Inconel 625 Powder丨Nickel based superalloy in625 powder
In625 powder is a powdered form of the nickel-chromium alloy Inconel 625, which exhibits excellent corrosion resistance, high strength, and outstanding heat resistance. This superalloy is composed of nickel, chromium, molybdenum, and niobium, along with smaller amounts of other elements. Its unique composition imparts remarkable mechanical properties, making it a sought-after material in numerous industries.
Low MOQ
Provide low minimum order quantity to meet different needs.
OEM & ODM
Provide customized products and design services to meet unique customer needs.
Adequate Stock
Ensure fast order processing and provide reliable and efficient service.
Customer Satisfaction
Provide high quality products with customer satisfaction at the core.
share this product
Table of Contents
Inconel 625 powder is a nickel-based superalloy that possesses high strength properties and resistance to elevated temperatures. Inconel 625 (Alloy 625, UNS N06625) is widely used for its high strength, excellent fabricability (including joining), and outstanding corrosion resistance. Its service temperatures range from cryogenic to 1800°F (982°C). High tensile, creep, and rupture strength, outstanding fatigue and thermal-fatigue strength, oxidation resistance and excellent weldability and brazeability are the properties of INCONEL alloy 625 that make it interesting to the aerospace field.
It is being used in such applications as aircraft ducting systems, engine exhaust systems, thrust-reverser systems, resistance-welded honeycomb structures for housing engine controls, fuel and hydraulic line tubing, spray bars, bellows, turbine shroud rings, and heat-exchanger tubing in environmental control systems. It is also suitable for combustion system transition liners, turbine seals, compressor vanes, and thrust-chamber tubing for the rocket.
Inconel 625 Powder Specification
Norminal Composition(wt%) | ||||||
In625
|
Cr | Mo | Nb | Co | Fe | Al |
20-23 | 8-10 | 3.15-4.15 | ≤1 | ≤1 | ≤0.4 | |
Ti | C | Ni | O | N | ||
≤0.4 | ≤0.1 | Bal. | ≤500ppm | ≤100ppm |
Common Size:15-45um,15-53um,45-106um,45-150u,-200/-300/-400/-500/-600mesh etc,.
No | Name | Related Powder Composition(wt%) |
1 | 18Ni300 | Ni17-19,Mo4.5-5.2,Co8.5-9.5,Ti0.6-0.8,Al0.05-0.15,Fe(Bal.) |
2 | Hastelloy Alloy | Fe17-20,Cr20.5-23,Mo8-10,W0.2-1,Co0.5-2.5,C0.05-0.15,Ni(Bal.) |
3 | AlSi10Mg | Si9-11,Mg0.2-0.45,Al(Bal.) |
4 | CoCrW | Cr26.5-29,W7-9,Si1.2-1.9,Co(Bal.) |
5 | Co28Cr6Mo | Cr27-29,Mo5-7,Co(Bal.) |
6 | Spherical Ti Powder | Ti≥99.9 |
7 | TC4 | Al5.5-6.8,V3.5-4.5,Ti(Bal.) |
8 | TA15 | Al5.5-7.1,V0.8-2.5,Mo0.8-2,Zr1.5-2.5,Al(Bal.) |
9 | 316L | Cr16.00-18.00, Ni10.00-14.00,Mo2.00-3.00,Fe(Bal.) |
10 | S136 | Cr12.0-14.0,Si0.8-1.0,V0.15-0.4,C0.2-0.45,Fe(Bal.) |
11 | In625 | Cr20-23 , Mo8-10 , Nb 3.15-4.15 , Co≤1, Fe≤1 , Ni (bal.) |
12 | In718 | Cr17-21 , Mo2.8-3.3 , Nb 4.75-5.5 , Co≤1, Ni50-51 , Fe(Bal.) |
13 | Spherica WC | C3.7-4.2,W(Bal.) |
14 | Spherical Cr Powder | Cr≥99.9 |
15 | Spherica Mo Powder | Mo≥99.9 |
16 | Spherica Ta Powder | Ta≥99.9 |
17 | Spherica W Powder | W≥99.9 |
Inconel 625 Powder Properties:
- Tensile Strength/MPa: 910±20
- Yield Strength/MPa: 460±20
- Elongation After Break/%: 60±5
- Tensile Strength(815℃)/MPa: 910±20
- Yield Strength(815℃)/MPa: 460±20
- Elongation After Break(815℃)/%: 60±5
- Appearance: Grey spherica powder
- Tapping Density:4.95g/m3
- Apparent density: 4.32g/m3
- Flowability:15.5s/50g
- Size: 15-53um
- PSD: D10:17.1um, D50:30.2um, D90: 50.9um
Inconel 625 Powder Application:
Marine application:
Due to its high corrosion resistance, especially pitting and cracking resistance, the Inconel 625 is ideal for high-salt, subsea applications. The material is used as propeller blades for ships, mooring lines for fixing ships and similar ships, accessories and fixtures for submarines, and components for marine equipment.
