Overview
Metal powders are fine metal particles used as feedstock for manufacturing techniques like additive manufacturing, metal injection molding, and powder metallurgy pressing and sintering. Producing advanced specialty metal powders with precise control of chemistry, particle size distribution, morphology, and microstructure is critical to properties of finished components.
There are various methods used for large scale production of metal powder production from different alloy systems including:
- Gas atomization
- Water atomization
- Plasma atomization
- Electrode induction melting gas atomization
- Rotating electrode process
- Carbonyl process
- Electrolytic process
- Metal reduction processes
Each process results in powders with different characteristics suited to specific applications.
Metal Powder Production Methods
Method | Metals Used | Key Characteristics | Main Applications |
---|---|---|---|
Gas Atomization | Titanium, aluminum, stainless steel, tool steel, superalloys | Spherical powders, moderate production rate | Metal injection molding, Hot isostatic pressing |
Water Atomization | Low-alloy steel, iron, copper | Irregular powder shapes, higher oxygen content | Press and sinter process |
Plasma Atomization | Titanium alloys, superalloys | Very fine spherical powders | Additive manufacturing |
Rotating Electrode | Tungsten, molybdenum, tantalum | Controlled grain structure | Filaments, cutting tools |
Carbonyl Process | Iron, nickel, cobalt | Ultrafine high purity powders | Electronic components, magnets |
Electrolytic | Copper, nickel | Dendritic flake morphology | Surface coatings |
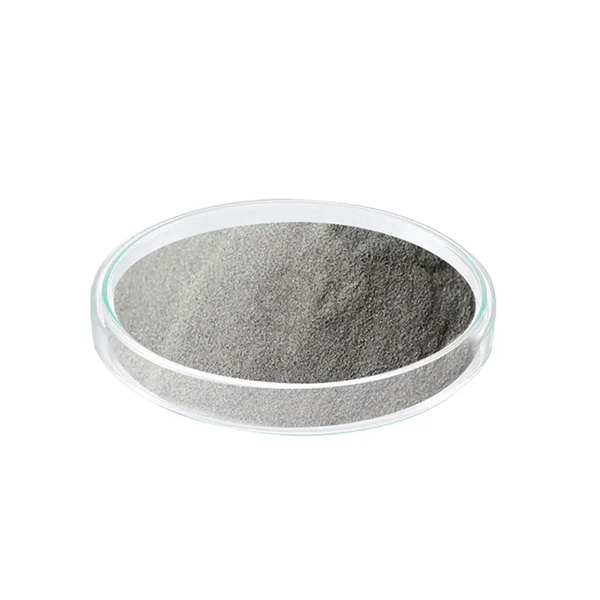
Metal Powder Production Methods
There are a variety of commercial methods used for producing metallic powders from different alloy systems. The choice of production method depends on factors like:
- Type of alloy material
- Purity requirements
- Desired powder characteristics like particle size, shape, grain structure
- Scale of production in tons per year
- Powder end use application
Here are some of the most common industrial processes for metal powder production:
Gas Atomization Process
In gas atomization process, a stream of molten metal alloy is disintegrated by high pressure jets of gas, usually nitrogen or argon. The metal stream breaks up into fine droplets, which solidify into powder particles.
Gas atomized powders have a spherical shape and smooth surface morphology. Particle size distribution can be controlled by adjusting process parameters. This is a widely used technique for reactive materials like titanium, aluminum, magnesium alloys as well as stainless steels, tool steels and nickel superalloys.
Parameter | Description |
---|---|
Metals used | Titanium alloys, aluminum, magnesium, stainless steel, tool steel, superalloys |
Particle shape | Spherical morphology |
Particle size | 50 – 150 μm typical |
Purity | High, inert gas prevents contamination |
Oxygen pickup | Minimal compared to liquid metal atomization |
Production scale | Up to 10,000 metric tons per year |
Water Atomization
In water atomization, the molten metal stream is hit by high velocity water jets. The sudden cooling causes an explosion that breaks the metal into fine particles. The powders have irregular shapes and contain higher oxygen content from water contact.
