Inconel is a nickel-chromium superalloy that can be 3D printed using various metal additive manufacturing processes. This guide provides a detailed overview of Inconel 3D printing including applicable technologies, material properties, applications, considerations, and more.
Introduction to 3D Printing Inconel
Inconel refers to a family of nickel-chromium-based superalloys exhibiting high strength, corrosion resistance, and heat resistance. Key properties that make Inconel suitable for 3D printing include:
- ความแข็งแรงของอุณหภูมิสูงและความต้านทานการคืบ
- Oxidation and corrosion resistance
- Good mechanical properties
- Weldability and workability
- Available in powder form for metal AM processes
Inconel alloy variants like Inconel 718 and 625 are widely used in aerospace engines, gas turbines, nuclear reactors, and other demanding applications. Additive manufacturing enables complex, optimized Inconel parts for improved performance.
This guide covers Inconel grades for AM, applicable processes, parameters, properties, applications, post-processing, costs, and comparisons.
Inconel Alloy Grades for 3D Printing
The main Inconel superalloys that can be 3D printed include:
Inconel Grades for AM
อัลลอยด์ | องค์ประกอบ | คุณสมบัติสำคัญ |
---|---|---|
Inconel 718 | Ni, Cr, Fe, Nb, Mo | Strength, toughness, weldability |
Inconel 625 | Ni, Cr, Mo, Nb | Corrosion resistance, fatigue strength |
Inconel 939 | Ni, Co, Cr, W, Nb, Ti | Hot hardness, creep strength |
Inconel X-750 | Ni, Cr, Fe, Ti, Al | High temperature oxidation resistance |
- Inconel 718 is the most widely 3D printed grade due to its optimal strength and cost.
- Inconel 625 offers the best corrosion resistance and is suitable for marine applications.
- Inconel X-750 withstands extreme temperatures up to 700°C.
- Grades are optimized for specific operating conditions and requirements.
- Custom Inconel alloys can also be formulated and 3D printed.
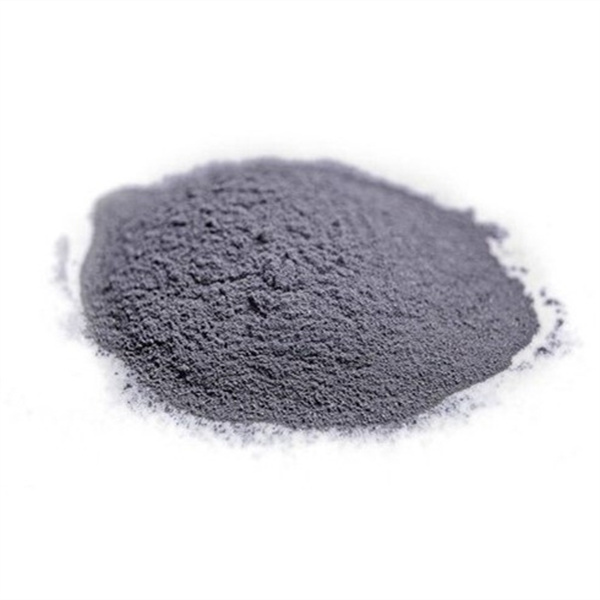
3D Printing Processes for Inconel
Inconel can be printed using both powder bed fusion and directed energy deposition processes:
Inconel 3D Printing Processes
กระบวนการ | วิธีการ | คำอธิบาย |
---|---|---|
Powder Bed Fusion | DMLS, SLM, EBM | Powder bed is selectively melted by laser or e-beam |
Directed Energy Deposition | LENS, metal plasma deposition, wire-arc AM | Focused heat source melts metal powder or wire |
- Powder bed processes like DMLS and EBM are most common for Inconel printing.
- DED methods like LENS are used for repairs and large near-net shape parts.
- Process parameters must be optimized for each specific Inconel alloy.
- Post-processing like stress-relieving heat treatment is recommended.
คุณสมบัติของ 3D Printed Inconel
3D printed Inconel exhibits the following properties:
Inconel 3D Printing Properties
คุณสมบัติ | ค่าทั่วไป |
---|---|
ความหนาแน่น | 8.19 g/cm3 |
แรงดึง | 1000-1300 MPa |
ความแข็งแรงของผลผลิต | 500-1100 MPa |
Elongation at break | 10-40% |
จุดหลอมเหลว | 1350-1430°C |
การนำความร้อน | 11-20 W/mK |
ความต้านทานการกัดกร่อน | ยอดเยี่ยมในสภาพแวดล้อมที่หลากหลาย |
ความต้านทานความร้อน | ยอดเยี่ยมถึง 700 ° C |
- Mechanical properties equal or exceed those of traditionally manufactured Inconel.
- Directionally solidified microstructures result in anisotropic properties.
- Post-processing like HIP improves density, ductility, and isotropy.
- Properties depend significantly on 3D printing process parameters.
Applications of 3D Printed Inconel
Key industries using additively manufactured Inconel parts include:
Inconel 3D Printing Applications
อุตสาหกรรม | ใช้ |
---|---|
การบินและอวกาศ | Turbine blades, engine parts, nozzles, thrust chambers |
น้ำมันและก๊าซ | Valves, wellhead components, pressure vessels |
นิวเคลียร์ | Reactor internals, heat exchangers |
เกี่ยวกับยานยนต์ | Turbocharger wheels, exhaust components |
เคมี | ปั๊ม, วาล์ว, ภาชนะปฏิกิริยา |
ทางการแพทย์ | Implants, surgical instruments |
- Aerospace is the largest adopter for flight-critical superalloy components.
