AlSi10Mg powder
AlSi10Mg powder is a composite material composed of aluminum (Al), silicon (Si), and magnesium (Mg). It is specifically designed for use in additive manufacturing processes, where it is used as a feedstock material for 3D printers. The powder has a fine particle size and is tailored to ensure optimal flowability and compatibility with various additive manufacturing systems.
Low MOQ
Provide low minimum order quantity to meet different needs.
OEM & ODM
Provide customized products and design services to meet unique customer needs.
Adequate Stock
Ensure fast order processing and provide reliable and efficient service.
Customer Satisfaction
Provide high quality products with customer satisfaction at the core.
share this product
Table of Contents
AlSi10Mg Powder: A Technical Overview
Overview of AlSi10Mg Powder
AlSi10Mg is an aluminum alloy powder composed primarily of aluminum along with silicon and magnesium as the major alloying elements. It is widely used in metal additive manufacturing, also known as 3D printing, due to its excellent strength, durability, weldability, and corrosion resistance.
AlSi10Mg powder can be processed through selective laser melting (SLM), electron beam melting (EBM), and direct metal laser sintering (DMLS) to create complex metal parts with fine details and custom geometries. Its properties make it suitable for aerospace, automotive, medical, and industrial applications.
This article provides a comprehensive technical overview of AlSi10Mg powder covering its composition, properties, applications, pricing, suppliers, and other key information for materials engineers, product designers, and 3D printing professionals.
AlSi10Mg Powder Key Details:
- Composition: Aluminum with 9-11% silicon, 0.2-0.45% magnesium
- Particle shape: Spherical, high flowability
- Size range: 15-45 microns
- Density: 2.67 g/cc
- Melting point: ~615°C
- Strength: Medium to high
- Uses: Aerospace, automotive, industrial 3D printing
Composition of AlSi10Mg Powder
The composition of AlSi10Mg powder consists mainly of aluminum with additions of silicon and magnesium as alloying elements. The nominal composition range is provided below:
Element | Weight % |
---|---|
Aluminum (Al) | Base/remainder |
Silicon (Si) | 9-11% |
Magnesium (Mg) | 0.2-0.45% |
Other (Fe, Mn, etc.) | < 0.55% total |
Silicon is added to aluminum to improve castability and enhance mechanical properties like yield strength and hardness. It increases fluidity during melting and improves feeding characteristics.
The addition of magnesium results in precipitation hardening which strengthens the alloy through heat treatment. Magnesium also improves corrosion resistance.
Trace amounts of iron, manganese, and other elements may be present as impurities up to 0.55% maximum. The levels of alloying additions can be varied within range to tailor the properties as per application requirements.
Table: Nominal composition range of AlSi10Mg alloy powder
Element | Minimum wt% | Maximum wt% |
---|---|---|
Aluminum | Bal. | Bal. |
Silicon | 9 | 11 |
Magnesium | 0.2 | 0.45 |
Other | – | 0.55 |
Properties of AlSi10Mg Powder
AlSi10Mg exhibits properties making it suitable for demanding applications across aerospace, automotive, and industrial sectors. The key properties are highlighted below:
Mechanical Properties
- High strength and hardness
- Good ductility in annealed state
- Excellent weldability
- High fatigue strength
Physical Properties
- Density: 2.67 g/cc
- Melting point: ~615°C
- Thermal conductivity: 130 W/m-K
- Coefficient of thermal expansion: 21-24 x 10^-6 K^-1
Other
- Good corrosion resistance
- Excellent printability and surface finish
- Biocompatible per ISO 10993 and ASTM F67
- Non-magnetic
The density is comparable to aluminum alloys like AlSi12 and AlSi7Mg. The melting point is also similar to standard Al-Si casting alloys. These properties allow processing and consolidation via sintering and melting.
