ภาพรวมของ Inconel 718 Powder
Inconel 718 is a nickel-chromium-based superalloy powder used for high strength applications at elevated temperatures. Key properties include:
- Excellent strength up to 700°C
- High corrosion and oxidation resistance
- Good fatigue and creep resistance
- Ability to withstand cryogenic temperatures
- Compatibility with post-processing like hot isostatic pressing
Inconel 718 powder is widely used to fabricate components for aerospace, oil and gas, nuclear, and other demanding industries via metal additive manufacturing or powder metallurgy.
Types of Inconel 718 Powder
Inconel 718 powder is available in different particle size distributions, shapes, and production methods:
พิมพ์ | คำอธิบาย | ขนาดอนุภาค | Shape | วิธีการผลิต |
---|---|---|---|---|
Gas atomized | Irregular spheroidal powder | 15-75 μm | ส่วนใหญ่เป็นทรงกลม | การทำให้เป็นอะตอมก๊าซ |
Plasma atomized | Highly spherical powder | 15-45 μm | เป็นทรงกลมสูง | การทำให้เป็นอะตอมพลาสมา |
Blended | Mixture of gas atomized and crushed powders | 15-150 μm | Mixed morphology | Mechanical blending |
Alloyed | Prealloyed powder with uniform composition | 15-105 μm | เป็นทรงกลมหรือไม่สม่ำเสมอ | Gas/plasma atomization of prealloyed melt |
Spherical and prealloyed powders provide higher quality but cost more than blended or gas atomized options. The choice depends on application requirements.
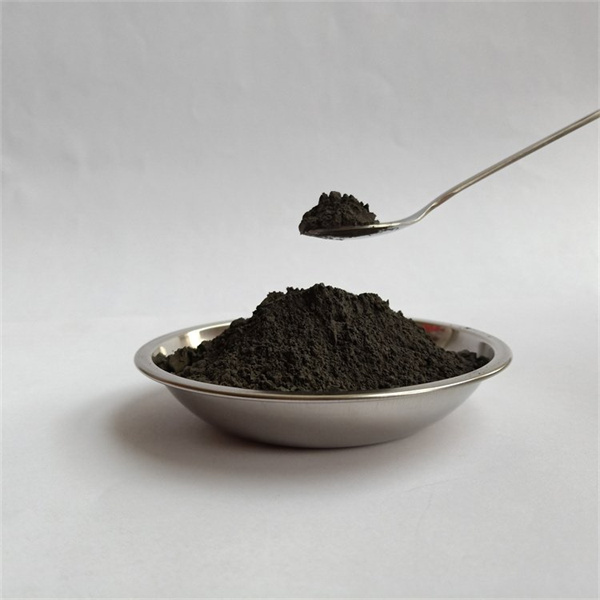
Properties and Composition of Inconel 718
Inconel 718 possesses an exceptional combination of mechanical properties and corrosion resistance:
คุณสมบัติ | ค่า |
---|---|
ความหนาแน่น | 8.19 g/cm3 |
จุดหลอมเหลว | 1260-1336°C |
ความแข็งแรงแรงดึงสูงสุด | 1,103 – 1,551 MPa |
ความแข็งแรงของผลผลิต | 758 – 1,379 MPa |
การยืดตัว | 12% minimum |
โมดูลัสของ Young ’ | 205 เกรดเฉลี่ย |
อัตราส่วน Poisson ’ | 0.29 |
โมดูลัสเฉือน | 79 GPa |
ความแข็งแรงเมื่อยล้า | 517 – 1,034 MPa |
The nominal composition of Inconel 718 is:
- Nickel: 50-55%
- Chromium: 17-21%
- Iron: Balance
- Niobium: 4.75-5.5%
- Molybdenum: 2.8-3.3%
- Titanium: 0.65-1.15%
- Aluminum: 0.2-0.8%
This combination of nickel, chromium, and niobium additions gives Inconel 718 its excellent high temperature mechanical properties.
