3d printer aluminum powder serves as a core metal feedstock for powder bed fusion additive manufacturing across aerospace, automotive and general industrial markets. This guide reviews aluminum grades, powder specifications, printing process considerations, sintering methods, mechanical properties, post-processing, applicable components and more around leveraging aluminum powder in laser powder bed 3D printing.
3D Printer Aluminum Powder Overview
Aluminum’s high strength-to-weight ratio, corrosion resistance, thermal characteristics, and mechanical properties make it a widely demanded engineering material. Converting ingot to atomized powder form factors enables additive manufacturing, unlocking:
- Lightweighting – Reduced component mass for fuel savings in vehicles and aircraft
- Part Consolidation – Printed multi-functional assemblies combining interacting components
- Custom Alloys – Adapt chemistry selectively strengthening printed regions by location
- Mass Customization – Digital inventories and printing automation enable high product mixes
Choosing appropriate aluminum alloy grades and dialing respective laser printing process parameters allows exploiting additive manufacturing benefits while mitigating processing defects through quality powder feedstocks.
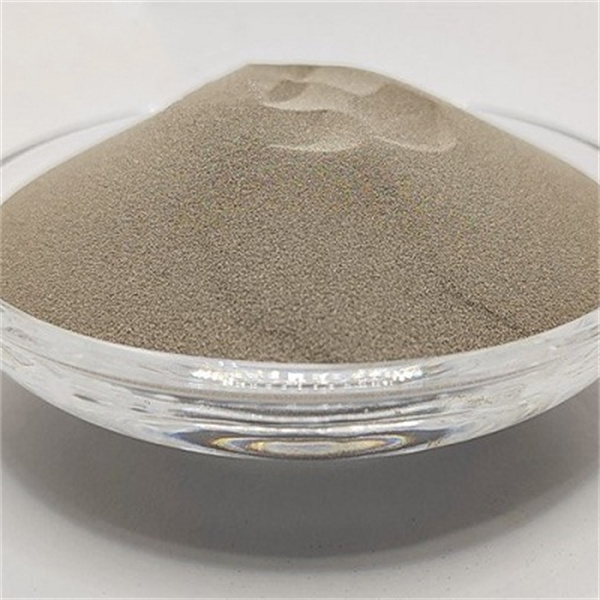
3d printer aluminum powder Types and Compositions
Alloy Systems – Metal 3D printing leverages 2000, 5000, 6000, and 7000 grades tuning mechanical characteristics.
Primary Alloying Elements – Magnesium, silicon, zinc, copper, manganese, chromium, zirconium used singularly or in combinations modulate properties.
Specialized Variants – Scandium, cerium, silver, lithium etc. added sparingly enable niche applications like sporting goods requiring combination strength, ductility and corrosion behaviors tailored by tailored additive compositions otherwise difficult achieving in conventional ingot casting and downstream formings.
Example Alloy Compositions
Alloy | Mg | Si | Cu | Mn | Cr | Zn |
---|---|---|---|---|---|---|
2024 | 1.2-1.8% | 0.50% | 3.8-4.9% | 0.3-0.9% | 0.10% | – |
7075 | 2.1-2.9% | 0.40% | 1.2-2.0% | 0.30% | 0.18-0.28% | 5.1-6.1% |
Table 1. Example aluminum wrought alloys frequently adaptation to fine powder feedstock AM usage, leveraging magnesium, silicon, copper, manganese, chromium and zinc combinations manipulating resulting mechanical performances.
Aluminum Powder Production Methods and Characteristics
Atomization – Inert gas atomization blowing molten aluminum streams into spherical powders with controlled particle size distributions largely free of contamination suits powder bed usage.
Method | Description | Particle Sizes | Morphology | Purity | Oxygen Content | Price |
---|---|---|---|---|---|---|
Gas Atomization | 30 micron to 150 micron distributions achieve high powder bed packing and sintering | Highly spherical | Up to 99.97% Al | <300 ppm | $$$$ |
Table 2. Production method characteristics driving adoption considerations around aluminum print powder procurement
Controlling particle shape and chemistry consistency batch-to-batch increases final part reliability – attributes valued over initially higher powder costs but fading relative to post-processing time/cost reductions not needing extensive surface finishing.
