Spherical tungsten powder refers to tungsten metal particles in a spherical powder form produced by atomization processes. With the highest melting point of all metals, tungsten provides unique properties including high density, strength, hardness, and conductivity. This guide provides an overview of spherical tungsten powder including manufacturing methods, characteristics, applications, specifications, usage recommendations, suppliers, and frequently asked questions.
Introduction to Spherical Tungsten Powder
Tungsten is a refractory metal valued for its extremely high melting point of 3422°C, density of 19.3 g/cc, hardness, high temperature strength, wear resistance, and electrical conductivity.
Converting tungsten into a spherical powder form enables use in manufacturing techniques such as:
- Metal injection molding (MIM)
- Additive manufacturing
- Thermal spray coatings
- Composite production
- Electronic thick film pastes
- Ballast applications
Benefits of spherical tungsten powder include:
- Consistent shape and size distribution
- High purity
- Good flow and packing characteristics
- Tunable density in finished parts
- High loadings in composites
- High density resolution in AM
- Smooth surface finish in MIM
This guide provides a detailed overview of spherical tungsten powder and its applications.
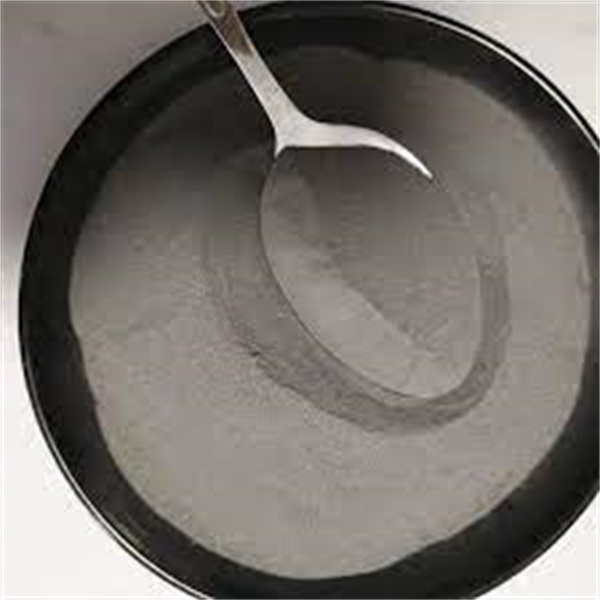
Methods for Producing Spherical Tungsten Powder
Spherical tungsten powder is commercially produced via specialized processes:
- Plasma Spheroidization – Tungsten particles pass through a plasma torch and are melted into spheres by surface tension before rapidly solidifying. This produces the most spherical powder.
- Rotating Electrode Process – Tungsten wire feeds into an electric arc to produce droplets that are spun into spheres by centrifugal forces.
- Atomization – Molten tungsten is gas or water atomized into spherical droplets.
- Mechanical Spheroidization – Irregular tungsten powder is mechanically processed into more spherical particles. Lower cost but less spherical results.
Plasma spheroidization makes the roundest and most consistently sized tungsten powder ideal for high performance applications.
Properties of Spherical Tungsten Powder
Spherical tungsten powder exhibits properties ideal for improving density, conductivity, and wear resistance:
- High density up to 18 g/cm3
- High melting point of 3422°C
- Excellent hardness up to 550 VPN
- High thermal and electrical conductivity
- Low vapor pressure
- Resistance to acids and alkalis
- Biocompatible and non-toxic
Combined with spherical morphology for excellent packing and flowability, tungsten powder provides ideal performance characteristics.
Key Applications of Spherical Tungsten Powder
Thanks to its unique properties, spherical tungsten powder is used across a range of industries:
- Additive manufacturing
- Metal injection molding
- Tungsten heavy alloys
- Radiation shielding
- Vibration damping
- Counterweights
- Ballasts
- Electrodes
- Thermal spray coatings
- Composite fillers
- Electrical contacts
- Medical radiotherapy
Spherical morphology improves performance in powder-based manufacturing methods like metal AM and MIM in particular.