Table: Overview of key properties of AlSi10Mg powder
Property | Typical Values |
---|---|
Density | 2.67 g/cc |
Melting Point | ~615°C |
Thermal Conductivity | 130 W/m-K |
Electrical Resistivity | 4-8 x 10^-8 Ωm |
Young’s Modulus | 70-80 GPa |
Poisson’s Ratio | 0.33 |
Yield Strength | 215-365 MPa |
Tensile Strength | 330-430 MPa |
Elongation | 8-10% |
Hardness | 80-100 Brinell |
Note: Properties depend on precise composition, manufacturing method, build orientation, heat treatment etc. Values shown are typical or standard.
The mechanical properties like high yield and tensile strength along with good ductility make AlSi10Mg suitable for high-performance parts across industries. The alloy can be age hardened to further enhance strength. Excellent corrosion resistance is achieved by silicon additions creating a protective oxide layer. Overall, AlSi10Mg provides a versatile combination of properties for metal AM.
Applications of AlSi10Mg Powder
The lightweight, strong, and printable characteristics of AlSi10Mg powder make it one of the most widely used alloys in additive manufacturing. Some typical applications include:
Aerospace: Turbine blades, rocket nozzles, structural brackets, satellite components, UAV parts
Automotive: Powertrain parts, pistons, turbochargers, heat exchangers
Industrial: Robotics, tooling, jigs and fixtures, driveshafts
Medical: Orthopedic implants, prosthetics, surgical instruments
Other: Heat sinks, hydraulic manifolds, housings, cooling channels
AlSi10Mg enables complex, optimized geometries that improve performance and efficiency in the above applications. The fine structures possible via 3D printing enhances heat transfer, fluid flow, and other properties.
The excellent strength-to-weight ratio of AlSi10Mg reduces component weight while maintaining mechanical performance. This helps improve fuel economy in vehicles and lower launch costs in space applications.
Table: Overview of AlSi10Mg applications across industries
Sector | Typical Applications |
---|---|
Aerospace | Turbine blades, structural brackets, rocket nozzles, satellites |
Automotive | Powertrain, pistons, turbochargers, heat exchangers |
Industrial | Robotics, tooling, jigs and fixtures |
Medical | Orthopedic implants, prosthetics |
General | Heat sinks, hydraulic manifolds, housings |
AlSi10Mg is certified for aerospace applications meeting standards like AMS4967 and AMS4169. Extensive qualifications and testing validates its performance under extreme environments. The biocompatibility per ISO 10993 and ASTM F67 allows use in medical devices and implants. Overall, AlSi10Mg provides a versatile lightweight material solution for critical applications.
Processability of AlSi10Mg Powder
AlSi10Mg powder can be processed via major metal additive manufacturing methods like:
- Selective Laser Melting (SLM)
- Direct Metal Laser Sintering (DMLS)
- Electron Beam Melting (EBM)
Laser-based Methods: SLM and DMLS use a high power laser to selectively fuse regions of a powder bed to build up parts layer-by-layer. The consolidated material has properties comparable to conventional aluminum alloys. SLM typically uses higher laser power for full melting. DMLS has lower power for sintering powder particles.
Electron Beam Melting: EBM uses an electron beam as heat source to melt and fuse material. It can achieve higher build rates than laser processes since it fuses each layer rapidly. Material properties are similar to SLM and DMLS.
Print Parameters: Typical SLM parameters – Laser power 175-350 W, Scan speed 700-1500 mm/s, Layer thickness 20-100 μm. For EBM – Beam power 3-7 kW, Scan speed 1000-2500 mm/s, Layer thickness 50-200 μm.
Other methods: AlSi10Mg powder can also be used in binder jetting where a liquid binder is selectively deposited to form the shape. The “green” part is then sintered. Cold spray deposition is also possible.
Table: AM processes compatible with AlSi10Mg alloy powder
Process | Heat Source | Description |
---|---|---|
SLM | Laser | Selective laser melting |
DMLS | Laser | Direct metal laser sintering |
EBM | Electron beam | Electron beam melting |
Binder jetting | Liquid binder | Binder printed, then sintered |
Cold spray | Kinetic | Powder sprayed onto substrate |
AlSi10Mg powder has high absorbance to the laser/electron beam, and excellent flow and packing density. This results in good spreadability across powder bed and efficient melting/sintering. The particle size and spherical morphology also plays a key role.