Aerospace equipment:
The superalloy has also found its way into the aircraft industry, especially for exhaust equipment, fuel pipes, heat exchanger casings and rocket parts.That’s because the Inconel 625 works well even at extreme temperatures and pressures.
Nuclear technology:
Inconel 625’s strength and corrosion and stress resistance make it a suitable component for nuclear reactors, especially control rods and cores. Nuclear systems also typically involve temperatures in excess of 650°C, which Inconel 625’s strength can withstand.
Industrial processes:
Because the alloy is easy to manufacture and resistant to high temperatures and corrosion, it is a useful component in the production of manufacturing equipment such as vessels, heat exchangers, valves and fluid distribution systems. Its excellent weldability also makes it a suitable component for pipes used in manufacturing plants.
Oil and Gas Industry:
In625 powder finds extensive usage in the oil and gas sector, where equipment operates in challenging conditions. It is utilized for producing components like valves, couplings, and connectors that must endure high pressures, corrosive fluids, and elevated temperatures. In625 powder’s resistance to pitting and crevice corrosion, along with its exceptional mechanical strength, ensures the durability and longevity of these vital components.
Medical Sector:
The medical field benefits greatly from In625 powder’s unique attributes. It is widely employed in the manufacturing of surgical instruments, orthopedic implants, and dental prosthetics. The biocompatibility and corrosion resistance of In625 powder make it an excellent choice for these applications, ensuring the safety and reliability of medical devices while promoting better patient outcomes.
Advantages of In625 Powder
High Strength and Durability
In625 powder boasts exceptional mechanical properties, including high tensile and yield strength, enabling it to withstand heavy loads and resist deformation. Its outstanding durability ensures the longevity and reliability of components manufactured using this powder.
Superior Corrosion Resistance
The corrosion-resistant nature of In625 powder makes it highly suitable for applications in aggressive environments, such as marine or chemical processing industries. It resists both oxidizing and reducing environments, preventing degradation and enhancing the overall lifespan of components.
Excellent Heat Resistance
With a melting point of approximately 1290°C (2350°F), In625 powder demonstrates superb heat resistance. It can withstand extreme temperatures without significant loss of strength or deformation, making it suitable for applications exposed to high thermal stresses.
Versatile Machinability
In625 powder exhibits good machinability, allowing for precise and intricate designs. It can be easily shaped into complex geometries, providing flexibility and facilitating the production of intricate components.
Weldability
The weldability of In625 powder is another notable advantage. It can be welded using various techniques, such as gas tungsten arc welding (GTAW) and electron beam welding (EBW), enabling the fabrication of large and complex structures with ease.
FAQs (Frequently Asked Questions)
Q1. Is In625 powder suitable for high-temperature applications?
Yes, In625 powder exhibits excellent heat resistance and can withstand extreme temperatures, making it suitable for high-temperature applications.
Q2. What industries benefit the most from using In625 powder?
In625 powder finds applications in diverse industries, including aerospace, oil and gas, medical, and chemical processing industries.
Q3. Can In625 powder be welded?
Yes, In625 powder can be welded using various techniques, providing flexibility in fabricating complex structures.
Q4. Does In625 powder have good corrosion resistance?
Absolutely! In625 powder demonstrates superior corrosion resistance, making it highly suitable for aggressive environments.
Q5. Is In625 powder compatible with biomedical applications?
Yes, In625 powder is biocompatible and widely used in the production of surgical instruments, orthopedic implants, and dental prosthetics.
About Met3DP
Product Category
HOT SALE
CONTACT US
Any questions? Send us message now! We’ll serve your request with a whole team after receiving your message.
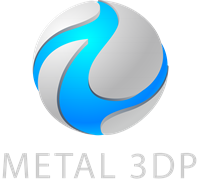
Leading provider of additive manufacturing solutions headquartered in Qingdao, China.
COMPANY
PRODUCT
cONTACT INFO
- Qingdao City, Shandong, China
- info@metal3dp.com
- amy@metal3dp.com
- +86 19116340731