Overview of Aluminium Alloy 7050 Powder
Aluminium 7050 is a high-strength aluminium alloy commonly used in aerospace applications. Key details about 7050 aluminium alloy powder:
- Contains zinc, magnesium, copper as primary alloying elements.
- Exhibits excellent strength-to-weight ratio and corrosion resistance.
- Used for critical structural parts, landing gear, fuselage components in aerospace.
- Available in powder form for additive manufacturing processes like selective laser melting (SLM) and electron beam melting (EBM).
- Powder production methods include gas atomization, plasma atomization, and cryomilling.
- Powder characteristics like particle size distribution and morphology optimized for AM.
Typical Applications of 7050 Aluminium Parts
Category | Applications |
---|---|
Aerospace | Structural airframe components, landing gear, rockets |
Automotive | Wheels, control arms, drivetrain parts |
Industrial | Robotics, tooling jigs and fixtures, instrumentation |
Marine | Propellers, drive shafts, pumps, valves |
The lightweight strength of 7050 makes it suitable for high-performance structural parts across industries.
Aluminium 7050 Powder Specifications
Parameter | Typical Value | Role |
---|---|---|
Particle size | 20-63 μm | Affects packing density and flow |
Morphology | Spherical | Improves powder flow in AM machines |
Alloy composition | Zn – 6%, Mg – 2%, Cu – 2.3% | Determines properties |
Apparent density | 1.7-2.0 g/cc | Impacts final part density |
Hall flow rate | <30 s/50g | Fast flow ensures uniform layers |
Moisture content | <0.1% | Minimizes powder oxidation |
Maintaining consistent powder characteristics is crucial for high quality AM processing.
Equipment for Aluminium Powder Production and Handling
Equipment | Description |
---|---|
Atomizers | Convert molten alloy into fine powder using gas or plasma energy |
Mills | Mechanical milling reduces powder particle size and morphology |
Sieves | Classify powder into narrow size ranges suitable for AM |
Mixers | Homogenize blended powders evenly |
Hoppers | Store and supply powder to printers |
Recyclers | Remove contamination from reused powder and improve flow |
Specialized powder handling equipment required to prevent oxidation and contamination.
Suppliers of 7050 Aluminium Powder
Supplier | Details | Pricing |
---|---|---|
Supplier 1 | Wide range of aluminium alloys. | $80-100/kg |
Supplier 2 | Custom alloy development. | $100-150/kg |
Supplier 3 | High purity medical/aerospace grades. | $150-300/kg |
Price depends on purity, distribution, lot size, quality, and other parameters. Small R&D batches typically more expensive.
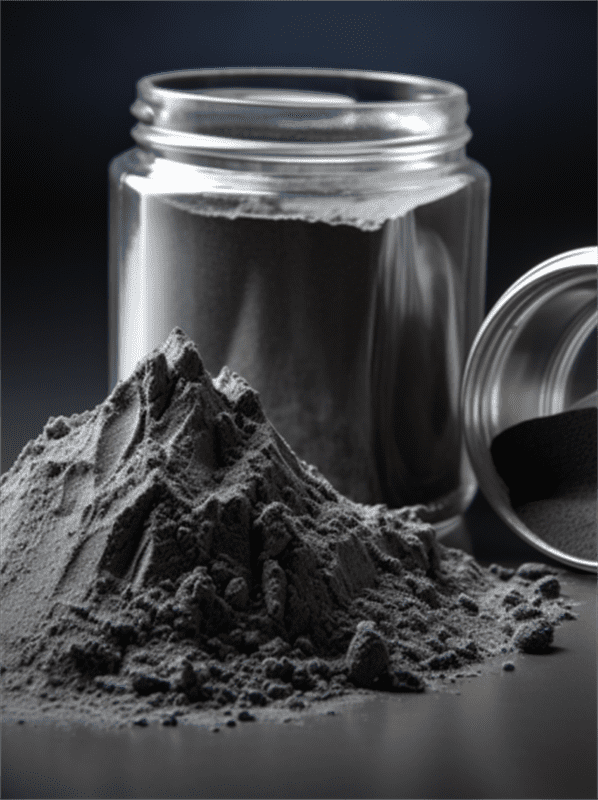
How to Choose a 7050 Aluminium Powder Supplier
Key factors when selecting a 7050 aluminium powder supplier:
- Experience – Look for an established supplier with extensive technical experience with aluminium alloy powders. This results in higher quality and consistency.
