ภาพรวมของ Metal Powder for Sale
Metal powders are finely atomized metallic materials used in manufacturing processes like metal injection molding, additive manufacturing, and powder metallurgy. Key details about ขายผงโลหะ:
- Available in many alloys like stainless steel, titanium, nickel, aluminum, and more.
- Particle sizes typically 5-45 microns for optimal flow and packing.
- Produced via gas atomization, water atomization, carbonyl decomposition, electrolysis, and milling.
- Exhibits high surface area per unit weight compared to solid forms.
- Powder characteristics like morphology, size distribution, purity are tightly controlled.
- Sold in small R&D batches up to large commercial quantities.
- Offered in both virgin and recycled grades.
- Used to manufacture end-use components across aerospace, automotive, medical, and industrial markets.
ชนิดผงโลหะทั่วไป
วัสดุ | คุณสมบัติสำคัญ | Typical Uses |
---|---|---|
สแตนเลส | Corrosion resistance, durability | Pumps, valves, tooling |
โลหะผสมไทเทเนียม | High strength-to-weight | Aerospace, medical implants |
Cobalt-chrome | Wear/corrosion resistance | Dental, medical devices |
โลหะผสมนิกเกิล | Heat resistance, toughness | Turbine blades, rocket nozzles |
อลูมิเนียมอัลลอยด์ | Lightweight, conductive | Automotive, electronics |
Many grades and alloys are available for different applications and process compatibility.
Metal Powder Processing Equipment
อุปกรณ์ | คำอธิบาย |
---|---|
Atomizers | Convert molten alloys into fine droplets that solidify into powder particles. |
Sieves | Classify powders into specific particle size ranges. Crucial for AM. |
Mixers | Homogenize blended powders with uniform composition. |
Compactors | Compress powder into dense compacts using pressure and heat. |
Sintering furnaces | Heat powder compacts just below melting to increase strength. |
Specialized equipment required to safely handle reactive fine powder while maintaining purity and properties.
Metal Powder ข้อกำหนด
พารามิเตอร์ | ค่าทั่วไป | บทบาท |
---|---|---|
ขนาดอนุภาค | 1-100 microns | Affects packing, spreading, melting |
การกระจายขนาด | Tight range | Improves density, flowability |
สัณฐานวิทยา | Spherical preferred | Enables powder flow in AM |
ความหนาแน่นที่ชัดเจน | 40-60% of solid | Impacts final part density |
แตะความหนาแน่น | 60-80% of solid | Higher is better for compression |
อัตราการไหล | 25-35 s/50g | Fast powder flow aids AM productivity |
Oxide content | <0.5% by weight | Oxidation affects material properties |
Powder characteristics optimized based on fabrication process requirements and specifications.
Suppliers Offering Metal Powder for Sale
ผู้จัดหา | วัสดุ | Production Scales |
---|---|---|
Supplier 1 | Custom alloys, refractory metals | Small R&D batches |
Supplier 2 | Stainless, tool steels, nickel | Medium-to-large volumes |
Supplier 3 | Titanium, aluminum alloys | Large production quantities |
Supplier 4 | Exotic alloys, precious metals | Small batches |
Pricing varies based on factors like material, quality, lot size, distribution, and recycling.
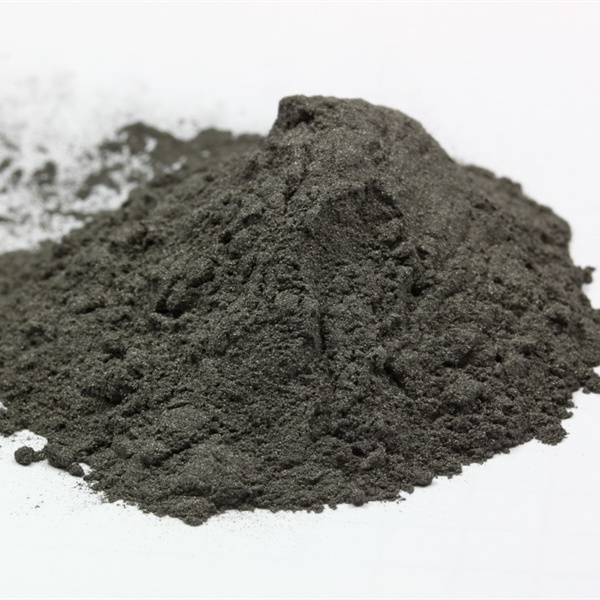
How to Choose a Metal Powder Supplier
When selecting a metal powder supplier, key factors to consider include:
- Material options – Supplier should offer a range of alloys compatible with your process.