Applications of Inconel 718 Powder
Inconel 718 powder is widely used in:
- Aerospace – Engine components like turbine blades, disks, fasteners
- Oil and gas – Downhole tools, valves, wellhead components
- Power generation – Gas turbine hot section parts, fasteners
- Automotive – Turbocharger wheels, valves, engine components
- Chemical processing – Reactor vessels, heat exchangers, piping
- Tooling – Injection molds, dies, tooling fixtures
- Medical – Orthopedic implants due to biocompatibility
Its high strength at elevated temperatures, corrosion resistance, and stability make Inconel 718 an ideal material for critical components across industries.
Benefits of Inconel 718 Powder
Key advantages of using Inconel 718 powder include:
- Parts maintain high strength and toughness up to 700°C
- Withstands oxidizing, corrosive, and cryogenic environments
- Twice the tensile strength compared to stainless steel 316L
- Excellent fatigue and creep rupture properties
- Can be precipitation strengthened by aging treatment
- Readily weldable for repairs and joining
- Resists cracking during hot isostatic pressing
- Can be reused up to 10 times with minimal deterioration
- Enables complex geometries not possible through machining
- Reduces component weight compared to solid forms
- Decreases buy-to-fly ratio relative to billet or forgings
These properties allow substantial performance improvements and weight savings in components.
Limitations of Inconel 718 Powder
Some limitations when working with Inconel 718 powder include:
- High material cost compared to steel and titanium alloys
- Part size constrained based on additive machine build volume
- Susceptible to oxidation and corrosion above 700°C
- Requires hot isostatic pressing after additive manufacturing to relieve stresses
- Difficult to fully densify during laser powder bed fusion
- Post-processing like machining can be challenging due to work hardening
- Surface finishing is required to achieve desirable roughness
- Requires dry powder handling and storage to prevent contamination
- Limited number of qualified suppliers compared to more common alloys
Design Principles for Inconel 718 Parts
Key design guidelines for Inconel 718 components fabricated from powder:
- Minimum wall thickness of 2 mm recommended for adequate strength
- Include chamfers and fillets to minimize stress concentrations
- Internal channels should have ≥ 2mm diameter for powder removal
- Limit overhangs without supports to no more than 10 mm
- Optimize build orientation to minimize supports and overall height
- Allow for isotropic shrinkage of ~20% during sintering
- Account for lower accuracy and higher surface roughness than machined parts
- Design for easier powder removal by including openings
- Allow extra machining stock if high dimensional precision or surface finish needed
Simulating builds early in the design process helps identify any issues before manufacturing.
Process Parameters for Inconel 718 AM
Critical parameters for additive manufacturing Inconel 718 include:
- Laser power: 100-500 W
- Scanning speed: Up to 10 m/s
- Beam diameter: 50-100 μm
- ความหนาของชั้น: 20-50 μm
- Hatch spacing: 50-200 μm
- Scan strategy: Alternating between layers
- Shielding gas: Argon or nitrogen
- Gas flow rate: 2-8 L/min
- Build plate temperature: 60-100°C
- Post-processing: Hot isostatic pressing, heat treatment
These parameters must be precisely optimized to obtain dense components with the desired microstructure and mechanical properties.
Post-Processing of Inconel 718 Parts
Typical post-processing steps for Inconel 718 AM components include:
- Removal of loose powder via blasting with plastic beads
- Stress relieving heat treatment at 1080°C for 1 hour followed by air cooling
- Hot isostatic pressing at 1120°C for 4 hours under 100 MPa pressure
- Wire-cut EDM to remove parts from build plate
- CNC machining – milling, drilling, turning to improve finish and precision
- Surface enhancement – grinding, sanding, polishing
- Shot peening to induce compressive stresses on surfaces
- Quality testing – tensile, hardness, microstructure, fractography
Proper post-processing is vital to achieve the material properties required by the application.
