Tổng quan
Atomized metal refers to metal powders produced through atomization, a process where molten metal is converted into fine droplets which solidify into powder particles. Atomization allows the production of metal powders with precise particle sizes, shapes and chemical compositions.
Atomized metal powders find a wide range of applications in manufacturing, 3D printing, metal injection molding, brazing, welding, thermal spraying and more. This article provides a detailed guide on atomized metal equipment including types, characteristics, applications, specifications, suppliers, installation, operation, maintenance and more.
Types of Atomized Metal Equipment
Thiết bị | Sự miêu tả |
---|---|
Gas atomizers | Use high velocity inert gas (N2, Ar) to break up molten metal stream into fine droplets |
Water atomizers | Use high pressure water jets to atomize molten metal into powder |
Rotating electrode atomizers | Use centrifugal force from rotating metal wire or disk to disintegrate molten metal into droplets |
Ultrasonic atomizers | Use ultrasonic vibrations to create capillary waves and disintegrate molten metal stream |
Centrifugal atomizers | Molten metal poured on spinning disk breaks into droplets flung outwards by centrifugal force |
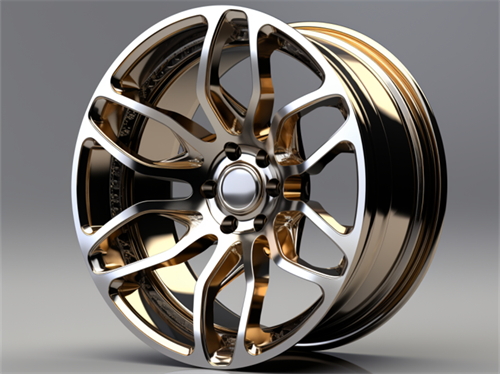
Đặc điểm của bột kim loại nguyên tử
Đặc tính | Sự miêu tả |
---|---|
Kích thước hạt | Microns to millimeters; controlled by atomization process parameters |
Hình dạng hạt | Spherical, irregular or satellite shaped; depends on method and conditions |
Phân bố kích thước | Can be made very narrow using certain atomization techniques |
Sự thuần khiết | High purity possible by using refined molten metal feedstock |
Tỉ trọng | Can approach theoretical density of the metal |
Khả năng chảy | Affected by particle size, shape and distribution; important for handling |
Sintering activity | Fine powders with large surface area sinter rapidly during compaction into solid metal |
Applications of Atomized Metal Powders
Ứng dụng | Details |
---|---|
Metal powder bed fusion | Atomized fine powders used in laser/electron beam powder bed 3D printing |
Binder phun | Stainless steel, tool steel, aluminum powders for binder jet 3D printing |
Đúc kim loại | Stainless steel, titanium, aluminum powders mixed with binder and molded |
Lớp phủ phun nhiệt | Fe, Ni, Co, Cu and alloy powders sprayed onto surfaces for wear/corrosion protection |
Brazing pastes | Ag, Cu, Ni alloy powders in paste formulations for joining metals |
Friction materials | Cu, Fe powders improve friction and wear in brake linings and clutch facings |
Hàn | Atomized Ti, Al powders added during arc welding to improve weld properties |
Powder metallurgy | Press and sinter atomized Fe, steel, Cu powders into net shape components |
Magnetics | Insulated Fe, ferrite powders pressed into magnets and inductors |
Metal catalysts | Wide range of alloy powder catalysts used in chemical industry |
Specifications of Atomized Metal Equipment
Tham số | Phạm vi điển hình |
---|---|
Khả năng sản xuất | 10-100 kg/hour |
Gas consumption | 10-100 Nm3/hr argon or nitrogen |
Cooling water usage | 100-1000 L/min |
Power consumption | 50-500 kW |
Floor space | 100-500 sqft |
Control systems | PLC, SCADA, data monitoring |
Safety systems | Gas detectors, fire suppression, safety PPE |
