Stainless steel 316L powder is a popular material choice for many applications due to its excellent corrosion resistance, mechanical properties, and biocompatibility. This guide provides a detailed overview of 316L powder, including its properties, production methods, applications, suppliers, and more.
Overview of Stainless Steel 316L Powder
Stainless steel 316L powder is a type of stainless steel alloy that contains molybdenum for enhanced corrosion resistance. The “L” refers to the low carbon content, which improves weldability.
Some key properties and characteristics of 316L powder include:
- Excellent corrosion resistance, especially against pitting and crevice corrosion
- High strength and good ductility
- Outstanding biocompatibility and suitable for medical implants
- Non-magnetic austenitic structure
- High oxidation and creep resistance at elevated temperatures
- Available in various particle sizes and morphologies
316L powder can be produced through gas atomization, water atomization, and other methods. The powder production process influences the powder characteristics like particle shape, size distribution, flowability, and more.
Here is a comparison of different 316L powder types and their typical applications:
Powder Type | Particle Size | Morphology | Applications |
---|---|---|---|
Gas atomized | 15-150 μm | Spherical | Additive manufacturing, MIM |
Water atomized | 10-300 μm | Irregular, dendritic | Metal injection molding |
Plasma atomized | <100 μm | Spherical | Additive manufacturing |
Electrolytic | <150 μm | Dendritic, spiky | Additive manufacturing, pressing |
Carbonyl | <10 μm | Spherical | Powder metallurgy, pressing |
316L powder is valued for its combination of strength, corrosion resistance, and biocompatibility. Some of the major applications include:
- Additive manufacturing – Selective laser melting, direct metal laser sintering, binder jetting
- Metal injection molding – Small, complex parts like orthopedic implants
- Press and sinter – Filters, porous structures, self-lubricating bearings
- Surface coating – To improve wear and corrosion resistance
- Brazing and welding – As filler material
Here is an overview of how 316L powder is used in different manufacturing processes:
Manufacturing Process | How 316L Powder is Used |
---|---|
Additive manufacturing | Powder bed is selectively melted by laser to build 3D parts |
Metal injection molding | Powder mixed with binder, molded, then sintered |
Press and sinter | Powder is pressed into shape and then sintered |
Surface coating | Sprayed or fused onto surface by thermal spraying, laser cladding etc. |
Brazing and welding | Used as filler material for joining |
The ultrafine grain structure and homogeneous consistency obtained from powders make 316L an ideal material for critical applications in aerospace, medical, chemical processing, and more.
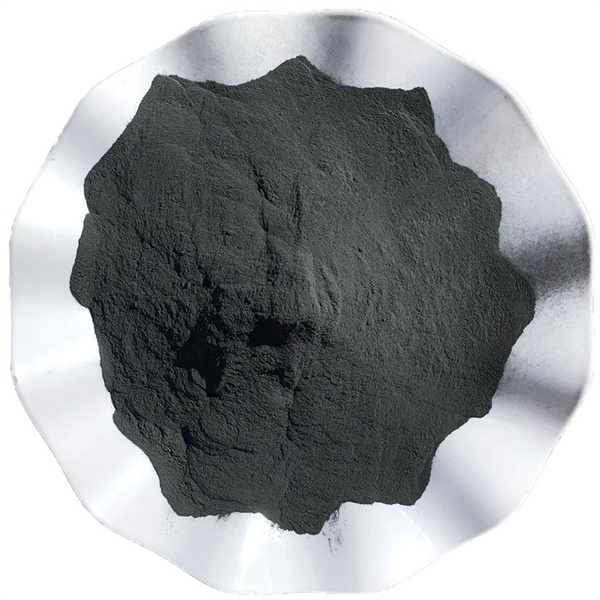
Properties of 316L Stainless Steel Powder
316L powder provides a combination of beneficial properties like corrosion resistance, strength, hardness, weldability, and biocompatibility. Here are some key properties of 316L powder:
Mechanical Properties
- Tensile strength: 500-700 MPa
- Yield strength: 200-300 MPa
- Elongation: 40-50%
- Hardness: ≤ 200 HV
- Modulus of elasticity: 190-210 GPa
Physical Properties
- Density: 7.9-8.1 g/cc
- Melting point: 1370-1400°C
Corrosion Resistance
- PREN > 23 for pitting/crevice corrosion resistance
- High resistance to acids, chlorides, sulfates
Other Properties
- Non-magnetic austenitic structure
- Excellent biocompatibility and machinability
- Low thermal expansion coefficient
- Good thermal/electrical conductivity
The mechanical strength, hardness, and corrosion resistance can be optimized through proper control of powder production, particle size distribution, and post-processing like hot isostatic pressing.
