sản xuất phụ gia, also known as 3D printing, is revolutionizing production across industries. One of the key materials that makes this possible is metal powder. As additive manufacturing continues rapid growth, understanding metal powders is essential.
When we think about metal 3D printing, it’s easy to focus on the mind-blowing printers. Yet none of it works without high-quality metal powder! This powder serves as the “ink” for printing intricate metal parts layer by layer.
But what makes a good metal powder? What types are used today? And why does it matter? This guide takes an in-depth look to uncover everything you need to know.
Metal Powder 101
First, what exactly is metal powder? Simply put, it’s fine metallic material in powder form used as the base feedstock for 3D printing metal components.
I know what you may be thinking…metal powder sounds more like a chemistry experiment than an engineering material! But particle size and consistency is no accident here. Metal powders for AM are carefully engineered to strict specifications.
This gives prints the material integrity needed for robust real-world parts. Now let’s decode the critical characteristics that set quality metal printing powders apart.
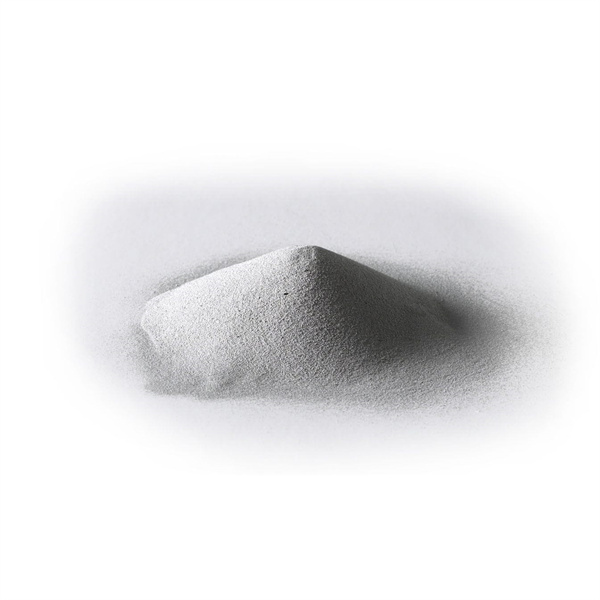
sản xuất phụ gia Metal Powder Types
Many metals and alloys can be converted into fine uniform powders for additive manufacturing. But only certain ones have found mainstream use so far.
Here’s a breakdown of the most common metal powders in 3D printing today:
Vật liệu | Key Properties |
---|---|
Titan | High strength-to-weight ratio, biocompatibility |
Nhôm | Lightweight, corrosion resistant |
Thép không gỉ | High strength, corrosion/heat resistant |
Cobalt chrome | Biocompatibility, high hardness |
Nickel Alloys | Heat/corrosion resistant, ductile |
Thép công cụ | Heat treatable, high hardness |
Titanium and aluminum see heavy use for aerospace and automotive parts where weight savings matter. Stainless steel covers a broad range of applications needing good physical properties. Exotic alloys like cobalt chrome and nickel alloys take on specialized medical or high-temp roles. And tool steels are ideal for industrial tooling, molds, dies requiring high wear resistance after heat treatment.
Now let’s break down powder metallurgy specifics in more detail!
Metal Powder Composition
As discussed before, metal powders contain pure base metals or metal alloys as very fine spherical particles. What about particle composition? Generally powders fall into these categories:
- Pre-alloys: Homogenous particles with uniform internal chemistry throughout each powder grain
- Blended alloys: Physical mixtures of different pure metal powders in specific ratios to achieve a desired bulk chemistry after printing
- Hybrid alloys: Particles contain some sections of one metal or alloy mixed with sections of another composition within each powder grain
Pre-alloys ensure consistency since every particle has identical properties. However blended alloys allow more flexibility to create custom materials. In reality, most metal printing powders used today are pre-alloys. But blended and hybrid powders add unique capabilities.
