pressing is a high pressure, high temperature densification process used to remove internal voids and porosity in materials. The goal is to improve the mechanical properties and performance by eliminating defects.
HIP achieves high pressures through an isostatic medium, which is a gas or liquid applied uniformly in all directions. This subjects the material to an equal force from all sides as opposed to unidirectional pressure. The high temperature plasticizes the material so the pressure can collapse internal voids and fuse defects closed.
The combination of heat and pressure during HIP leads to densification and significant improvements in fracture toughness, fatigue, strength, leakage, and other properties in treated parts.
The HIP Process Step-by-Step
Hot isostatic pressing involves multiple stages to encapsulate, heat, pressurize, cool, and release parts. The main steps are:
- Load – The parts are fixtured and loaded into a HIP vessel. Several small parts can be batched together.
- Seal – The vessel is evacuated, sealed shut, and leak tested. The parts must be completely enclosed.
- Heat – The vessel is heated up to the target HIP temperature, which depends on the material. This takes several hours.
- Pressurize – Once at temperature, high pressure gas is introduced into the vessel, subjecting the contents to isostatic pressure up to 30,000 PSI.
- Hold – The temperature and pressure are held for a duration ranging from 1-6 hours depending on requirements.
- Cool – After the hold time, the vessel is allowed to cool before releasing the pressure.
- Unload – The vessel is opened, the encapsulation material removed, and the treated parts unloaded.
This cycle times ranges from 4-10 hours based on the HIP process parameters required. Parts can go through multiple HIP cycles if needed.
Table 1 outlines the four key process parameters – temperature, pressure, time, and heating/cooling rates.
Process Parameter | Typical Ranges |
---|---|
Nhiệt độ | 1000 – 2000°C (1830 – 3630°F) |
Pressure | 15,000 – 30,000 PSI |
Time | 1 – 6 hours |
Heating & Cooling Rates | 100 – 500°C/hour (180 – 930°F/hour) |
Table 1: Key process parameters for hot isostatic pressing
How HIP Improves Material Properties
The high pressures and temperatures during HIP facilitate multiple changes in the material at a microstructural level:
- Closing of internal pores and voids
- Diffusion bonding of powder particles
- Elimination of micro-cracking
- Removal of casting defects
- Improved homogenization
- Grain refinement
This significantly improves density, strength, ductility, and other mechanical properties. Key benefits include:
- Increased load bearing capacity
- Higher fracture toughness
- Improved fatigue life
- Enhanced corrosion resistance
- Reduced variability in material performance
- Leak-proofing for gas or fluid containment
- Restoration of ductility in embrittled alloys
HIP is often used as a post-processing step after additive manufacturing to improve the density, performance, and reliability of 3D printed parts.
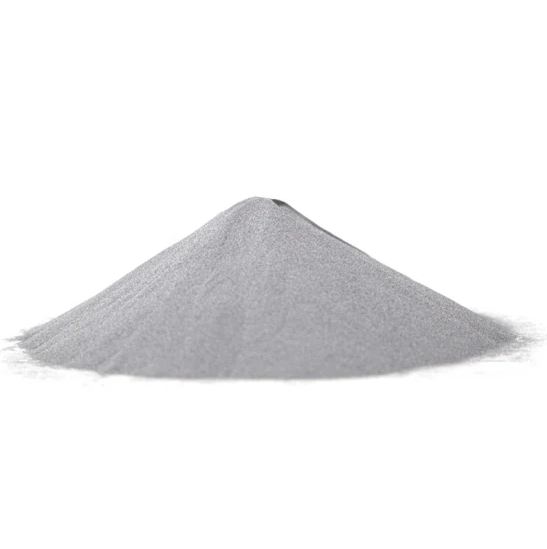
HIP Equipment Types and System Components
There are two main types of HIP systems:
Gas Pressure Systems
- Use an inert gas such as argon as the isostatic medium.
- Can achieve higher pressures – up to 30,000 PSI.
- Used for higher temperature HIP cycles above 1200°C.
- Suitable for reactive materials like titanium alloys.
Liquid Pressure Systems
- Use a liquid such as oil as the pressurizing medium.
- Typically limited to 10,000 PSI pressure capacity.
- Used for lower temperature HIP below 1000°C.
