ภาพรวม
Atomized metals refer to metal powders produced through atomization, a process where molten metal is broken up into fine droplets and rapidly cooled to form a powder. The atomization process allows for precise control over the powder’s particle size, morphology, and microstructure.
Atomized metal powders are used in a wide range of applications including manufacturing, 3D printing, and surface coating. They provide benefits such as high purity, consistency, and ability to develop specialty alloys. The most commonly atomized metals include aluminum, copper, iron, nickel, and titanium.
This guide provides a detailed overview of atomized metal powders covering types, characteristics, applications, specifications, suppliers, installation, operation, maintenance, and more. It aims to help readers understand the technology and make informed choices when selecting atomized metal powders.
Types of Atomized Metals
There are two main types of atomized metal powders:
Air Atomized Metals
In air atomization, the molten metal stream is broken into droplets by high pressure air or an inert gas. Air atomized powders have a spherical morphology with a smooth surface. They are suitable for applications requiring good flowability.
Water Atomized Metals
In water atomization, the molten metal is disintegrated by high pressure water jets. Water atomized powders have an irregular shape with a rough surface texture. They provide higher compressibility preferred for pressing applications.
The table below summarizes the key differences between air and water atomized metal powders:
พารามิเตอร์ | Air Atomized | Water Atomized |
---|---|---|
รูปร่างอนุภาค | เป็นทรงกลม | Irregular, jagged |
Surface Texture | Smooth | Rough |
ความสามารถในการไหลได้ | ยอดเยี่ยม | ปานกลาง |
ความหนาแน่นที่ชัดเจน | 2 – 3.5 g/cc | 3 – 4 g/cc |
การบีบอัดได้ | ปานกลาง | สูง |
Production Rate | ต่ำกว่า | สูงกว่า |
ค่าใช้จ่าย | สูงกว่า | ต่ำกว่า |
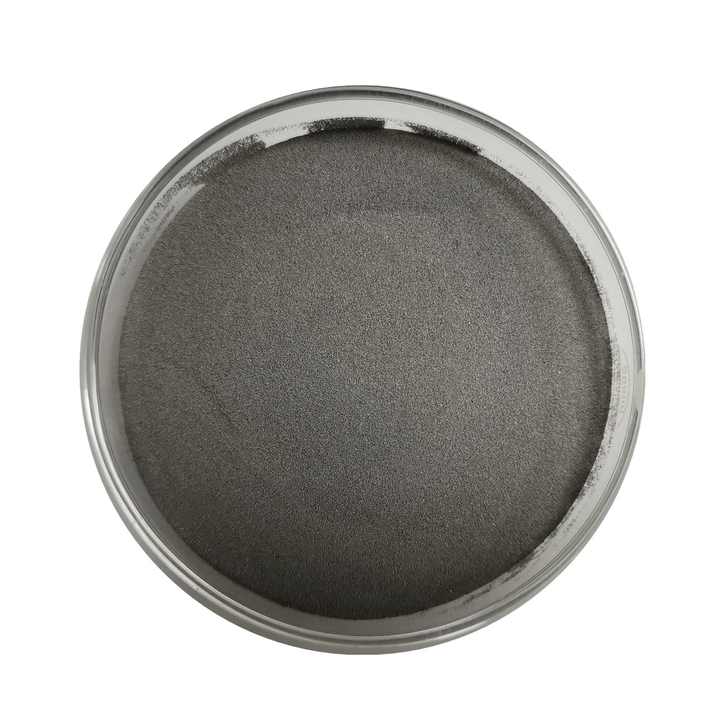
ลักษณะของผงโลหะอะตอม
The main characteristics defining the quality and performance of atomized metal powders include:
ขนาดอนุภาค – The particle size distribution determines packing density, flowability, and surface area. Tighter control over size leads to better product consistency.
สัณฐานวิทยา – Particle shape impacts density, compaction, and sintering. Spherical particles offer better flow whereas irregular shapes provide higher green strength.
ความบริสุทธิ์ – High purity is essential for critical applications. Impurities can be minimized through using raw materials with low contamination.
ปริมาณออกซิเจน – Lower oxygen content reduces powder reactivity and improves final material properties. Water atomized powders tend to have higher oxygen pickup.
ความหนาแน่นที่ชัดเจน – Higher density translates to better flow and handling efficiency. Typical values range from 25% to 60% of theoretical density.
ความสามารถในการไหลได้ – Good powder flow ensures reliability in automated processes for shaping, filling, and packaging. It depends on parameters like particle size, shape, and surface roughness.
การบีบอัดได้ – Compressibility determines the pressed part’s green strength before sintering. Irregular particle shape improves interlocking and green strength.
Carefully controlling these powder characteristics through the atomization process is crucial for achieving repeatable high performance.