Key Metal Powder Characteristics
Now onto the meat and potatoes! Exactly what makes a metal powder right for 3D printing? Turns out powder characteristics really do matter, whether for powder bed fusion or directed energy deposition printing. Here are the crucial ones:
Kích thước hạt: Raw metal powder starts around 1-100 microns then gets further classified into size ranges under 45 microns for AM compatibility. Common bands are 0-10, 10-45, or 10-30 microns.
Hình dạng hạt: Spherical, flowing particles print the best vs jagged flakes. Powders should demonstrate good flow rates without sticking together.
Particle size distribution: A narrow distribution with minimum satellites and fines ensures homogeneous prints. Standards call for Gaussian curves with 95% between designated smallest and largest sizes.
Apparent density: Higher densities above 50% of a material’s solid density print better due to powder bed physics. Values range widely from 30-80% though depending on composition.
Tap density: Test measuring change in density under vibration. High tap density above 65% indicates better packing and spreadability.
Flow rate: Key indicator for powder spreadability scaled from 1 (very cohesive) to 10 (free flowing). Most metal AM powders fall between 3-6 with higher being better.
There are more advanced metrics like Hausner ratio, Carr index, and Scott density used to characterize flow and interparticle interactions influencing quality. But what do we make of all these cryptic powder statistics? Let’s clarify next how these properties translate into better real-world metal printing.
Why Metal Powder Properties Matter
At first glance, the importance of all these granular powder characteristics may not be obvious. After all, aren’t shiny new printers doing all the real work?
In short – the powder matters more than you might think! Here’s why:
- Powder spreading inside printers relies on flow dynamics and packing behavior. Particles that spread well and pack densely enable thinner print layers for higher accuracy and surface finishes.
- Particle size directly influences minimum feature resolution. Smaller particles around 10 microns handle intricate details better. Ultra-fine nano powders below 1 micron can produce extremely high resolutions.
- Uniform particle size distribution prevents defects like porosity or cracking from particle segregation interfering with dense prints.
- Spherical particles fuse better across print layers since they pack tightly and melt uniformly upon laser or electron beam exposure during printing.
- Apparent density indicates how much solid material resides in a certain powder volume. Higher density brings more actual metal content into play during printing.
In other words, quality powder translates to quality prints! Now let’s see how powders actually get produced with properties intentionally tuned for additive manufacturing.
Sản xuất bột kim loại
Turning raw materials into precision sub-45 micron spherical powders is an art and science unto itself. Specialized powder production techniques for metal AM include:
- Gas atomization: Blast molten metal alloy stream with high pressure inert gas to break it into fine droplets that solidify into powder. Most common method yielding small spherical particles ideal for printing.
- Water atomization: Use water jet to atomize molten metal into powder. Lower cost but limited for reactive materials like titanium or aluminum.
- Plasma atomization: Use plasma torch to atomize alloys with extremely high melting points beyond capabilities of gas atomization.
- Electrode induction melting: Repeatedly melt and evaporate end of metal rod under inert atmosphere allowing droplets to solidify into powder. Lower cost source of niche alloys.
- Mechanical attrition: Physically grind metal feedstock into powder form through ball milling or other pulverization approaches. Least preferred due to non-spherical particle shapes.
- Electrolysis: Electrically extract pure reactive metals like titanium from molten salts into powder form. Source of specialty reactive printing powders.
- Chemical reduction: Produce metal powders like nickel through chemical reactions and precipitation from aqueous solutions.
The chart below compares each modern powder production technique at a glance:
Phương pháp | Cost Level | Nguyên vật liệu | Particle Morphology | Common Use |
---|---|---|---|---|
nguyên tử hóa khí | Cao | Most alloys | Hình cầu | Mainstream AM powders |
Nguyên tử nước | Thấp | Limited alloys | không thường xuyên | Niche applications |
Nguyên tử plasma | Rất cao | Reactive metals | Hình cầu | Aerospace alloys |
Electrode Melting | Low/Moderate | Most alloys | Hình cầu | Custom alloys |
Mechanical Attrition | Thấp | Any metal | Flaky | Legacy powders |
Điện phân | Cao | Reactive metals | Variable | Specialty powders |
Giảm hóa chất | Vừa phải | Certain pure metals | Variable | Niche powders |
With an overview of powder making methods under our belt, now let’s survey the landscape of commercial metal powders engineered specifically for additive manufacturing.
