Titanium powder is a critical material for printing high-strength, lightweight titanium components using additive manufacturing techniques like selective laser melting (SLM) and electron beam melting (EBM). This guide provides a comprehensive overview of titanium powders for AM.
Introduction to Titanium Powder for AM
Titanium powder enables 3D printing of titanium parts with exceptional properties:
- High strength-to-weight ratio
- Excellent corrosion resistance
- Good high temperature properties
- Biocompatibility for medical uses
- Reactive and requires controlled processing
Common titanium alloys for AM:
- Ti-6Al-4V (Ti64)
- Ti-6Al-7Nb (Ti647)
- Ti-5Al-5Mo-5V-3Cr (Ti5553)
- Ti-6Al-2Sn-4Zr-2Mo (Ti-6-2-4-2)
Key powder characteristics:
- Chemistry and microstructure
- Particle size and distribution
- Particle shape and morphology
- Purity
- Flowability and apparent density
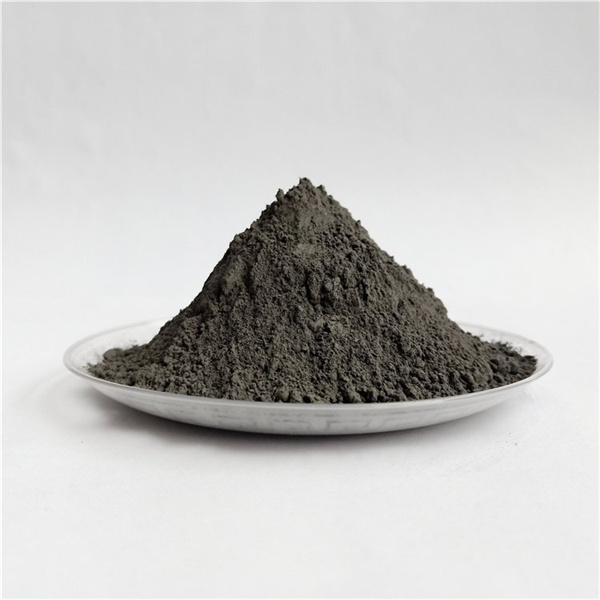
Ti-6Al-4V Powder
Ti-6Al-4V is the most common titanium alloy powder used in AM:
- Provides an excellent combination of strength, ductility and corrosion resistance
- Strength can reach 1300 MPa and higher for AM parts
- Melts around 1600°C and requires thermal management during printing
- Sensitive to oxygen pickup – requires controlled atmosphere
Applications:
- Aerospace and automotive components
- Biomedical implants like orthopedic knee and hip replacements
- Food and chemical processing industry parts
- Consumer products
Suppliers: AP&C, Tekna, Carpenter Additive, Arcam AB
Ti-6Al-7Nb Powder
Ti-6Al-7Nb powder provides superior tensile strength and creep resistance:
- High strength up to 1500 MPa from precipitation hardening
- Good weldability
- Used as an alternative to toxic vanadium-alloys
- Requires hot isostatic pressing (HIP) to minimize voids
Applications:
- Aerospace components like airframes and turbines
- Motorsport parts subjected to high stresses
- Dental implants and medical prosthetics
- Marine applications like ships and propellers
Suppliers: AP&C, TLS Technik GmbH, Tekna
Ti-5Al-5Mo-5V-3Cr Powder
Ti-5-5-5-3 powder offers excellent hardenability and deep hardening:
- Strength levels exceed 1400 MPa
- Retains properties at over 350°C
- Used for difficult-to-machine titanium parts
- Provides high fatigue resistance and creep strength
Applications:
- Aircraft landing gear and structural parts
- Formula-1 engine and chassis components
- Turbine engine discs and compressor parts
- Aerospace fasteners and hardware
Suppliers: AP&C, Carpenter Additive, Arcam AB