Applications of Atomized Metal Powders
Atomized metal powders are used in a wide array of industries and applications leveraging their unique benefits. Some major application areas include:
Metal Additive Manufacturing
Also known as metal 3D printing, this involves building metal components layer-by-layer from powder material. Fine spherical powders with controlled size distribution are preferred for smooth flow and packing during spreading. Common materials include titanium, aluminum, nickel alloys, and tool steels.
ผงโลหะวิทยา
Atomized powders are compressed at high pressures into “green” parts and then sintered to produce finished components. Irregularly shaped powder particles offer better compressibility. Parts with complex geometries can be manufactured near net-shape, minimizing material waste.
Surface Coatings
Thermal spray techniques like plasma spraying deposit molten or semi-molten powders onto surfaces forming protective or functional coatings. Finer spherical powders improve coating density and bond strength. Wear and corrosion resistant coatings are commonly applied.
การฉีดยาฉีดโลหะ (MIM)
This combines plastic injection molding with powder metallurgy to manufacture small, complex, net-shape metal parts. Smooth flowing powders with tailored particle size and binders are required for defect-free mold filling.
Brazing and Soldering
Atomized powder preforms enable metallurgical joining of intricate components. Smooth powders with controlled size ensure optimal preform fabrication. Brazing filler metals include aluminum, silver, and copper.
วัสดุเสียดสี
Atomized metal powders serve as friction modifiers in brake pads and other applications. Copper, iron, and brass powder additions improve friction and wear resistance compared to non-asbestos organic formulations.
Specifications of Atomized Metal Powders
Atomized metal powders must meet exacting specifications tailored to the manufacturing process and end use requirements. Typical powder specifications are outlined below:
การกระจายขนาดอนุภาค
พารามิเตอร์ | ช่วงทั่วไป |
---|---|
D10 | 10 – 45 μm |
D50 | 20 – 75 μm |
D90 | 40 – 150 μm |
D10, D50, D90 refer to the powder particle size below which 10%, 50%, and 90% of the sample lies respectively. Tighter distribution improves density and performance.
สัณฐานวิทยา
- Shape – Spherical, irregular
- Surface Texture – Smooth, rough
- Satellites – Less than 5% by weight
ความบริสุทธิ์
- Oxygen – <1000 ppm
- Nitrogen – <100 ppm
- Carbon – <1000 ppm
- Other Impurities – Element specific
ความหนาแน่นที่ชัดเจน
- Powder Tap Density – Typically 40-60% of theoretical density
- Poured Density – 25-40% of theoretical density
Meeting powder specifications is vital for repeatable processing and final product quality. Reputable suppliers provide comprehensive certificates of analysis.
Suppliers of Atomized Metal Powders
Many companies specialized in producing atomized metal powders catering to diverse applications. Some leading global suppliers include:
Atomising Systems Limited
- HQ – Sheffield, UK
- Materials – Al, Cu, Fe, Ni
- Capacity – 4000 tons/year
- Serving AM, thermal spray markets
Sandvik Osprey
- HQ – Neath, UK
- Materials – Ti, Al, steels, superalloys
- Capacity – 14,000 tons/year
- Large portfolio for AM industry
Höganäs AB
- HQ – Höganäs, Sweden
- Materials – Fe, Cu, Al alloys
- Capacity – 300,000 tons/year
- Focus on automotive industry
โลหะผง ATI
- HQ – Pittsburgh, USA
- Materials – Ti, Ni, Al, Fe alloys
- Capacity – 15,000 tons/year
- Leading supplier for additive manufacturing
Mitsubishi Materials
- HQ – Tokyo, Japan
- Materials – Cu, Ni, cemented carbides
- Capacity – 8000 tons/year
- Strong presence in Asian markets
Prices vary widely depending on material, purity, particle size, and purchase volume. Expect to pay $20-100 per kg for common metals and $100-500 per kg for specialty alloys.
