Aluminum alloy powders offer light weighting combined with strength, durability and corrosion resistance across automotive, aerospace and industrial applications. This guide covers common compositions, properties, manufacturing methods, sizes, suppliers, applications and selection.
aluminum alloy powder Overview
Spherical aluminum powders with controlled particle size enable high performance light metal components via PM, MIM and AM:
Alloys | 2xxx, 6xxx, 7xxx series Aluminum |
Properties | Low density, strength, hardness, wear resistance |
Processes | Powder metallurgy, Metal injection molding, Aluminum AM |
Applications | Automotive, Aerospace, Industrial |
Benefits | Weight reduction, performance, recyclability |
Advanced aluminum powders balance ultra lightweight density with improved mechanical properties over cast or wrought alloys.
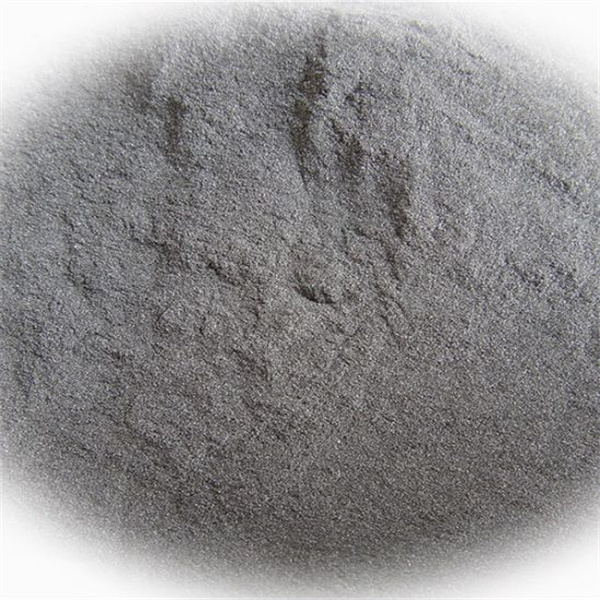
aluminum alloy powder Types
Series | Alloying Elements | Characteristics |
---|---|---|
2000 | Copper | Good strength, machinability, ductility after PM consolidation |
6000 | Magnesium, Silicon | Medium strength, superior corrosion resistance |
7000 | Zinc | Highest strength, used mainly for high performance aerospace components |
Emerging Alloys
Scandium or zirconium containing aluminum alloys and nanocomposite Al-TiC achieve substantial strengthening for specialized applications.
aluminum alloy powder Properties
Property | Typical Values |
---|---|
Density | 2.55-2.8 g/cc |
Tensile strength | 200-600 MPa |
Yield strength | 160-500 MPa |
Elongation | 3-10% |
Melting point | 500-650°C |
Finer aluminum powder sizes produce higher consolidated strength values approaching wrought alloys. Heat treatability also boosts mechanical performance.
Manufacturing Method
Atomization | Gas or water atomization from molten alloy produces fine spherical powders |
Mechanical Mill | Cost-effective method using ball or attritor mills, less spherical particles |
Alloying | Direct alloying or ad-mixing elemental/pre-alloyed base powders |
Gas atomization allows the most precise property control while milling increases shape complexity and internal porosity. AM suitable powders utilize atomization but maintain flowability.
aluminum alloy powder Particle Sizes
Typical aluminum alloy powder sizes used:
Process | Size Range |
---|---|
Press and sinter | 50-150 microns |
Metal Injection Molding (MIM) | 10-25 microns |
Binder jet Additive Manufacturing (BJAM) | 20-60 microns |
Directed Energy Deposition (DED) | 50-150 microns |
Optimizing particle size distribution and shape impacts packing density and sintering response.
Leading Suppliers
Company | Grades | Price Estimate |
---|---|---|
Hoeganaes | 1001, 2003, 6065, 7009 | $5-8 per lb |
BASF | 2024, 6061, 7050, 7068 | $6-10 per lb |
Sandvik Osprey | 2024, 6061, 7075 | $8-15 per lb |
Kymera | 2024, 6061, 7068, 7093 | $7-12 per lb |
Prices vary based on order volume, powder characteristics and alloy composition.