- Allow faster cooling rates due to better heat transfer.
In addition to the main pressure vessel, HIP systems include several auxiliary components:
- Các yếu tố sưởi ấm – Graphite or metal resistance heaters that heat the vessel.
- Cooling system – For active cooling via water or oil to achieve faster cooling rates.
- Vacuum pumps – For initial degassing and evacuation of the vessel.
- Gas boosters – Intensifiers to compress the gas to required pressure levels.
- Control system – For programming and monitoring of the HIP cycle.
Advanced HIP machines may also incorporate features like rapid cooling capabilities, multi-stage cycles, higher throughput, and Industry 4.0 data capabilities.
Table 2 summarizes the different equipment types and main components of a HIP system:
Equipment Type | Heating Method | Pressurizing Medium | Maximum Pressure | Typical Temperature Range | Key Components |
---|---|---|---|---|---|
Gas HIP | Electrical resistance heating | Inert gas – argon | Up to 30,000 PSI | Above 1200°C | Vessel, heaters, gas boosters, control system |
Liquid HIP | Electrical resistance heating | Liquid – oil | Up to 10,000 PSI | Below 1000°C | Vessel, heaters, intensifier, cooling system, control system |
Table 2: Comparison of different HIP equipment types and main components
HIP System Size and Capacity
HIP machines are characterized by the vessel size and usable diameter. Typical capacities range from 1-100 inches in diameter.
Smaller laboratory units under 6 inches are used for research and pilot production. Mid-size systems between 18-42 inches are common for production applications. Large HIP units over 60 inches in diameter are used to densify extremely large parts.
The main size metrics are:
- Vessel diameter – The internal diameter of the pressure vessel in inches. This limits the maximum size of parts.
- Charge size – The total volume that can be loaded for densification in one cycle.
- Throughput – The production rate based on the cycle time. Smaller more frequent batches provide higher throughput.
In addition to size, key factors in selecting a HIP system include the maximum temperature, pressure rating, cooling rate, and cycle time.
Table 3 indicates common vessel sizes and corresponding capacities.
Vessel Diameter | Typical Charge Size | Suitable Applications |
---|---|---|
1-6 inches | Up to 0.5 ft3 | Small parts, research |
18 inches | 1-2 ft3 | Medium parts |
24-42 inches | 4-12 ft3 | Large parts, high production |
Above 60 inches | Above 20 ft3 | Very large parts |
Table 3: Comparison of HIP equipment sizes and capacity
HIP Process Standards and Codes
Several standards exist that specify procedures and requirements for hot isostatic pressing to achieve proper densification. These help define the process parameters, inspection methods, safety, and qualification protocols.
Some of the main standards include:
- AMS-H-81200 – SAE aerospace standard for HIP of parts
- ISO-20421 – International standard for HIP of metal powders
- ASTM F-3049 – Standard guide for HIP for metal injection molded materials
- EN-28401 – European standard for HIP vessels
Parts made using HIP may also need to meet industry or application-specific standards, for example in aerospace, defense, nuclear, or oil & gas sectors.
It is important to review all applicable codes and standards when defining a HIP process to achieve densification goals while meeting regulatory requirements.
Typical HIP Applications and Suitable Materials
Hot isostatic pressing is used across many industries to improve the properties of metals, alloys, ceramics, and composite materials.
Typical applications include:
Không gian vũ trụ
- Turbine blades, disks, housings
- Structural airframe components
- Rocket nozzles and combustion chambers
Ô tô
- Engine valves and connecting rods
- Transmission gears
- Suspension components
Năng lượng
- Oil field tools and drill bits
- Valves, pipes, and vessels
- Nuclear fuel elements
Công nghiệp
- Cutting tools and dies
- Hot and cold work tool steels
- Hard metals like tungsten carbide
sản xuất phụ gia
- HIP of 3D printed metals to improve density, strength, and surface finish
Almost any material can benefit from HIP densification. The most common alloys and material types include:
- Thép không rỉ
- Thép công cụ
- Titanium & nickel alloys
- Superalloys – Inconel, Waspaloy
- Tungsten & molybdenum alloys
- Ceramics – silicon nitride, alumina, zirconia
- Metal matrix composites
Table 4 summarizes some applications of hot isostatic pressing by material and industry:
Ngành công nghiệp | Materials & Alloys | Typical Parts & Uses |
---|---|---|
Không gian vũ trụ | Titanium, nickel & iron alloys | Turbine blades, structural airframe parts |
Phòng thủ | Armor materials, tungsten alloys | Body armor plates, penetrators |
Ô tô | Thép công cụ, Superalloys | Gears, connecting rods |
Dầu & amp; khí ga | Stainless steels, Inconel | Downhole tools, valves |
Sản xuất điện | Superalloys, composites | Turbine blades, heat exchangers |
sản xuất phụ gia | Titanium, Inconel, CoCr | 3D printed metals, implants |
Table 4: Hot isostatic pressing applications by material and industry
HIP Process Development
Determining the appropriate HIP process parameters requires development testing based on the material, part design, and properties desired.
