การพิมพ์ 3 มิติที่ไม่สะดวก 625 is a nickel-chromium-molybdenum alloy that can be 3D printed into high performance components for demanding applications. This guide covers everything about Inconel 625 for additive manufacturing.
ภาพรวมของ 3D Printing with Inconel 625
Inconel 625 is a superalloy exhibiting:
- High strength and hardness at elevated temperatures
- ความต้านทานการกัดกร่อนที่ยอดเยี่ยม
- Good weldability and workability
- Oxidation and creep resistance
Key properties make it suitable for 3D printing complex geometries using powders:
- Available for major printing processes: DMLS, SLM, Binder Jetting
- Ability to print overhangs and internal channels
- Good dimensional accuracy and surface finish
- High density components with fine microstructure
- Properties comparable to or exceeding cast and wrought
- Reduction in waste compared to subtractive techniques
Inconel 625’s combination of strength, ductility, and corrosion resistance allows lightweight, high-performance printed parts across industries.
Composition of Inconel 625
Typical composition of Inconel 625 alloy:
- Nickel – 58%
- Chromium – 20-23%
- Molybdenum – 8-10%
- Iron – 5% max
- Niobium – 3-4%
- Trace amounts of C, Si, P, S
Key alloying elements like chromium, molybdenum, and niobium provide oxidation resistance at high temperatures, extra hardness, and precipitation strengthening. The composition can be adjusted based on application requirements.
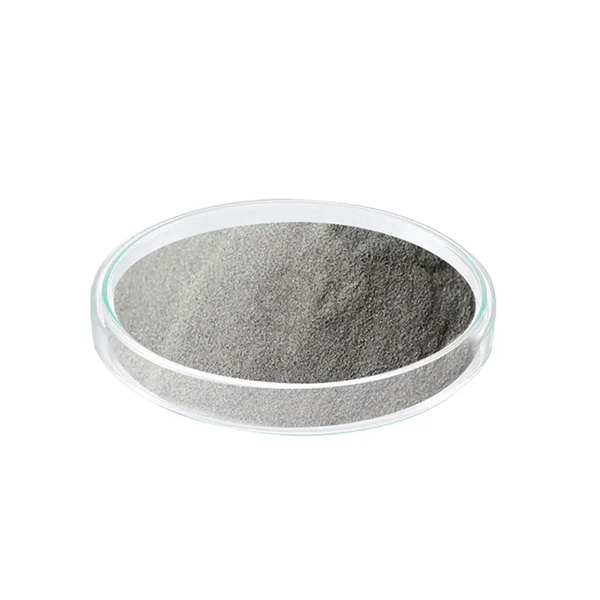
Key Properties of Inconel 625
Properties of Inconel 625:
- Density – 8.44 g/cm3
- Melting point – 1300°C
- Tensile strength – 760-1380 MPa
- Yield strength – 550 MPa
- Elongation – 50%
- Modulus of elasticity – 200-217 GPa
- Thermal conductivity – 9.8 W/m-K
- Coefficient of thermal expansion – 12.8 x 10-6 m/m°C
The balance of high strength, ductility, corrosion resistance, and stable properties at elevated temperatures make this superalloy useful for demanding applications.
Inconel 625 Powder for 3D Printing
Key characteristics of Inconel 625 powder for additive manufacturing:
Inconel 625 Powder Properties
- Particle shape – Mostly spherical
- Particle size – 15-45 microns
- Apparent density – 4 g/cm3
- Flowability – Slightly cohesive
- Purity – Nickel + other alloying elements > 99.5%
- Oxygen content – <500 ppm
Spherical morphology and controlled particle size distribution allows smooth powder spreading during printing. High purity minimizes defects.
