ta15 powder equipment plays a critical role in many industrial processes. This comprehensive guide provides detailed information on different types of ta15 powder equipment, key specifications, applications, installation and maintenance procedures, suppliers, costs and more.
Overview of ta15 powder Equipment
ta15 powder equipment refers to machines and systems used for handling or processing ta15 powder. Here is a quick overview:
- Purpose – Used for conveying, mixing, separating, dosing, heating, reacting, pelletizing, compacting, coating ta15 powder materials.
- Types – Conveyors, mixers, separators, feeders, dryers, reactors, pelletizers, compactors, coaters.
- Sizes – From small lab-scale equipment to large industrial-scale units.
- Materials – Stainless steel, carbon steel, aluminum, plastics, ceramics.
- Drives – Electric motors, hydraulic systems, pneumatic power.
- Automation – Manual, semi-automatic, fully automatic PLC/DCS controlled.
- Applications – Chemicals, pharmaceuticals, plastics, food, minerals processing, metals, nuclear, defense.
- Suppliers – OEMs like Hosokawa Micron, Fitzpatrick, Alexanderwerk, etc. Or customized fabricators.
- Costs – $$ to $$$$ depending on capacity and level of automation.
Now let’s look at the different types of ta15 powder equipment in detail:
Types of ta15 powder Equipment
Equipment | Description | Applications |
---|---|---|
Belt conveyors | Continuous conveying using rubber or fabric belts | Transport over long distances; connecting processes |
Bucket elevators | Vertical conveying using bucket attached to chain/belt | Vertical lifting; loading/unloading |
Screw conveyors | Enclosed conveying using rotating spiral screw | Horizontal, inclined or vertical transport; feeding to process machines |
Vibrating conveyors | Trough/tube with vibrating drive | Quick flow control; useful for fragile materials |
Pneumatic conveyors | Using air flow through pipe to move material | Flexible transfer; can go long distances |
Cyclones | Conical vessel creates vortex to separate particles | Dust removal; product classification |
Air classifiers | Separation of fines from coarse using airflow | Grading powders; removal of fines |
Screeners | Sieving powders using meshed screens | Particle sizing; removal of oversize particles |
Magnetic separators | Remove magnetic particles from non-magnetic | Protection of equipment; product purification |
Mixers | Blending of powders with uniformity | Homogenous mixes for improved processing |
Reaction vessels | Enclosed vessels with agitator for chemical reactions | Polymerization, catalysis, crystallization, etc. |
Dryers | Remove moisture from powders using heat | Improve flow; prevent caking/sticking |
Pelletizers | Form pellets by agglomerating particles | Improve handling; make free-flowing product |
Briquetters | Compact powder into high density briquettes | Create concentrated product; improve logistics |
Coaters | Apply liquid coating to pellets/tablets | Create controlled release; mask taste, color |

ta15 powder Equipment Characteristics
Here are some key characteristics and design parameters to consider when selecting ta15 powder equipment:
- Capacity – Batch size or throughput rate needed.
- Particle properties – Size, shape, density, abrasiveness.
- Temperature – Maximum temperature the equipment needs to handle.
- Chemical compatibility – Ensure all wetted parts are resistant to the chemicals used.
- Drives – Consider speed, load, torque, efficiency requirements.
- Containment – Level of contamination control needed – open, enclosed, glovebox etc.
- Cleaning – Easy to dismantle equipment for fast changeovers and cleaning.
- Automation – Degree of manual vs automatic operation required.
- Maintenance -Frequency and complexity of routine maintenance tasks.
- Standards compliance – Where necessary conform to hygiene, electrical, pressure vessel standards.
- Flexibility – Ability to handle a range of products orrecipes if needed.