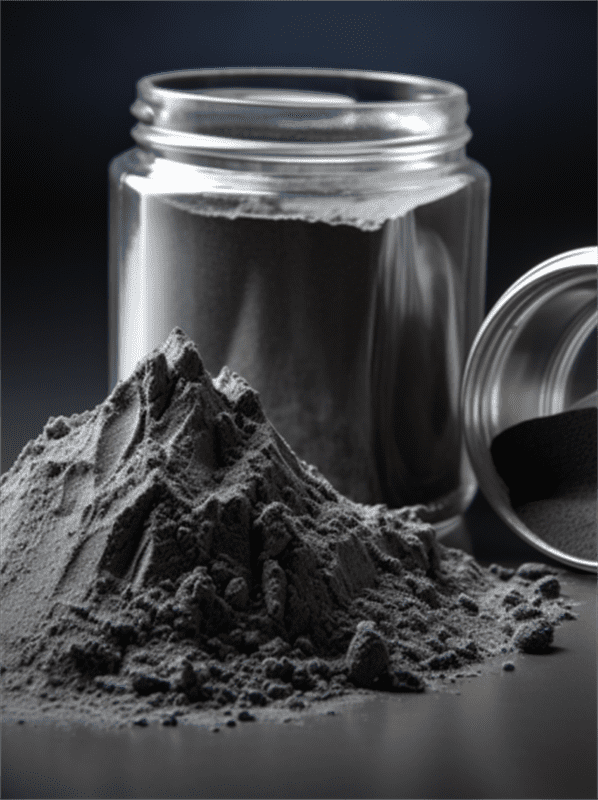
Installation of Atomized Metal Powder Systems
Installing equipment for handling atomized metal powders requires attention to safety, cleanliness, and reliability. Here are some key considerations:
Containment
- Use sealed containers for storage and transport
- Minimize open handling through enclosed conveyors and transfers
- Integrate glove boxes, RTP hoods for manual operations
- Provide dust extraction with baghouse or cyclone filters
Explosion Prevention
- Ensure electrical equipment is properly grounded and bonded
- Install spark detection and suppression systems
- Avoid potential ignition sources in hazardous areas
Cleanliness
- System should have smooth interior surfaces for ease of cleaning
- Include provision for purging with inert gas if needed
- Establish procedures for routine cleaning and maintenance
Material Handling
- Select equipment compatible with powder flow properties
- Consider vibratory feeders, rotary valves, vacuum transport
- Ensure optimal powder flow with no rat-holing or bridging
Proper installation following supplier recommendations is key for maximizing equipment effectiveness and safety.
Operation of Atomized Metal Powder Systems
Efficient operation of metal powder handling systems requires training personnel on procedures and safe practices. Key aspects include:
- Wear appropriate PPE – respirators, gloves, safety glasses
- Avoid powder spills and minimize dust
- Do not open equipment under load
- Follow purge sequences before maintenance interventions
- Conduct periodic inspections and leak checks
- Maintain optimal flow and pre-set pressures/vacuums
- Monitor oxygen and moisture levels if needed
- Store powder samples safely for quality checks
- Keep detailed logs for processing parameters
- Adhere to recommended preventive maintenance schedule
Establishing SOPs and checklists will help personnel perform critical tasks consistently and safely. Digital monitoring of critical parameters can also improve reliability.
Maintenance of Atomized Metal Powder Systems
Regular maintenance keeps powder handling systems running reliably over the long term. Key aspects of maintenance program include:
การตรวจสอบ
- Check hoses, seals for leaks, cracks periodically
- Inspect screws, motors, bearings, belts for damage
- Verify gauges, sensors, detectors are functional
การทำความสะอาด
- Follow schedule for deep cleaning equipment internals
- Remove powder buildup to prevent flow issues
- Clean filters to maintain air quality and avoid sparks
การสอบเทียบ
- Calibrate flow meters, pressure sensors per schedule
- Confirm powder feeder settings match rate
- Check load cells on hoppers ensure accurate level
Replacement
- Replace worn out hopper liners, screws as needed
- Overhaul or replace aged feeders and valves
- Keep spares of common wear items on hand
Documentation
- Log all maintenance and repairs performed
- Track equipment operating hours/cycles
- Update procedures as needed
Effective maintenance keeps powder systems running safely and productively.
Choosing an Atomized Metal Powder Supplier
Selecting a reliable supplier of atomized metal powder is critical for manufacturing operations. Here are key considerations when evaluating suppliers:
Powder Quality
- Tight control of particle size distribution
- Consistent spherical morphology
- Low oxygen/nitrogen levels
- Stringent quality control standards
Technical Expertise
- Experience tailored to application
- Knowledge of atomization process
- Capability to develop custom alloys
Production Capability
- Sufficient capacity to meet demand
- Backup options for supply continuity
- Scalability to accommodate growth
Testing and Certification
- Comprehensive analytical testing
- Detailed certificate of analysis
- Qualification to industry standards
บริการลูกค้า
- Responsiveness to inquiries
- Guidance on best product fit
- Flexibility for custom orders
Evaluation of factors beyond just price enables selection of the supplier best positioned to deliver performance and partnership over the long term.