Production Methods for 316L Powder
316L powder can be produced through various methods. Each production route results in powders with different characteristics optimized for specific applications.
Gas Atomization
In gas atomization, the 316L alloy is melted and then disintegrated into fine droplets using high-pressure inert gas jets. The droplets rapidly solidify into spherical powders.
Typical powder properties:
- Particle size: 15-150 μm
- Morphology: Highly spherical
- Flowability: Excellent
- Apparent density: 2.5-4.5 g/cc
- Oxygen content: Low
Gas atomized 316L powder has high sphericity and flowability desired for additive manufacturing. Smaller particles sizes below 45 μm are used for laser-based AM processes.
Water Atomization
In water atomization, the molten 316L stream is broken into droplets by high-velocity water jets. The powders have irregular shapes due to rapid cooling.
Typical powder properties:
- Particle size: 10-300 μm
- Morphology: Irregular, dendritic
- Flowability: Moderate
- Apparent density: 2-4 g/cc
- Oxygen content: Higher
The irregular morphology provides mechanical interlocking when compressed, making water atomized 316L suitable for metal injection molding.
Plasma Atomization
Plasma atomization uses plasma gas to atomize the melt into finer and more spherical powders than gas atomization.
Typical powder properties:
- Particle size: 5-100 μm
- Morphology: Highly spherical
- Flowability: Excellent
- Apparent density: >3 g/cc
- Oxygen content: Low
Plasma atomized 316L powder has very fine sizes required for laser AM and excellent flow properties.
Electrode Induction Melting Gas Atomization (EIGA)
EIGA involves inductive melting of the 316L wire feedstock followed by gas atomization. It produces highly spherical nano-size powders.
Typical powder properties:
- Particle size: 10-150 nm
- Morphology: Highly spherical
- Flowability: Moderate
- Apparent density: ∼3 g/cc
- Oxygen content: Low
The ultrafine 316L powder from EIGA has properties optimized for binder-jetting AM process.
Electrolysis
In electrolytic process, 316L is dissolved from an anode and deposited at the cathode to produce spiky and dendritic powders.
Typical powder properties:
- Particle size: Up to 150 μm
- Morphology: Spiky, dendritic
- Flowability: Poor
- Apparent density: 2-4 g/cc
- Oxygen content: Low
The irregular morphology and porous structure of electrolytic 316L powder make it suitable for AM processes like electron beam melting.
Carbonyl Process
The carbonyl process involves decomposition of gaseous metal carbonyls to produce fine spherical powders.
Typical powder properties:
- Particle size: Less than 10 μm
- Morphology: Highly spherical
- Flowability: Good
- Apparent density: ∼4 g/cc
- Oxygen content: Low
carbonyl 316L powder has very fine particle sizes used for press and sinter applications. The high purity leads to excellent sintered properties.
Applications of 316L Stainless Steel Powder
316L powder is used across many industries due to its excellent well-balanced properties. Some major application areas include:
Additive Manufacturing
- Aerospace and aircraft components
- Orthopedic and dental implants
- Automotive parts like valves, pumps
- Biomedical devices like surgical instruments
- Maritime applications like impellers
Metal Injection Molding
- Orthopedic implants – knee, hip etc.
