Overview
Titanium Aluminum Alloys are a class of metallic materials that contain a mixture of titanium and aluminum. They are lightweight, have high strength, and excellent corrosion and oxidation resistance at high temperatures.
TiAl alloys are considered an important high-temperature structural material for aerospace and automotive applications due to their unique combination of properties. Their low density makes them lighter than nickel-based superalloys, while still retaining strength and stability at temperatures up to 750°C.
Key Properties of Titanium Aluminum Alloys
Property | Description |
---|---|
Density | 3.7 – 4.1 g/cm3, much lower than nickel alloys |
Strength | Retain high strength at temperatures up to 750°C |
Stiffness | High elastic modulus of about 160 GPa |
Ductility | Brittle at room temperature but becomes more ductile at high temperatures |
Corrosion Resistance | Excellent corrosion resistance due to presence of titanium |
Oxidation Resistance | Form protective oxide layer resulting in good oxidation resistance up to 750°C |
Cost | More expensive than titanium alloys but cheaper than nickel alloys |

Types of Titanium Aluminum Alloys
There are two primary types of titanium aluminum alloys:
Gamma TiAl Alloys
Gamma TiAl alloys have a lamellar microstructure and contain about 45-48% titanium, with the remainder aluminum. Small additions of elements like niobium, carbon, boron and chromium are also made to enhance properties.
The gamma phase TiAl alloys offer a good balance of low density, strength, ductility and oxidation resistance. They are the most widely used TiAl alloys.
Alpha-2 Ti3Al Alloys
Alpha-2 Ti3Al alloys contain about 25% aluminum and have a hexagonal crystal structure. They offer very high tensile strength but have lower ductility and fracture toughness compared to gamma TiAl alloys.
Alpha-2 alloys are typically used in very high temperature applications above 800°C such as in turbochargers.
Composition of Titanium Aluminum Alloys
Titanium aluminum alloys contain titanium as the major component, with aluminum and small amounts of other elements. Here is the typical composition range:
Alloy Element | Composition Range | Role |
---|---|---|
Titanium (Ti) | 52-56% | Primary base element |
Aluminum (Al) | 44-48% | Main alloying element with Ti |
Niobium (Nb) | Up to 2% | Increases strength and creep resistance |
Chromium (Cr) | Up to 2% | Increases oxidation resistance |
Boron (B) | Up to 0.2% | Improves ductility |
Carbon (C) | Up to 0.1% | Increases strength |
Silicon (Si) | 0.1-1% | Improves oxidation resistance |
Tungsten (W) | 0.1-1% | Refines grain size |
Molybdenum (Mo) | 0.1-1% | Increases strength |
The percentages of alloying elements are precisely controlled to achieve the right microstructure and properties in the alloy.
Key Properties of Titanium Aluminum Alloys
Titanium Aluminum Alloy Strength Properties
Property | Value | Description |
---|---|---|
Tensile Strength | 500 – 1100 MPa | Very high strength compared to titanium alloys |
Yield Strength (0.2% offset) | 400 – 1000 MPa | Measure of elastic strength in alloy |
Compressive Strength | 600 – 1500 MPa | Excellent compressive strength |
Creep Strength | 100 – 350 MPa | Ability to withstand loads at high temperatures |
Fracture Toughness | 15 – 35 MPa√m | Resistance to crack propagation is lower than nickel alloys |
Physical Properties
Property | Value |
---|---|
Density | 3.7 – 4.1 g/cm3 |
Melting Point | 1360°C – 1460°C |
Thermal Conductivity | 6 – 25 W/mK |
Electrical Resistivity | 150 – 250 μΩ.cm |
Coefficient of Thermal Expansion | 11 – 13 x 10<sup>-6</sup> /K |
Mechanical Properties at Room Temperature
Property | Value | Description |
---|---|---|
Hardness | 300 – 400 HV | Measure of resistance to indentation |
Young’s Modulus | 150 – 160 GPa | Measure of stiffness |
Shear Modulus | 60 – 65 GPa | Measure of rigidity |
Poisson’s Ratio | 0.25 – 0.34 | Ratio relating strain in directions perpendicular and parallel to applied load |
Machinability | Difficult | Challenging to machine compared to steels |
Applications and Uses of Titanium Aluminum Alloys
Titanium aluminum alloys are used in wide range of high performance engineering applications. Some key uses are:
Uses in Aerospace Industry
- Aircraft engine components like blades, discs, air inlet cowls
- Airframe and wing structures in high-speed aircraft
- Space vehicle parts due to combination of low weight and temperature resistance
Automotive Industry Uses
- Turbocharger turbine wheels and housings
- Connecting rods, valves, springs and fasteners in high performance engines
- Motorsport components like conrods and valves
Other Applications
- Gas turbine engine parts, power generation and marine applications
- Biomedical implants like artificial hip joints
- Sporting goods like bicycle frames, golf clubs
Here is a comparison of the use of titanium aluminum alloys versus alternatives:
Application | TiAl Alloys | Alternative Materials |
---|---|---|
Aircraft Engines | ✅ Excellent strength-to-weight ratio up to 750°C makes it suitable for blades, vanes, shafts | Nickel superalloys have higher temperature capability but are heavier |
Automotive Turbochargers | ✅ Good balance of high strength, temperature resistance and lower density than nickel alloys | Nickel alloys can withstand higher peak temperatures |
Airframes | ✅ 20-35% lighter than titanium alloys with equivalent strength for plane wings, tails and fuselage | Titanium alloys offer higher fracture toughness |
Biomedical Implants | ✅ Contains titanium which allows natural bonding to human bone | Stainless steel, cobalt chrome alloys also commonly used |
Industry Standards and Specifications
Some widely used industry standards for titanium aluminum alloys are:
Standard | Description |
---|---|
AMS 4928 | Standard specification for gamma titanium aluminide alloy sheet, strip and plate |
AMS 4965 | Standard for gamma titanium aluminide alloys processed by powder metallurgy |
AMS 4972 | Standard specification for alpha-beta or beta titanium aluminides bars, rods and wire |
ISO 21365 | Specification for structural gamma TiAl alloys |
ASTM B381 | Standard classification for titanium-aluminum-vanadium alloys for surgical implants |
Alloy products are offered in variety of grades that meet different standards for chemistry, microstructure, and mechanical properties.
