M2 Powder
M2 is a high-speed steel powder characterized by its high hardness and wear resistance along with good toughness and compressive strength. It is widely used in metal additive manufacturing to produce durable tooling for cutting, forming and stamping applications.
Low MOQ
Provide low minimum order quantity to meet different needs.
OEM & ODM
Provide customized products and design services to meet unique customer needs.
Adequate Stock
Ensure fast order processing and provide reliable and efficient service.
Customer Satisfaction
Provide high quality products with customer satisfaction at the core.
share this product
Table of Contents
M2 is a high-speed steel powder characterized by its high hardness and wear resistance along with good toughness and compressive strength. It is widely used in metal additive manufacturing to produce durable tooling for cutting, forming and stamping applications.
Composition of M2 Powder
The composition of M2 high-speed steel powder is:
Element | Weight % | Purpose |
---|---|---|
Tungsten | 6.0 – 6.8 | Hardness, wear resistance |
Molybdenum | 4.8 – 5.5 | Toughness, strength |
Chromium | 3.8 – 4.5 | Hardening, wear resistance |
Vanadium | 1.9 – 2.2 | Hardening, wear resistance |
Carbon | 0.78 – 0.88 | Hardening |
Manganese | 0.15 – 0.45 | Hardening |
Silicon | 0.15 – 0.45 | Deoxidizer |
The high tungsten, molybdenum and chromium content impart excellent hardness and wear resistance.
Properties of M2 Powder
Key properties of M2 powder include:
Property | Description |
---|---|
Hardness | 64 – 66 HRC when heat treated |
Wear resistance | Excellent abrasion and erosion resistance |
Toughness | Higher than tungsten carbide grades |
Compressive strength | Up to 300 ksi |
Heat resistance | Can be used up to 600°C |
Corrosion resistance | Better than plain carbon steels |
The properties make M2 suitable for durable cutting, stamping and forming tooling.
AM Process Parameters for M2 Powder
Typical parameters for printing M2 powder include:
Parameter | Typical value | Purpose |
---|---|---|
Layer height | 20-50 μm | Resolution versus build speed |
Laser power | 250-500 W | Sufficient melting without evaporation |
Scan speed | 400-1200 mm/s | Density versus production rate |
Hatch spacing | 80-120 μm | Mechanical properties |
Support structure | Minimal | Easy removal |
Hot isostatic pressing | 1160°C, 100 MPa, 3 hrs | Eliminate porosity |
Parameters tailored for density, microstructure, build rate and post-processing requirements.
Applications of 3D Printed M2 Tooling
AM fabricated M2 components are used for:
Industry | Tooling applications |
---|---|
Automotive | Stamping dies, forming tools, fixtures |
Aerospace | Jigs, fixtures, trim tools |
Appliances | Punches, blanking dies, bending dies |
Consumer goods | Injection molds, stamping dies |
Medical | Cutting tools, rasps, drill guides |
Benefits over traditionally processed M2 tooling include complexity, lead time and cost reduction.
Specifications of M2 Powder for AM
M2 powder must meet strict specifications:
Parameter | Specification |
---|---|
Particle size range | 15-45 μm typical |
Particle shape | Spherical morphology |
Apparent density | > 4 g/cc |
Tap density | > 6 g/cc |
Hall flow rate | > 23 sec for 50 g |
Purity | >99.9% |
Oxygen content | <300 ppm |
Custom size distributions and controlled moisture levels available.
Suppliers of M2 Powder
Reputable M2 powder suppliers include:
Supplier | Location |
---|---|
Sandvik Osprey | UK |
Carpenter Additive | USA |
Erasteel | Sweden |
Hoganas | Sweden |
LPW Technology | UK |
Prices range from $50/kg to $120/kg based on quality and order volume.