- Production capability – Supplier should be able to produce consistent batches meeting specified size distribution, morphology, purity etc.
- Quality systems – ISO 9001 or AS9100 certification indicates reliable quality control and assurance.
- Technical expertise – Powder production requires significant metallurgy and materials science knowledge. Ensure suppliers have this.
- Testing capabilities – Supplier should fully test all powder lots and provide detailed certification data.
- Responsiveness – They should respond quickly to inquiries, requests for quotes, samples, etc.
- Customer support – Choose a supplier who provides good technical advice and application support.
Select a supplier familiar with needs of the AM industry and your specific application requirements.
How to Optimize 7050 Powder for AM Processing
Follow these guidelines when preparing 7050 aluminium powder for additive manufacturing:
- Start with high purity gas-atomized powder with controlled particle size distribution (e.g. 20-45 μm).
- Use spherical powder morphology for optimal packing density and spreading. Avoid satellite particles.
- Store powder properly in sealed, inert environments to prevent oxidation. Desiccant drying may be needed.
- Consistently characterize new powder lots – composition, size distribution, morphology, flow rate, oxide content.
- Blend in any alloying elements homogeneously to prevent composition gradients in printed parts.
- For SLM, use minimum layer thicknesses equal to 8-12x the powder particle size.
- Adjust laser power to achieve full melting and density without excessive evaporation.
- Minimize contact between powder and oxygen/moisture during printing to reduce oxidation.
- Consider classifying and sieving recycled powder to refresh size distribution and flowability.
Work jointly with your powder and AM machine suppliers to identify ideal powder characteristics and printing parameters.
Design Principles for AM Parts in Aluminium 7050
When designing aluminium 7050 parts for additive manufacturing, consider these guidelines:
- Use minimum wall thicknesses of 1-2 mm to ensure sufficient strength. Thinner walls risk cracking.
- Design with angular transitions instead of sharp corners to reduce stress concentrators.
- Avoid overhangs exceeding 45° to eliminate the need for extra supports.
- Position the part orientation to minimize support requirements and avoid collisions with the recoater blade.
- Account for 20-50% lower strength horizontally vs vertically due to anisotropy from layer-based construction.
- Allow for post-machining removal of 0.3-0.5 mm of stock material to improve surface finish.
- Consolidate sub-assemblies into a single printed part where possible to reduce weight and minimize fasteners.
- Include vent holes in enclosed volumes to prevent pressure buildup during processing.
Validate designs using finite element analysis simulation and actual AM build trials.
Post-Processing Aluminium 7050 AM Parts
Common post-processing techniques used for as-printed aluminium 7050 components include:
- Support removal via hands tools or dissolution in caustic solutions.
- Stress relieving heat treatment at 300°C for 2 hours. Prevents cracking.
- Machining – CNC milling and turning to improve dimensional precision and surface finish. Use rigid setups and sharp tools.
- Abrasive blasting or grinding reduces surface roughness. Must control media to prevent embedment.
- Vibratory finishing smoothes surfaces and removes adhered particles.
- Anodizing increases hardness and corrosion resistance.
- Metal plating improves wear resistance or conductivity.
- Joining processes like screwing or riveting to assemble components. Adhesives also possible.
Use qualified operators familiar with aluminium alloys during all post-processing steps.
Integrating Printed 7050 Parts into Assemblies
To successfully integrate 3D printed aluminium 7050 parts into end-use assemblies and products:
- Thoroughly clean surfaces of any residual powder, oxidation layers, or other contaminants. Use chemical or thermal deburring if needed.
- Apply protective coatings as needed – anodizing, painting, powder coating all suitable. Improves durability.
- Account for lower ductility compared to cast or wrought aluminium when designing interfaces and joints.
- Allow for thermal expansion differences when mating AM components to parts of other materials.
- Select optimal joining techniques – adhesives, fasteners, brazing, and welding can all be used depending on loads.
- Heat treatment during integration may be needed – for example, stress relieving AlSi10Mg support structures.
- Validate assembly functionality under expected use conditions through prototyping and testing.
Work collaboratively with manufacturing engineers throughout the integration process to ensure performance requirements are met.
Operating and Maintaining Printed Aluminium 7050 Parts
To achieve the best performance from additively manufactured aluminium 7050 components when in service:
- Operate within recommended high temperature limits based on the alloy specifications. Prolonged exposure over 120°C accelerates precipitation hardening.