Water atomization is lower cost process used for producing large volumes of stainless steel, alloy steel, iron and copper powders for pressing and sintering type applications.
Parameter | Description |
---|---|
Metals used | Carbon steels, low alloy steels, stainless steels, copper, iron powders |
Particle shape | Irregular morphology from explosive water breakup |
Particle size | 10 – 300 μm typical |
Purity | Lower, water contact increases oxygen levels by 200-500 ppm |
Production scale | Very high, over 50,000 tons per year |
Plasma Atomization Process
In plasma atomization process, a plasma torch is used to melt the metal alloy before disintegration into fine droplets through gas jets. The ultra-high temperatures enable highly reactive elements like titanium aluminides to be successfully atomized.
The powders have a very spherical shape and narrow size distribution suitable for additive manufacturing methods like laser melting and electron beam melting.
Parameter | Description |
---|---|
Metals used | Titanium alloys, nickel superalloys, titanium aluminides |
Particle shape | Highly spherical |
Particle size | 15 – 45 μm typical |
Purity | Very high purity due to melting under inert atmosphere |
Production scale | Lower, about 100 – 1000 tons per year |
Rotating Electrode Process (REP)
In the rotating electrode process, a cylindrical metallic electrode is spun at high speeds in an evacuated chamber. It is melted using an electric arc and the molten metal droplets flung off through centrifugal forces cool to form powders.
REP powders have a grain structure and morphology ideal for hot extrusion into fine wires and rods for aerospace alloys like tungsten, molybdenum, tantalum.
Parameter | Description |
---|---|
Metals used | Tungsten, molybdenum, tantalum |
Particle shape | Irregular, controlled microstructure |
Particle size | 45 – 150 μm typical |
Purity | Very high from processing under vacuum |
Production scale | Small volumes of high value powders |
Electrode Induction Gas Atomization (EIGA)
The EIGA process uses induction heating to melt consumable electrode tips in an inert gas atmosphere. The droplets undergo secondary gas atomization by argon jets into fine spherical powders.
EIGA enables very high purity of reactive nickel superalloys for critical aerospace components through controlled melting and minimizing contamination.
Parameter | Description |
---|---|
Metals used | Nickel superalloys, titanium aluminides |
Particle shape | Spherical |
Particle size | 15 – 53 μm typical |
Purity | Extremely high, customized for critical alloys |
Production scale | R&D/prototyping to mid-volume |
Carbonyl Process
In the carbonyl process, metal is converted into a volatile carbonyl, which decomposes under controlled conditions to produce uniform, ultrafine metallic particles. This approach is suitable for producing highly pure iron, nickel and cobalt powders.
Parameter | Description |
---|---|
Metals used | Iron, nickel, cobalt |
Particle shape | Spherical to polyhedral |
Particle size | 1 – 10 μm typical |
Purity | Extremely high 99.9%+ purity |
Production scale | Up to 30,000 tons per year |
Other Powder Production Methods
Some other techniques used for specialty metal powder production include:
- Electrolytic Process: Used for producing irregular shaped copper and nickel powders with dendritic morphology by electro-deposition process
- Metal Reduction Processes: Reduction of metal oxides using hydrogen or carbon to produce titanium, zirconium, tungsten, molybdenum powders
- Mechanical Alloying: High energy ball milling to synthesize composite and nanostructured alloys
Metal Powder Specifications
Critical quality attributes and specifications tested for metal powders depend on production method and end-use application but typically include:
Powder Chemistry
- Alloy composition using optical emission or X-ray fluorescence spectroscopy
- Minor alloying elements
- Impurity elements like oxygen, nitrogen, hydrogen
- Loss on ignition testing at high temperature
Particle Size Distribution
- Volume mean particle size
- Distribution widths like D10, D50, D90
Particle Shape Characterization
- Scanning electron microscopy for morphology
- Shape factors like aspect ratio and form factor
Microstructure
- Phases present using X-ray diffraction
- Grain characteristics from imaging
Powder Properties
- Apparent/tap density
- Flow rates through Hall flowmeter funnel tests
- Compressibility levels
Specification requirements for powders vary widely depending on end use in different applications:
Parameter | Metal Injection Molding (MIM) | Additive Manufacturing | Press & Sinter |
---|---|---|---|
Particle size range | 3 – 25 μm | 15 – 45 μm | 150 – 300 μm |
Aspect ratio | 1 – 1.25 preferred | <1.5 spherical | Not critical |
Oxygen levels | <1000 ppm | <500 ppm | 2000 – 4000 ppm |
Apparent density | >2.5 g/cm3 | >2.8 g/cm3 | 2 – 3 g/cm3 |
Hall flow rate | 15 – 35 s/50g | 25 – 35 s/50g | >12 s/50g |
Characterization Methods
There are several analytical methods used to characterize the properties of metal powders essential to product performance:
Particle Size Analysis
Laser diffraction methods are most widely used to characterize the particle size distribution. This technique passes a laser beam through a dispersed powder sample which scatters light at an angle dependent on particle sizes. Computer analysis of the diffraction pattern provides detailed statistically relevant size distribution data within seconds.
