Titanium alloys powder is an important material used across many industries due to its exceptional properties like high strength-to-weight ratio, corrosion resistance, and biocompatibility. This guide provides a comprehensive overview of titanium alloys powder covering everything from types, characteristics, applications, specifications, suppliers, installation, operation, maintenance, how to select suppliers, pros and cons, and frequently asked questions.
Overview of Titanium Alloys Powder
Titanium alloys powder refers to titanium-based metallic materials in powder form containing titanium as well as other alloying elements like aluminum, vanadium, iron, and molybdenum.
Some key characteristics of titanium alloys powder:
- Tỷ lệ sức mạnh trên trọng lượng cao
- Chống ăn mòn
- Điện trở nhiệt
- Biocompatibility and non-toxicity
- Không từ tính
- Low thermal and electrical conductivity
Titanium alloys powder is used across industries like aerospace, automotive, medical, chemical, marine, sports equipment, and power generation. The most common titanium alloys are Ti-6Al-4V, Ti-6Al-4V ELI, and Ti-3Al-2.5V.
The powder metallurgy production method provides better microstructure and mechanical properties compared to ingot metallurgy. Titanium alloys powder can be used to manufacture near-net shape components through methods like metal injection molding, hot isostatic pressing, additive manufacturing, and powder forging.
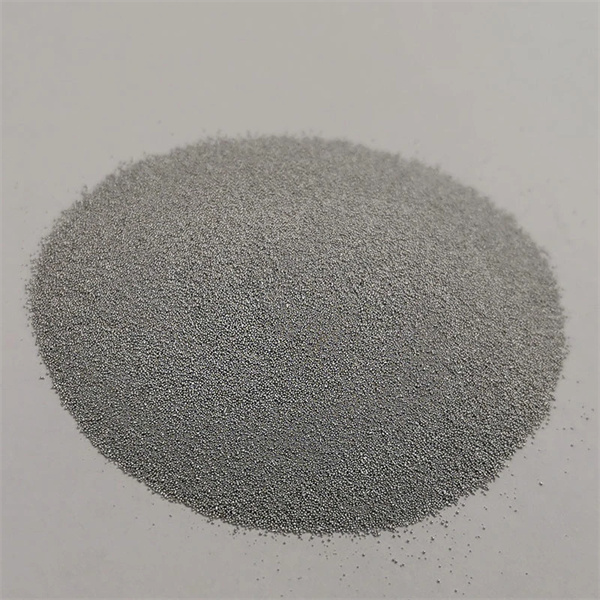
Types of Titanium Alloys Powder
There are many types of titanium alloys powder classified based on the alloying elements and metallurgical processing.
Types | Alloy Composition | Key Characteristics |
---|---|---|
Bạn-shal-hv | 6% aluminum, 4% vanadium | Most common titanium alloy, excellent strength, hardness, corrosion resistance |
Ti-6Al-4V ELI | 6% aluminum, 4% vanadium, low interstitial | Improved ductility and fracture toughness |
Đính kèm, ánh sáng | 3% aluminum, 2.5% vanadium | Excellent creep resistance, used in jet engines |
Ti-10V-2Fe-3Al | 10% vanadium, 2% iron, 3% aluminum | High strength, hardness, wear resistance |
Ti-15V-3Cr-3Al-3Sn | 15% vanadium, 3% chromium, 3% aluminum, 3% tin | Good cold formability, used in fasteners |
Ti-13V-11Cr-3Al | 13% vanadium, 11% chromium, 3% aluminum | Oxidation resistance, used in hot sections of jet engines |
Ti-15Mo-5Zr-3Al | 15% molybdenum, 5% zirconium, 3% aluminum | Excellent corrosion resistance, used in chemical plants |
Ti-35.5Nb-5.7Ta-7.3Zr-0.7O | Niobium, tantalum, zirconium, oxygen | Low modulus, biocompatibility for implants |
Applications and Uses of Titanium Alloys Powder
Titanium alloys powder finds diverse applications across industries owing to its beneficial properties. Some major applications include:
Ngành công nghiệp | Các ứng dụng |
---|---|
Không gian vũ trụ | Aircraft engine components, airframes, hydraulic systems, fasteners, nacelles |
Ô tô | Connecting rods, valves, springs, fasteners, suspension parts |
Thuộc về y học | Orthopedic and dental implants, surgical instruments |
Hóa chất | Heat exchangers, pipes, valves, pumps |
Hàng hải | Propellers, shafts, desalination plants, offshore rigs |
Sản xuất điện | Steam and gas turbine blades, heat exchangers |
Sports equipment | Golf clubs, tennis rackets, bicycles, hockey sticks |
Hóa dầu | Crackers, separators, condensers, oil rigs |
Some key usage benefits:
- High specific strength for weight reduction
- Corrosion resistance for long service life
- Biocompatibility for medical implants
- Heat resistance for high temperature applications
- Non-magnetic property for sensitive applications
Specifications of Titanium Alloys Powder
Titanium alloys powder is available in various size ranges, shapes, purity levels, and can be customized as per application requirements.