Methods for 3D Printing Inconel 625
Popular additive manufacturing processes suitable for Inconel 625 include:
3D Printing Methods for Inconel 625
วิธี | คำอธิบาย |
---|---|
DMLS | Uses laser to fuse metal powder |
SLM | Selective laser melting of powder |
เครื่องผูก jetting | Binds powder with liquid agent |
LENS | Laser engineered net shaping |
EBM | Electron beam melting in vacuum |
DMLS and SLM offer high accuracy and surface finish. Binder jetting is more economical. EBM and LENS build larger near-net shape components. Parameters must be optimized for each process.
Applications of 3D Printed Inconel 625 Parts
Industries using additively manufactured Inconel 625 components:
Applications of 3D Printed Inconel 625
อุตสาหกรรม | แอปพลิเคชัน |
---|---|
การบินและอวกาศ | Turbine blades, combustors, nozzles |
น้ำมันและก๊าซ | Valves, wellhead parts exposed to sour gas |
การผลิตไฟฟ้า | Heat exchanger tubing, pump shafts |
เกี่ยวกับยานยนต์ | Turbocharger wheels, exhaust components |
การแปรรูปเคมี | Corrosion-resistant fluid handling parts |
Other uses include heat shields, press dies, nuclear reactors, sporting equipment, and biomedical implants leveraging strength, ductility, and biocompatibility.
Benefits of 3D Printing Inconel 625
Key advantages of additive manufacturing with Inconel 625:
Benefits of 3D Printing Inconel 625
- Ability to produce complex, optimized geometries
- Shorter lead times and lower costs versus machining
- Reduced weight due to topology optimization
- Less waste compared to subtractive techniques
- Superior material properties over casting
- No need for expensive tooling or dies
- Consolidation of subassemblies into single parts
- Customization and rapid prototyping
3D printing overcomes limitations of traditional fabrication to manufacture high-performance Inconel components.
Limitations of Printing Inconel 625
Challenges With 3D Printing Inconel 625
- High cost of Inconel 625 powder
- Requirement of inert gas during printing
- Difficulties in removing support structures
- Post-processing may be needed to relieve stresses
- Testing needed to qualify printed parts
- Lower ductility than wrought Inconel 625
- Limited number of qualified suppliers
- Large parts restricted by printer build volume
Process refinements and qualifications will expand adoption of additively manufactured Inconel 625 components for mission-critical applications.
Inconel 625 Powder Suppliers for 3D Printing
Reputable suppliers of Inconel 625 powder for AM include:
Suppliers of Inconel 625 Powder
บริษัท | ที่ตั้ง |
---|---|
Sandvik | ประเทศเยอรมนี |
แพรพ์เซอร์ | สหรัฐอเมริกา |
ช่างไม้ | สหรัฐอเมริกา |
ap & amp; c | แคนาดา |
โซลูชั่น SLM | ประเทศเยอรมนี |
เทคโนโลยี LPW | สหราชอาณาจักร |
These companies manufacture Inconel 625 powder using inert gas atomization and strictly control particle size distribution, morphology, oxygen content, and other quality attributes.
Inconel 625 Material Cost Analysis
Inconel 625 Powder Cost
ปริมาณ | ราคาต่อกิโลกรัม |
---|---|
1-10 kg | $100-150 |
10-50 kg | $80-120 |
>50 kg | $50-100 |
Cost is higher than stainless steel powder but lower than reactive alloys like titanium. Bulk order discounts apply. Part cost also depends on product geometry and build rates.
Comparative Analysis of Inconel 625
Comparison of Inconel 625 with Stainless Steel and Cobalt Chrome
อัลลอยด์ | Inconel 625 | สแตนเลส 316L | CoCr Alloy |
---|---|---|---|
ความหนาแน่น (g/cm3) | 8.4 | 8.0 | 8.3 |
Tensile Strength (MPa) | 1035 | 515 | 655 |
Melting Point (°C) | 1300 | 1370 | 1290 |
ความต้านทานการกัดกร่อน | ยอดเยี่ยม | ดี | ยุติธรรม |
ค่าใช้จ่าย | สูง | ต่ำ | ปานกลาง |
ความสามารถพิมพ์ได้ | ยุติธรรม | ยอดเยี่ยม | ดี |
Inconel 625 offers the best high temperature performance but has higher material costs. Stainless steel is easier to print and less expensive. Cobalt chrome provides a balance for dental and medical uses.