Morphology and Surface Imaging
Scanning electron microscopy (SEM) provides high resolution images of powder particle shape, surface topographies and features at much higher magnification and depth of focus compared to optical microscopy.
SEM imaging is used to study particle rounding, satellite formation, surface smoothness and defects like porosity.
Density and Flow Property Measurement
Standard test methods have been established to quantify bulk behavior using:
- Hall flowmetry funnel to measure powder flow rates through an orifice
- Carney funnel to assess flowability by angle of repose
- Scott volumeter to determine tap density and compressibility
These methods help predict ease of handling, blending, die filling and spreading during component manufacturing.
X-ray Methods for Composition and Crystal Structure
- X-ray fluorescence spectroscopy accurately identifies and quantifies elemental composition of metals
- X-ray diffraction analyzes the atomic arrangements and phases present by diffraction peak patterns
Applications of Metal Powders
Some major end uses of engineering metal powders include:
Additive Manufacturing
Also known as 3D printing techniques like selective laser melting (SLM), direct metal laser sintering (DMLS) and electron beam melting (EBM) to build complex geometries from titanium, aluminum, stainless steel, superalloy, cobalt chrome powders.
Metal Injection Molding (MIM)
Powders like stainless steels, titanium alloys and tool steels are combined with a binder, injection molded then sintered to manufacture small, complex parts at high volumes for lower costs.
Powder Metallurgy Press and Sinter
Compacting and sintering iron, copper and alloy steel powders into high volume components like gears, bushings and magnets.
Application | Metals Used | Key Property Needs |
---|---|---|
Additive manufacturing | Titanium alloys, nickel superalloys, aluminum, tool steel, stainless steel, cobalt chrome | Spherical morphology Good flowability High purity |
Metal injection molding | Stainless steel, titanium, tool steel, tungsten heavy alloys | Fine <25 μm powder Good packed density |
Press and sinter | Iron, steel, stainless steel, copper | Cost effective powder Lubricant coatings |
There are also niche applications in areas like welding, diamond tools, electronics and surface coatings that use specialty metal powders.
Suppliers and Pricing
Some leading global suppliers of various metal powders are:
Company | Production Methods | Materials |
---|---|---|
Sandvik Osprey | Gas atomization | Titanium, aluminum, nickel alloys |
AP&C | Plasma atomization | Titanium aluminides, superalloys |
Carpenter Technology | Gas, water atomization | Tool steels, stainless steels, alloys |
Höganäs | Water atomization | Iron, stainless steels |
JFE Steel | Water atomization | Stainless steel powders |
Rio Tinto | Aluminum powder | Carbonyl nickel and iron |
Pricing for metal powders varies widely by:
- Alloy material and composition
- Production method used
- Processing to achieve particle characteristics
- Purity levels and degree of contamination
- Purchase volumes – very high volume contracts bring lower pricing
Typical base prices per kilogram are:
Material | Pricing Estimate |
---|---|
Stainless steel 316L | $12 – $30 per kg |
Aluminum AlSi10Mg | $15 – $45 per kg |
Titanium Ti-6Al-4V | $80 – $220 per kg |
Nickel superalloy Inconel 718 | $90 – $250 per kg |
Specialty alloys for AM | $250 – $1000 per kg |
Prices go up significantly for highly customized particle size distributions, controlled oxygen and nitrogen levels below 100 ppm, and small lot purchases.