Nhà cung cấp bột kim loại
A slew of professional vendors offer an expanding array of specialized metal AM powders today. Quality can vary widely however between suppliers.
When evaluating metal powder sources, perks beyond basic specs to consider include:
- Vertically integrated powder production in-house for quality control
- Range of available materials including custom alloys
- R&D for novel alloys not available elsewhere
- Scaled custom batch production vs mix-on-demand
- Powder testing services and sampling capabilities
- Secure storage and transport options
- Buyback or recycling programs
With those buyer tips in mind, below are leading global suppliers of professional-grade metal powders for AM:
Metal Powder Manufacturer | Materials Offered | Notable Highlights |
---|---|---|
Ap & amp; c | Titanium, tantalum, niobium, alloys | Aerospace focus, plasma atomization |
Arconic | Aluminum, titanium, nickel alloys | Vertically integrated, wide material range |
Phụ gia thợ mộc | Stainless steels, cobalt chrome, more | Custom alloys, quality focus |
Erasteel | Tool steels, stainless steels | Diverse steel grades and treatments |
Phụ gia GE | Titanium, aluminum, cobalt chrome, more | OEM spinoff, wide material portfolio |
Höganäs | Stainless steels, tool steels | Industry experience, scale |
Công nghệ LPW | Titanium, aluminum, nickel, more | Metal powder R&D, quality testing |
HOÀN TOÀN | Titanium, Niken, Cobalt hợp kim | Industrial gas and powder legacy |
Sandvik | Stainless steels, superalloys, more | Established powder metals leader |
With leading global suppliers covered, smaller expert boutique powder houses are cropping up too. These often focus on very niche alloys using special manufacturing techniques unavailable from big vendors.
And major material firms like Aubert & Duval, GKN Powder Metallurgy, Rio Tinto Metal Powders, and others also support AM. Check locally too since regional shops are expanding. The metal powder supply chain has something for everyone!
Metal Powder Costs
We’ve surveyed a range of advanced metal powders purpose-made for printing. But how much does quality AM-grade powder actually cost? Here are ballpark figures:
- Stainless steel 316L: $ 50-120 cho kg
- Aluminum AlSi10Mg: $70-150 per kg
- Titanium Ti64: $200-500 per kg
- Inconel 718: $80-220 per kg
- Cobalt Chrome: $130-350 per kg
- Tool steel H13: $50-150 per kg
Of course market prices fluctuate with supply and demand. But expect to pay a premium for printing consistency versus raw metal powders used in traditional press-and-sinter powder metallurgy. You get what you pay for!
Metal Powder Standards
With so many critical powder properties for additive manufacturing, standards play an important role. Groups like ASTM International, ISO, and ASME are releasing a growing list of metal powder specifications:
- ASTM F3049: Standard guide for characterizing metal powders used for AM
- ASTM F3056: Specification for additive manufacturing nickel alloy powders
- ASTM F3301: Specification for additive manufacturing stainless steel powders
- ISO/ASTM 52921: Standard terminology for AM powder bed fusion
- ISO/ASTM TS 52900: Additive manufacturing — General principles — Requirements for purchased AM parts
- ASME MSFC-Spec-3717: Specification for gas atomized titanium alloy powder
These documents provide consistent test methods and acceptance criteria for critical powder properties. Standards continue evolving with more materials and processes on the horizon. But they already establish baselines for quality and consistency.
Metal Powder Storage and Handling
Metallic powders can be reactive so proper storage and handling prevents degradation before printing. Some key measures include:
- Store in sealed containers under inert argon or nitrogen atmospheres
- Use non-reactive containers like stainless steel vs plastics
- Limit temperature extremes during transport and storage
- Ensure containers have grounding mechanisms
- AvoidVISIBLE moisture which causes clumping and oxidation
- Handle inside non-oxygen atmospheres like glove boxes
- Use hazards controls since powders can combust with air
Task-specific protective gear like static-dissipating gloves, clothing, and masks keeps handlers safe. And hazardous production material (HPM) compliant rooms or containers provide secure on-site powder storage areas before loading printers.
