ภาพรวม
Metal powder water atomization is a popular technique used in the manufacturing industry to produce high-quality metal powders for various applications, including การผลิตสารเติมแต่ง (3D printing), powder metallurgy, and more. This process involves melting metal and forcing it through a small-diameter nozzle, where it is atomized by high-pressure water jets, resulting in the formation of fine, spherical metal powder particles.
What is Metal Powder Water Atomization?

Metal powder water atomization is a process that involves the production of metal powders by disintegrating a molten metal stream using high-pressure water jets. The molten metal is melted in a furnace and then poured through a small-diameter nozzle, where it encounters high-velocity water jets that break the metal stream into small droplets. These droplets rapidly solidify and form spherical metal powder particles due to the rapid cooling effect of the water.
The water atomization process is widely used for producing metal powders with specific particle size distributions, morphologies, and chemical compositions required for various applications. The process parameters, such as water pressure, metal flow rate, and nozzle design, can be adjusted to control the characteristics of the resulting metal powder.
Metal powder water atomization is particularly suitable for producing powders from a wide range of metals and alloys, including aluminum, copper, iron, nickel, titanium, and various other materials. The spherical shape of the particles produced by this process offers advantages in terms of improved flowability, packing density, and sinterability, making them ideal for applications like additive manufacturing, powder metallurgy, and thermal spraying.
How Does Metal Powder Water Atomization Work?
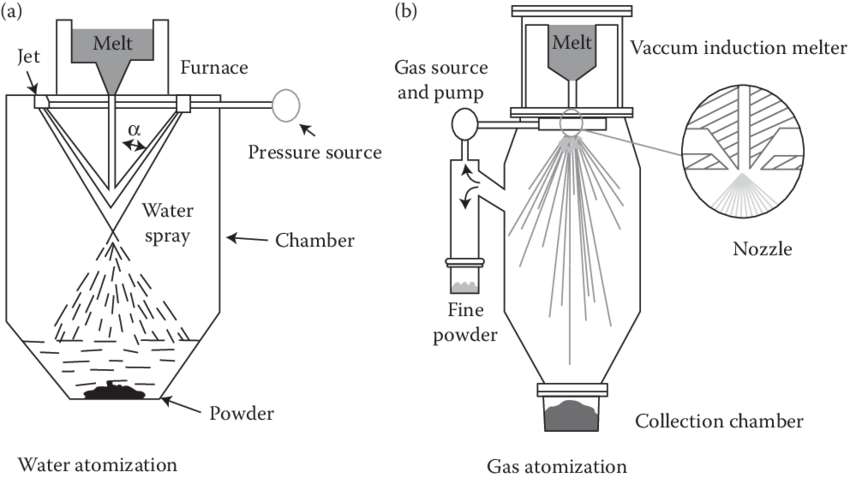
The metal powder water atomization process involves several key steps:
- Melting: The metal or alloy is melted in a furnace, typically an induction furnace or a vacuum induction melting (VIM) furnace, to achieve the desired temperature and chemical composition.
- Pouring: The molten metal is poured through a small-diameter nozzle, often made of a refractory material like ceramic or tungsten, which controls the flow rate and stream diameter.
- Atomization: As the molten metal stream exits the nozzle, it encounters high-pressure water jets that are strategically positioned around the nozzle. The water jets impinge on the molten metal stream, causing it to disintegrate into small droplets due to the high kinetic energy and cooling effect of the water.
- Solidification: The atomized droplets rapidly solidify into spherical particles as they are cooled by the water. The cooling rate and solidification behavior of the particles depend on the metal composition, particle size, and water temperature.
- Collection: The solidified metal powder particles, along with the water, are collected in a collection tank or chamber. The water is typically recycled, and the powder is separated and dried for further processing or use.
The water atomization process can be further classified into different techniques based on the specific nozzle design and water jet configuration, such as free-fall water atomization, confined water atomization, and close-coupled water atomization.