Applications of aluminum alloy powder
Industry | Components |
---|---|
Automotive | Power train parts like connecting rods, shafts |
Aerospace | Structural brackets, airfoil components like flap tracks |
Industrial | Heat sinks, pistons, seals, fasteners, sprockets |
Electronics | Heat dissipation devices like LED housings |
Benefits
- Weight reduction over titanium/steel alternatives
- Improved fuel economy or range
- Reduced numbering of parts via integration
Selection Guidelines
Criteria | Best Practices |
---|---|
Alloy | Match powder to mechanical and environmental needs |
Manufacturing Method | AM needs spherical gas atomized; MIM extra fine |
Size distribution | Tailor based on consolidation technique density targets |
Apparent density | Higher improves sintering response |
Surface oxygen analysis | <0.5% for strongest performance |
Price | Get quotes based on volume from at least 2 suppliers |
Carefully balancing application requirements, manufacturing process and budget informs optimal aluminum alloy powder sourcing. Consider sampling evaluation programs.
Pros vs. Cons
Pros | Cons |
---|---|
Lightweighting and fuel efficiency | Lower strength than ferrous alloys |
Corrosion/oxidation resistance | Prone to galvanic corrosion |
Recyclability | Poor high temperature properties |
Improved life cycle impact | Higher cost than cast aluminum |
Key Takeaways
- Advanced aluminum powders outperform cast and wrought grades on density-specific basis
- Tailor powder characteristics to requirements of end-use manufacturing techniques
- Alloy customization and emerging composites continue expanding capabilities
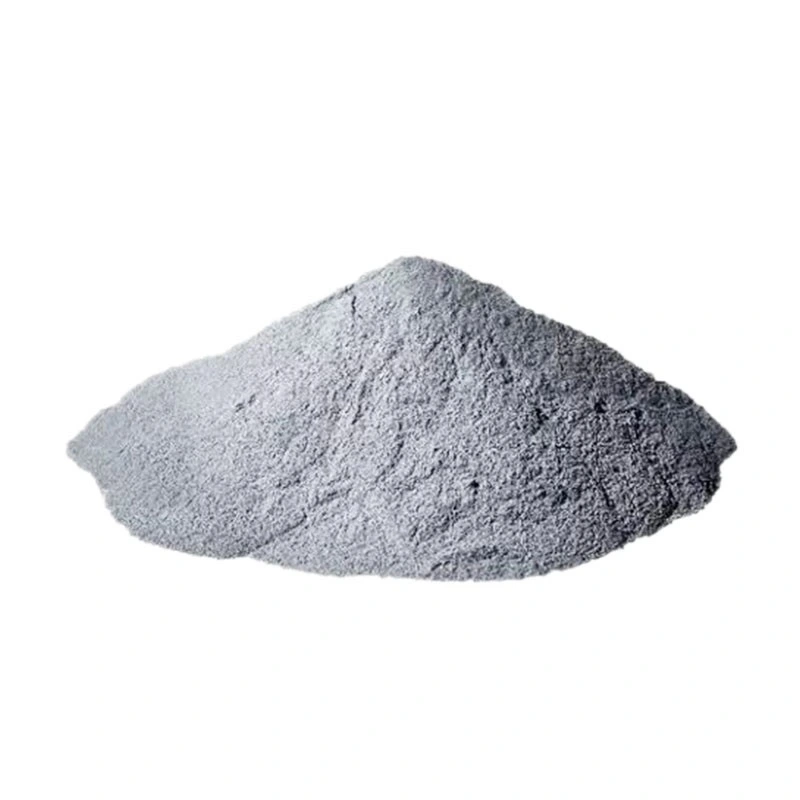
FAQs
Q: What is the most widely used aluminum alloy powder?
A: Aluminum 6061 is the workhorse alloy leveraged across automotive and general engineering for its versatile mechanical properties, corrosion performance and moderate cost.
Q: How does aluminum powder cost compare with titanium?
A: Aluminum powders start around $5/lb versus $50+/lb for titanium demonstrating significant conversion cost benefits for lightweighting despite lower mechanical properties.
Q: Does aluminum powder oxidize?
A: Fine aluminum powders present oxidation risks during handling, storage and processing requiring inert environments and tight quality controls to minimize risks.
Q: Can you 3D print aluminum alloy parts?
A: Yes, aluminum DED and binder jet AM is maturing quickly for structural aerospace components leveraging advanced powders and processing refinements to achieve over 99% density after sintering.