Overview of Inconel Alloy 718 Heat Resisting Powder
Inconel 718 is a high-strength, corrosion-resistant nickel chromium alloy powder used for additive manufacturing and metal 3D printing applications. It has excellent mechanical properties and oxidation resistance at high temperatures.
Some key features of Inconel 718 alloy powder include:
- Sức mạnh và độ cứng cao
- Sự ăn mòn và khả năng chống oxy hóa tốt
- Excellent creep and fatigue strength
- Retains strength and hardness at elevated temperatures
- Withstands thermal fatigue and thermal shocks
- Can be used for cryogenic applications
- Compatible with many additive manufacturing processes
Inconel 718 is popular in aerospace, oil and gas, automotive, medical, and tooling industries where high strength at high temperatures, corrosion resistance, and long-term durability are required.
Types of Inconel 718 Alloy Powder
Gas Atomized Inconel 718 Powder
Gas atomized Inconel 718 powder is produced by atomizing molten alloy using high-pressure inert gas jets. This produces near-spherical powder particles with a smooth surface morphology ideal for additive manufacturing.
Advantages:
- Excellent flowability and packing density
- Consistent particle size distribution
- High powder reuse rates
- Good mechanical properties
- Low porosity and oxide inclusions
Limitations:
- More expensive than water atomized powder
- Limited to smaller particle sizes
Water Atomized Inconel 718 Powder
Water atomized Inconel 718 is produced by breaking up a molten alloy stream using high-pressure water jets. This produces irregular shaped powder particles.
Advantages:
- Lower cost compared to gas atomized powder
- Larger range of particle sizes
- Higher yield during atomization
Limitations:
- Poor flowability due to irregular shapes
- Oxide inclusions and porosity issues
- Lower powder reuse rates
- Variable particle size distribution
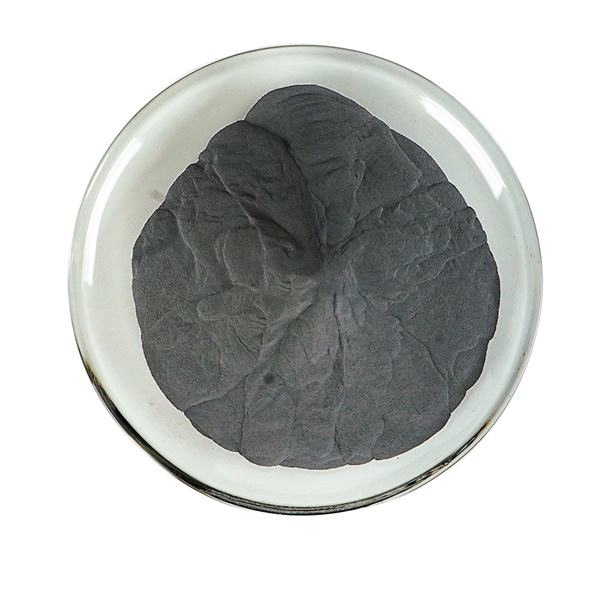
Applications and Uses of Inconel 718 Alloy Powder
Các thành phần hàng không vũ trụ
Inconel 718 is widely used to 3D print turbine blades, impellers, exhaust cones, frames, ducts, and other high-temperature components for aircraft engines and structural elements.
Gas Turbines
The high-temperature strength of Inconel 718 makes it suitable for 3D printing combustor liners, heat shields, turbine nozzles and blades for industrial and power generation gas turbines.
Phụ tùng ô tô
Inconel 718 can 3D print high-performance automotive components like turbocharger wheels and manifolds that are exposed to extreme temperatures and corrosive exhaust gases.
Biomedical Implants
The biocompatibility and corrosion resistance of Inconel 718 allow it to be used for 3D printed orthopedic and dental implants.
Chemical Processing Equipment
Inconel 718’s excellent corrosion resistance enables it to be used for 3D printing valves, fittings, reaction vessels, and pumps for chemical and petrochemical processing.
Tooling and Molds
Inconel 718 printed tools and injection molds maintain high strength and thermal stability for longer service life under high pressure and temperature conditions.
Specifications of Inconel 718 Alloy Powder
Tham số | Sự chỉ rõ |
---|---|
Thành phần | 50-55% Ni, 17-21% Cr, 4.75-5.5% Nb, 2.8-3.3% Mo, 0.65-1.15% Ti, 0.2-0.8% Al, 0.08% C max, 0.35% Si max, 0.015% S max, 0.015% P max, bal. Fe |
Tỉ trọng | 8.19 g/cm3 |
Độ nóng chảy | 1260-1336°C |
Average Particle Size | 15-45 micron |
Particle Morphology | Hình cầu |
Lưu lượng dòng chảy | ≥ 25 s/50g |
Mật độ rõ ràng | ≥ 4.0 g/cm3 |
Powder Reuse | Minimum 5 times reuse |
Design Considerations for Using Inconel 718 Powder
- Parts designed with thicker walls and conformal lattice structures allow effective heat dissipation.