- ระบบคุณภาพ – ISO 9001 or AS9100 certification indicates reliable quality control.
- ความเชี่ยวชาญทางเทคนิค – Look for knowledge of powder production and metallurgy.
- Lot traceability – The supplier should provide full certification for each powder lot.
- Sampling – Ask for samples to conduct own powder analysis and testing.
- ความสม่ำเสมอ – Powder composition and characteristics should not vary between lots.
- Testing capabilities – Supplier should fully test powder properties like size, shape, chemistry.
- Price – Compare pricing between suppliers for desired material, quantity, purity etc.
Partner with a metal powder supplier focused on your application needs and quality requirements.
How to Optimize Metal Powder for AM Processing
To achieve high density, defect-free 3D printed parts using metal powders, follow these AM process optimization guidelines:
- Start with high purity, spherical, gas atomized powder with a tight particle size distribution.
- Store powder properly in sealed containers under inert gas to prevent oxidation or contamination.
- Characterize new powder lots fully – size distribution, morphology, flow rate, density, chemical composition.
- Blend premixed alloys homogenously to prevent composition gradients in the final parts.
- Refresh used powder by sieving to remove satellites and large agglomerates that cause defects.
- Adjust layer thickness relative to powder particle size – a 10:1 ratio is a good starting point.
- Minimize contact with oxygen/moisture during processing to avoid oxidation.
- Dial in ideal laser/electron beam parameters by varying power, speed, etc. in test builds.
Work closely with your powder supplier to identify the optimal powder characteristics for your AM process.
Design Principles for Powder-Based AM Parts
When designing parts intended for additive manufacturing processes like binder jetting, DMLS, and SLS that utilize metal powders, consider the following design principles:
- Avoid overhangs exceeding 45 degrees to prevent unsupported surfaces.
- Design wall thicknesses greater than 0.8-1 mm to prevent fractures.
- Include small fillets and radii in corners to reduce stresses. Sharp corners crack easily.
- Position the part in the build chamber to minimize support requirements.
- Orient directionally-dependent features like text along the build direction for best resolution.
- Consolidate sub-assemblies into a single printed part when possible.
- Allow an additional 0.5-1 mm of stock material to account for post-processing steps.
- Optimize shapes for functionality rather than traditional manufacturability constraints.
Work side-by-side with AM process engineers to design parts tailored to the specific metal powder production method.
Post-Processing Metal AM Parts
Common post-processing techniques for additively manufactured metal parts include:
- สนับสนุนการกำจัด – Carefully remove support structures from the parts.
- การบรรเทาความเครียด – Heat parts to 600-800°C to relieve residual stresses from the layered buildup.
- การตัดเฉือน – CNC milling, turning, and drilling improve dimensional precision and surface finish.
- Grinding – Automated or manual grinding processes yield tighter tolerances.
- การขัด – Removes residual particle/oxide layers and creates smooth surface finishes.
- การเคลือบ – Apply functional coatings like anodizing for corrosion resistance or durability.
- กด isostatic ร้อน (สะโพก) – Further densifies internal structure by applying high temperature and isostatic pressure.
Post-process using qualified operators familiar with handling printed metal components. Incorporate any steps needed to integrate parts into end assemblies.
How to Install Metal Powder-Based Components
When preparing metal AM parts for installation and end-use:
- Clean surfaces thoroughly – remove any loose powder, oxidation, oils, films etc. for optimal bonding.
- Apply protective and functional coatings as needed – improves corrosion, wear, friction, etc.
- Control temperatures carefully during any joining operations – preheating and cooling rates are critical.
- Account for differences in thermal expansion when mating to other metal components to minimize stresses.
- Select suitable joining techniques – adhesives, mechanical fasteners, brazing, and welding can all be used effectively.
- Allow for lower ductility and impact resistance of metal AM parts compared to wrought materials. Avoid stress concentrators.
- Perform periodic inspections using techniques like x-ray, ultrasound, and penetrant testing to check for flaws.