The key steps in process development are:
- Establish densification goals – target density, properties
- Characterize starting material – composition, defects, voids
- Perform thermal analysis to determine HIP temperature
- Analyze capsule design – size, fixturing, venting
- Run HIP trials – vary time, temperature, pressure
- Test samples to measure density, properties
- Optimize cycle based on results
This development aims to define the minimum parameters needed to achieve full densification and improvements in fracture toughness, fatigue, strength, and other mechanical properties.
Rapid process optimization methods like design of experiments (DOE) can accelerate HIP parameter development compared to traditional one-factor-at-a-time testing.
Design Guidelines and Considerations for HIP
Several design factors must be considered when developing parts intended for hot isostatic pressing:
Wall Thickness
- Thicker sections over 2 inches may require thermal demolding cycles
- Use draft angles to avoid trapped powder
- Optimize flow to allow venting
Surface Finish
- As-HIPped surfaces have roughness over 125 microinches
- Post-HIP machining is often required
- Tolerances around 0.02 inches or lower are difficult
Hình học
- Avoid sharp corners which hinder densification
- Design uniform sections for even HIPping
- Minimize trapped volumes
Nguyên vật liệu
- Match alloy composition to HIP temperature range
- Consider HIP effects on microstructure
- Use compatible metals for assemblies
Performing engineering simulation of the HIP process can identify problem areas in the design requiring modification to enable full densification.
Table 5 summarizes some key design guidelines for parts to be hot isostatic pressed:
Design Aspect | Recommendations |
---|---|
Wall thickness | Keep sections under 2 inches to allow venting of trapped gases |
Surface finish | Expect as-HIPped roughness over 125 microinches |
Corners | Use large radius fillets instead of sharp corners |
Tolerances | Keep tolerances above 0.02 inches for as-HIPped condition |
Trapped volumes | Minimize enclosed volumes not connected to the exterior |
Venting | Ensure pathway for trapped gases to escape |
Draft angles | Incorporate draft angles to facilitate powder removal |
Fixturing | Design fixturing to prevent part movement during HIP |
Table 5: Hot isostatic pressing design guidelines
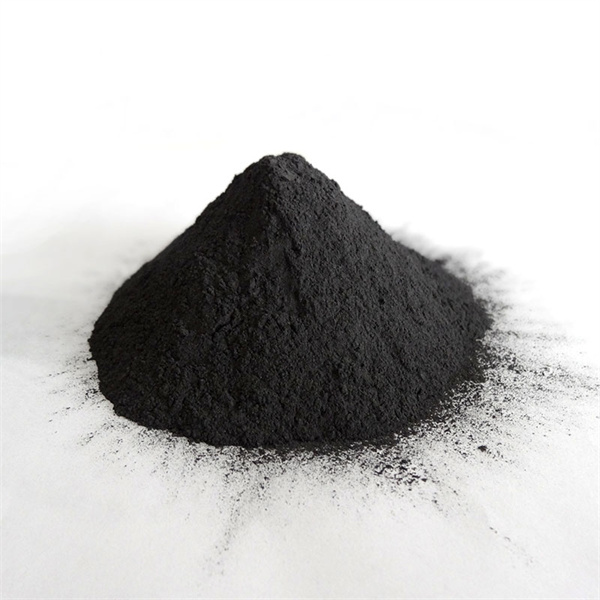
Selecting a HIP Service Provider
Companies that do not have in-house HIP capabilities can utilize toll HIP service providers to densify parts. Here are key factors in selecting a vendor:
- Thiết bị – Consider maximum temperature, pressure, and part size needs.
