Titanium Alloy Powder
All You Need To Know About 3D Printing Metal Powder Suppliers
Product Category
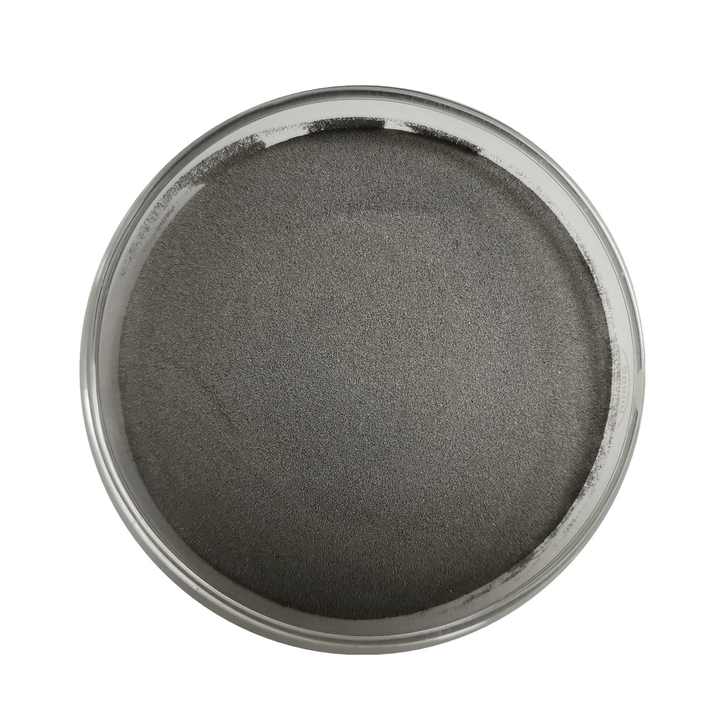
Titanium alloy powder is composed of titanium mixed with other metallic elements like aluminum, vanadium, iron, and molybdenum. The powders are made by gas atomization, a process that uses high-pressure gas to turn molten alloy into fine spherical particles ideal for additive manufacturing.
Titanium alloys offer the best strength-to-weight ratio of any metallic material. They are as strong as steel but 45% lighter. When produced as fine powders, titanium alloys become suitable feedstock for advanced manufacturing techniques like selective laser sintering (SLS), electron beam melting (EBM), and binder jetting. These methods allow intricate shapes and custom designs not possible with traditional fabrication.
Titanium and its alloys stand out for their corrosion resistance in harsh environments. They withstand saltwater, acids, and chlorine much better than aluminum, magnesium, or steel alloys. Titanium is also inert and non-toxic when implanted in the human body. This biocompatibility makes it invaluable for medical devices and implants.
With advanced properties like high strength, low density, corrosion resistance, and biocompatibility, titanium alloy powders enable lighter, stronger, longer-lasting parts across aerospace, automotive, medical, chemical, marine, and consumer industries.
Titanium Alloy Powder Composition
Titanium alloy powders contain primarily titanium along with alloying elements to improve strength, hardness, and high-temperature performance. The most common titanium alloys are Ti-6Al-4V, Ti-6Al-4V ELI, and Ti-3Al-2.5V.
Alloy | Composition |
---|---|
Ti-6Al-4V | 90% titanium, 6% aluminum, 4% vanadium |
Ti-6Al-4V ELI | 90% titanium, 6% aluminum, 4% vanadium, low interstitial impurities |
Ti-3Al-2.5V | 95% titanium, 3% aluminum, 2.5% vanadium |
Other alloying elements like iron, molybdenum, zirconium, tin, tantalum, or niobium may be present in small quantities. The composition is carefully controlled to achieve target properties after additive manufacturing.
Properties of Titanium Alloy Powder
The unique properties of titanium alloys in powder form enable advanced manufacturing, aerospace, medical, and other leading-edge applications.
Property | Ti-6Al-4V | Ti-6Al-4V ELI | Ti-3Al-2.5V |
---|---|---|---|
Density | 4.43 g/cm3 | 4.43 g/cm3 | 4.48 g/cm3 |
Melting Point | 1604°C | 1604°C | 1615°C |
Tensile Strength | Min 1170 MPa | Min 1100 MPa | Min 1095 MPa |
Yield Strength | Min 1035 MPa | Min 1035 MPa | Min 1000 MPa |
Elongation | 10-15% | 8-15% | 8-10% |
Elastic Modulus | 114 GPa | 114 GPa | 115 GPa |
Fatigue Strength | 485 MPa | 485 MPa | 450 MPa |
Fracture Toughness | 75 MPa-m^1/2 | 60 MPa-m^1/2 | 65 MPa-m^1/2 |
Thermal Conductivity | 7 W/m-K | 7 W/m-K | 6.7 W/m-K |
Electrical Resistivity | 170-190 μΩ-cm | 170-190 μΩ-cm | 172 μΩ-cm |
Coefficient of Thermal Expansion | 8.6 μm/m-°C | 8.6 μm/m-°C | 8.8 μm/m-°C |
The properties of printed parts depend on the additive manufacturing process as well as heat treatment after printing. For example, electron beam melting (EBM) generates finer microstructures and better mechanical properties compared to selective laser melting (SLM). Post-processing like hot isostatic pressing (HIP) can further enhance density, surface finish, dimensional accuracy, and material performance.