- Avoid excessive loads that result in yielding, deformation, or fatigue failure. AM parts have lower ductility.
- Use protective anodized or painted coatings in corrosive environments. 7050 is susceptible to corrosion without protection.
- Periodically inspect critical dimensions and parameters to check for wear, cracks, or distortions indicating an issue.
- Disassemble mechanisms and apply fresh grease/oil if required – prevent seizing over time.
- Replace any components approaching their expected service life as a preventive measure.
- Monitor manually or via nondestructive testing for developing flaws like cracks during routine maintenance intervals.
Develop detailed part maintenance plans and schedules in conjunction with design and test engineers to ensure in-service performance.
Pros and Cons of Aluminium 7050 AM vs Traditional Methods
Advantages of additive manufacturing with aluminium 7050 powder:
- Complex geometries and lightweight lattices can be fabricated.
- No required tooling investment for small to medium production volumes.
- Rapid prototyping of new designs and custom parts on demand.
- Reduced waste – use only required amount of material.
- Ability to consolidate sub-assemblies into single printed parts.
- Shorter development timelines versus traditional manufacturing methods.
Limitations to consider:
- Higher per-part cost for small production volumes, although AM scale effects can be favorable.
- Limitations on maximum part size based on printer build volume.
- Additional post-processing often needed to achieve final material properties and tolerances.
- Anisotropic properties due to layer-by-layer printing.
- Supply chain restrictions for aerospace-grade powder material.
- Lower ductility and fatigue life than wrought 7050 aluminium.
Evaluate the pros/cons relative to production volumes, cost targets, quality needs and specific application requirements.
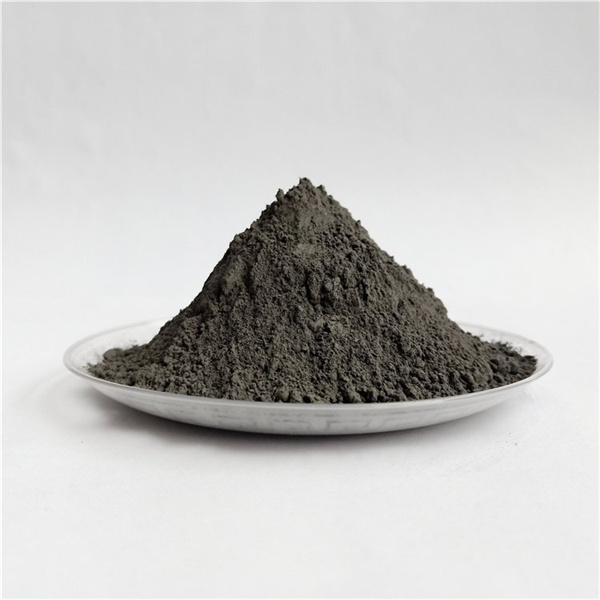
FAQ
Q: What particle size range is recommended for 7050 aluminium AM powder?
A: Typically 20-45 microns, with a tightly controlled distribution. Too fine causes handling issues while too large negatively affects density.
Q: What applications are 7050 aluminium AM parts used for?
A: Primarily structural components in aerospace, automotive, and high-performance machinery where high strength-to-weight ratios are critical.
Q: Does aluminium 7050 powder require special storage precautions?
A: Yes, 7050 powder is highly susceptible to oxidation. It must be stored in vacuum sealed bags with desiccant packs and minimal air exposure.
Q: What post-processing methods are commonly used on 7050 AM parts?
A: Support removal, stress relieving, machining, blasting, anodizing, and plating. Apply any steps needed for integration like fastening.
Q: Is heat treatment needed for 7050 AM parts?
A: Yes, 7050 is typically stress relieved at 300°C for 2 hours after printing to prevent cracking due to internal stresses.
Q: What density can be achieved with optimally processed 7050 aluminium AM parts?
A: Density above 99% is achievable with careful control of powder quality and dialing in ideal SLM/EBM parameters.
Q: Can you weld aluminium 7050 AM components?
A: Yes, friction stir welding is recommended for aluminium AM parts if needed. Conventional fusion welding alters local material properties.
Q: What safety precautions are required when handling aluminium powders?
A: Use protective equipment to prevent inhalation or skin contact. Control dust levels to avoid combustion hazard since aluminium is flammable.