Specifications of Spherical Tungsten Powder
The powder is characterized by metrics like particle size, shape, purity, and chemistry:
Typical Spherical Tungsten Powder Specs
Parameter | Specification |
---|---|
Particle Size | 1 – 150 μm |
Particle Shape | Spherical |
Size Distribution | D10, D50, D90 |
True Density | 18.7 g/cm3 |
Apparent Density | 10 – 15 g/cm3 |
Purity | 99.9% |
Oxygen Content | < 50 ppm |
Carbon Content | < 50 ppm |
Understanding specifications allows matching powder properties to manufacturing process and end product requirements.
Particle Size Distribution
Spherical tungsten powder is classified by particle size according to standard ranges:
Tungsten Powder Size Classifications
Type | Particle Size Range |
---|---|
Coarse | 10-150 μm |
Medium | 1-10 μm |
Fine | 1-5 μm |
Nanoscale | < 1 μm |
- Larger particles improve powder flow
- Smaller particles allow higher density but may be pyrophoric
- Particle sizes tailored to application method
Controlling particle size distribution through classification improves packing density, flow characteristics, and repeatability.
How to Select Spherical Tungsten Powder
Key considerations for selecting tungsten powder include:
- Application method and ideal powder properties
- Particle shape and degree of sphericity
- Particle size distribution (PSD) as classified
- Purity levels and chemistry characteristics
- Sampling and lots testing certification
- Apparent and tap density specifications
- Handling and safety precautions required
- Pricing based on order quantity
- Manufacturer’s capabilities and experience
Consult closely with experienced tungsten powder suppliers to match an optimized product to your production requirements.
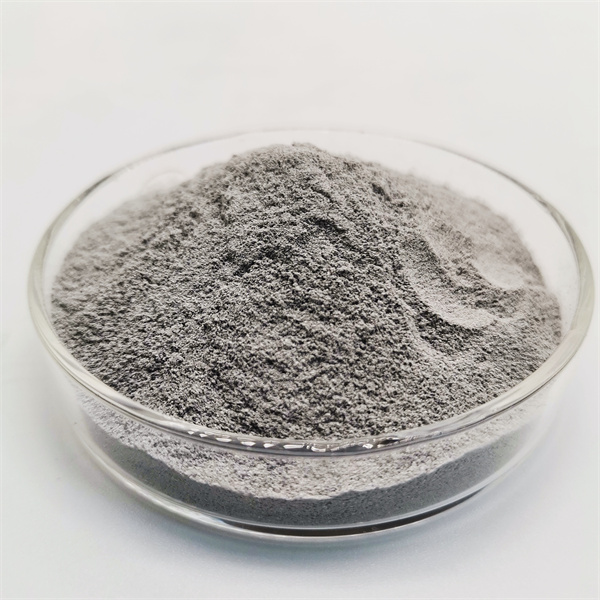
Handling and Storage of Tungsten Powder
Safe handling practices are critical when working with fine tungsten powder:
- Use inert gas glove boxes to prevent oxidation
- Avoid airborne dust through ventilation controls
- Powders may be pyrophoric when very fine
- Ground all equipment and use conductive containers
- Store sealed powder containers away from moisture and heat
- Follow guidance in the Safety Data Sheet (SDS)
- Wear PPE and avoid skin contact or inhalation
Proper techniques and controls mitigate safety risks and maintain powder properties.
Where to Buy Spherical Tungsten Powder
Leading global suppliers of spherical tungsten powder include:
Spherical Tungsten Powder Suppliers
Company | Location |
---|---|
Buffalo Tungsten | USA |
H Cross Company | USA |
Tekna | Canada |
Midwest Tungsten | USA |
Wolfram Company | USA |
HC Starck | Germany |
Jiangxi Tungsten | China |
Factors to consider when selecting a supplier:
- Production capabilities and capacity
- Powder sphericity, size distribution consistency
- Range of available size classifications
- Testing reports and lot data provided
- Packaging options available
- Lead times for both stock and custom orders
- Technical expertise and customer service
Sample testing and site visits help validate supplier quality and capabilities.