- Dental implants and products
- Cutting tools, razor blades
- Watch components
Press and Sinter
- Filters and porous structures
- Self-lubricating bearings
- Magnet retaining components
- Pistons, synchronizer hubs
Surface Coating
- Corrosion and wear-resistant coatings
- Biomedical coatings like stents, implants
- Restoration coatings for valves, pumps
- Decorative coatings
Welding and Brazing
- Aerospace components
- Cryogenic vessels and pipes
- Food processing equipment
- Biomedical devices
316L powder is also used for blending with other alloys to achieve tailored properties. Due to its biocompatibility, 316L is extensively used to make surgical tools, implants, stents, and other healthcare products.
Here is an overview of how 316L powder properties like particle size and morphology affect its usage in different applications:
Application | Preferred Powder Properties |
---|---|
Laser AM | Small particle size (<45 μm), spherical, flowable |
Electron beam AM | Medium particle size (45-150 μm), spherical |
Binder jetting AM | Ultrafine particle size (<1 μm), spherical |
MIM | Medium size (10-25 μm), irregular morphology |
Press and sinter | Fine particles (<10 μm) with some larger sizes |
Surface coating | Wide range (10-100 μm), spherical |
Specifications and Standards
316L powder composition, quality, and properties are governed by various international specifications and standards.
ASTM Standards
- ASTM A240 – Standard for chromium and chromium-nickel stainless steel plate, sheet, and strip for pressure vessels and general applications. Defines composition limits and mechanical properties for 316L alloy.
- ASTM B822 – Standard test method for particle size distribution of metal powders and related compounds by light scattering. Used to characterize powder size distribution.
- ASTM F3055 – Standard specification for additive manufacturing nickel alloy powder intended for use in powder bed fusion applications. Defines stringent requirements for AM nickel alloy powder including 316L.
- ASTM F3049 – Guide for characterizing properties of metal powders used for additive manufacturing processes. Provides guidance on measuring characteristics like flow, density, morphology etc.
Other Standards
- ISO 9001 – Quality management for production of metallic powders
- ISO 13485 – Quality management for metallic powders for medical applications
- ASME Boiler and Pressure Vessel Code – Material requirements for pressure vessel applications
Reputable 316L powder suppliers have quality systems certified to ISO and ASTM standards. Lot traceability and extensive testing are maintained to ensure compliance.
316L Powder Suppliers
Some leading global suppliers of 316L stainless steel powder include:
Company | Production Methods | Powder Types | Particle Size |
---|---|---|---|
Sandvik | Gas atomization | Osprey® 316L | 15-45 μm |
LPW Technology | Gas atomization | LPW 316L | 15-63 μm |
Carpenter | Gas atomization | Carpenter 316L | 15-150 μm |
Höganäs | Water atomization | 316L | 10-45 μm |
CNPC | Gas, water atomization | 316L | 10-150 μm |
Pometon | Gas, water atomization | 316L | 10-150 μm |
ATI | Gas atomization | 316L | 10-63 μm |
316L powder pricing depends on factors like:
- Powder quality, composition, particle size and morphology
- Production method
- Order quantity and lot size
- Level of quality control and testing
- Packaging and delivery requirements
Indicative pricing for gas atomized 316L powder is in the range of $50-100 per kg for standard orders. Custom orders with special requirements may cost more.
When selecting a 316L powder supplier, some key considerations include:
- Powder characteristics – particle size distribution, morphology, flowability etc. should match application needs
- Consistent quality and composition per specifications
- Reliable supply chain and logistics
- Compliance to international standards and certifications
- Technical expertise and customer service
- Pricing and minimum order quantity
Leading 316L powder manufacturers have decades of experience in producing powders tailored to AM, MIM, and other applications with stringent quality control.