Thông số kỹ thuật | Details |
---|---|
Phạm vi kích thước | 10 – 150 micron |
Hình dạng hạt | Hình cầu, góc, hỗn hợp |
Sự thuần khiết | Commercially pure (CP), alloy grades |
Phương pháp sản xuât | Gas atomization, plasma rotating electrode process, hydride-dehydride |
Phân phối kích thước hạt | Customizable based on sieving |
Khả năng chảy | Improved flow with spherical powder |
Mật độ rõ ràng | 2.5 – 4.5 g/cc |
Chạm vào mật độ | Up to 75% of theoretical density |
Some key titanium alloy grades and their properties:
Hợp kim | Yield Strength (MPa) | Tensile Strength (MPa) | Kéo dài (%) |
---|---|---|---|
Bạn-shal-hv | 880 | 950 | 10 |
Ti-6Al-4V ELI | 825 | 900 | 15 |
Đính kèm, ánh sáng | 900 | 950 | 8 |
Titanium alloys powder can be customized as per requirements in terms of composition, particle size, shape, density, flowability, and microstructure.
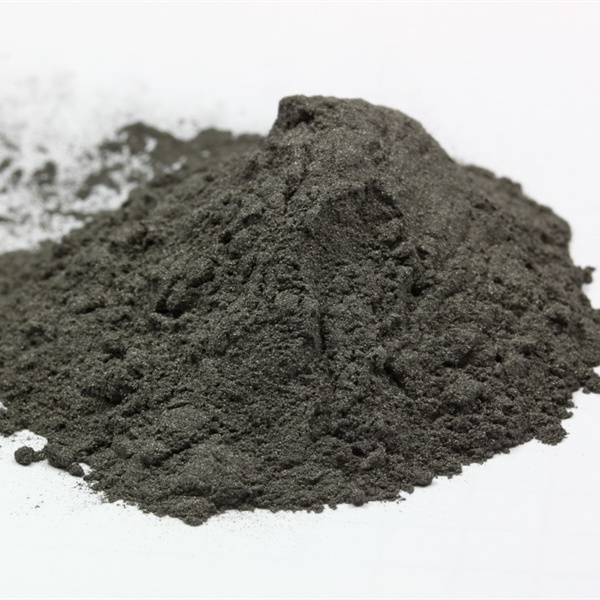
Suppliers and Pricing of Titanium Alloys Powder
Some of the major global suppliers of titanium alloys powder include:
Các nhà cung cấp | Vị trí | Phạm vi giá |
---|---|---|
Amethec | Hoa Kỳ | $50 – $120 per kg |
Ap & amp; c | Canada | $55 – $150 per kg |
TLS Technik | nước Đức | $45 – $130 per kg |
CNPC POWDER | Trung Quốc | $40 – $100 per kg |
KOBE STEEL | Nhật Bản | $60 – $140 per kg |
Giải pháp SLM | India | $30 – $90 per kg |
The price range depends on:
- Thành phần hợp kim
- Mức độ tinh khiết
- Kích thước và phân phối hạt
- Production process used
- số lượng đặt hàng
- Additional powder characterization
Reduced prices for bulk orders. Customization available at premium pricing.