- Maintain section thicknesses between 0.4 – 2 mm for better sintering.
- Include tensile test bars and witness samples for powder qualification.
- Use appropriate support structures for overhangs and angled surfaces.
- Optimize build orientation to minimize supports and avoid overhangs.
- Control layer thickness, hatch spacing and scan strategies based on part geometry.
Process Parameters for Printing Inconel 718
Table: Recommended Parameters for Printing Inconel 718
Tham số | Powder Bed Fusion | Binder Jetting | Directed Energy Deposition |
---|---|---|---|
Laser power (W) | 195-400 | – | 1000-2000 |
Scan speed (mm/s) | 600-1200 | – | 100-500 |
Layer thickness (μm) | 20-50 | 100-200 | 200-1000 |
Hatch spacing (μm) | 80-150 | – | – |
Bed temperature (°C) | 100-200 | 60-80 | – |
Khí trơ | Argon | Air | Argon |
Oxygen level (%) | 0.03-0.1 | Air | 0.03-0.1 |
Suppliers of Inconel 718 Alloy Powder
Table: Inconel 718 Powder Suppliers
Nhà cung cấp | Kích thước hạt | Delivery Form | Giá |
---|---|---|---|
Ap & amp; c | 15-45 m | Argon packed | $90-100/kg |
Phụ gia thợ mộc | 15-53 m | Argon packed | $75-120/kg |
Sandvik Osprey | 5-150 μm | Argon packed | $50-110/kg |
HOÀN TOÀN | 10-45 m | Argon packed | $80-110/kg |
Công nghệ LPW | 10-45 m | Argon packed | $70-90/kg |
Tips for Selecting Supplier:
- Ensure powder certification meets industry specifications like AMS, ASTM, ISO.
- Get safety data sheet, technical data sheet for quality and composition info.
- Ask for samples to test flowability, density, reuse and print results.
- Partner with reliable suppliers providing lot-to-lot consistency.
- Compare pricing and minimum order quantities.
Installation, Operation, and Maintenance of Printers Using Inconel 718
Table: Printer Installation, Operation, and Maintenance Guidelines for Inconel 718
Stage | Hướng dẫn |
---|---|
Installation | Clean build area and remove sources of contamination. Install fume extraction system. Check inert gas hookups and leaks. Calibrate all sensors, optics, and mechanical components. |
Operation | Establish environment controls like argon level and humidity. Set up monitoring for O2 level, gas flow rates. Use recommended processing parameters. Conduct test prints to optimize parameters. Monitor powder quality and reuse metrics. |
Maintenance | Clean optics, recoater and wipers regularly. Inspect mechanical components and guides. Prevent buildup of spatter and condensate. Change filters as needed on gas flow system. Monitor powder handling system. |
How to Select an Inconel 718 Powder Supplier
Choosing the right Inconel 718 powder supplier is key to getting consistent, high-quality powder for printing end-use parts. Here are some tips:
- Quality certifications – Supplier should have ISO 9001 and AS9100 certifications.
- Chuyên môn kỹ thuật – Look for metallurgy and AM powder expertise.
- Testing capabilities – Supplier should test every powder lot for composition, particle size, morphology, density, flow characteristics etc.
- Traceability – Ask about sourcing, production records, lot traceability.
- Post-sales support – Choose a supplier who provides support for powder handling, storage, reuse etc.
- Sampling – Ask for powder samples for testing before purchasing.
- Customer reviews – Check feedback and reviews of the supplier from industry forums and networks.
- Giá cả – Compare pricing between suppliers for the same grade powder. Consider volume discounts.
- Thời gian dẫn đầu – Supplier should provide reasonable lead time with good inventory and production planning.
Comparison of Inconel 718 vs Stainless Steel vs Cobalt Chrome Powders
Table: Comparison of Key Properties of Inconel 718, Stainless Steel, and Cobalt Chrome Alloy Powders
Tham số | Inconel 718 | Thép không gỉ | Cobalt chrome |
---|---|---|---|
Tỉ trọng | Cao hơn | Trung bình | Cao hơn |
Sức căng | Cao hơn | Trung bình | Thấp hơn |
Sức mạnh năng suất | Cao hơn | Trung bình | Thấp hơn |
Kéo dài | Thấp hơn | Cao hơn | Cao hơn |
Độ cứng | Cao hơn | Thấp hơn | Trung bình |
Chống ăn mòn | Xuất sắc | Tốt | Nghèo |
Heat Resistance | Xuất sắc | Nghèo | Tốt |
Trị giá | Cao hơn | Thấp hơn | Trung bình |
Key Takeaways:
- Inconel 718 has the highest strength and hardness while stainless steel has higher elongation.