ta15 powder Equipment Applications
ta15 powder equipment finds use across many industries. Here are some typical applications:
Industry | Equipment Used | Purpose |
---|---|---|
Chemicals | Dryers, conveyors, reactors, mixers | Production of catalysts, battery materials, pigments |
Pharmaceuticals | Mills, dryers, pelletizers, coaters | Processing APIs, excipients; making tablets, capsules |
Food | Conveyors, cyclones, classifiers | Handling grains, flour, spices, confectionery |
Plastics | Screeners, separators, conveyors | preparing resins, compounding, molding |
Nuclear | Gloveboxes, manipulators | Handling radioactive powders |
Cement | Bucket elevators, screeners | Raw meal grinding, product classification |
Minerals | Flotation cells, classifiers | Ore processing and concentration |
ta15 powder Equipment Specifications
Here are some typical specifications of ta15 powder processing equipment that buyers should look for:
Parameter | Typical Specifications |
---|---|
Production capacity | 1 kg/h to 50 TPH |
Maximum particle size | 5 mm to 300 mm |
Batch sizes | 0.1 liters to 10,000 liters |
Temperature range | -10°C to +1200°C |
Pressure rating | Vacuum to 30 barg |
Moisture handling | 1% to 25% moisture content |
Power consumption | 1 kW to 1500 kW motors |
Voltage | Up to 690V AC as required |
Frequency | 50/60 Hz |
Plant air pressure | 4 – 10 bar |
Material of construction | SS 304/316, MS, Hastelloy, nickel |
Drive types | Geared motor, variable frequency |
Containment | ISO 5 to ISO 8 |
Automation | PLC, DCS, SCADA |
Compliance | ATEX, ASME, OSHA, FDA |
Buyers should engage with suppliers to get equipment customized to their specific process requirements.
ta15 powder Equipment Design Considerations
Here are some important factors to consider in the design of ta15 powder handling systems:
- Ergonomics – Operator accessibility and visibility for manual loading/unloading. Platforms, stairs, railings.
- Containment – Minimizing dust leaks. Seals, gaskets, fume extractors.
- Cleaning – Easy dismantling, no crevices. Avoiding cross-contamination.
- Material flow – Optimizing powder conveying trajectories, angles, transitions. Removing bottlenecks.
- Services – Required utilities like cooling water, steam, power. Location of pipes, ducts, cables.
- Control – Local and/or remote monitoring and control. Analog vs digital systems.
- Automation – Level feasible from manual to fully automatic. Cost vs benefit.
- Safety – Preventing accidents and explosions. Compliance to codes.
- Validation – Installation Qualification (IQ), Operational Qualification (OQ), Performance Qualification (PQ).
- Standards – CE marking, electrical area classification, hygienic design.
- Flexibility – Ability to handle a variety of products. Modular vs dedicated design.
ta15 powder Equipment Installation Guidelines
Correct installation of ta15 powder equipment is crucial for proper functioning. Here are some key guidelines:
- Carefully unload all components using appropriate lifting gear – cranes, jacks, slings.
- Position on flat, level surface and grout or epoxy coat as required.
- Ensure correct alignment with other equipment and proper Tramp Metal removal.
- Fasten all anchor bolts and grout as needed for stability.
- Make all service connections – electrical, piping, ducting.
- Check direction of rotation of rotating equipment. Install belt guards.
- Lubricate all moving parts – bearings, motors.
- Verify that instrumentation is calibrated and functioning.
- Test all safety switches and interlocks. Install all guards.
- Check for free movement of actuators. Set limit switches and actuator stops.
- Confirm that control system is wired properly and all I/Os functioning.
- Check correct rotation of fans, blowers – modify ducts if needed.
- Verify rated flows for air handling systems. Measure power consumption.
- Commission equipment as per Manufacturer’s Instructions. Get service contract if needed.
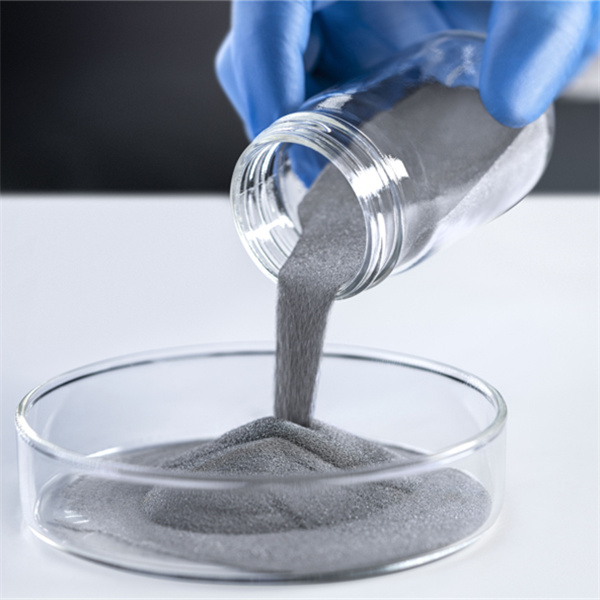
ta15 powder Equipment Operation
Here are some key steps and tips for proper operation of ta15 powder equipment:
- Carry out daily visual inspection of equipment – check for any damage, leaks, wear.