Quality Control Testing for Inconel 718
Comprehensive quality control testing ensures powder and printed part quality:
- Chemical analysis – ICP-OES confirms powder composition conforms to AMS specification
- Powder particle size distribution – Laser diffraction particle size analyzer
- Powder morphology – SEM imaging verifies spherical powder shape
- Powder microstructure – EBSD mapping of grain structure
- Powder flowability – Measured through Hall and Carney funnel tests
- Density analysis – Helium pycnometry and Archimedes method verifies >99.5% density
- Mechanical testing – Tensile, fatigue, fracture toughness, hardness testing
- Microstructure – Grain size and phase distribution using optical and SEM microscopy
- Defect analysis – X-ray and CT scans check for internal defects
- Surface roughness – Measured by stylus or optical profilometer
Extensive testing ensures that Inconel 718 parts meet strict aerospace and industrial standards.
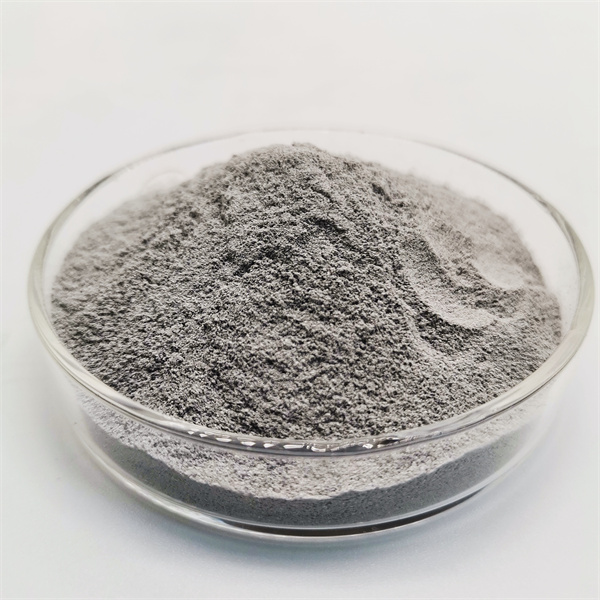
Cost Analysis for Inconel 718 AM
The costs associated with Inconel 718 AM production include:
- Machine cost – $500,000 to $1 million for quality AM system
- Material cost – $350-500/kg for virgin Inconel 718 powder
- Labor cost – Skilled operators to run build and post-processing
- Energy cost – Large electricity consumption during builds
- Post-processing – HIP, machining and other finishing costs
- ควบคุมคุณภาพ – Testing and characterization expenses
- Reusability – Unused powder can be recycled to reduce material costs
- ปริมาณการสั่งซื้อ – Higher volume orders provide economy of scale benefits
- Buy-to-fly ratio – Must consider unused powder that must be recycled
- Part geometry – Well-designed parts maximize material utilization
For low-mid volume production, AM becomes cost-effective compared to subtractive machining due to material savings and buy-to-fly ratio reduction.
Selecting an Inconel 718 Powder ผู้จัดหา
Key factors when selecting an Inconel 718 powder supplier:
- Technical expertise in gas and plasma atomization of nickel superalloys
- Range of available powder sizes and morphologies – spherical, blended, alloyed
- Quality assurance procedures and certifications – ISO 9001, AS9100, etc.
- Ability to conduct chemical analysis and particle size distribution testing
- Capacity to deliver large powder quantities with short lead times
- Customization capabilities like sieving to specific particle size distributions
- Competitive and stable pricing, especially for large quantity orders
- Ability to meet regulatory compliance if required – ITAR, REACH, RoHS
- Samples for customer powder qualification and testing
- Technical support for powder handling and storage
- Geographic proximity for faster logistics and support
Established suppliers with niche expertise in nickel alloy powders tend to best satisfy user needs in terms of quality, customization, pricing, and support.