- Experience – Look for expertise in your industry and applications.
- Chất lượng – Ensure certifications and process controls are in place.
- Turnaround time – Evaluate logistics and typical lead times.
- Data – Can they provide detailed HIP reports and mapping?
- R&D support – Capability to develop processes and trials.
- Trị giá – Balance capabilities against pricing and minimum charges.
Visiting a potential supplier to audit their processes first-hand is highly recommended.
Table 6 summarizes criteria to evaluate when selecting a hot isostatic pressing service provider:
Criteria | Key Questions |
---|---|
Equipment & Capabilities | Do they have required temperature, pressure, and size capabilities? |
Industry Experience | Do they have expertise in your materials and applications? |
Quality Systems | Are rigorous quality control procedures in place? Are applicable certifications held? |
Delivery & Lead Times | Where are they located? How long is the typical lead time? |
Development Support | Can they support process development trials and optimization? |
Data & Reporting | Will they provide detailed parameter reporting and mappings for each run? |
Giá cả | What is the cost structure? Are there minimum order quantities or charges? |
Table 6: Criteria for selecting a hot isostatic pressing provider
Pros and Cons of Hot Isostatic Pressing
Hot isostatic pressing offers many benefits but also has some limitations to consider.
Advantages of HIP:
- Increase density and improve mechanical properties
- Close internal voids and prevent leaks
- Consolidate powder materials into final parts
- Refine microstructure
- Mitigate casting defects
- Suitable for complex geometries
- Combine multiple steps into one (HIP + heat treat)
Disadvantages of HIP:
- High equipment investment cost
- Parts require encapsulation and fixturing
- Limited maximum part size
- Restrictions around geometry, venting, etc.
- Post-process machining often required
- Can influence microstructure in some alloys
- Cycle times are typically long
For many applications, the performance improvements enabled by HIP make it a beneficial processing step despite the longer cycle time and higher cost compared to other consolidation methods.
Careful process development and design for manufacturing is key to utilize HIP effectively while avoiding limitations around part configuration, system capacity, and tolerances.

Câu hỏi thường gặp
Here are answers to some frequently asked questions about hot isostatic pressing technology and processes:
Q: What materials can be HIPed?
A: HIP can densify and improve the properties of most alloys including stainless steels, titanium, nickel alloys, tool steels, tungsten alloys, ceramics like alumina and silicon nitride, and metal matrix composites. The material must be compatible with the temperature range of the HIP process.
Q: What size parts can be processed with HIP?
A: Typical hot isostatic presses range from 1 inch to over 60 inches in diameter. Maximum part size is limited by the internal dimensions of the pressure vessel. Larger parts may require customized HIP systems.
Q: How long does HIP take?
A: Cycle times range from 4-10 hours typically based on heating, cooling, and hold times. Large parts can take over 50 hours. Multiple HIP cycles may be used for complete densification.
Q: What is a typical HIP process?
A: A common HIP cycle is heating to 1200°C at 100°C/min followed by 1-3 hour hold at 100 MPa pressure and cooling at 200°C/min. But parameters are highly dependent on the material and application.
Q: What is the difference between hot isostatic pressing and cold isostatic pressing?
A: HIP uses high temperatures up to 2000°C combined with high pressure, while CIP uses room temperature and more moderate pressures. HIP achieves full densification and property improvements versus just consolidation with CIP.
Q: Does HIP replace other processes like heat treating or machining?
A: HIP complements other steps like heat treatment and machining. HIP provides densification then further thermal or mechanical steps help achieve the final part properties, tolerances, and finish.
Q: How much does hot isostatic pressing cost?
A: The equipment has high capital costs. For toll HIP services, pricing varies based on part size, cycle parameters, number of pieces, and other factors. Expect costs ranging from hundreds to thousands of dollars per cycle.
Q: What standards apply to HIP?
A: Key standards include AMS-H-81200 for aerospace applications, ISO-20421 for powder HIP, ASTM F-3049 for metal injection molded materials, and EN-28401 for HIP vessels. Industry-specific codes may also apply.