Applications of Titanium Alloy Powder
Some of the major application areas for titanium alloy powder include:
Industry | Applications |
---|---|
Aerospace | Engine components, airframe parts, fasteners, hydraulic systems |
Medical | Implants, surgical instruments, dental roots, braces |
Automotive | Connecting rods, valves, springs, fasteners, gears |
Chemical | Pumps, valves, pipes, heat exchangers, reaction vessels |
Oil and gas | Drill bits, completion tools, subsea components |
Power generation | Turbine blades, heat exchangers, steam and gas piping |
Sporting goods | Golf clubs, bicycle frames, hockey sticks, lacrosse sticks |
Consumer goods | Watches, glasses, jewelry, smartphones, cameras |
Titanium alloys enable lightweight, high-performance designs across industries where strength, corrosion resistance, and biocompatibility are critical. The flexibility of powder metallurgy allows production of complex, net-shape parts not possible with conventional titanium mill products.
Titanium Alloy Powder Specifications
Titanium alloy powders are available in different size ranges, compositions, production methods, and purity levels. Here are some of the key specification parameters:
Parameter | Typical Values |
---|---|
Particle size | 10-45 μm, 15-53 μm, 45-150 μm |
Particle shape | Spherical, irregular |
Production method | Gas atomization, plasma rotating electrode process, hydride-dehydride |
Purity | Grade 1, 2, 3, 4, 5 |
Alloy grade | Ti-6Al-4V, Ti-6Al-7Nb, Ti-555, Ti-1023, etc. |
Apparent density | 2.5-4.5 g/cm3 |
Tap density | Up to 80% of material density |
Oxygen content | 3000-5000 ppm |
Nitrogen content | 150-500 ppm |
Hydrogen content | 100-200 ppm |
Flow rate | Up to 25 s/50 g |
Specific surface area | 0.1-1.0 m2/g |
Specifications are based on ASTM B988 for gas atomized spherical titanium alloy powder and other international standards. Custom compositions and particle characteristics are also available for specialized applications.
Titanium Alloy Powder Pricing
Pricing for titanium alloy powder depends on many factors:
Factor | Impact on Price |
---|---|
Alloy composition | Higher alloying content increases cost |
Purity level | Higher purity grades are more expensive |
Particle size distribution | Smaller sizes are priced higher |
Production method | Plasma and HDH powders cost more than gas atomized |
Order quantity | Prices decrease with larger order quantities |
Packaging | Argon purged sealed cans add cost |
Some indicative price ranges:
- Ti-6Al-4V powder 15-45 μm: $50-80/lb
- Ti-6Al-4V powder 45-150 μm: $30-50/lb
- Small lots in sealed cans are ~30% higher
- Plasma Ti-6Al-4V powder: $120-150/lb
- Purity grade 1 powder: $200-300/lb
Contact reputable suppliers like AP&C, Tekna, and Advanced Powders for quoted pricing based on your specific requirements. Be wary of low-cost powders from unknown sources with questionable quality.
Comparison of Titanium Powder Production Methods
Comparison of Titanium Powder Production Methods
Method | Gas Atomization | Plasma Atomization |
---|---|---|
Description | Alloy melted in vacuum chamber, impinged by high-velocity inert gas jets to make powder | Alloy melted using plasma arc torch, steam of ultrafine droplets rapidly solidified into powder |
Particle Size | 15-150 microns | 5-45 microns |
Particle Shape | Irregular spheroids | Very spherical |
Oxygen Pickup | Moderate | Low |
Cost | Lower | Higher |
Scalability | Higher capacity | Small batches |
Typical Applications | Most additive manufacturing | Aerospace, medical |
Gas atomization is the standard production method used by major titanium powder suppliers. Plasma atomization creates finer, more spherical powders but has higher cost and lower output.
Frequently Asked Questions
Q: What are the main advantages of using titanium alloy powder?