- Cobalt chrome has lower strength than Inconel 718 but better than stainless steel.
- Inconel 718 has far superior heat and corrosion resistance than stainless steel and cobalt chrome alloys.
- Inconel 718 is more expensive than stainless steel powders but cheaper than exotic cobalt chrome alloys.
Pros and Cons of Using Inconel 718 Powder
Ưu điểm
- Excellent tensile, fatigue, and creep strength at high temperatures
- Resists thermal shocks and cycling
- Withstands oxidation and corrosion in aggressive environments
- Độ cứng cao và khả năng chống mài mòn
- Can be easily post-processed and machined
- Powder feedstock readily available
Nhược điểm
- High material cost compared to steels
- Lower elongation than stainless steel powder
- Dễ bị nứt ở độ tuổi căng thẳng
- Difficult to weld using conventional fusion welding
- Requires hot isostatic pressing (HIP) to improve densities
- Limited number of qualified suppliers
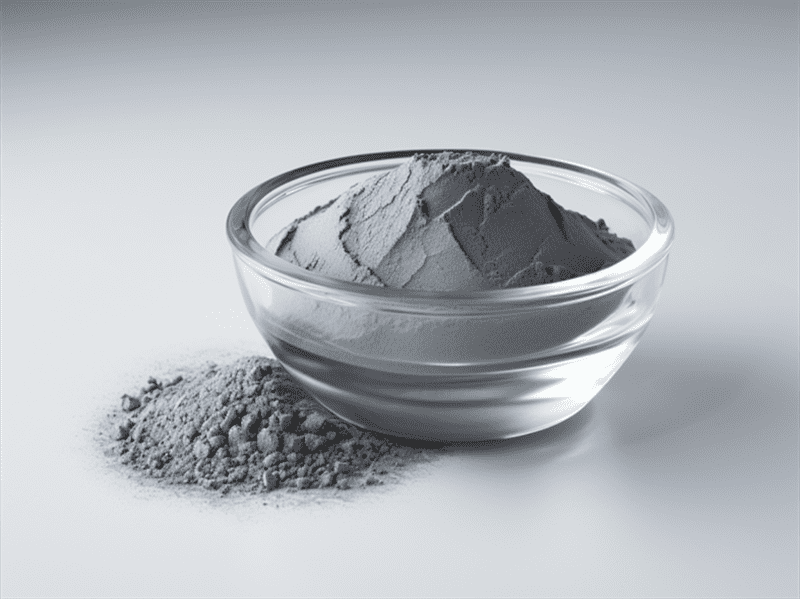
Frequently Asked Questions About Inconel 718 Powder
Q: What particle size range is recommended for Inconel 718 powder?
A: A particle size range of 15-45 microns is typically recommended for Inconel 718 powder for most AM processes. Finer powders around 10-25 microns can help achieve better resolution.
Q: What is the reuse limit for Inconel 718 powder in AM?
A: Inconel 718 powder can be reused up to 5-10 times if handled properly. Monitor powder size distribution and shape during reuse to check for degradation. Use powder sieving and conditioning systems to improve reuse rates.
Q: Does Inconel 718 powder require hot isostatic pressing (HIP) post-processing?
A: HIP helps improve the density, mechanical properties and microstructure of Inconel 718 AM parts. However, HIP may not be required if recommended build parameters are used to achieve densities above 99.5%.
Q: What are some post-processing methods used for Inconel 718 AM parts?
A: Common post-processing steps include – heat treatment, HIP, machining, shot peening, coatings, and hot forming. This helps improve surface finish, dimensional accuracy and material performance.
Q: What industries use Inconel 718 powder for AM applications?
A: Key industries using Inconel 718 powder include aerospace, oil and gas, power generation, automotive, chemical processing and biomedical. Usage is driven by high temperature strength requirements.
Q: What certifications are required for aerospace-grade Inconel 718 powder?
A: Powder manufacturers must have AS9100 certification. Inconel 718 powder lots must meet AMS specification AMS5662 and rigorous testing standards for aerospace component production.
Q: How is Inconel 718 powder made?
A: Inconel 718 is made using gas atomization or plasma atomization to produce fine spherical powder from the molten alloy for AM applications. Water atomization is also used sometimes.
Q: Does Inconel 718 require an inert atmosphere for printing?
A: Yes, an inert argon atmosphere is essential to prevent oxidation of the Inconel 718 powder during laser or electron beam powder bed fusion printing.
Q: What healthcare applications use 3D printed Inconel 718 parts?
A: Inconel 718 is used to print dental implants, surgical instruments, prosthetics, and medical devices due to its biocompatibility, corrosion resistance and high strength.