Handling and Storage of M2 Powder
As a reactive material, careful M2 powder handling is essential:
- Store sealed containers away from moisture, sparks, ignition sources
- Use inert gas padding during transfer and storage
- Ground equipment to dissipate static charges
- Avoid dust accumulation through extraction systems
- Follow applicable safety precautions
Proper techniques ensure optimal powder condition.
Inspection and Testing of M2 Powder
Quality testing methods include:
Method | Parameters Tested |
---|---|
Sieve analysis | Particle size distribution |
SEM imaging | Particle morphology |
EDX | Chemistry and composition |
XRD | Phases present |
Pycnometry | Density |
Hall flow rate | Powder flowability |
Testing per ASTM standards verifies powder quality and batch consistency.
Comparing M2 to Alternative Tool Steel Powders
M2 compares to other tool steel alloys as:
Alloy | Wear Resistance | Toughness | Cost | Ease of Processing |
---|---|---|---|---|
M2 | Excellent | Good | Medium | Fair |
H13 | Good | Excellent | Low | Excellent |
S7 | Excellent | Fair | High | Difficult |
420 stainless | Poor | Excellent | Low | Excellent |
With its balanced properties, M2 supersedes alternatives for many wear-resistant tooling applications.
Pros and Cons of M2 Powder for Metal AM
Pros | Cons |
---|---|
Excellent hardness and wear resistance | Lower toughness than cold work tool steels |
Good heat resistance and thermal stability | Required post-processing like HIP and heat treatment |
Established credentials for metal AM | Controlled atmosphere storage required |
Cost advantage over exotic tool steels | Difficult to machine after printing |
Properties match conventional M2 | Limited corrosion resistance |
M2 enables high wear resistance additive tooling, though not suitable for highly corrosive environments.
Frequently Asked Questions about M2 Powder
Q: What particle size range works best for printing M2 powder?
A: A typical range is 15-45 microns. It provides optimal powder flowability combined with high resolution and dense parts.
Q: What post-processing methods are used for M2 AM parts?
A: Hot isostatic pressing, heat treatment, surface grinding/EDM, and shot peening are typically used to eliminate voids, harden, and finish parts.
Q: Which metal 3D printing process is ideal for M2 alloy?
A: M2 can be effectively printed using selective laser melting (SLM), direct metal laser sintering (DMLS) and electron beam melting (EBM) processes.
Q: What accuracy and surface finish can be expected for M2 printed parts?
A: Post-processed M2 components can achieve dimensional tolerances and surface finish comparable to CNC machined M2 tooling.
Q: What industries use additively manufactured M2 tooling components?
A: Automotive, aerospace, medical, consumer goods, appliances, and industrial sectors benefit from 3D printed M2 tooling.
Q: What is the key difference between M2 and M4 grades of high speed steel?
A: M4 has slightly lower vanadium and molybdenum content leading to a better combination of wear resistance and toughness compared to M2.
Q: Does M2 require support structures when 3D printing?
A: Minimal supports are recommended on overhangs and bridges to prevent deformation and allow easy removal after printing.
Q: What density can be expected with optimized M2 3D printed parts?
A: Density above 99% is achievable for M2 using ideal parameters tailored specifically for this alloy.
Q: What defects can occur when printing M2 powder?
A: Potential defects are cracking, distortion, porosity, incomplete fusion, and surface roughness. Most can be prevented through optimized parameters.
Q: Is HIP required for all M2 AM tooling components?
A: While highly recommended, HIP may not be absolutely necessary for non-critical tooling applications. Heat treatment alone may suffice.
About Met3DP
Product Category
HOT SALE
CONTACT US
Any questions? Send us message now! We’ll serve your request with a whole team after receiving your message.
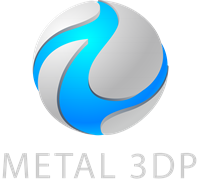
Leading provider of additive manufacturing solutions headquartered in Qingdao, China.
COMPANY
PRODUCT
cONTACT INFO
- Qingdao City, Shandong, China
- info@metal3dp.com
- amy@metal3dp.com
- +86 19116340731