Molten metal handling | Launders, troughs, pouring systems |
Powder collection | Cyclones, bag filters, screw conveyors |
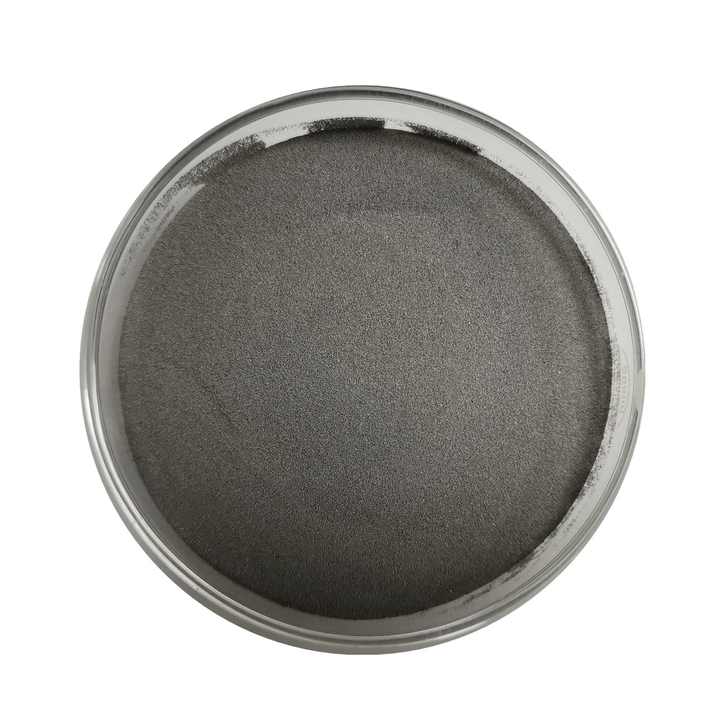
Nhà cung cấp và giá cả
Nhà cung cấp | Thiết bị | Phạm vi giá |
---|---|---|
Gasbarre | Gas atomizers | $500,000 – $2 million |
Idra | Water atomizers | $1 – 5 million |
Kessenich | Rotating electrode | $250,000 – $1 million |
Sodick | Ultrasonic nozzle | $100,000 – $500,000 |
AcuPowder | Centrifugal wheel | $50,000 – $250,000 |
Atomized metal equipment prices vary widely depending on capacity, automation features, ancillary systems, brand reputation and other factors. Budget at least $250,000 to $1 million for an industrial scale production unit.
Installation and Facilities
- Atomized metal equipment should be installed in a well-ventilated, temperature and humidity controlled production space.
- Provide sufficient overhead cranes, hoists and rigging gear for equipment installation and maintenance.
- Ensure adequate power supply, utilities and compressed air connections are in place.
- Have qualified personnel for equipment assembly, alignment, testing and commissioning.
- Design proper foundations, anchor bolts, equipment platforms for secure installation.
- Include dust collection ducting, cyclones and baghouse for collecting atomized metal powder.
- Install safety features like gas monitoring sensors, fire suppression systems.
- Allow enough free space for material handling, workflows and maintenance access.
Operation and Maintenance
Activity | Details | Frequency |
---|---|---|
Equipment inspection | Check fluid levels, leaks, unusual noise/vibration, safety devices | Daily |
Parameter monitoring | Log process data like temps, pressures, flows, power | Continuous |
Consumable replenishment | Refill cooling water, inert gas cylinders, lubricants | As needed |
Housekeeping | Clean spills, empty dust collectors, general cleaning | Daily |
Component replacement | Replace worn out nozzles, bearings, seals, filters | Per schedule |
Calibration | Calibrate sensors, measurement devices, control systems | Quarterly |
Major maintenance | Inspect major parts; repair/replace if needed | Annually |
Proper operation and preventive maintenance as per manufacturer guidelines is key to maximizing equipment life and performance. Maintain detailed logs of all maintenance work.
Choosing an Atomized Metal Equipment Supplier
Consideration | Details |
---|---|
Chuyên môn kỹ thuật | Long experience in atomization technology and metal powder production |
Customization | Ability to customize equipment to meet specific production needs |
Reliability | Proven track record of robust, reliable equipment with low failure rates |
Automation | Advanced control systems, data monitoring for optimized powder characteristics |
Aftersales service | Installation support, operator training, service contracts for maintenance |
References | Positive feedback from existing customers on equipment quality and vendor reputation |
Giá trị | Right balance of quality, performance and fair pricing |
Local presence | Physical proximity for face-to-face meetings and quick response |
Evaluate vendors thoroughly on the above parameters before investing in atomized metal equipment. Weigh factors like quality, reliability, service over lowest cost while making a selection.
