Refractory Powder Materials represent a specialized class of inorganic non-metallic materials exhibiting extremely high heat resistance used across demanding industries. This comprehensive guide serves technical professionals and buyers understanding all key characteristics of refractory powders – spanning typical composition, critical properties data, manufacturing processes, applications, specifications and suppliers.
Overview of Refractory Powder Materials
Refractory powders comprise finely divided inert non-metallic materials demonstrating exceptional thermal stability, retaining strength and form at high temperatures exceeding 1000°C. Key subclasses include oxides, carbides, nitrides and ceramics.
Critical Attributes:
- Heat resistance over 1000°C
- Resist thermal shock
- Withstand corrosion
- High melting point
- Keep structural integrity
Their exceptional capabilities empower performance in furnaces, boilers, kilns, reactors and other extreme thermal environments where traditional materials fail rapidly.
Typical Composition
Material | Role | Wt% Range |
---|---|---|
Alumina | Thermal properties | 40-100% |
Silica | Bind the matrix | 0-60% |
Magnesia | Resist deterioration | 0-20% |
Graphite | Increase thermal shock resistance | 0-15% |
Balancing key constituents enables optimizing characteristics like heat capacity, insulation, erosion resistance, melting point and cost.
Major Types of Refractory Powders
Type | Description |
---|---|
Fused | Extreme purity, withstand over 1800°C |
Sintered | Powder pressing/firing, lower cost |
Silicon carbide | Ceramic with high heat conductivity |
Chromite | Resist slag, metal penetration |
Zirconia | Thermal shock resistance |
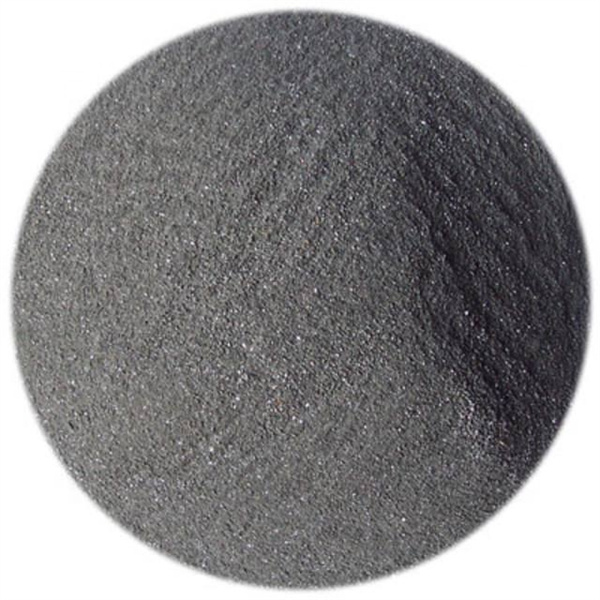
Refractory Powder Materials Manufacturing Processes
Producing advanced refractory powders requires stringent processing protocols under specialized conditions.
Primary Production Methods
Process | Details |
---|---|
Ball milling | Mechanical alloying |
Sol-gel | Chemical precipitation |
Fused | Molten phase quenching |
Sintering | Controlled powder consolidation |
Plasma spraying | Very high temperature spheroidization |
Resulting Particle Morphology
- Spherical
- Angular
- Platelet
- Mixed globular and angular
Typical Refractory Powder Size Distribution
Mesh Size | Micrometers |
---|---|
-170 | 90 μm |
-325 | 45 μm |
-500 | 25 μm |
Both standard and custom particle engineering allows tailoring product characteristics.
Properties of Refractory Powder Materials
Property | Typical Value |
---|---|
Melting Point | Over 1600°C |
Density | 2 – 6 g/cm3 |
Compressive Strength | 20 – 100 MPa |
Flexural Strength | 10 – 60 MPa |
Fracture Toughness | 2 – 10 MPa-m^1/2 |
Thermal Conductivity | 20 – 100 W/m-K |
Electrical Resistivity | 10^8 – 10^13 Ohm-cm |
Maximum Service Temperature | 1200°C – 2000°C |
Balancing requirements like melting point, heat capacity, thermal shock resistance, insulation value, chemical inertia and cost determines selection.