Design Considerations for 316L Powder
Here are some key design aspects to consider when using 316L powder in manufacturing:
Part Geometry
- Optimize wall thickness, overhangs, bridges, and diameters for the AM or MIM process
- Account for shrinkage of ~20% for binder-based processes like MIM
- Include supports where needed, integrate support structures into design
Porosity
- Control process parameters to limit porosity to less than 1%
- Strategically orient part to avoid trapped powder
- Optimize heat treatment, HIP can further reduce porosity
Surface Finish
- AM processes require additional finishing like machining, grinding, electro-polishing to improve surface finish
- Account for ~0.1-0.4 mm of stock removal during finishing procedures
Mechanical Properties
- Meet minimum property requirements like tensile and yield strength
- Account for anisotropy; build orientation affects properties
- Solution annealing, aging treats can optimize properties
Dimensional Tolerances
- Account for dimensional variations of AM or MIM process
- Allow wider tolerances, use post-processing to improve accuracy
- Critical interfaces may require additional machining
Involving manufacturing engineers early in the design process is key to designing and optimizing parts for AM and MIM processes with 316L powder.
Post-Processing of 316L Parts
316L parts from AM and MIM processes often require post-processing to achieve the final properties and finish. Some key post-processing steps include:
Heat Treatment
- Stress relief annealing to release internal stresses
- Solution treatment to dissolve precipitates and optimize corrosion resistance
- Aging treatment to increase strength through precipitation hardening
Hot Isostatic Pressing
- Closes internal voids and porosities in the material
- Improves density, strength, ductility and fatigue life
Surface Finishing
- Machining and grinding to improve dimensional accuracy and surface finish
- Electro-polishing for smooth mirror-like surface finish
- Media blasting provides decorative finishes
Coatings
- PVD, CVD coatings can enhance wear and corrosion resistance
- Passivation treatments improve corrosion resistance
Quality Testing
- CT scans check for internal defects and porosity issues
- Mechanical testing confirms properties meet specifications
- Non-destructive inspection for critical defect detection
The optimal post-processing pathway depends on the AM process, part geometry, critical defects, and final performance requirements.
Common Defects in 316L Parts
Some potential defects in 316L parts made through AM, MIM, and other powder-based processes include:
- Porosity – Gas entrapment leads to voids and porosity, reducing density.
- Cracking – Develops due to internal stresses during processing and improper heat treatment.
- Anisotropy – Differences in properties along build directions due to layer-by-layer fabrication.
- Surface Roughness – Layer-wise roughness, partially sintered particles, unmolten regions lead to poor surface finish.
- Dimensional Variations – Part shrinkage, curling, and warpage result in deviations from design dimensions.
- Compositional Changes – Segregation, evaporation loss, contamination can alter composition locally.
- Lack of Fusion – Incomplete melting between layers and tracks due to lack of energy input.
- Balling – Formation of small spheres during AM instead of uniform tracks, leads to porosity.
- Residual Stresses – Develop during processing due to high thermal gradients and interfere with performance.
Thorough process monitoring, optimized parameters, quality control testing, and proper post-processing steps can help minimize defects in 316L parts.
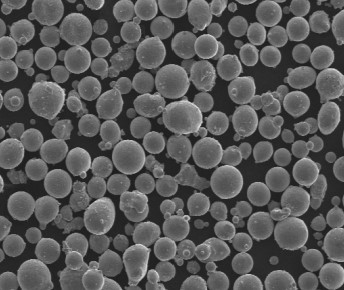
How to Choose a 316L Powder Supplier
Here is a step-by-step guide on selecting a supplier for 316L stainless steel powder:
Step 1: Determine Application Requirements
- Consider which manufacturing process will be used – AM, MIM etc.
- Identify the critical powder properties needed like particle size, shape, purity etc.
- Consider the part specifications – mechanical properties, accuracy, surface finish etc.
Step 2: Research Potential Suppliers
- Search for leading 316L powder manufacturers with long experience
- Check capabilities – production methods, powder varieties, QC testing etc.
- Review case studies and customer reviews relevant to your application
Step 3: Evaluate Technical Capabilities
- Can they customize 316L powder to your application needs?
- Do they have expertise in AM, MIM or other powder technologies?
- What is their level of vertical integration and quality control?
Step 4: Assess Service Offerings
- Technical support during powder selection, application development
- Sample testing, trialling services
- Responsiveness to inquiries, lead time flexibility
Step 5: Review Certifications and Compliance
- International quality certifications – ISO 9001, ISO 13485 etc.