Installation of Titanium Alloys Powder Equipment
Key aspects to consider for installing equipment for handling titanium alloys powder:
Thông số | Details |
---|---|
Design | Enclosed systems preferred to prevent exposure |
Thông gió | Ensure adequate ventilation to remove fine dust |
Explosion prevention | Use inert gas blanketing, avoid ignition sources |
Hazards | Consider fire, explosion, and health hazards |
Safety | Personnel protective equipment, automated systems |
Kho | Inert gas atmosphere, temperature control |
Material handling | Specialized powder transport and metering systems |
Critical design factors:
- Minimize oxygen content to prevent explosions
- Eliminate ignition sources and static buildup
- Containment systems for spillage and leakage
- Ergonomic filling and emptying provisions
- Suitable materials resistant to powder abrasion
Operation and Maintenance of Titanium Alloys Powder Equipment
Activity | Instructions |
---|---|
Filling | Controlled inert gas purging, slow powder fill rates |
Operation | Parameter monitoring and control per SOPs |
Điều tra | Check powder quality, equipment seals, leak tightness |
Maintenance | Regular inspection, replace worn parts, leak checks |
Housekeeping | Frequent cleaning to remove powder accumulation |
Safety | Follow standard precautions for titanium powder handling |
Training | Ensure personnel competence in safe handling |
Key operation guidelines:
- Maintain inert gas atmosphere at all times
- Prevent oxygen ingress above safety limits
- Follow SOPs for parameter control
- Monitor pressure, temperature, flows
- Inspect frequently for leakages
- Đảm bảo thông gió đầy đủ
- Conduct spark testing to check grounding
Choosing a Titanium Alloys Powder Supplier
Key factors to consider when selecting a titanium alloys powder supplier:
Criteria | Considerations |
---|---|
Powder quality | Composition, purity levels, particle size distribution, microstructure |
Chuyên môn kỹ thuật | Alloy knowledge, customization capabilities, testing facilities |
Manufacturing process | Gas atomization preferred for quality and consistency |
Chứng nhận | ISO, industry-specific certifications indicate quality systems |
R&D capabilities | Development of advanced alloys and powder characterization |
Prices | Competitive pricing, discounts for bulk orders |
Thời gian dẫn đầu | Ability to deliver on schedule |
Customer service | Responsiveness to inquiries, technical support |
Vị trí | Distance and logistics cost implications |
Conduct audits and sampling trials before large purchases. Review quality certifications and compliance with standards. Prioritize suppliers with strong technical expertise in titanium alloys powder manufacturing.
Pros and Cons of Titanium Alloys Powder
Ưu điểm | Nhược điểm |
---|---|
Tỷ lệ sức mạnh trên trọng lượng cao | Đắt so với thép |
Kháng ăn mòn tuyệt vời | Reactivity and flammability hazards |
Heat resistance for high temperature uses | Lower stiffness than steel |
Không độc hại và tương thích sinh học | Difficult to machine and fabricate |
Non-magnetic for sensitive applications | Limited availability of some alloys |
Good fatigue and crack growth resistance | Complex manufacturing process |
Advantages make titanium alloys suitable for critical applications in aerospace, medical, and chemical industries where performance outweighs cost. Limitations in machinability, availability, and cost restrict usage for more common applications.
