Tungsten powder is a fine gray powder made from tungsten metal. It has unique properties that make it useful across many industrial and commercial applications. This guide provides a comprehensive overview of tungsten powder, its manufacturing methods, applications, suppliers, costs, and more.
Overview of Tungsten Powder
Tungsten powder, also known as tungsten metal powder or Wolfram powder, refers to micron-sized particles of pure elemental tungsten. It appears as a gray-black powder which feels heavy and gritty to touch.
Tungsten has the highest melting point of all metals and is exceptionally dense and hard. This gives tungsten powder excellent high-temperature properties as well as wear resistance, hardness, and durability. At the same time, it can be alloyed with other metals or formed into shapes through powder metallurgy techniques.
Some key properties and characteristics of tungsten powder include:
- High density – 19.3 g/cm3, almost twice that of lead
- High melting point – 3422°C, the highest of all metals
- Low coefficient of thermal expansion
- Excellent thermal and electrical conductivity
- Resistance to wear, erosion, and arcing
- Biocompatible and non-toxic when pure
- Grayish-black color with metallic luster
Tungsten powder is available in different particle sizes ranging from 1 micron to 150 microns. The particle shape can be spherical, flaky or irregular. Finer powders provide more uniform mixing and better densification. Coarse particles are preferred for applications like tungsten weights.
The key manufacturing process used to produce tungsten powder is hydrogen reduction of tungsten oxides. Pure tungsten powders are bright silver-gray while impure grades appear brown or black.
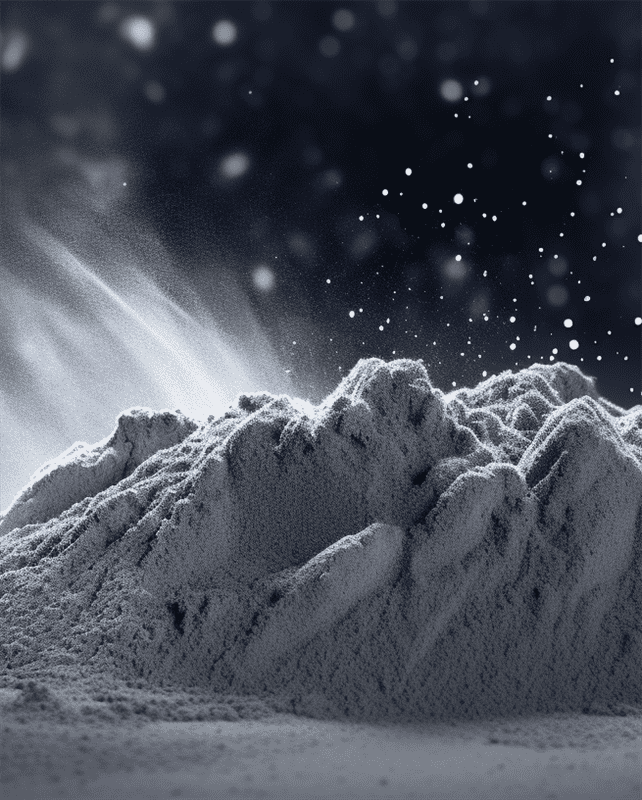
Applications and Uses of Tungsten Powder
Tungsten powder has diverse uses across the following major sectors:
Military and Defense
- Tungsten alloys in kinetic energy penetrators, armor-piercing ammunition, weights in missiles and rockets
- Tungsten carbide balls and darts in anti-tank ammunition
- Radiation shielding in nuclear reactors
Automotive
- Tungsten filaments in light bulbs and lamps
- Contact points and electrical components withstanding arcing
- Tungsten carbide ball bearings and other wear-resistant parts
- Tungsten alloys for engine components like valves and turbochargers
- Counterweights and vibrational damping components
Manufacturing
- Cutting tools, dies, punches made with tungsten carbide
- Tungsten electrodes for welding
- Added to steel to make high-speed tool steels
- Components for electrical contacts and resistance heating
- Metal evaporation boats and crucibles
Electronics
- Heat sinks and thermal management components for semiconductors
- Vapor deposition boats and heating elements
- Field emission tips, electron emitters, and cathodes
- Contacts, connectors, and lead wires
- Radiation shielding
Healthcare
- Dense tungsten alloy collimators, filters, and shielding for X-ray machines and cancer radiation treatments
- Tungsten powder mixed with polymers for making dense composites for radiation shielding
- Ballast weights for medical equipment
- Components for medical implants like stents and bone screws
Other Applications
- Tungsten alloy counterweights for applications like golf clubs, yacht keels, helicopter rotor blades
- Weights for sports equipment like darts, bowling balls, golf club heads
- Fishing lures, diving lures
- Jewelry components