Different Types of Metal Powder Water Atomization Techniques
There are several variations of the metal powder water atomization process, each with its own unique characteristics and advantages:
- Free-Fall Water Atomization: In this method, the molten metal stream falls vertically through a series of high-pressure water jets. The water jets are arranged in a circular pattern around the metal stream, atomizing it into fine droplets. This technique is suitable for producing powders with a wide range of particle sizes.
- Confined Water Atomization: In this variation, the molten metal stream and the water jets are confined within a chamber or tube. The water jets impinge on the metal stream at an angle, resulting in improved atomization efficiency and better control over particle size distribution.
- Close-Coupled Water Atomization: This method involves positioning the water jets very close to the molten metal stream, typically within a few millimeters of the nozzle exit. This configuration ensures highly efficient atomization and produces finer powder particles with a narrower size distribution.
- Ultrasonic Water Atomization: In this technique, ultrasonic vibrations are applied to the molten metal stream, causing it to break up into fine droplets before encountering the water jets. This method can produce even finer powder particles and is often used for specialized applications.
- Vacuum Water Atomization: This process is carried out in a vacuum environment, which helps to minimize oxidation and contamination of the metal powder during the atomization process. It is particularly useful for producing reactive metal powders, such as titanium or zirconium.
Each of these techniques has its own advantages and limitations, and the choice of method depends on the specific requirements of the application, such as the desired particle size distribution, production volume, and metal composition.
metal powder water atomization equipment application
แอปพลิเคชัน | คำอธิบาย |
---|---|
Additive Manufacturing (3D Printing) | Metal powders produced by water atomization are widely used in additive manufacturing processes, such as selective laser sintering (SLS), direct metal laser sintering (DMLS), and การละลายของลำแสงอิเล็กตรอน (EBM), to create complex metal parts and components. |
ผงโลหะวิทยา | Water-atomized metal powders are used in powder metallurgy processes, such as pressing and sintering, to produce high-performance metal components with controlled porosity and precise dimensions. |
การฉีดพ่นความร้อน | Spherical metal powders from water atomization are suitable for thermal spraying processes like plasma spraying and high-velocity oxy-fuel (HVOF) spraying, which are used to apply protective coatings on various substrates. |
การฉีดยาฉีดโลหะ (MIM) | Water-atomized powders with consistent particle size and shape are used in metal injection molding, a process that combines plastic injection molding with powder metallurgy techniques to produce complex, high-precision metal components. |
Welding and Hardfacing | Metal powders produced by water atomization are used in welding and hardfacing applications, where they are applied as coatings or fillers to enhance wear resistance, corrosion resistance, or other properties. |
Water Atomization Equipment metal powders
Metal powder water atomization equipment can produce a wide range of metal powders for various applications. Here are some common metal powders that can be created using this process:
Metal Powder | แอปพลิเคชันทั่วไป |
---|---|
Aluminum Powder | Additive manufacturing (3D printing), powder metallurgy, thermal spraying, explosives |
Copper Powder | Electrical and electronics, friction materials, metal matrix composites |
ผงสแตนเลส | Additive manufacturing, powder metallurgy, hardfacing, welding |
Nickel-based Superalloy Powder | Aerospace components, gas turbine blades, additive manufacturing |
ผงไทเทเนียม | Biomedical implants, aerospace, chemical processing equipment |
Cobalt-based Alloy Powder | Cutting tools, wear-resistant coatings, hard-facing |
Iron Powder | Powder metallurgy, welding electrodes, magnetic materials |
Tungsten Carbide Powder | Cutting tools, wear-resistant coatings, mining tools |
ผงแทนทาลัม | Capacitors, chemical processing equipment, medical implants |
ผงโมลิบดีนัม | High-temperature applications, electrical components, catalysts |
These metal powders find applications across various industries, such as aerospace, automotive, biomedical, electronics, and manufacturing. The water atomization process allows for the production of spherical particles with controlled particle size distributions, which is crucial for many of these applications.