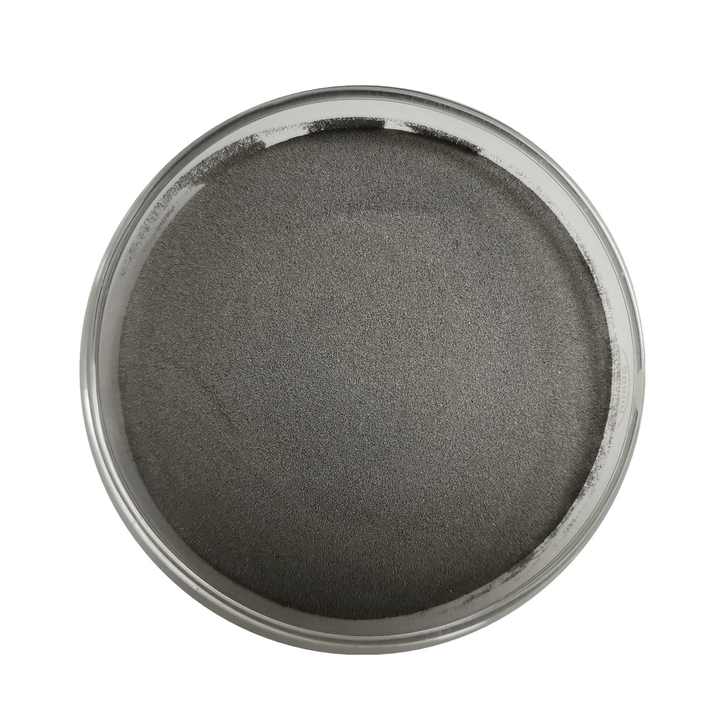
คำถามที่พบบ่อย
Q: Whatparticle sizeis optimal for3D printingInconel 625?
A: A particle size range of 15-45 microns is recommended, with a spherical morphology and tight distribution for optimal flowability and high packing density during printing.
Q: Which printing process is most suitable for Inconel 625?
A: DMLS and SLM using a high-powered laser provide the best accuracy, density, and surface finish. Binder jetting offers faster build speeds but lower mechanicals.
Q: Does Inconel 625 require heat treatment after 3D printing?
A: Yes, a solution annealing and aging heat treatment cycle is often performed to relieve stresses and achieve optimum ductility, strength, and other mechanical properties.
Q: What industries use 3D printed Inconel 625 the most?
A: Aerospace is the biggest adopter for combustion components. Oil and gas, power generation, automotive, and chemical processing also leverage 3D printed Inconel 625.
Q: Is it possible to 3D print functionally graded Inconel 625 parts?
A: Yes, voxel control methods allow continuously varying compositions and microstructures within a single printed part by precise powder mixing and laser modulation.
Q: Does Inconel 625 require hot isostatic pressing after additive manufacturing?
A: While HIP can eliminate internal voids and improve fatigue resistance, recent process refinements now allow full density to be achieved during printing for most applications.
Q: What finishing processes are used on printed Inconel 625?
A: Printed parts often undergo abrasive tumbling, shot peening, grinding, and polishing to smooth surfaces and remove supports. Hot isostatic pressing can also be applied.
Q: Are the material properties of 3D printed Inconel 625 comparable to wrought?
A: Correctly printed and processed Inconel 625 can match and even exceed the tensile strength, ductility, fracture toughness and other properties of conventionally processed wrought alloy.
Q: What design considerations apply for Inconel 625 AM parts?
A: Fine features require thicker walls. Designs should avoid overhangs, minimize supports, and account for thermal stresses. Modules can be consolidated into monolithic components.