- Ballast in motorsport vehicles
Types of Tungsten Powder
Tungsten powder is available in different grades classified based on particle size, shape, purity levels, powder density, and intended applications:
Type | Description |
---|---|
Ultrafine | Particle sizes under 1 micron, high surface area, used in chemical processes |
Submicron | 1-5 microns, spherical morphology, high purity, used in cemented tungsten carbide |
Fine | 1-10 microns, high densification, for tungsten mill products |
Medium | 10-40 microns, moderate surface area, general use in powder metallurgy |
Coarse | 40-150 microns, low surface area, used in weights |
Pure | 99.9%-99.99% tungsten, low impurity levels, bright silver-gray |
Commercial | 97%-99% tungsten, contains minor impurities, grayish or brownish |
Shaped | Flakes, needles, dendrites, or custom shapes, special applications |
Tungsten Powder Specifications
Tungsten powder for industrial uses needs to meet a range of physical, chemical, and morphological specifications as per international standards like ISO, ASTM, DIN, JIS, GB, and GOST:
Parameter | Typical Specifications |
---|---|
Particle size | 1 – 150 microns |
Powder shape | Spherical, irregular, flaky |
Apparent density | 2 – 3 g/cm3 for unsintered powder |
Tap density | 4 – 6 g/cm3 for unsintered powder |
Purity | 99% to 99.995% tungsten |
Oxygen content | <100 – 1000 ppm |
Carbon content | <100 – 500 ppm |
Heavy metal impurities | Parts per million limits for each element |
Surface area | 0.5 – 15 m2/g for powder |
Color | Bright silver-gray to brownish-gray |
Powder flow rates | Hall flowmeter testing |
The optimal powder characteristics like particle size distribution, morphology, apparent density, and tap density depend on the press and sinter requirements for the final component. Custom tungsten powder blends are formulated to meet the needs of each application.
Design and Engineering Standards
Tungsten powder metallurgy components are designed as per various international standards governing composition, manufacture, quality control testing, and applications:
Standard | Details |
---|---|
ASTM B777 | Standard specification for tungsten base, high-density alloys |
ISO 13320 | Specification for hardmetals – Metal powder briquettes |
MIL-T-21014 | Military specification for tungsten and tungsten alloy mill products |
SAE-AMS-T-21014 | Aerospace material specification for tungsten mill shapes |
GB/T 13383-2008 | Chinese standard for tungsten rod and bar |
JIS C 2805 | Japanese industrial standard for tungsten mill products |
DIN 2240 | German standard for heavy metal mill products |
Component and powder manufacturers ensure compliance with applicable standards for chemistry, microstructure, mechanical properties, non-destructive testing, quality assurance, and more.
Manufacturing and Production
Tungsten metal powder is primarily produced by the hydrogen reduction of tungsten oxides:
Tungsten oxide powder + Hydrogen → Tungsten powder + Water vapor
This is an exothermic process performed at 700-1000°C in a hydrogen atmosphere inside specialized reduction furnaces.
The key steps in tungsten powder production are:
- Mining and extraction – Tungsten ores like wolframite and scheelite are mined, crushed, milled, and concentrated through froth flotation to produce ammonium paratungstate (APT).
- Conversion to oxides – APT is thermally decomposed to tungsten trioxide (WO3) which is milled into a fine yellow/brown powder.