Ti-6Al-2Sn-4Zr-2Mo Powder
Ti-6-2-4-2 powder provides superior hot gas erosion resistance:
- Resists oxidation and corrosion up to 600°C
- Excellent strength up to 1300 MPa
- Used for parts subjected to high temperature gases
- Requires hot isostatic pressing to achieve full densities
Applications:
- Aircraft engine blades and vanes
- Rocket engine nozzles
- Missile components subjected to hot gas flows
- Nuclear reactors components
Suppliers: AP&C, Tekna, Sandvik Osprey
Grade 1 and Grade 2 Titanium
Grade 1 and 2 unalloyed titanium powders provide excellent corrosion resistance:
- High purity with low interstitial elements
- Excellent biocompatibility
- Low strength compared to alloys; about 380 MPa
- Used for chemical, marine and consumer applications
Applications:
- Biomedical implants like cranial plates
- Chemical reactor vessels and tubing
- Marine components like propeller shafts
- Food processing equipment
Suppliers: AP&C, TLS Technik, Tekna Plasma Systems
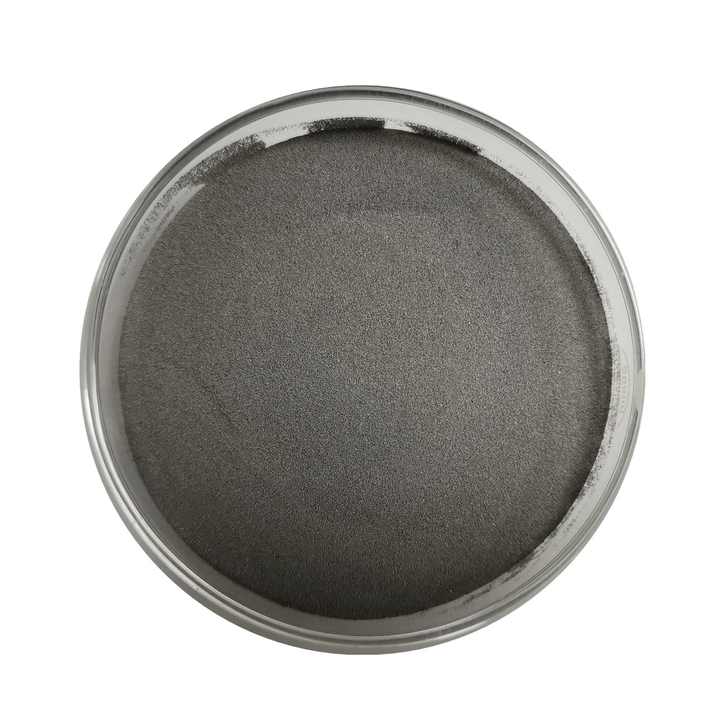
Titanium Aluminide Powders
Titanium aluminide alloys like Ti4522 print lightweight components:
- Low density – 3.7 g/cm3
- Strength up to 1000 MPa
- Excellent corrosion resistance
- High-temperature capability up to 750°C
- Challenging to process due to fast cooling and solidification
Applications:
- Aerospace compressor parts
- Automotive turbocharger wheels
- Combustion chamber liners
- Missile and aircraft structures
Suppliers: Kennametal, AP&C, Sandvik
Titanium Powder Production Methods
1. Gas Atomization
- Inert gas used to atomize molten metal into fine droplets
- Spherical powders ideal for AM, 10-100 microns
- High purity, can be pricey
2. Plasma Atomization
- Uses plasma gas to atomize molten metal
- Controlled particle shapes and sizes
- Lower oxygen pickup than gas atomization
3. Hydride-Dehydride (HDH)
- Crushed titanium hydride is dehydrided
- Irregular shapes, large particle sizes
- Lower cost, can have higher impurities
Technical Specifications
Typical titanium powder specifications for AM:
Parameter | Specification | Test Method |
---|---|---|
Particle size | 10 – 45 microns | ASTM B214 |
Apparent density | 2.2 – 4.5 g/cc | ASTM B212 |
Tap density | 3.5 – 5.5 g/cc | ASTM B527 |
Flow rate | 25 – 35 s/50g | ASTM B213 |
Oxygen content | < 0.20% | Inert gas fusion |
Nitrogen content | < 0.05% | Inert gas fusion |
Hydrogen content | < 0.015% | Inert gas fusion |
Morphology | Spheroidal | SEM imaging |
Controlling particle size distribution, shape, chemistry, and density is critical.