Pros and Cons of Atomized Metal Processes
nguyên tử hóa khí
Ưu điểm
- Produces highly spherical, smooth powders ideal for AM, MIM etc.
- Narrow particle size distribution possible
- Operates continuously with good productivity
- Lower capital cost compared to water atomization
Nhược điểm
- Limited to smaller particle sizes, usually below 100 microns
- Requires large volumes of expensive inert gas
- Dust levels in work area may be high
Nguyên tử nước
Ưu điểm
- Can produce a wide range of powder sizes including large diameters
- Lower gas consumption than gas atomization
- Denser powders compared to gas atomized
Nhược điểm
- Less spherical particles, more satelliting
- Water treatment needed for atomizing water
- Oxide inclusions possible from water contact
Centrifugal Atomization
Ưu điểm
- Simple mechanism with minimal utilities
- Compact design with lower capital costs
- Operates semi-continuously with good productivity
Nhược điểm
- Limited control over particle size distribution
- Irregular, non-spherical particle shapes
- Contamination risk from disk wear over time
Limitations of Atomized Metal Processes
- High production costs especially for very fine metal powders
- Particle shape and size range constraints based on technique
- Requirement ofSpecialized equipment with controlled conditions
- High purity feedstock metals needed for pure powders
- Batch operation in some methods lowers productivity
- Post-processing like sieving often needed to control particle sizes
- Highly skilled personnel needed to operate equipment
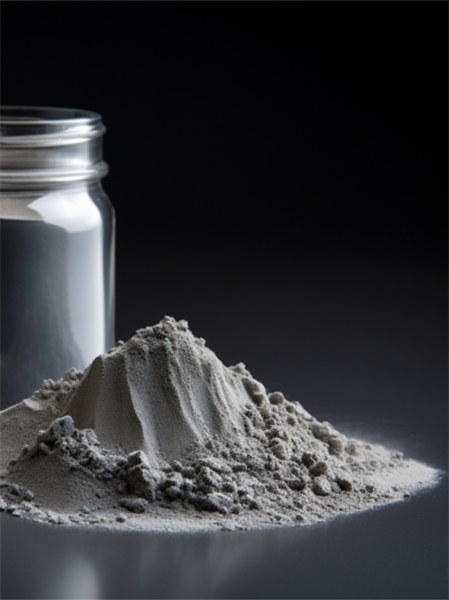
Câu hỏi thường gặp
What methods are used for classifying atomized metal powders by particle size?
Common methods for classifying atomized metal powders include:
- Sieving – Stack of sieves with decreasing mesh size separates powder into size fractions
- Air classification – Centrifugal or cyclone separators classify fines from coarser particles
- Elutriation – Counterflow air/water fluidization allows fines to overflow by gravity
- Sedimentation – Particles settle downward in liquid at rates dependent on size/density
What safety precautions are required when handling atomized metal powders?
Key safety precautions when handling atomized powders:
- Use PPE – gloves, eye protection, filter masks to prevent skin/eye contact and inhalation
- Inert gas purging to prevent powder oxidation and dust explosions
- Proper grounding of powder handling equipment to dissipate static charges
- Avoid all ignition sources in powder processing areas
- Install dust collection equipment to capture airborne powder
- Conduct air monitoring to check for combustible dust levels
How are atomized metal powders handled and transported?
Typical powder handling steps:
- Collected in drums below cyclone separators or bag house filters
- Transported in sealed containers to prevent oxygen contact
- Pneumatic conveying via nitrogen or argon through pipelines
- Vacuum suction transfer into powder storage vessels
- Manual scooping/shovelling for small batches
- Automated mechanical conveyors for large volumes
Powders are kept sealed until ready for use to prevent contamination.
What steps are taken to prevent contamination during atomized metal powder production?