Treating metal powders with care ensures high reuse rates and less waste!
Metal Powder Recycling
Reusing spent powder after printing has huge economic and environmental advantages. Collection systems filter and blend used powder back with fresh stocks to enter production again.
Since metal powder represents up to 30-50% of part costs in AM, recycling drives big savings. Some best practices include:
- Use integrated vacuum systems on printers to collect overspray
- Sieve used powder to remove large impurities like spatter
- Blend recycled powder in controlled ratios with virgin stocks
- Perform quality checks on recycled blends for reuse viability
- Look for decreasing yields after multiple reuse cycles
- Refine chemically or re-atomize degraded powder when needed
As sản xuất phụ gia continues explosive expansion, recycling metal powders is crucial for growth. It’s a key pillar of sustainability in the 3D printing industry going forward.
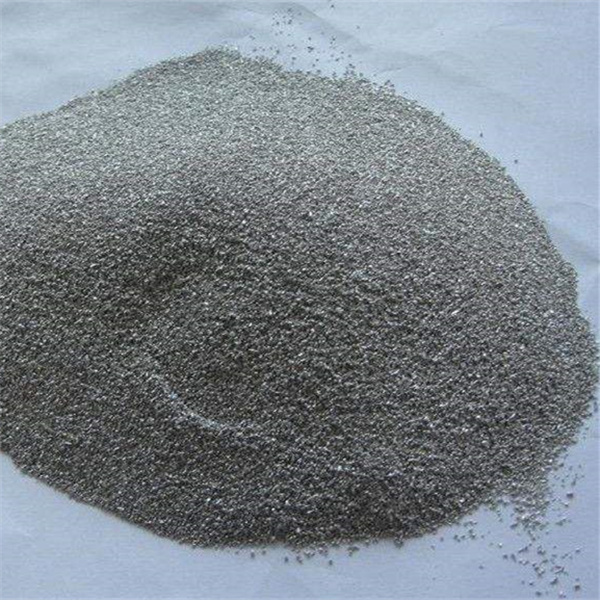
The Future of Metal Powder Development
Metal powders enabled the 3D printing revolution. And continued powder advances will support next-gen applications too. Areas seeing active R&D today include:
- Novel alloys: New chemistries extend material properties beyond conventional metallurgy
- Nano powders: Ultrafine sub-micron particles for extreme resolution
- Hybrid powders: Composite met/ceramic/polymer mixes with enhanced qualities
- Powder modification: Coatings and treatments for better flow or reactivity
- Characterization: Improved metrology and testing for quality control
- Recycling: Increased reuse and recovery capabilities
From tiny startups to the biggest materials firms, massive investments continue improving AM powders. That means more capable printing applications leveraging these powders over the horizon!
Câu hỏi thường gặp
What’s the main benefit of metal AM powders vs conventional metal powders?
AM powders focus on characteristics like particle shape, size distribution, and flow properties to enable printing vs just composition for press-and-sinter use.
How are metal AM powders made spherical with tight size distributions?
Gas and plasma atomization of molten alloys under carefully controlled conditions imparts precise particle consistency.
Is post-processing always needed on additively manufactured metal parts before use? What does this involve?
Post-processes like hot isostatic pressing (HIP) and heat treatment densify prints and enhance mechanical properties by modifying microstructures. Surface finishing is often needed too.
What are common metal alloy powders used in biomedical printing applications and why?
Titanium and cobalt chrome powders are prevalent thanks to excellent biocompatibility. Stainless steel sees uses too where cost matters like surgical instruments.
How much does a container of common metal printing powder like AlSi10Mg or 316L stainless steel weigh? And how is it shipped?
Containers typically ship 10-30 kg loads on pallets under protective atmospheres like argon. Small samples may use vacuum sealed bags. Always follow safety precautions though!