Cost Analysis of Tungsten Powder
Tungsten powder pricing depends on:
- Purity grade
- Particle size distribution
- Sphericity level
- Production method sophistication
- Sampling and analytical testing
- Order quantity
- Packaging and delivery
As a guide, spherical tungsten powder costs between $50 to $500 per kg currently. Quotes from suppliers establish exact pricing based on custom requirements.
Innovations in Tungsten Powder Manufacturing
Recent advances in tungsten powder production include:
- Additive manufacturing using tungsten powder
- Automated powder production with higher yields
- Micron to sub-micron size control
- Recycling and reprocessing of scrap powder
- Simulation modeling for atomization parameters
- Specialized alloy powder compositions
- Continuous rather than batch processing
These innovations expand the applications and improve the cost-effectiveness of spherical tungsten powder.
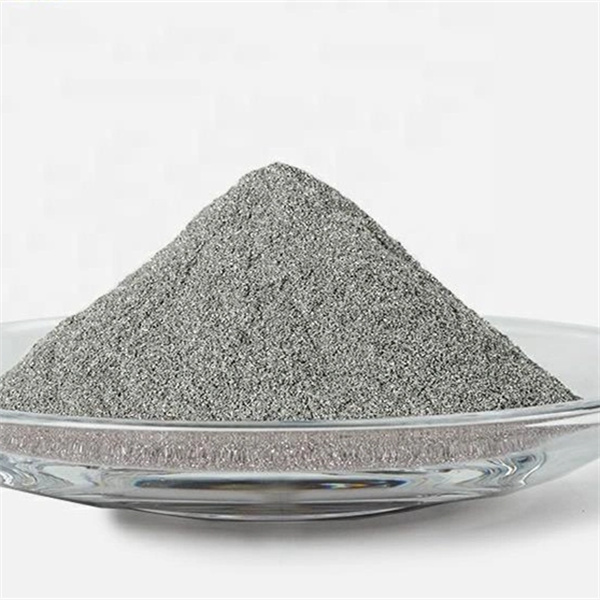
Key Takeaways on Spherical Tungsten Powder
- Produced via plasma spheroidization or rotating electrode process
- Excellent density, hardness, and high temperature properties
- Spherical shape improves powder flow and packing density
- Used in composites, ballasts, counterweights, radiation shielding
- Particle size distribution carefully controlled through classification
- Require proper inert atmosphere handling to prevent fires or explosions
- Pricing ranges based on purity, size distribution, and order quantity
- Leading tungsten powder suppliers provide various size classifications
With its extreme properties and spherical morphology, tungsten powder enables high performance manufacturing across 3D printing, injection molding, and other powder-based technologies.
FAQs
Q: Is tungsten powder dangerous to handle?
A: Yes, fine tungsten powder can pose dust explosion risks and may be pyrophoric at small sizes. Proper inert atmosphere handling is critical.
Q: What is spherical tungsten mainly used for?
A: Currently the main uses are in tungsten heavy alloys, counterweights, ballasts, and radiation shielding, though additive manufacturing applications are expanding.
Q: What is the difference between spherical and irregular tungsten powders?
A: Spherical powders have superior flow, packing density, and surface finish. Irregular powder is less expensive but does not perform as well in many powder-based applications.
Q: Is tungsten environmentally friendly?
A: Yes, tungsten is non-toxic with excellent recyclability and reuse potential. Protective controls prevent environmental releases.
Q: Which makes a more spherical powder – gas atomization or plasma spheroidization?
A: Plasma spheroidization makes the most consistently spherical and smooth powders compared to other methods.
Q: How is powder size measured and classified?
A: Laser diffraction particle size analyzers determine the distribution. Sieves and air classification separate powder into size fractions.
Q: Can you 3D print using spherical tungsten powder?
A: Yes, tungsten’s excellent high temperature properties make it suitable for specialized additive manufacturing applications, though challenging to print.
Q: Does spherical shape affect tungsten material properties?
A: Sphericity enhances powder performance but does not significantly alter tungsten’s inherent physical properties like density or melting point.
Q: What alloying elements are combined with tungsten powder?
A: Typical alloys include nickel, iron, and cobalt combinations to enhance strength and ductility for applications like cutting tools.