- Monitor pressure gauges, flow meters, amp meters during operation.
- Take frequent product samples and analyze for proper functioning.
- Listen for any abnormal noise from drives, bearings – investigate immediately.
- Measure vibration on critical equipment like motors regularly.
- Keep adequate spares for wear parts – seals, screens, belts. Plan maintenance downtime.
- Follow SOPs for startup, shutdown, changeovers, emergency response.
- Ensure operators are adequately trained and follow all safety procedures. Employ lock out/tag out system.
- Maintain logs for production, quality, breakdowns, maintenance. Track KPIs.
- Audit equipment efficacy periodically. Make upgrades to components if needed.
ta15 powder Equipment Maintenance
Routine maintenance is essential for reliable functioning of ta15 powder equipment. Key aspects:
Preventive Maintenance
- Inspections – daily checks for leaks, damage, loose parts
- Lubrication – follow schedule to grease bearings, gears
- Component servicing – belts, liners, seals
- Drive servicing – shafts, motors, gearboxes
- Instrument calibration – weigh feeders, transmitters
- Safety checks – interlocks, alarms, grounding
Breakdown Maintenance
- Troubleshooting guide to isolate root cause
- Spares inventory management to cut downtimes
- Train technicians on equipment repair procedures
- Standard Operating Procedures (SOPs) for each maintenance task
Shutdown Maintenance
- Annual equipment overhaul during plant shutdown
- Dismantling and inspection of all parts
- Replacement of worn components – liners, seals, screens
- Refurbishing drives, gearboxes, motors
Turnaround Maintenance
- Major restoration activities once in 5-10 years
- Refractory relining, pressure vessel recertification
- Repairs to structural supports, access platforms
Proper maintenance planning reduces risks of prolonged downtime and production losses.
Choosing the Right ta15 powder Equipment Supplier
Choosing the right supplier is key to getting high-performing ta15 powder equipment. Below are important factors to consider:
Technology
- Specialized expertise in ta15 powder handling technology
- Extensive experience across different applications
- In-house R&D and pilot plant testing capabilities
Quality
- Use of high-grade materials resistant to wear, corrosion
- Stringent quality control in manufacturing processes
- Well-designed components for reliability and life
Range
- Capability to supply integrated systems with multiple equipment types
- Scalability from lab to full production scale
- Modular and customized equipment design offered
Services
- Technical support for selecting right equipment
- Installation and commissioning assistance
- Operator training and maintenance support
- Readily available spare parts supply
Compliance
- Products certified to international standards
- Manufacturing facilities with ISO 9001 quality certification
- Equipment compliant to applicable codes and regulations
Cost
- Competitive pricing on equipment and spares
- Value for money based on total life cycle costs
Buyers should evaluate different suppliers based on these parameters before selecting one with the right expertise, technology and value proposition.
ta15 powder Equipment Costs
The cost of ta15 powder equipment varies significantly depending on:
- Type and capacity
- Level of customization
- Materials of construction
- Automation features
- Additional accessories
Here is an indicative price range for different types of equipment:
Equipment | Indicative Price Range |
---|---|
Conveyors | $2,000 to $100,000 |
Elevators | $5,000 to $50,000 |
Feeders | $1,000 to $20,000 |
Mixers | $5,000 to $100,000 |
Dryers | $10,000 to $500,000 |
Mills | $5,000 to $250,000 |
Granulators | $2,000 to $50,000 |
Briquetters | $5,000 to $200,000 |
Pelletizers | $10,000 to $300,000 |
Classifiers | $1,000 to $50,000 |
Buyers are recommended to get quotes specific to their capacity needs from shortlisted suppliers to arrive at a realistic budget estimate. Expect higher costs for highly customized or corrosive chemical/radioactive service.