Overall, AlSi10Mg offers excellent processability across PBF and related methods to fabricate complex geometries with good surface finish and feature resolution.
Powder Characteristics and Quality
AlSi10Mg powder used in AM processes exhibits the following characteristics:
- Spherical powder morphology with smooth surface
- Flowability with minimal agglomeration
- Apparent density ~1.2-1.6 g/cc
- Tap density ~2.2-2.7 g/cc
- Uniform composition distribution
- High purity with low internal porosity
- Controlled particle size distribution
Particle shape: Spherical powder morphology provides good flow and spreadability across the powder bed. It results in uniform melting and material properties. Gas atomization is commonly used to achieve sphericity >90%.
Flowability: Powders with high flowability spread evenly and pack densely on powder bed platforms. Flow rates of 23-27 s/50g through Hall funnel are typical.
Particle size: The particle size distribution is generally 10-45 μm or 15-45 μm. Larger particles ~35-45 μm improve flow while smaller ones ~15-25 μm enhance density and resolution.
Composition control: Tight control of composition within specification maximizes material performance. Uniform distribution of alloying elements is ensured.
Purity: High purity with low porosity and inclusions prevents process defects. Oxygen content <1000 ppm.
Table: Typical characteristics and properties of AlSi10Mg powders
Parameter | Typical Value | Role |
---|---|---|
Particle shape | Spherical >90% | Flowability, density |
Particle size (μm) | 15-45 | Density, resolution |
Flow rate (s/50g) | 23-27 | Powder bed packing |
Apparent density (g/cc) | 1.2-1.6 | Recyclability |
Tap density (g/cc) | 2.2-2.7 | Green density |
Purity | >99.5% | Defect reduction |
Oxygen (ppm) | <1000 | Clean melting |
Parameters like particle shape distribution (PSD) and Hausner ratio indicate powder quality. Strict control over gas atomization results in high batch-to-batch consistency. Powder is supplied with composition report and lot-specific certificates of analysis (COA).
AlSi10Mg Powder Suppliers
Some of the major global suppliers of AlSi10Mg powders for AM include:
AP&C
- Trade name: Atomized Aluminum Powder 5056
- Size range (μm): 15-45, 23-53
- Packaging: 5 kg bottles to 1 metric ton boxes with argon
GE Additive
- Product name: AlSi10Mg
- Size range (μm): 15-45
- Packaging: 10 kg bottles with argon
Sandvik Osprey
- Product: Osprey AlSi10Mg
- Particles: Spherical, D50 40 μm
- Packaging: Argon-filled bottles
LPW Technology
- Product: AlSi10Mg AM Powder
- Size range (μm): 15-45
- Packaging: 2 – 12 kg bottles in argon
SLM Solutions
- Product: SLM AlSi10Mg
- Size range (μm): 15-45
- Packaging: 10 liter cans, 2 kg bottles
Table: AlSi10Mg powder suppliers and specifications
Supplier | Product | Size (μm) | Packaging |
---|---|---|---|
AP&C | Atomized Al 5056 | 15-45 | Bottles/boxes with Ar |
GE Additive | AlSi10Mg | 15-45 | 10 kg bottles with Ar |
Sandvik Osprey | Osprey AlSi10Mg | D50 40 | Argon bottles |
LPW | AlSi10Mg AM | 15-45 | 2-12 kg bottles in Ar |
SLM Solutions | SLM AlSi10Mg | 15-45 | Cans/bottles with Ar |
Custom variations of AlSi10Mg with optimized particle fractions or distributions can be sourced from manufacturers upon request.
AlSi10Mg Powder Pricing
The price of AlSi10Mg powder for AM processing typically ranges from $90-150 per kg based on quantity and manufacturer.
Pricing considerations:
- Powder quantity – Prices reduce for bulk orders due to lower packaging costs
- Composition variants – Minor additions or optimizations may increase cost
- Quality and certification – Higher purity/consistency increases cost
- Manufacturer – Premium suppliers tend to have higher pricing
- Packaging – Specialized packaging (cans, bottles etc.) impacts price
Indicative Pricing:
Quantity | Price per kg (USD) |
---|---|
1 kg | $140-200 |
10 kg | $120-160 |
100 kg | $100-130 |
1,000+ kg | $90-110 |
Shipping, taxes, and any special certification requirements may add to the final delivered cost. Large OEM orders often get discounted rates from manufacturers via contracts.