Handling and Storage of Titanium Powder
Special handling is needed to prevent oxidation and moisture pickup:
- Use stainless steel containers and transfer vessels
- Handle powder only in inert gas gloveboxes
- Use high purity argon atmosphere
- Avoid direct air and water exposure
- Ground all material handling equipment
- Maintain -10°C to 30°C storage temperatures
- Freeze powder bed when printer is idle to prevent oxygen absorption
Proper storage extends reuse life of titanium powder significantly.
Powder Sieving
Sieving is used to obtain a consistent particle size distribution:
Benefits
- Breaks up agglomerates
- Removes satellite particles
- Reduces likelihood of defects
- Improves powder flow and packing
Procedure
- Sieve powder through fine mesh around 20 microns
- Use rotational or vibratory sieving
- Perform under inert cover gas
- Document remaining powder weight percentage
High quality starting powder combined with sieving minimizes final part defects.
Suppliers and Pricing
Supplier | Grades | Price Range |
---|---|---|
AP&C | Ti64, Ti64 ELI, Ti5553 | $150 – $450/kg |
Carpenter Additive | Ti64, Ti5553, Ti64 ELI | $200 – $500/kg |
TLS Technik | Ti64, Ti4522, Ti54M | $250 – $600/kg |
Tekna | Ti64, Ti64 ELI, Ti45Nb | $180 – $480/kg |
- Grade 1 and Grade 2 unalloyed powders cost ~$150-250/kg
- Ti-6Al-4V and Ti-6Al-7Nb cost ~$250-450/kg
- Special alloys cost $500-650/kg
Prices depend on order volume, quality level, microstructure, and morphology.
Printer Installation and Commissioning
Installing a titanium AM printer requires:
- Thorough cleaning and leak checks
- Checking purity of argon systems
- Loading and testing the powder handling system
- Calibrating and leveling the build plate
- Integrating chiller, gas supply, sieving station
- Programming process parameters
- Printing test parts to validate quality
Vendors provide installation support to ensure ideal machine setup.
Best Practices for Printing
Printer operation:
- Maintain high purity argon levels
- Careful monitoring of melt pool and thermal behavior
- Validation of all critical dimensions
- Regular replacement of filters and consumables
- Monitoring of powder for reuse levels
Personnel safety:
- Use PPE like respirators when handling powder
- Avoid contact with fine titanium powder
- Proper disposal of used titanium powder
Part post-processing:
- Remove supports carefully from delicate parts
- Heat treatment tailored to alloy and application
- Hot isostatic pressing to improve densities
- CNC machining and finishing steps if required
Following vendor recommended procedures is critical to achieve defect-free printed parts in titanium alloys.
Maintenance and Inspection
Regular maintenance activities required:
Daily:
- Inspect optics for damage and deposits
- Monitor argon levels and oxygen sensors
- Check powder handling system seals and sensors
- Clean build chamber and sieve Powder residues
Weekly:
- Calibrate instrumentation and sensors
- Lubricate and inspect moving parts
- Inspect electrical terminals and grounding
Monthly:
- Perform leak tests on argon system
- Inspect safety devices and alarms
- Check filter status and replace if needed
- Monitor overall system health
Annual:
- Schedule preventive maintenance
- Replace consumables and optics
- Hardware inspection and upgrades
Proactive maintenance improves equipment reliability and lifespan.
Selecting a Titanium Printing System
Key selection criteria for a titanium 3D printing system:
1. Production Requirements
- Types of parts to be produced
- Material grade based on properties needed
- Production volumes required
- Accuracy and surface finish needs
2. Printer Specifications
- Alloys supported and optimized
- Build rate, precision, and repeatability
- Inert gas control and containment
- Automation features
- Size and capacity
3. Powder Handling System
- Integrated or standalone
- Sieving, storage and reuse capabilities
- Monitoring for oxygen and moisture
- Ease of operation and containment
4. Standards Compliance
- Industry standards like ASTM F2924
- Manufacturer quality certifications
- CE, FCC compliance
5. Supplier Credentials
- Specialized expertise in titanium AM
- Local application engineering support
- Operator training offered
- Maintenance and service contracts
Evaluating options based on these factors ensures selection of the ideal titanium additive manufacturing system meeting production needs.