ta15 powder Equipment Comparison
Here is a brief comparison of different types of commonly used ta15 powder equipment:
Parameter | Screw Conveyor | Pneumatic Conveyor | Ribbon Blender | Ball Mill | Fluid Bed Dryer |
---|---|---|---|---|---|
Principle | Enclosed rotating screw to push powder horizontally or at an incline | Using air flow to pneumatically convey powder through pipes | Double helical ribbons that rotate and blend powder | Rotating chamber with grinding media that creates particle size reduction | Hot air passes through perforated bed plate where powder is fluidized |
Typical capacity | 1 – 100 m3/hr | 0.5 – 50 m3/hr | 50 – 6000 L | 1 – 50 kg/hr | 10 kg/hr – 10 TPH |
Pros | Low cost, simple, gentle handling | Flexible, encloses powder | Fast and homogeneous mixing | Grinds down to micron sizes | Good heat transfer, suited for heat sensitive materials |
Cons | Limited conveying distance | Dilution of powder with air | Limited capacity | Batch process, can be slow | Relatively high operating costs |
Typical applications | Feeding from bag dump stations | Loading/unloading vessels | Mixing food ingredients | Grinding minerals, medicines | Drying chemicals, pharma products |
So in summary, screw conveyors are simple and inexpensive but capacity over long distances is limited. Pneumatic conveyors are flexible but dilute the product. Ribbon blenders provide quick blending but at smaller batches. Ball mills are ideal for fine grinding but slow. Fluid bed dryers efficiently dry powder but operating costs are high.
Understanding these key differences allows selection of the most suitable equipment based on specific powder handling requirements.
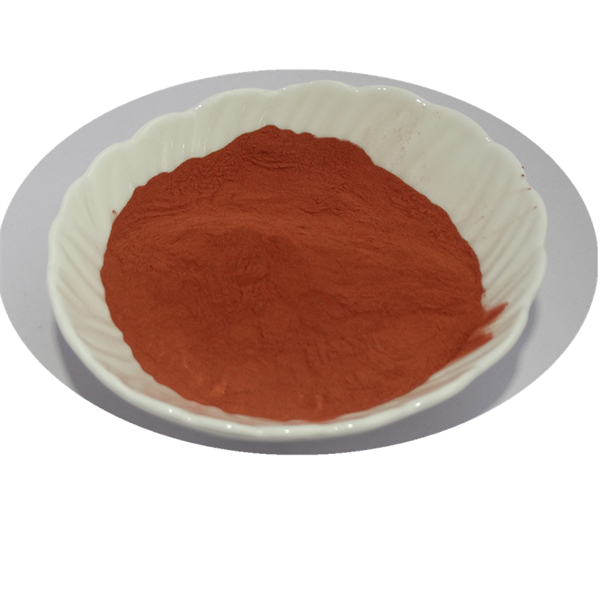
ta15 powder Equipment – Advantages and Limitations
ta15 powder equipment delivers important functionality for industrial processes. However, each type has its own pros and cons that must be evaluated.
Advantages
- Precision – Advanced designs for highly accurate feeding, mixing, drying, reacting, milling, pelletizing etc.
- Productivity – Continuous processing, consistent results and higher throughputs.
- Automation – Reduced manual intervention through use of instrumented and automated systems.
- Reliability – Robust designs with high availability and long service life.
- Safety – Reduced risks by minimizing operator exposure and dust handling.
- Cost efficiency – Lower operating costs through efficient continuous processing.
- Versatility – Various customizations possible for range of powders and capacities.
- Confinement – Minimized powder leakage to environment for contained processes.
Limitations
- High capital cost – Significant upfront investment for equipment purchase and installation.
- Complexity – Specialized skill needed for selection, operation and maintenance.
- Inflexibility – Dedicated equipment with limited ability to handle other materials.
- Process understanding needed – Operating parameters must be well defined based on powder properties and chemistry.
- Maintenance requirements – Regular preventive maintenance needed for consistent functioning.
- Customization constraints – Limitations in tailoring standardized equipment for specific requirements.
- Utilities – May require uninterrupted supply of utilities – electricity, water, air, fuel.
- Fixed capacity – Hard to accommodate large demand fluctuations.
- Space needs – Larger footprint than batch systems. Layout must allow maintenance access.
In summary, ta15 powder equipment enable continuous and reliable processing but require significant capital investment and maintenance efforts. The advantages must be balanced against limitations based on application-specific needs.
FAQ
Q: What are the most common types of ta15 powder equipment used in industry?
A: The most common types are conveyors (screw, belt, pneumatic), separators (air classifier, sifter, cyclone), size reduction machines (grinding mill, crusher), dryers (tray, rotary, flash), and reactors (continuous, batch).
Q: Should I buy new or used ta15 powder equipment?
A: New equipment ensures latest technology, customized features, warranty/guarantee, technical support. Used equipment costs less but may require repairs, upgrades and lacks support. Evaluate based on application criticality.
Q: How to select capacity of ta15 powder equipment?
A: Consider current demand, expected growth, process parameters, batch sizes. It’s recommended to size the equipment with a reasonable buffer for increased future demand. Oversizing also affects efficiency and operating costs.