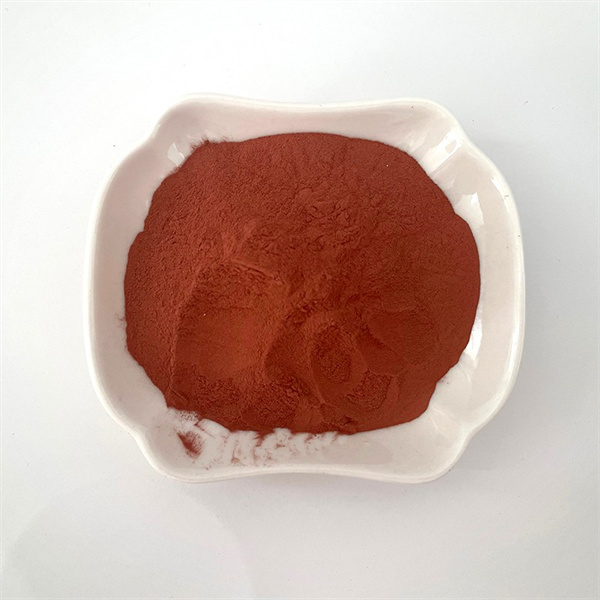
Câu hỏi thường gặp
Q: What are the main alloying elements used in titanium alloys powder?
A: The most common alloying elements are aluminum, vanadium, iron, molybdenum, zirconium, tin, niobium, and tantalum. These elements enhance strength, corrosion resistance, creep resistance, hardness, and other properties.
Q: What particle size range is commonly used for titanium alloys powder in AM?
A: For additive manufacturing using titanium alloys powder, particle size range of 15-45 microns is typically used. Finer particles below 100 microns are preferred for better sintering and part properties.
Q: What precautions are necessary when handling titanium powder?
A: Use inert gas blanketing, explosion-proof equipment, grounding to prevent static buildup, avoid all ignition sources, safety gears for personnel, and follow fire and electrostatic discharge prevention procedures.
Q: What are some common applications of Ti-6Al-4V alloy powder?
A: Ti-6Al-4V is widely used in aerospace components like airframe parts, engine components, fasteners, and medical implants like joint replacement parts owing to its strength, corrosion resistance and biocompatibility.
Q: What methods can be used to produce titanium alloy powder?
A: Common production methods include gas atomization, plasma rotating electrode process, hydride-dehydride process and electrolysis. Gas atomization is the most widely used method.
Q: How is titanium alloys powder used in additive manufacturing?
A: Titanium powder is commonly used in additive techniques like selective laser sintering, electron beam melting, and direct metal laser sintering to produce complex, lightweight components for aerospace and medical applications.
Q: What are the advantages of using powder metallurgy for titanium alloys?
A: Powder metallurgy results in fine, homogeneous microstructures with superior mechanical properties. It allows the manufacture of complex net-shape components using techniques like metal injection molding.
Q: What is the typical price range of Ti-6Al-4V alloy powder for additive manufacturing?
A: For additive manufacturing applications, Ti-6Al-4V powder of 15 to 45 microns size range costs between $80 to $150 per kilogram based on quantity and quality.
Q: What are some alternatives to titanium alloys powder in certain applications?
A: Alternatives like aluminum, magnesium, and nickel alloys are lower cost options but with inferior high temperature strength. Stainless steel offers better fabrication ability. Composites can match strength in some cases.
Q: What are the latest trends in titanium alloys powder technology?
A: Development of titanium aluminides like gamma-TiAl for jet engines, low-cost titanium powder production methods, and newer alloys like Ti-1023 and Ti-5553 are some emerging trends in titanium alloys powder technology.
Phần kết luận
Titanium alloys powder provides an exceptional combination of properties like strength, corrosion resistance, and biocompatibility which make it critical for demanding applications across aerospace, medical, chemical, and other industries. This guide summarizes the various types, manufacturing methods, specifications, pricing, pros and cons, and FAQs pertaining to titanium alloys powder to support engineers, designers, and technical procurement teams in effectively leveraging this advanced material. With continued research leading to newer alloys and lower cost powder production techniques, the applications and use of titanium alloys powder is expected to rapidly grow in the future.