Pros and Cons of Atomized Metal Powders
ข้อดี
- High purity with low oxide content
- การกระจายขนาดอนุภาคที่สอดคล้องกัน
- Good flowability due to spherical shape
- Allows small feature fabrication <100 μm
- Near net-shape capability to minimize waste
- Cuts energy use and emissions versus primary metal production
- Recyclable to recover expensive alloys
ข้อเสีย
- Expensive production due to complex processing
- Limited sizes and volumes available
- Requires handling systems for containment
- Powder beds have lower thermal conductivity
- Safety issues like dust explosions require mitigation
- Post-processing often needed to achieve properties
Understanding both benefits and limitations helps identify the best opportunities to leverage atomized metal powders.
Future Outlook for Atomized Metal Powders
The market for atomized metal powders is projected to see strong growth as applications like additive manufacturing continue gaining adoption.
Key trends shaping the future include:
- Development of new specialty alloys using atomization
- Tighter particle size control and customized distributions
- Multi-metal powders with compositional gradients
- Powder recycling systems and services gain traction
- Increased automation and process monitoring
- More industry consolidation among suppliers
- Declining prices as higher volumes are produced
- Expansion into emerging applications like biomedical
Advances in atomization technology will enable expanding use of metal powders, unlocking new geometries and material performance.
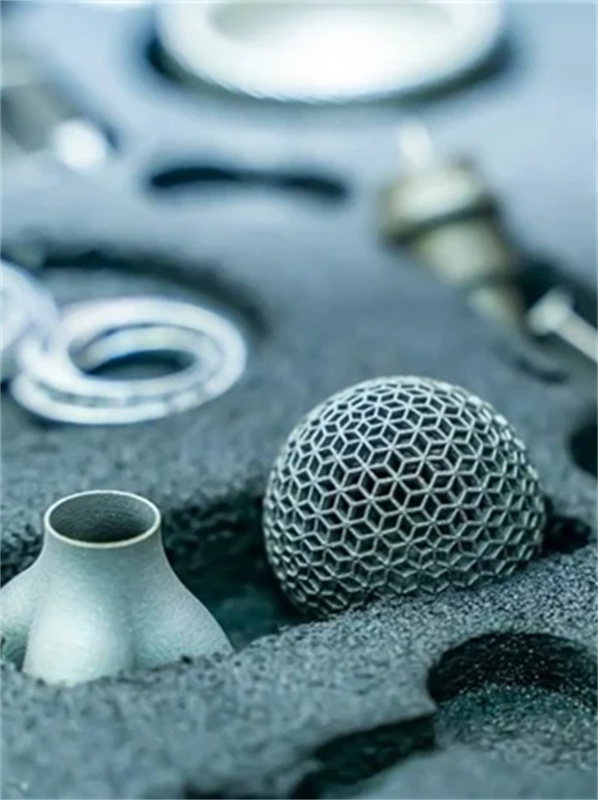
คำถามที่พบบ่อย
Q: What is the difference between atomized and spherical metal powders?
A: Spherical powders refers to the particle shape being close to a perfect sphere. Atomized powders can have spherical as well as irregular morphology depending on the production method. So all atomized powders are not spherical, but spherical powders are produced via atomization.
Q: How are pre-alloyed and master alloy atomized powders different?
A: Pre-alloyed powders are produced from an alloyed melt so the composition is uniform throughout each particle. Master alloy powders contain high percentages of alloying elements which get blended with base powders to achieve the final chemistry.
Q: What safety measures are required when handling atomized metal powders?
A: Key precautions when handling atomized powders include adequate PPE, minimizing dust, proper grounding, ignition source control, inert purging, and explosion prevention systems. Appropriate training of personnel is critical.
Q: How does grain size in atomized powders compare to conventional alloys?
A: Because of the rapid solidification, atomized powders have much finer grain sizes than conventional alloys, typically a few microns or less. This leads to different properties.
Q: What is the shelf life of common atomized metal powders?
A: If stored properly in sealed containers under controlled humidity, most atomized powders last 12-24 months before significant oxidation occurs. Moisture sensitive powders have shorter 6-12 month shelf life.
Q: What is the typical size range of particles in atomized powders?
A: Atomized powders span a wide size range from 1 micron to 1000 microns. But the major fraction used for manufacturing is typically 10-150 microns for good flow and packing characteristics.
Q: How are atomized metal powders recycled?
A: Atomized scrap and powders are remelted under controlled atmosphere to avoid oxidation. The recovered alloy is then reused to produce new powder feedstock. Some processes allow direct powder reuse.
Q: What is the benefit of inert gas atomized versus air atomized powders?
A: Inert gas atomization using argon or nitrogen allows lower oxygen pickup. This improves powder reactivity and leads to higher performance, making it preferred for reactive materials like titanium alloys.
Q: How do you determine if a powder is air atomized versus water atomized?
A: Air atomized powders have spherical morphology with smooth surface while water atomized particles are more irregular in shape with rougher surface texture. Also, water atomized powders tend to have higher oxygen content.