Pros and Cons of Titanium AM
Advantages
- Excellent strength-to-weight ratio
- Corrosion resistance, biocompatibility
- Reduced parts, improved performance
- Quick turnaround of complex geometries
- Customized designs and batch production
- Reduces scrap compared to machining
- Consolidates assemblies into one part
Disadvantages
- High material and machine cost
- Additional post-processing steps
- Limitations on maximum part size
- Control of internal defects can be challenging
- Material properties can vary vs wrought
- Specialized expertise required
Troubleshooting Titanium AM Issues
Issue | Possible Causes | Corrective Actions |
---|---|---|
Porosity | Low purity argon atmosphere | Ensure argon levels above 99.99% purity |
Poor powder quality | Use high quality powder combined with sieving | |
Incorrect process parameters | Optimize parameters like power, speed, hatch spacing | |
Cracking | High residual stresses | Optimize thermal management, use preheating |
Brittle microstructure | Adjust scan strategy, use HIP | |
Contamination | Improve powder handling, ensure high argon purity | |
Surface Finish | Poor melt pool control | Adjust focus offsets, layer thickness, power |
Contaminated powder | Use fresh sieved titanium powder | |
Distortion | Uneven heating | Optimize scan patterns, use support structures |
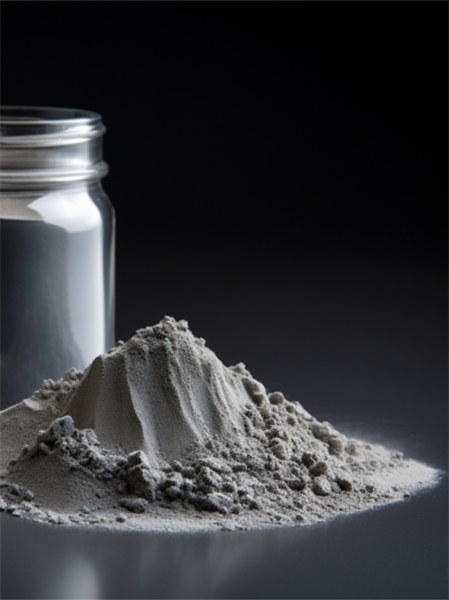
FAQs
Q: How is reactive titanium powder handled safely?
A: Using inert gas gloveboxes and hoppers, avoiding air exposure, and maintaining proper argon levels during printing.
Q: What particle size is used for titanium AM powder?
A: Typically 10-45 microns, with tighter control around 20-45 micron distribution.
Q: What post-processing methods are used?
A: Support removal, heat treatment, hot isostatic pressing, and finish machining/polishing.
Q: What contaminants affect titanium powder reuse?
A: Oxygen, nitrogen, hydrogen, and carbon pickup reduce reuse life. Strict handling procedures are required.
Q: How many times can titanium powder be reused?
A: Typically 20-100 prints depending on alloy, handling, and storage. Grade 23 titanium offers better reuse than Grade 5.
Q: What temperature is used for heat treating titanium AM parts?
A: Solution treatment is done 50-100°C below beta transus temperature, followed by aging and air/furnace cooling.
Q: What standards apply to titanium AM powder?
A: ASTM B801, ASTM F2924, ASTM F3001, ISO 23304 (in development).
Q: Why is hot isostatic pressing used?
A: HIP helps to close internal voids and achieve higher densities and improved mechanical properties.
Conclusion
Titanium powder enables printing of highly strong, lightweight titanium components for advanced aerospace, medical, automotive and industrial applications using AM techniques like SLM and EBM. With properties superior to conventional titanium, complex geometries can be manufactured quickly and efficiently. However, reactive powder handling, controlled process parameters, trained operators, and part qualification procedures are essential to achieve defect-free results. As expertise develops further, AM using titanium powder provides unprecedented capabilities to manufacture customized, high-performance titanium parts at reduced lead times.