Some common titanium aluminum grades are:
- Ti-48Al-2W-0.5Si (AMS 4928)
- Ti-47Al-2Cr-2Nb (ISO 21365 Grade 5)
- Ti-45Al-5Nb-0.2C-0.2B (AMS 4965 Grade 5)
Suppliers and Costs
Some leading global suppliers of titanium aluminum alloys include:
Supplier | Grades Offered | Production Methods |
---|---|---|
VSMPO | Ti-47Al-2Cr-2Nb<br>Ti-48Al-2Cr-2Nb-1Ta-0.7W | Investment casting<br>Forging |
ATI | Ti-48Al-2W-0.5Si<br>Ti-47Al-2Cr-2Nb | Precision casting<br>Powder metallurgy |
Precision Castparts Corp | Custom alloys | Investment casting |
Plansee | TiAl gamma alloys | Powder metallurgy |
Titanium aluminum alloys are more expensive than titanium alloys but cheaper than nickel-based superalloys. Some typical pricing estimates are:
Grade | Pricing Estimate |
---|---|
Ti-48Al-2Cr-2Nb | $85 – $125 per kg |
Ti-47Al-2W-0.5Si | $100 – $150 per kg |
Custom TiAl alloys | $150 – $250 per kg |
Pricing varies based on order volume, size specifications, certification requirements and other customizations.
Advantages and Limitations of Titanium Aluminum Alloys
Benefits and Advantages
- Very high specific strength – high strength-to-weight ratio
- Excellent strength retention up to 750°C
- Good environmental resistance – oxidation, burning and corrosion
- Lower cost than nickel and cobalt superalloys
- Some hot workability for forging, rolling
Shortcomings and Limitations
- Processing difficulties – hot working as well as machining
- Brittle behavior at room temperature
- Relatively low fracture toughness
- Maximum use temperature limited to 750°C
- Subject to hydrogen and moisture absorption
Here is a comparison of the advantages and disadvantages relative to alternatives:
Parameter | TiAl Alloys | Nickel Superalloys | Titanium Alloys |
---|---|---|---|
High Temperature Strength | Good up to 750°C | ✅ Excellent above 900°C | Poor above 500°C |
Density | ✅ Lowest | Higher | Comparable |
Oxidation Resistance | Good up to 750°C | ✅ Best above 800°C | Poor above 550°C |
Cost | ✅ Lower | Highest | Higher |
Workability | Poor | Good | ✅ Best |
Damage Tolerance | Poor | Good | ✅ Excellent |
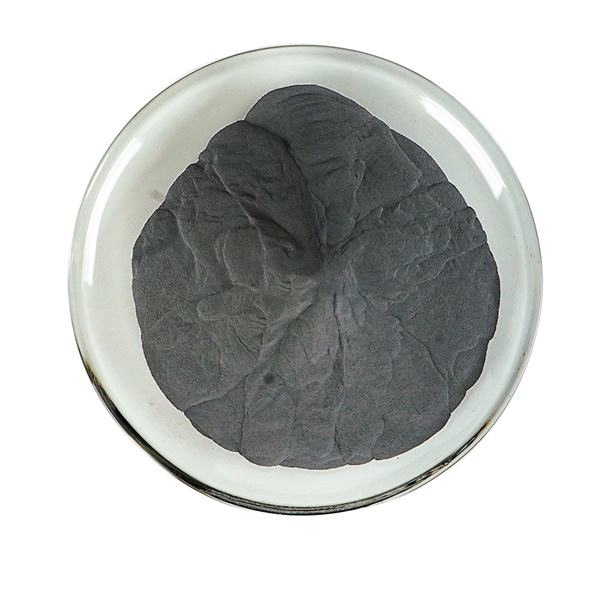
FAQs
Q: What are gamma titanium aluminides?
A: Gamma TiAl aluminides are intermetallic alloys containing titanium (Ti) and aluminum (Al) with a gamma (γ) phase crystal structure. They have an ordered lamellar arrangement of Ti and Al atoms. Gamma TiAl is the most commonly used alloy type.
Q: Why are TiAl alloys considered for aerospace applications?
A: TiAl alloys offer an excellent combination of low density and good mechanical properties up to 750°C. This allows lighter and more efficient aero-engine components to be designed using TiAl instead of much heavier nickel alloys.
Q: What are some examples of TiAl turbocharger components?
A: TiAl alloys are increasingly used to make turbocharger wheels and housings in high performance diesel and gasoline car engines. The low density and temperature resistance provide higher power density and efficiency.
Q: What are the main challenges in using TiAl alloys?
A: Difficulty in processing via casting, forging and machining along with intrinsic brittleness at room temperature, and lower damage tolerance than competing alloys creates barriers for adoption. However, processing methods and alloy development continue to advance.
Q: What is the typical oxygen content limit for TiAl alloys?
A: Oxygen is limited to less than 0.2% in TiAl alloys. Higher oxygen levels negatively impact ductility. Advanced melting and casting methods are used to control oxygen pickup.