Applications of Refractory Powder Materials
Metallurgy and Foundries
- Crucibles, ladles
- Tundish nozzles
- Pouring shrouds
- Slag conditioners
High Temperature Processing
- Fired heater linings
- Ceramic kilns
- Incinerators
- Nuclear fuel cladding
Chemical Industry
- Reformer tubes
- Reactor internals
- Syngas coolers
- Catalyst support structures
Power Generation
- Boiler linings
- Heat exchangers
- Steam pipes/valves
- Heat shields
Aerospace and Defense
- Missile casings
- Rocket nozzles
- Ablative composites
- Furnace elements
Specifications and Grades
Attribute | Typical Values |
---|---|
Purity | Over 98% |
Contamination | Minimized S, P, Si, Fe |
Particle Size | 10μm – 150μm |
Shape Factor | 0.8 – 1 |
Specific Surface Area | 0.5 – 2 m2/g |
Bulk Density | 0.6 – 2 g/cm3 |
Flow Characteristics | Angle of Repose <40° |
Widely Used Refractory Grades
Grade | Description |
---|---|
Tabular alumina | Platy powder, thermal shock resistance |
Fused mullite | Alumina-silica, resists creep deformation |
Silicon carbide | Extreme hardness, thermal conductivity |
Fused zirconia | Toughness, high ionic conductivity |
Boron nitride | Outstanding dielectric properties |
Refractory Powder Materials Suppliers
Company | Location |
---|---|
Saint-Gobain | Global |
RHI Magnesita | Brazil, Austria, China |
Krosaki Harima | Japan |
Vesuvius | Europe, United States |
Morgan Advanced Materials | United Kingdom, United States |
Pricing Estimates
Grade | Price per kg |
---|---|
Tabular Alumina | $10-30 |
Silicon Carbide | $50-150 |
Zirconia | $100-500 |
Others | $20-100 |
Economies of scale influence costs – customized compositions and strict quality requirements command premiums.
Pros vs Cons
Pros | Cons |
---|---|
Exceptional heat/corrosion resistance | Brittle mechanical properties |
Ultra-high melting points | Sensitive processing methods |
Withstand thermal shock | Higher material cost |
Custom composition and properties | Limited form factors |
Enable extreme environment applications | Challenging to fully characterize |
Pushing boundaries of thermal stability proves essential for continuous technology advancements – refractory powders make this possible despite production obstacles.
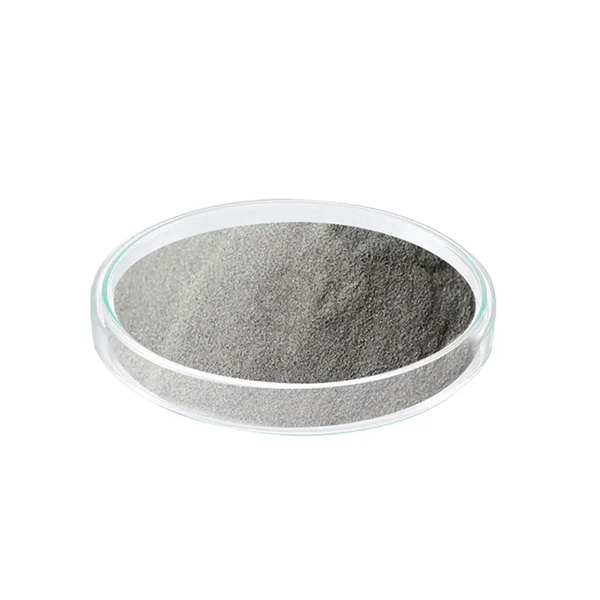
FAQs
Q: What is the difference between refractory powders and refractory bricks?
A: Bricks are pre-formed consolidated constructions, while powders represent raw material feedstocks enabling fabrication of specialty refractory components through pressing/firing or advanced additive manufacturing methods.
Q: Can all refractory powders get 3D printed using AM technology?
A: Yes – binder jetting and directed energy deposition printing proves compatible with most thermally resistant alumina, zirconia and silicon carbide grades for previously impossible refractory geometries.
Q: Which refractory powder offers the highest service temperature?
A: Ultra-high purity fused mullite and zirconia grades reliably withstand over 2000°C for the most demanding furnace, aerospace and nuclear applications where alternatives melt or decompose.
Q: What is the difference between synthetic and natural refractory materials?
A: Natural raw materials like bauxite, magnesite and clay must get extensively processed into precisely controlled powders to achieve the enhanced uniformity and extreme thermal resistance possible with synthetic engineered formulations.
Conclusion
This guide aimed providing a holistic reference on refractory powders – special materials overcoming limitations of ordinary metals and alloys in the hottest, most aggressive industrial environments through exceptional heat resistance. Please connect with an industry expert to discuss tailoring advanced refractory grades to your specific extreme processing needs. The possibilities stretch far.