Work collaboratively with design and manufacturing engineers throughout the integration process to ensure performance, reliability, and safety.
Operating and Maintaining Powder-Based AM Parts
To achieve optimal in-service performance from metal AM components:
- Operate within recommended temperature ranges for prolonged use per the alloy specifications.
- Avoid excessive cyclical stresses that can lead to fatigue failure – plan for extra safety factors.
- Use protective coatings and treatments to prevent corrosion damage in harsh environments.
- Routinely check parts for wear, cracks, dimensional distortions or other degradation during use.
- Disassemble, clean, and re-apply lubrication on moving printed parts like bearings and hinges.
- Take advantage of AM to produce replacement parts or spares on-demand when needed.
- Compare dimensions against original CAD regularly – material can creep over time if near yield strength.
Work with engineers familiar with the alloys and applications to develop proper maintenance schedules and procedures.
Pros and Cons of Using Metal Powder vs Traditional Methods
There are both advantages and limitations to using metal powder-based AM versus conventional manufacturing approaches:
Advantages
- Design freedom to create complex, organic shapes.
- Lightweighting by optimizing exactly for function.
- Customization and rapid prototyping capabilities.
- Reduced waste – use only required material.
- Consolidate sub-assemblies into single printed parts.
- Shorter development times for new components.
ข้อเสีย
- Higher per-part cost for small production volumes.
- Anisotropic properties due to layer-based construction.
- Post-processing often required to achieve final material specs.
- Limitations on maximum part sizes.
- Lower ductility and fracture toughness than wrought metals.
- Process sensivity to powder quality and contamination.
Weigh the pros and cons relative to production volumes, cost targets, quality needs and application requirements.
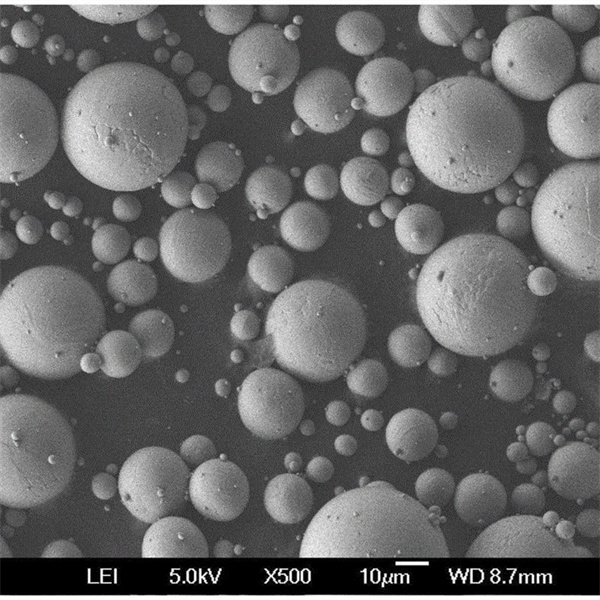
คำถามที่พบบ่อย
Q: What are some key advantages of using metal powders?
A: Design freedom, lightweighting, part consolidation, rapid prototyping, reduced waste, and shortened development times versus traditional fabrication.
Q: What post-processing methods are typically used for metal AM parts?
A: Stress relieving, machining, grinding, polishing, coatings, and hot isostatic pressing are common. Apply any steps needed for integration and assembly.
Q: How are most metal powders produced?
A: Gas atomization is a common production method where inert gas flow rapidly cools molten alloys into fine powder particles.
Q: What precautions are important when handling metal powders?
A: Use protective equipment to avoid inhaling fine powders. Handle powders in well-ventilated areas and avoid ignition sources to control fire risks.
Q: What particle size range is optimal for metal AM powders?
A: Typically 10-45 microns. Too large and the powder doesn’t spread well. Too fine and it can cake or blow around.
Q: How is recycled powder different from virgin powder?
A: Recycled powder can perform comparably if refreshed properly, but may have wider size distributions or less spherical particles that impact density.
Q: What qc testing should be done on incoming metal powders?
A: Conduct chemical composition analysis, particle size distribution, morphology checks, flow rate testing, and other characterization to verify powder quality.
Q: Which alloys are compatible with metal AM processes?
A: Most standard alloys like titanium, stainless steel, inconel, aluminum can be processed. Some higher carbon tool steels remain challenging.