Table: AlSi10Mg powder price ranges based on order quantity
Order Quantity | Price per kg (USD) |
---|---|
1 kg | $140-200 |
10 kg | $120-160 |
100 kg | $100-130 |
1,000+ kg | $90-110 |
Choosing AlSi10Mg Powder
Key considerations for choosing AlSi10Mg powder include:
Application requirements: Performance needs like strength, hardness, ductility, fatigue life, etc. Applications may demand specific material certifications also.
AM process variables: Matching particle size range, shape and distribution to the printer model, layer thickness, beam power and related parameters.
Quality and consistency: Powder batches that reliably meet composition, purity, particle characteristics etc. are critical for production use.
Availability and lead times: For prototype work availability of small quantities may be key while production needs bulk orders and stable long-term supply.
Pricing: Price per kg will depend on quantity, shipment costs, supplier margins etc. Large OEM contracts get better pricing.
Technical support: Manufacturers with strong technical expertise in metal powder production and AM can provide guidance on best powder options.
Working with established suppliers and collaborating early in the AM part design process is advised when selecting AlSi10Mg powder.
Pros and Cons of AlSi10Mg Powder
Pros
- High strength with good ductility
- Excellent corrosion resistance
- Readily weldable and machinable
- Good thermal properties
- Widely qualified for aerospace use
- Biocompatible for medical implants
Cons
- Lower yield strength than AlSi7Mg and AlSi12 alloys
- Susceptible to porosity defects during printing
- High reflectivity demands higher laser power
- Not optimal for high temperature applications >150°C
- More expensive than unalloyed aluminum powders
FAQs
Q. What is the chemical composition of AlSi10Mg powder?
A. The typical composition is aluminum base with 9-11% silicon and 0.2-0.45% magnesium. Remaining is other trace elements at <0.55% total.
Q. What is the density of AlSi10Mg and AlSi10Mg powder?
A. The density is around 2.67 g/cc for both the bulk alloy and the powder form.
Q. What are the mechanical properties of AlSi10Mg parts made by AM?
A. Printed AlSi10Mg has a tensile strength of 330-430 MPa, yield strength of 215-365 MPa, and elongation of 8-10% in the as-built condition. Heat treatment can further improve properties.
Q. What particle size is recommended for AlSi10Mg powder in AM?
A. A particle size range of 15-45 microns is commonly used, though size distributions can be optimized for specific printers and layer thickness requirements.
Q. Can you machine/weld AlSi10Mg AM parts?
A. Yes, AlSi10Mg parts made by 3D printing can be machined and welded via conventional methods after an appropriate stress relief heat treatment.
Q. Is AlSi10Mg powder reusable?
A. AlSi10Mg powder can typically be recycled 5-10 times before a refresh is needed, depending on AM process and contamination levels.
Conclusion
AlSi10Mg is an important aluminum alloy powder for metal additive manufacturing, finding use across aerospace, automotive, medical and industrial applications. Key advantages include high strength-to-weight ratio, corrosion resistance, excellent mechanical properties, and wide certifications for demanding applications.
AM enables complex optimized geometries not possible via casting or machining. AlSi10Mg powder with controlled particle characteristics and composition is critical to achieving defect-free parts. Leading global suppliers provide high quality powder tailored to AM processes like DMLS and SLM.
About Met3DP
Product Category
HOT SALE
CONTACT US
Any questions? Send us message now! We’ll serve your request with a whole team after receiving your message.
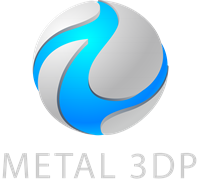
Leading provider of additive manufacturing solutions headquartered in Qingdao, China.
COMPANY
PRODUCT
cONTACT INFO
- Qingdao City, Shandong, China
- [email protected]
- [email protected]
- +86 19116340731