- Compliance to powder composition standards like ASTM
- Lot traceability, extensive testing and documentation
Step 6: Compare Pricing
- Price per kg for required particle size, quality level, quantity
- Minimum order quantity and lot size requirements
- Shipping/logistics costs
Step 7: Check Availability and Reliability
- Steady in-stock supply and ability to meet demand fluctuations
- Order tracking and monitoring, transparent lead times
- Proven on-time delivery record
Selecting a supplier with application expertise, consistent product quality, and responsive service ensures a smooth procurement experience.
How to Optimize 316L Powder for AM
Match Particle Size to AM Process
- Use 10-45 μm particles for powder bed fusion like DMLS, SLM
- Optimize size distribution – too wide can cause packing issues
- Finer 1-10 μm particles better suited for binder jetting
Achieve High Sphericity and Flowability
- Flowability directly affects powder spreading and layer uniformity
- Gas atomization produces spherical, free-flowing powders
- Test powder flow as per ASTM B213 standard
Minimize Satellite Particles
- Use sieving, classification to remove satellites and fines
- Satellites can cause agglomeration and defects
Control Composition Tolerance
- Tightly control elemental composition within ASTM specified range
- Limit impurities like O, N, C which affect properties
Reduce Porosity
- Optimize process parameters and scan patterns
- Use hot isostatic pressing to minimize porosity
- Maintain >99% density for high performance
Minimize Residual Stresses
- Optimize thermal gradients in the build process
- Use appropriate heat treatments to relieve stresses
Achieve Target Mechanical Properties
- Solution annealing and aging improves strength
- Maintain uniform properties in all build directions
Careful powder characterization, parameter optimization, and post-processing are key to achieve defect-free 316L parts using AM.
FAQ
Q: What is 316L stainless steel powder typically used for?
A: 316L powder is most widely used for additive manufacturing, metal injection molding, and press & sinter applications due to its excellent corrosion resistance combined with good mechanical properties and biocompatibility. Common applications include implants, aerospace components, automotive parts, biomedical devices, and tooling.
Q: What particle size is recommended for laser-based AM processes?
A: A particle size range of 10-45 microns is typically recommended for laser powder bed fusion processes like DMLS and SLM. Finer particles below 10 microns can cause issues with flow and spreading. Particle size distribution should also be well controlled.
Q: How does powder morphology affect properties?
A: Highly spherical, free-flowing powder is desirable for AM applications. Irregular, spiky powder is suited for press and sinter methods. Satellite particles and fines negatively impact powder flow and can create defects. Controlling powder morphology is key for optimal performance.
Q: What are some key differences between gas atomized vs water atomized 316L powder?
A: Gas atomized 316L powder has more spherical morphology and better flowability. Water atomized powder displays more irregular shapes but provides higher compressibility desired for press and sinter applications. Gas atomized powder has lower oxygen content.
Q: What post-processing methods are used on 316L AM parts?
A: Common post-processing includes heat treatment, hot isostatic pressing, surface finishing through grinding/machining, coating, and quality control testing. This helps achieve target properties, dimensional accuracy, aesthetics, and defect detection.
Q: What are some common 316L powder defects and how can they be avoided?
A: Potential defects are porosity, cracking, poor surface finish, lack of fusion, and residual stresses. Careful process parameter optimization, powder quality control, build orientation, and post-processing can minimize these defects in 316L parts.
Q: What standards apply to 316L powder for AM and other applications?
A: Key standards are ASTM F3055 for AM powders, ASTM B822 for powder characterization, ASTM A240 for alloy composition, and ISO standards for quality management. Leading 316L powder suppliers are certified to these standards.
Q: What factors determine pricing for 316L powder?
A: Main factors affecting 316L powder pricing are quality level, particle size and distribution, production method, order quantity, buyer requirements for testing/QC, packaging and delivery. More stringent needs increase pricing.
Q: How can corrosion resistance of 316L AM parts be optimized?
A: Solutions include controlling impurity levels through tight chemical composition tolerances, using hot isostatic pressing to increase density and reduce porosity, applying passivation treatments, and solution annealing to improve corrosion resistance.