- Oil and gas leverage high temperature strength for well equipment.
- Nuclear industry uses it for radioactive corrosion resistance.
- Automotive sports applications take advantage of lightweight optimized geometries.
- Medical leverages bio-compatibility for implants and instruments.
Benefits of 3D Printing Inconel vs Traditional Manufacturing
Key advantages of 3D printing Inconel compared to conventional methods:
3D Printing vs Casting/Machining
- Freedom to produce complex, organic geometries not possible otherwise
- Ability to optimize and combine parts for weight and performance gains
- Reduced lead time and costs for small batch production
- Addresses tooling/fixture constraints of subtractive methods
- Allows functional gradations and topology optimization
- Reduces material waste using optimized designs
- Just-in-time, on-demand production close to point of use
Cost Analysis for 3D Printed Inconel
Inconel 3D printing costs vary based on:
Cost Drivers
- AM machine purchase, operating costs
- Inconel powder material cost (~$100-200/kg)
- Labor for design, printing, post-processing
- Production volume
- Part size and geometry complexity
- Post-processing requirements
Typical Part Cost Range
- $50 – $500 per kg of printed parts
- Small parts ~ $100 – $5000
- Larger complex aerospace components can cost $15,000+
ความท้าทายของ 3D Printing Inconel
Some challenges with Inconel AM include:
- High material costs for Inconel powder
- Control of residual stresses
- Requirement for Hot Isostatic Pressing (HIP)
- High surface roughness requiring extensive machining
- Limited number of capable AM equipment suppliers
- Process parameter optimization for each alloy grade
- Ensuring repeatability and quality standards
Further developments in AM technology continue to improve printability, surface finish, material properties, and reduce Inconel printing costs.
Comparison of Inconel with Other Materials for 3D Printing
Inconel vs. Other Materials for AM
วัสดุ | ข้อดี | ข้อเสีย |
---|---|---|
โลหะผสมไทเทเนียม | Lower density, excellent strength | ความสามารถอุณหภูมิลดลง |
เหล็กกล้าไร้สนิม | Cost, availability | Lower strength than Inconel |
เหล็กกล้าเครื่องมือ | Hardness, wear resistance | Issues with cracking |
โคบอลต์โครเมี่ยม | ความเข้ากันได้ทางชีวภาพ | ความแข็งแรงของอุณหภูมิสูง จำกัด |
อลูมิเนียมอัลลอยด์ | Lower cost and density | Much lower strength |
- Inconel provides the best combination of high strength, heat resistance, and corrosion resistance.
- It is more expensive than stainless steels but can operate at much higher temperatures.
- Titanium has better strength-to-weight but lower operating limit.
- Choice depends on specific application requirements.
Key Takeaways on 3D Printing Inconel
- Inconel nickel-chromium superalloys provide high strength and temperature resistance.
- Widely used grades are Inconel 718, 625, X-750 which can be 3D printed.
- Main processes are powder bed fusion like DMLS/SLM and DED methods.
-find – Compares favorably and often outperforms traditionally manufactured Inconel.
- Aerospace engines and nuclear reactors are major application areas.
- Costs range from $50-500 per kg for printing, depending on factors like size.
- Advancements aim for easier printability, better finishes, and wider adoption.
คำถามที่พบบ่อย
Q: What is Inconel used for in 3D printing?
A: Inconel is used to 3D print high-performance components requiring heat resistance for aerospace engines, gas turbines, nuclear reactors, and other applications.
Q: Which 3D printing process is best for Inconel?
A: Powder bed fusion methods like DMLS and SLM are most common for printing Inconel alloys. But DED processes like LENS offer benefits for large near-net shapes.
Q: Does 3D printed Inconel require post-processing?
A: Yes, post-processing like hot isostatic pressing (HIP) is recommended to relieve internal stresses and improve material isotropy and properties.
Q: Is 3D printed Inconel as strong as wrought Inconel?
A: Yes, additive manufacturing can produce Inconel parts with mechanical properties meeting or exceeding those of traditionally manufactured wrought Inconel.
Q: What are some differences between Inconel 718 and 625?
A: Inconel 718 offers better overall mechanical properties while Inconel 625 provides superior corrosion resistance especially for marine environments.
Q: Is it difficult to 3D print Inconel?
A: Inconel can be more challenging to print compared to metals like aluminum or titanium. Careful optimization of printer parameters is required to control residual stresses and cracking.
Q: What precision can be achieved with Inconel 3D printing?
A: Dimensional accuracy of around ±0.1-0.2% is possible for Inconel AM parts depending on the process used. Machining can further improve precision if needed.
Q: Is printed Inconel as strong as hot worked Inconel?
A: Yes, powder bed fusion processes can achieve fine microstructures in Inconel resulting in strengths comparable to or greater than hot worked components.
Q: What surface finish can be expected with Inconel AM parts?
A: As-printed surface roughness typically ranges from 10-25 microns Ra. Additional machining and polishing is often required to achieve finer surface finishes.