- Hydrogen reduction – WO3 powder undergoes reduction with dry hydrogen gas inside a pusher, belt or rotary furnace at temperatures up to 1000°C.
- Milling and classification – The reduced tungsten powder is milled in ball mills, classified into different particle sizes, and underwent further processing.
- Blending and compaction – Powders are blended, lubricated, compacted into ‘green’ preforms, and sintered into finished components.
High-purity grades may undergo additional hydrogen or vacuum degassing to lower impurity levels. Shaped and surface treated powders are made using specialized techniques. The powder morphology, size distribution, purity, and chemistry are tightly controlled to meet the needs of each application.
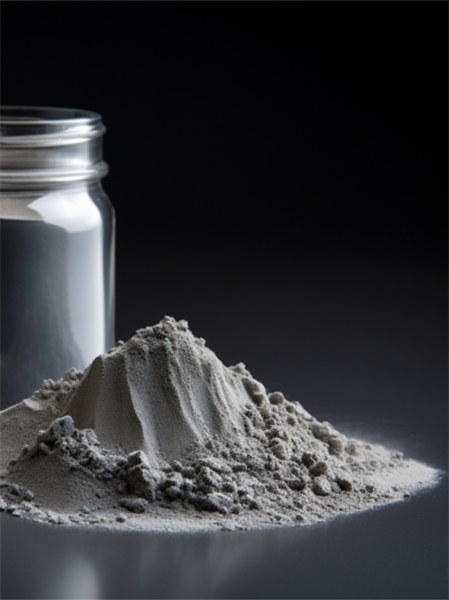
Suppliers and Pricing
Some leading global suppliers of tungsten powder include:
Company | Location |
---|---|
Buffalo Tungsten | USA |
Midwest Tungsten | USA |
TaeguTec | South Korea |
Wolfram | Austria |
HC Starck | Germany |
Xiamen Tungsten | China |
JX Nippon Mining | Japan |
Tungsten powder pricing depends on factors like:
- Purity – Ranges from US$50/kg for 97% tungsten to over $1000/kg for 99.995% ultrafine powders
- Particle size – Ultrafine under US$100/kg, micron-sized powder US$30-60/kg, coarse grades cheaper
- Quantity – Prices lower for bulk quantities in tons
- Powder properties – Spherical and high-density preferred for pressing cost more
- Product consistency – Established global brands command higher pricing
Price Ranges:
- Low-end: $30-$50 per kg
- Medium-grade: $50-$150 per kg
- High purity/performance: $150-$1000 per kg
Contact leading suppliers for exact price quotations based on your specifications and purchase volumes.
How to Select Tungsten Powder Suppliers
Here are tips for choosing reliable tungsten powder manufacturers and suppliers:
- Review company credentials including years in business, reputation, and customers
- Ensure they can customize powder characteristics to meet your requirements
- Look for consistent quality, rigorous testing, and ISO 9001 certification
- Evaluate their production capacity and ability to scale up supply if needed
- Consider location and logistics for efficient delivery to your facilities
- Request samples to test powder quality before large-scale purchases
- Compare pricing from different suppliers for cost-effectiveness
- Ensure high product purity, reliability, and lot-to-lot consistency
- Check lead times and inventory availability to avoid stockouts
- Evaluate flexibility for small test orders or to accommodate urgent requests
- Consider value-added services like blending, chemical analysis, and custom packaging
Installation and Operation Guide
Storage and Handling
- Store tungsten powder in clean, dry, sealed containers away from moisture, sparks, and flames
- Use inert gas blanketing if storing for over 6 months
- Limit exposure to air to minimize oxidation
- Provide proper ventilation and dust collection systems
- Avoid contamination from dirt, oils, or other powder fines
- Handle using clean scoops and tools; wear PPE like masks, gloves, goggles
- Prevent accumulation of powder on surfaces to minimize dust explosion risks
Processing and Operation
- Lubricate the powder with stearates or waxes prior to compacting
- For pressing, use tool steel or tungsten carbide dies lubricated with zinc stearate
- Compact the powder using smooth strokes of the press at optimal pressure
- For sintering, use hydrogen or vacuum furnaces and controlled heating profiles
- Follow recommended sintering temperatures and times based on the powder grade
