Metal molding machines produce precision net shape components from metallic powders via powder injection molding (PIM) for automotive, aerospace, medical and other demanding applications. This guide provides an overview of PIM equipment types, process steps, key specifications, leading manufacturers and comparative assessment.
metal molding machine ภาพรวม
Metal molding machines facilitate powder injection molding – a near net shape forming process providing complexity and precision at high volumes:
กระบวนการ | Thermoplastic injection molding of fine metal powders followed by debinding and sintering |
Metals | Stainless steels, tool steels, titanium, tungsten heavy alloys, nickel superalloys etc. |
Attributes | Complexity, Accuracy, Productivity, Automation |
แอปพลิเคชัน | Auto, Aerospace, Medical, Electronics |
Scale | Small, medium and high volume production |
Cost-effectively combining design freedom and mechanical properties between plastic molding and machining makes PIM suitable for small intricate components like turbocharger rotors and skull plates.
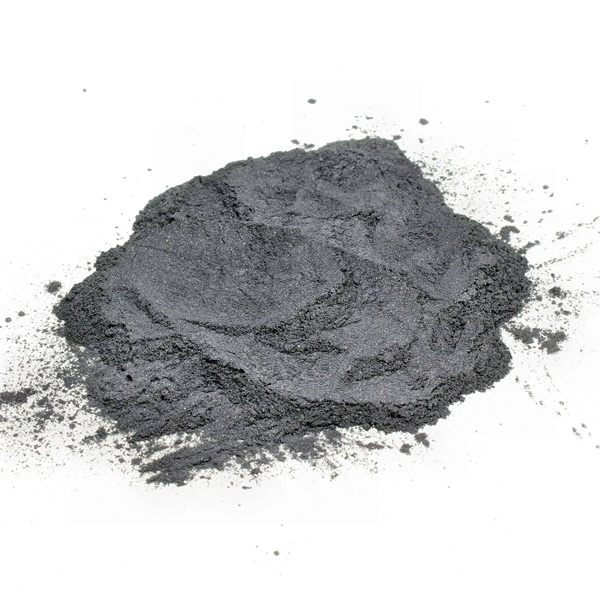
metal molding machine Types
Machine Type | คำอธิบาย |
---|---|
การฉีดขึ้นรูป | Precision molding machinery for first stage metal powder compaction at low pressures |
Debinding | Thermal or solvent equipment removing binder before sintering |
Sintering furnace | Density consolidation of brown parts via heating below melting point |
Complete PIM lines integrate these primary stations with supplementary equipment like mixers, feeders, robots and post-processing machines.
Process Steps
- Mixing – Fine metal powder is homogenously blended with thermoplastic binders
- การฉีดขึ้นรูป – Feedstock compounds into precision tool cavities through molding machines
- Debinding – Binder removal via thermal or chemical solvent techniques
- การเผา – Brown parts densified into final components reaching 95-99% solid metal densities
- Post processing – Secondary machining, joining or surface enhancement
Correct sequencing and optimized parameters are critical to cost-effectively maximizing mechanical properties.
Machine Specifications
Module | Key Parameters |
---|---|
การฉีดขึ้นรูป | Shot capacity, clamping force, injection rate, Homogeneity, precision |
Debinding | Atmosphere control, temperature uniformity, contamination prevention |
การเผา | Temperature, atmosphere, dwell times, quench rates |
Post processing | Tolerancing, surface finish requirements |
Medical or aerospace components demand tighter specifications and standards compliance verification than commercial fittings.
Leading Manufacturers
บริษัท | Models | ช่วงต้นทุน |
---|---|---|
อาร์เบิร์ก | Allrounder range | $150,000-$750,000 |
Milacron | Roboshot, Elektron, Magna | $100,000-$650,000 |
Nissei | PS,PN, Hyelectric series | $250,000-$800,000 |
Toshiba | EC,ET,EV Series | $200,000-$700,000 |
Larger shot capacities, special platens, clean room or robotic automation increase costs. Consider overall production volumes when investing.
Comparative Assessment
Injection Molding | Debinding | การเผา | |
---|---|---|---|
Throughput | สูง | ปานกลาง | ต่ำ |
Cycle time | Minutes | Hours | Days |
ค่าใช้จ่ายในการดำเนินงาน | ปานกลาง | ต่ำ | สูง |
Capital costs | สูง | ปานกลาง | Very high for large scale |
Design flexibility | สูง | ปานกลาง | ต่ำ |
Key Takeaways
- Total powder injection molding production cost dictate equipment investments scaled to volume
- Overall part complexity and quality targets drive specifications
- Integrated modeling and process monitoring enables defect reduction
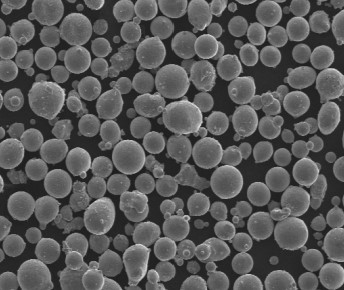
คำถามที่พบบ่อย
Q: What size press is optimal for 10000 parts per year?
A: 50-80 ton presses with <100g shot capacities facilitate suitable medium volumes cost-effectively. Integrate automation for optimal productivity.
Q: Are there material limitations for sintering furnaces?
A: Beyond 1900°C, options narrow significantly. Vacuum, protective atmospheres or inert environments may be necessary for reactive alloys. Continuous belt furnaces offer very large sintering scales.
Q: What determines injection molding machine productivity in PIM?
A: Shot capacity, dry cycle time and automation level primarily dictate hourly part output. Secondary factors include changeover, maintenance, mold design and heating/cooling rates.
Q: How tall can PIM parts be practically molded?
A: Keep height below 25mm for metals like stainless steel. For materials like tungsten alloys with high shrinkage, 15mm height is recommended maximum. Optimize gate positioning and mold venting.