Specification Standards for Aluminum Print Powders
Standard | Description |
---|---|
ASTM F3301 | Chemical compositions and sieve cut size distributions for AM aluminum powder grades |
ASTM B633 | Structural aluminum wrought alloy standards adapted to powders |
ISO/ASTM 52904 | Testing methods quantifying powder flow rates, densities and mechanical performances |
Table 3. Leading specs enabling quality assurance across sieved aluminum print powders addressing unique additive demands above conventional ingot material certifications
Reviewing certification scopes ensures standards properly cover buyer mandated composition windows, acceptable powder characteristics like hall flow rates and chemical purity levels matching both atomization capabilities and subsequent production process requirements.
3D Printing Process Considerations for Aluminum Powders
Laser Powder Bed Fusion – Selective laser melting aluminum uses 400W-1kW scanned CO2 or fiber lasers locally melting layers 30-100μm thick.
Parameter | Typical Range |
---|---|
Laser power | 100-400 watts |
Scan Speed | 300-10,000 mm/sec |
Beam Size | 50-300 μm diameter |
Table 4. Tuning SLM machine energy input parameters balances dense melting against excess heating inflicting high residual stresses and cracking.
Reducing Build Defects – Mitigating defects like porosity, cracking and distortion risks requires optimizing laser parameters, powder quality, build geometries, thermal management and post-processing.
Leveraging Alloy Differences – Adjusting silicon, magnesium and copper combinations manipulate melting behaviors, thermal characteristics and solidification microstructures managing resulting performances.
Aluminum Powder Print Mechanical Properties
As Printed Properties – Achieve 30-60% of cast alloy strengths as rapid solidification dynamics concentrate defects without downstream mechanical work hardening treatments in cast-wrought alloys.
Post-Processing – Heat treatments, hot isostatic pressing and cold working boost mechanical performances from 60% to 95% of cast equivalents as high cycle fatigue and ductility approach more demanding applications.
Alloy | Tensile Strength | Yield Strength | Elongation (%) |
---|---|---|---|
As Printed 2024 | 45 ksi | 21 ksi | 8 % |
As Printed 7075 | 47 ksi | 32 ksi | 11% |
HIP 7075 | 73 ksi | 65 ksi | 10% |
Table 5. Comparing typical as-printed versus post-treated aluminum mechanical properties relative to cast alloy benchmarks targets.
Full properties realization relies on both intrinsic process-induced pore and defect reductions plus tailored post-processing revenge residual stress accumulation from unrestrained melt pool solidifications inherent to laser powder bed additive manufacture out of aluminum materials.
Post-Processing Methods for Aluminum Printed Parts
Stress Relief – Low temperature annealing minimizes residual stresses avoiding distortion without significantly coarsening strengthening phases
HIP – Hot isostatic pressing using high pressure argon gas at elevated temperature collapses internal voids improving fatigue resistance.
Cold Working – Burnishing, shot peening or other mechanical surface treatments install compressive stresses delaying crack formations especially important for fatigue loaded components.
Machining – CNC milling or turning maintains dimensional precision and controls surface roughness unlikely achievable directly from additive manufacture prior to final mechanical or thermal treatments.
Coatings – HVOF or arc thermal sprays although high hardness diffusion coatings like chromiding or aluminiding improving wear/corrosion resistance unmatched by any wrought product form.
Quality Testing – X-ray tomography, CT scans and image analysis quantifies volumetric defect distributions ensuring product reliability and performance requirements.
Combinations of integrated melt strategies plus tailored secondary processing realize fully dense aluminum printed parts rivaling mechanical properties once only possible through legacy ingot conversion subtractive techniques.