A: The main advantages are excellent strength-to-weight ratio, corrosion resistance, bio-compatibility, design flexibility, ability to produce complex net shape parts, and performance at high temperatures.
Q: What industries use titanium alloy powder the most?
A: Aerospace, medical, automotive, chemical processing, oil and gas, sporting goods, and power generation are leading users of titanium powder for advanced components.
Q: What are some examples of titanium alloy powder applications?
A: Specific applications include aircraft engine and airframe parts, biomedical implants and instruments, automotive valves and connecting rods, chemical processing equipment, golf clubs, watches, and bicycles.
Q: What alloy compositions are commonly used with titanium powder?
A: Popular alloys include Ti-6Al-4V, Ti-6Al-7Nb, Ti-555, Ti-1023, and commercially pure titanium grades 1 through 4. Exact composition is tailored to meet property and processing requirements.
Q: What manufacturing processes use titanium alloy powder as feedstock?
A: The main processes are metal injection molding (MIM), laser powder bed fusion (L-PBF), electron beam powder bed fusion (EB-PBF), and directed energy deposition (DED).
Q: How are the properties of powder metallurgy titanium alloys compared to wrought and cast titanium?
A: With optimal processing, powder metallurgy titanium parts can achieve mechanical properties on par and sometimes superior to cast or wrought products. However, property anisotropy and defects require close control and qualification.
Q: What are some of the key specifications for titanium alloy powder?
A: Important characteristics include particle size distribution, particle shape, apparent density, tap density, flow rate, alloy composition, oxygen/nitrogen/hydrogen content, specific surface area, and powder production method.
Q: What precautions are required when handling titanium alloy powder?
A: An inert atmosphere, avoiding ignition sources, grounding equipment, minimizing dust generation, and wearing PPE are essential to handle reactive titanium powder safely. Strict procedures are needed to prevent contamination or changes to powder characteristics.
Wholesale Price: $20/Kg-$300/Kg
Showing all 12 results
-
TiNb Alloy Powder
-
TiNbZrSn Alloy Powder
-
Ti6Al4V Powder
-
CPTi Powder
-
TC18 Powder : Unlocking the Power of Titanium Carbide
-
TC11 Powder : A Comprehensive Guide
-
TC4 ELI Powder
-
Best Ti-6Al-4V powder (TC4 Powder)for additive manufacturing
-
Titanium and aluminum TA7 powder
-
Pure Titanium Powder
-
Ti-6Al-4V Titanium Alloy Powder
-
PREP Refractory Titanium Alloy Powder
FAQ About 3D Printing Metal Powder
How can I contact Metal3DP customer service?
We provide 24/7 customer support. You can find our contact details on the Contact Us page, including phone, email, and online chat.
What metal powder materials does Metal3DP offer?
We offer various high-quality metal powders including stainless steel, high-temperature alloys, suitable for processes like laser and electron beam powder bed fusion.
How does Metal3DP ensure the quality of 3D printing metal powder?
With extensive metal additive manufacturing expertise, we employ advanced processes and stringent quality control to ensure the mechanical properties and surface quality of parts.
In which industries are Metal3DP's 3D printing devices applied?
Our devices have a wide range of applications in industries like aerospace, medical, automotive, and more, providing solutions for high-performance metal components in manufacturing.
Does Metal3DP offer custom alloy options?
Yes, we provide custom alloy services to meet specific material requirements from clients.
What are the advantages of Metal3DP's SEBM systems?
Our SEBM systems excel in producing complex metal parts with exceptional mechanical properties. Key features include industry-leading build volume, precision, and reliability.
Can I find application cases on the Metal3DP website?
Yes, our website showcases a wide range of application cases demonstrating successful implementations of Metal3DP technology across various industries.
How can I start collaborating with Metal3DP?
Get in touch with us, and our team will provide you with tailored solutions and collaboration plans based on your needs.
What is the turnaround time for Metal3DP's custom services?
The turnaround time for custom services varies depending on project complexity. We will provide accurate delivery times based on your requirements.
What 3D printing technologies does Metal3DP offer?
We specialize in Selective Laser Sintering (SLS), Selective Laser Melting (SLM), and Selective Electron Beam Melting (SEBM) among other 3D printing technologies.
SEND US
Ask For Other Question?
If you cannot find the answer to your question in our FAQ, you can always leave us a message. We will answer to you shortly.
WAIT FOR US
Next step
01. We will prepare a proposal
Required scope, timeline and APR. Price will be included if you provide us with detail information about a project.
02. Discuss it together
Let’s get acquainted and discuss all the possible variants and options
03. Let’s start building
When the contract is signed, and all goals are set, we can start the first sprint.