Pros and Cons of Inconel 718 vs Stainless Steel
Advantages of Inconel 718:
- Twice the tensile strength of stainless steel 316L
- Significantly higher creep and fatigue resistance
- Withstands oxidation and corrosion up to 700°C
- Better high cycle fatigue life than steels
- Consistent properties due to nickel alloy composition
- Can be age hardened unlike standard stainless steels
- Produces stronger bonds when applied as feedstock coating
- Easier to recycle and reuse unused powder
Disadvantages of Inconel 718:
- Much higher material cost than stainless steels
- Lower maximum operating temperature than stainless
- More difficult to fully densify during AM printing
- Challenging to machine due to work hardening
- Limited number of qualified suppliers
- Susceptible to liquid metal embrittlement during AM
- Higher post-processing requirements – HIP, heat treatment
- Requires controlled inert atmosphere processing
For critical applications where performance exceeds cost considerations, Inconel 718 provides markedly superior high temperature properties compared to stainless steels.
Comparison of Inconel 718 vs Inconel 625
Inconel 718 and 625 have the following distinguishing characteristics:
อัลลอยด์ | ความแข็งแกร่ง | ความต้านทานการกัดกร่อน | การเชื่อมได้ | ค่าใช้จ่าย | Use Temperature |
---|---|---|---|---|---|
Inconel 718 | สูงมาก | ปานกลาง | ยุติธรรม | สูง | สูงถึง 700 ° C |
Inconel 625 | ปานกลาง | ยอดเยี่ยม | ยอดเยี่ยม | สูงมาก | Up to 980°C |
- Inconel 718 offers much higher tensile, creep, and fatigue strength.
- Inconel 625 provides better all-round corrosion and oxidation resistance.
- Inconel 625 has outstanding weldability while Inconel 718 is more challenging.
- Inconel 625 is costlier owing to extensive columbium alloying additions.
- Inconel 625 has higher maximum service temperature rating.
Inconel 718 is preferred for the most demanding high strength applications like aerospace components while Inconel 625 is selected when corrosion resistance is the foremost requirement.
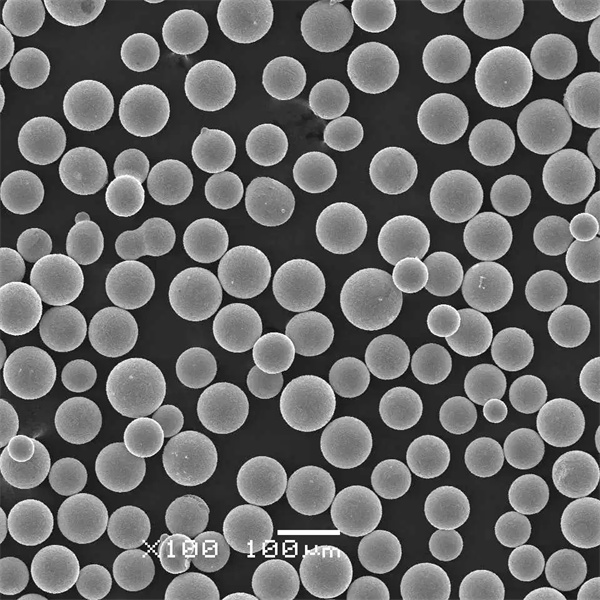
คำถามที่พบบ่อย
What particle size distribution is recommended for AM with Inconel 718 powder?
A particle size range of 15-45 microns with a majority between 20-35 microns is typically recommended for laser powder bed fusion with Inconel 718 to enable good flowability and dense compaction.
What are some post-processing heat treatments used for Inconel 718 AM parts?
Common heat treatments include 1270°C solution anneal, 960°C precipitation hardening, and 1080°C stress relieving. Multi-step aging treatments can further enhance strength and ductility.
What are some typical applications for Inconel 718 powder in aerospace?
Inconel 718 is widely used to fabricate aircraft engine components like blades, disks, fasteners, casings, and landing gear parts requiring high strength at elevated temperatures and in corrosive environments.
Does Inconel 718 require hot isostatic pressing after AM?
Yes, HIP is highly recommended after laser or electron beam powder bed fusion with Inconel 718 to eliminate internal voids and pores and improve fatigue life through microstructure homogenization.
How should unused Inconel 718 powder be handled?
All unsused powder must be handled in an inert atmosphere to prevent oxidation and contamination. Powder can be reused up to 10 times if maintained in a controlled environment. Beyond 10 recycles, new powder is recommended.