The specific powder characteristics, such as particle size range, chemical composition, and purity, can be tailored by adjusting the water atomization process parameters, including water pressure, metal flow rate, nozzle design, and atomization technique (free-fall, confined, close-coupled, etc.).
It’s important to note that some reactive metals or alloys may require specialized techniques, like vacuum water atomization, to minimize oxidation and contamination during the atomization process.
metal powder water atomization equipment benefits
Benefit | คำอธิบาย |
---|---|
Spherical Particle Shape | Water atomization produces highly spherical metal powder particles, which offer improved flowability, packing density, and sinterability compared to irregularly shaped particles. |
Controlled Particle Size Distribution | The process parameters can be adjusted to achieve desired particle size distributions, ranging from coarse to fine powders, tailored to specific applications. |
High Purity and Low Oxide Content | The rapid solidification and cooling of the molten metal droplets in water atomization minimizes the formation of oxides and other impurities, resulting in high-purity metal powders. |
Versatility | Water atomization can be used to produce powders from a wide range of metals and alloys, making it a versatile process for various industrial applications. |
Cost-Effective | Compared to other powder production methods, such as gas atomization, water atomization is generally more cost-effective, especially for larger-scale production runs. |
How to choose metal powder water atomization equipment?
ปัจจัย | Consideration |
---|---|
Application Requirements | Consider the specific requirements of the intended application, such as particle size, shape, purity, and chemical composition, to determine the most suitable water atomization technique. |
Production Volume | Evaluate the required production volume and choose a water atomization method that can efficiently meet the demand, considering factors like throughput and batch size. |
Metal Composition | Different metals and alloys may require specific process parameters or specialized atomization techniques to achieve the desired powder characteristics. |
Equipment Availability | Assess the availability and cost of the necessary equipment, including furnaces, nozzles, water jet systems, and collection systems, to ensure compatibility with the chosen water atomization method. |
Safety and Environmental Considerations | Consider factors such as the potential for metal oxidation, water and waste management, and other safety and environmental aspects when selecting the appropriate water atomization technique. |
where to buy metal powder water atomization equipment?
Source | คำอธิบาย |
---|---|
ผู้ผลิต | Many metal powder manufacturers offer water-atomized powders directly through their websites or sales channels. These manufacturers typically have specialized equipment and expertise in producing high-quality metal powders for various industries. |
Distributors | There are numerous distributors and resellers that offer a wide range of metal powders, including those produced by water atomization, from various manufacturers. These distributors can provide convenient access to different powder types and grades. |
Online Marketplaces | Several online marketplaces and e-commerce platforms have emerged as sources for purchasing metal powders, including water-atomized powders. These platforms often offer a wide selection from multiple suppliers and manufacturers. |
Industry Exhibitions and Trade Shows | Attending industry-specific exhibitions and trade shows can provide opportunities to connect with metal powder suppliers, learn about new products and technologies, and explore potential partnerships or purchasing options. |
Metal Powder Water Atomization Equipment Supplier
Met3DP Technology Co., LTD is a leading provider of additive manufacturing solutions headquartered in Qingdao, China. The company specializes in 3D printing equipment and high-performance metal powders for industrial applications.
Met3DP employs industry-leading gas atomization and PREP technologies to research and manufacture high-quality 3D printing metallic powders. Our gas atomization equipment uses a unique nozzle and gas flow design to produce metallic spheres with high sphericity and good flowability.