- Use high purity raw materials and feedstock
- Maintain inert atmosphere using argon/nitrogen
- Keep oxygen and moisture out through sealing
- Avoid contact between powder and tramp metal
- Frequent cleaning of equipment contacting powder
- Remove oil and grease residues using solvents
- Sieving/classification to isolate irregular particles
- Analysis to identify and eliminate impurity sources
What are the most common applications for stainless steel powders produced via atomization?
Typical applications of atomized stainless steel powders:
- Additive manufacturing – Selective laser melting, binder jetting
- Metal injection molding of small, complex parts
- Brazing pastes and solder fillers for joining
- Powder metallurgy pressing into porous filters
- Self-lubricating bearings manufacturing
- Production of stainless steel fibers for textiles
- Electrochemical machining/discharge machining electrodes
- Manufacture of stainless steel powder paints and coatings
How to choose inert gas supply systems for gas atomization?
Considerations for inert gas supply:
- Argon preferred over nitrogen for reactive metals like titanium
- High capacity gas storage tanks with backup cylinders
- Purity levels of 99.99%+ to prevent contamination
- Pressure regulators and flow meters for gas control
- Use of gas recovery systems to minimize waste
- Heated gas lines to prevent freezing of moisture
- Automated changeover and monitoring of gas parameters
- Proper alarms and interlocks for gas safety
Optimizing Atomized Metal Powder Characteristics
The properties of atomized metal powders can be optimized by controlling process parameters and atomization conditions:
Phân phối kích thước hạt
Phương pháp | Tác dụng |
---|---|
Increase molten metal flow rate | Larger mean particle size |
Use higher atomizer spinning speeds | Finer powder fraction increased |
Lower molten metal pour temperature | Tighter particle size distribution |
Classify powder via sieving/air separation | Remove oversize and undersize fractions |
Hình dạng hạt
Phương pháp | Tác dụng |
---|---|
Use gas or water atomization | More spherical particles |
Lower metal pour rate | More spherical particles |
Increase melt superheat temperature | Reduces satellites and irregular shapes |
Anneal powders after atomization | Improves spherical morphology |
Powder Purity
Phương pháp | Tác dụng |
---|---|
Use high purity metal feedstock | Reduces metallic impurities |
Add slag removal stage | Removes non-metallic inclusions |
Increase inert gas purity | Reduces gaseous impurities |
Use nickel-plated collection vessels | Lowers iron pickup |
Sieve powder to remove satellites | Increases powder purity |
Mật độ bột
Phương pháp | Tác dụng |
---|---|
Optimize atomization parameters | Uniform dense powder |
Anneal powder after atomization | Removes internal voids and pores |
Compress powder after atomizing | Work hardens and consolidates powder |
Thermomechanical processing | Improves powder microstructure |
By optimizing the atomization process and powder handling steps, the characteristics of atomized metal powders can be tailored to meet application requirements.
Emerging Trends in Atomized Metal Powder Production
Some key emerging trends in atomized powder production technology include:
- Additive manufacturing is driving demand for spherical ultrafine powders below 30 microns. New nozzles and atomization methods are enabling such powders.
- Automation of powder production using Industry 4.0 concepts allowing remote monitoring, control and data-driven manufacturing.
- Hybrid atomization techniques combining aspects of gas, water and centrifugal atomization for better particle control.
- Microwave assisted heating of molten metal for faster, more uniform heating prior to atomization.
- Simulation and modelling of droplet formation dynamics leading to better understanding of atomization physics.
- Development of new alloys tailored specifically for additive manufacturing applications.
- Improved powder handling systems with integrated sieving, classification and storage.
- Continuous powder production processes instead of batch methods for higher throughput.
- Advanced control systems using AI and machine learning algorithms for automated optimization of atomization process.
- Specialized gas atomization nozzles optimized for reactive metals like titanium and aluminum alloys.
- Recycling and reusing scrap metal powders from AM processes using thermal treatments.
- In-process monitoring techniques such as infrared imaging for better powder quality control.
Phần kết luận
Atomized metal powders enable critical applications across automotive, aerospace, medical, 3D printing and other key industries. With increasing demand for high quality powders, metal atomization technology continues to evolve through new innovations in process intensification, automation, alloys development and advanced characterization techniques. By adopting the latest advances, powder producers can manufacture powders in an agile, cost-effective and sustainable manner.