- Slowly cool sintered parts inside the furnace under inert atmosphere
- Additional steps like infiltrating, heat treatment, or HIP may be used as needed
- Observe safety precautions when handling powder and operating equipment
Maintenance
- Inspect powder containers and storage areas periodically for damage or leaks
- Clean powder spills immediately to prevent accumulation of fines
- Dispose spent tungsten powder and waste safely as hazardous industrial waste
- Clean powder press dies, punches, and other tooling regularly
- Lubricate and maintain presses per manufacturer instructions
- Follow recommended schedules for furnace maintenance and recalibration
Pros and Cons of Using Tungsten Powder
Advantages:
- Excellent high-temperature properties due to high melting point
- Wear and corrosion resistance for long component life
- Very high density lends heft and inertia
- Biocompatible and non-toxic when pure
- Good thermal and electrical conductivity
- Low thermal expansion coefficient
- Can be alloyed to optimize properties like hardness
- Powder metallurgy allows complex net-shape component fabrication
- Recyclable to recover tungsten
Disadvantages:
- Expensive compared to other metal powders
- Limited global supply and production concentrated in China
- Brittle unmodified, requires alloying or sintering
- Challenging to machine in fully sintered state
- High melting point makes fabrication energy-intensive
- Lower ductility and impact resistance versus steel
- Prone to oxidation at elevated temperatures
- Susceptible to contamination during processing
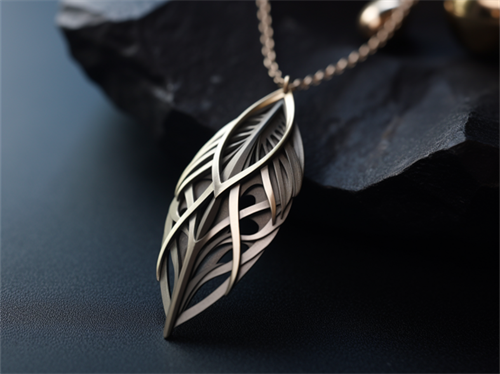
FAQ
Q: What are the different grades of tungsten powder available?
A: The main grades are classified based on particle size (ultrafine, fine, medium, coarse), purity (99.9% to 99.995%), powder shape (spherical, irregular, flaky), and end-use (general use, pressing, welding, etc.).
Q: What particle size is best for pressing and sintering?
A: A bimodal blend of finer (1-10 micron) and coarser (10-40 micron) powder is optimal, improving powder flow and green density. Ultrafine powder can also be used.
Q: What are the effects of impurities in tungsten powder?
A: Impurities like carbon, oxygen, copper, and iron can degrade properties. Ultra-high purity grades have lower impurities for demanding applications.
Q: How is tungsten powder compacted and sintered?
A: Powder is pressed into a green compact using high pressures in a die then sintered at temperatures near 2000°C under hydrogen or vacuum atmospheres.
Q: What alloying elements can be added to tungsten powder?
A: Tungsten is alloyed with elements like nickel, iron, cobalt, copper, and rhenium to enhance strength, ductility, and other properties.
Q: What are the recommended storage practices for tungsten powder?
A: Store in sealed containers in a clean, dry area protected from moisture and contamination. Limit air exposure. Use inert gas blanketing for long-term storage over 6 months.
Q: How is tungsten powder recycled and reused?
A: Scrap powder and solid tungsten can be recycled by crushing, grinding, blending, and re-compressing into new products. No degradation in properties occurs.
Q: What are the main applications for tungsten heavy alloys?
A: Military and defense components like kinetic energy penetrators, radiation shielding, counterweights, ballast weights, vibration damping in aerospace and automotive applications, etc.
Q: What are the advantages of using tungsten versus depleted uranium?
A: Tungsten is non-radioactive, safer to handle, less controversial, and easier to source than depleted uranium while offering similar density.