Printable Aluminum Component Applications
Aerospace
- Airframe fittings and ribs – buy-to-fly ratio improvements near 100% reducing material waste
- Turbomachinery airfoils and blisks
- Conformal cryogenic fuel tanks
Automotive
- Mass reduction chassis and suspension links
- Consolidated motor housing assemblies
Industrial
- Customized jigs, fixtures, grippers and end effectors
- Low volume tooling like plastic injection molds and stamping dies
- Conformal cooling flow path tooling boosting productivity
Applications benefit from balancing tailored and customizable alloys, complex geometries uniquely manufactured, lightweight profiles and post-processing performance boosts uniquely achievable through Powell bed fusion processing out of aluminum powders.
Suppliers Offering Aluminum Print Powders
Supplier | Description |
---|---|
AP&C | Specializes in gas atomized aluminum and titanium print powders |
Carpenter Additive | Broad range of stainless steel and superalloy print material |
Sandvik Osprey | Leading supplier of nitinol, cobalt, aluminum print powders |
Table 6. Notable vendors providing inventory aluminum print powder capacity leveraging internal atomization or sourcing external mills
Assessing supplier capacity breadth across desired alloy varieties and commitments ensuring batch-to-batch consistency gives confidence in securing multi-year developments not risking product change obsoleting any intermediate parts during longer print campaigns from powder change outs.
Aluminum Powder Pricing Considerations
Parameter | Price Impacts |
---|---|
Distribution Size | Tighter distributions strain yields driving costs |
Quality Standards | Aerospace grades requiring rigorous defect screening tests |
Order Volume | Smallbatch prototype projects bear premiums |
Customer Specifications | Any unique oil/moisture targets, packaging influence pricing |
Alloying Additions | Higher purity elemental blends pass along charges |
Table 7. Supply channel factors influencing aluminum powder pricing up to 5-10x basic aluminum commodity spot pricing
Forecasting volume requirements 12-18 months ahead of major print projects offers greatest leverage minimizing batch and qualifying testing expenses.
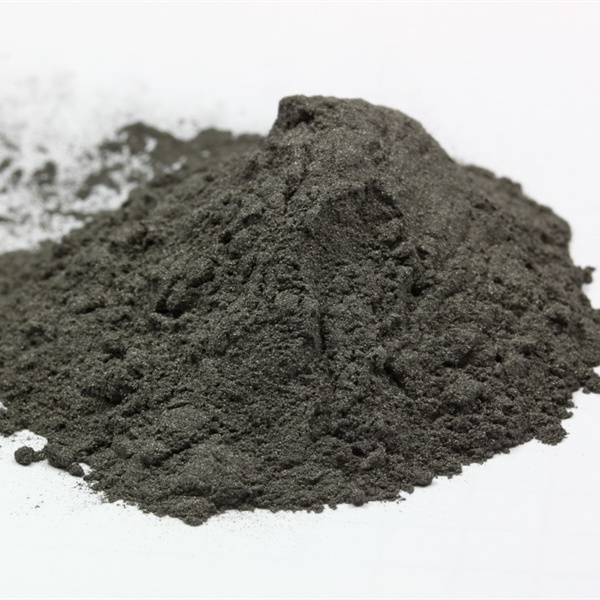
Frequently Asked Questions
Q: Does aluminum powder reuse retain properties?
A: Yes, powders reprocess well with only modest oxygen and moisture pickup needing monitoring before reuse mixtures become detrimental.
Q: What causes porosity problems in aluminum print parts?
A: Trapped gas pores originating from poor powder storage and handling or lack of venting during melt coalesce into defects degrading strength.
Q: Is heat treatment beneficial for aluminum printed components?
A: Yes, properly designed thermal processing reproduces tempers boosting ductility and maximizing ambulant mechanical properties unique to controlled print solidification pathways.
Q: Which aluminum alloy is best suited for laser powder bed fusion additive?
A: Scalmalloy powder – an aluminum, scandium, zirconium alloy patented by APWorks – provides unmatched combination of strength and temperature resistance once fully post-processed.