metal powder water atomization equipment price range
ช่วงราคา | คำอธิบาย |
---|---|
50,000−50,000−100,000 | Entry-level or smaller-scale water atomization systems suitable for research, development, or low-volume production. |
100,000−100,000−500,000 | Mid-range water atomization equipment with higher production capacities and more advanced features, suitable for small to medium-sized manufacturing operations. |
500,000−500,000−1,000,000 | High-end, large-scale water atomization systems with high throughput, automation, and advanced process control capabilities, designed for large-scale industrial production. |
$1,000,000+ | Customized, fully integrated water atomization systems with specialized features, such as vacuum or ultrasonic capabilities, for specific applications or metal compositions. |
metal powder water atomization equipment pros & Cons
ข้อดี | ข้อเสีย |
---|---|
Produces spherical particles with good flowability | Limited control over particle size distribution compared to gas atomization |
Cost-effective for large-scale production | Potential for metal oxidation and contamination |
Versatile for various metals and alloys | High water consumption and wastewater treatment requirements |
Simple and well-established process | Potential for nozzle erosion and clogging |
Scalable to different production volumes | Limitations in producing ultra-fine powders (below 20 microns) |
metal powder water atomization equipment คำถามที่พบบ่อย
- What is the difference between water atomization and gas atomization? Water atomization and gas atomization are both techniques used to produce metal powders, but they differ in the medium used for atomization. Water atomization uses high-pressure water jets to break up the molten metal stream, while gas atomization employs inert gas jets, such as argon or nitrogen. Gas atomization generally offers better control over particle size distribution and can produce finer powders, but it is more expensive and complex compared to water atomization.
- Can water atomization produce powders from any metal or alloy? Water atomization is a versatile process that can be used to produce powders from a wide range of metals and alloys, including aluminum, copper, iron, nickel, titanium, and various others. However, certain reactive metals or alloys may require specialized techniques, such as vacuum water atomization, to minimize oxidation and contamination during the atomization process.
- What factors influence the particle size and shape of water-atomized powders? Several factors can influence the particle size and shape of water-atomized powders, including the water pressure, metal flow rate, nozzle design, atomization technique (free-fall, confined, or close-coupled), and the physical properties of the molten metal, such as surface tension and viscosity.
- How does the water atomization process affect the purity and oxide content of the metal powders? The rapid solidification and cooling of the molten metal droplets in the water atomization process help minimize the formation of oxides and other impurities, resulting in high-purity metal powders with low oxide content. However, proper water management and filtration are crucial to prevent contamination from the water itself.
- What are the typical applications of water-atomized metal powders? Water-atomized metal powders are widely used in various applications, including additive manufacturing (3D printing), powder metallurgy, thermal spraying, metal injection molding (MIM), welding, and hardfacing. The spherical shape and controlled particle size distribution of these powders make them suitable for processes requiring good flowability and sinterability.
- How does the water atomization process compare to other powder production methods in terms of cost and scalability? Compared to other powder production methods, such as gas atomization or plasma atomization, water atomization is generally more cost-effective, especially for larger-scale production runs. It is also a scalable process, with equipment available for various production volumes, ranging from small research and development systems to large-scale industrial installations.
- Are there any environmental or safety concerns associated with water atomization? While water atomization is generally considered a safe process, there are some environmental and safety considerations to address. These include proper management and treatment of the water used in the process, potential metal oxidation and contamination, and the handling of hazardous materials, such as molten metals. Appropriate safety measures, personal protective equipment, and waste management practices should be followed.
- How is the water atomization process automated and controlled? Modern water atomization systems often incorporate advanced automation and process control features to ensure consistent and repeatable powder production. This includes precise control of parameters such as water pressure, metal flow rate, nozzle positioning, and atomization chamber conditions. Automated systems can also handle tasks like powder collection, drying, and packaging.
- Can water-atomized powders be used for additive manufacturing processes like selective laser sintering (SLS) or direct metal laser sintering (DMLS)? Yes, water-atomized metal powders are widely used in additive manufacturing processes like SLS and DMLS. The spherical shape and controlled particle size distribution of these powders contribute to good flowability and packing density, which are essential for successful powder bed fusion processes.
- How does the choice of water atomization technique (free-fall, confined, close-coupled, etc.) affect the powder characteristics? The choice of water atomization technique can significantly influence the powder characteristics, such as particle size distribution, shape, and surface quality. Free-fall atomization is suitable for producing powders with a wider size range, while confined and close-coupled techniques offer better control and can produce finer, more uniform particles. The specific application requirements and desired powder properties guide the selection of the appropriate atomization technique.