Advantages and Limitations of Powder Metallurgy
Benefits of Powder Metallurgy
- Ability to produce complex geometries not possible through casting or machining
- Near-net-shape manufacturing reduces material waste
- Higher performance metals and alloys can be used
- Consistent porosity structures not possible in ingot metallurgy
- Components can be mass customized
Limitations of Powder Production and Processing
- Capital investment for production and handling equipment is very high
- Increased surface area makes handling pyrophoric reactive powders risky
- Achieving high compaction densities can require high pressures
- Additional process steps compared to casting
- Portability of AM machines due to powder being LO/NO
Here is a quick comparison of powder metallurgy against the conventional casting process:
Parameter | Powder Metallurgy | Casting |
---|---|---|
Complex shapes | ✅ Excellent for layered AM builds | Limited for typical castings |
Mechanical properties | Can approach cast properties after Hot Isostatic Pressing | ✅ Predictable properties |
Cycle time | Slower process for AM methods | ✅ Faster for volume production |
Dimensional accuracy | Varies, depends on post-processing | Very good for precision investment castings |
Equipment costs | Very high for industrial AM machines | ✅ Lower capital costs |
Types of metals | Continually expanding options | ✅ Broadest selection |
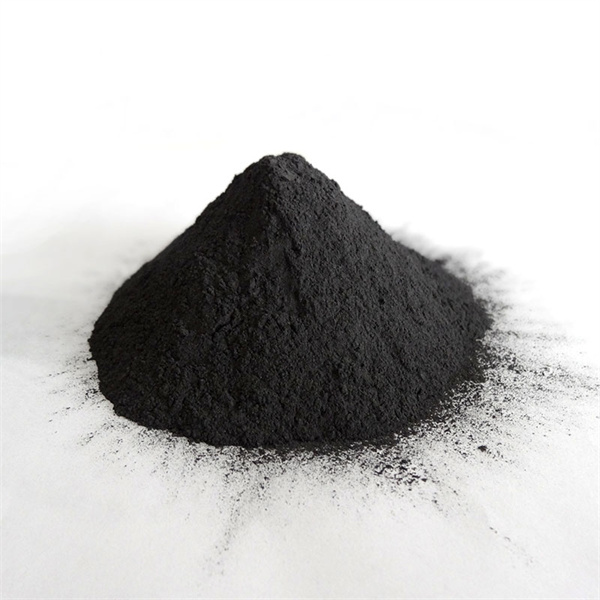
FAQs
Q: What is the typical particle size range used in metal 3D printing powders?
A: In powder bed technologies like selective laser melting (SLM) and electron beam melting (EBM), the optimal particle size range is 15-45 microns. Finer powders improve resolution but can be challenging to handle and process.
Q: What determines morphology of metal powders from different methods?
A: Production factors like intensity of melt stream breakdown forces from gas jets or water impacts and subsequent cooling rates determine particle shapes. Faster cooling produces irregular, dendritic particles while slower solidification (spherical atomization) enables smooth rounded structures.
Q: Why is high purity important for metal powders in additive manufacturing?
A: Impurities can cause defects, porosity issues, alter alloy microstructures, reduce density, affect performance under loads and temperatures – negatively impacting mechanical properties. Target oxygen levels below 500 ppm and nitrogen levels below 100 ppm have become typical.
Q: How are metal powders handled safely during transportation and storage?
A: Reactive metal powders are passivated to create oxidized surfaces minimizing flammability risk. Powders are sealed in drums under inert gases like argon instead of air during shipment to prevent ignition. Storage containers must be properly grounded. Personnel wear specialized PPE while handling.
Q: What are common powder characterization methods?
A: Hall flowmetry, tap density tests, pycnometry, LOI testing, spectrographic analysis, metallography and particle size distribution using laser or sieve techniques are vital to quantifying behavior, building quality process control for metal powder production and assessing batch suitability for given applications.