Ti6Al4V Powder
Ti6Al4V powder, also referred to as Grade 5 titanium alloy, is one of the most popular titanium alloy powders. It contains 6% aluminum and 4% vanadium as the key alloying elements along with the remainder titanium. Ti6Al4V powder offers an exceptional combination of high strength, low weight, corrosion resistance, biocompatibility, and workability.
Low MOQ
Provide low minimum order quantity to meet different needs.
OEM & ODM
Provide customized products and design services to meet unique customer needs.
Adequate Stock
Ensure fast order processing and provide reliable and efficient service.
Customer Satisfaction
Provide high quality products with customer satisfaction at the core.
share this product
Table of Contents
Overview of Ti6Al4V Powder
Ti6Al4V powder, also referred to as Grade 5 titanium alloy, is one of the most popular titanium alloy powders. It contains 6% aluminum and 4% vanadium as the key alloying elements along with the remainder titanium.
Spherical powder ti6al4v offers an exceptional combination of high strength, low weight, corrosion resistance, biocompatibility, and workability.
Key properties and advantages of Ti6Al4V powder:
Ti6Al4V Powder Properties and Characteristics
Properties | Details |
---|---|
Composition | Ti-6Al-4V alloy |
Density | 4.43 g/cc |
Particle shape | Predominantly spherical |
Size range | 15-45 microns |
Apparent density | Up to 60% of true density |
Flowability | Good |
Strength | High for a titanium alloy |
Corrosion resistance | Excellent |
Ti6Al4V is widely used across aerospace, medical, automotive, chemical, and consumer industries owing to its well-balanced property profile.
Ti6Al4V Powder Composition
Typical composition of Ti6Al4V powder:
Ti6Al4V Powder Composition
Element | Weight % |
---|---|
Titanium | Balance |
Aluminum | 5.5-6.75% |
Vanadium | 3.5-4.5% |
Oxygen | <0.2% |
Carbon | <0.1% |
Nitrogen | <0.05% |
Hydrogen | <0.015% |
Iron | <0.3% |
- Titanium forms the matrix providing strength and corrosion resistance
- Aluminum stabilizes alpha phase and increases strength
- Vanadium stabilizes beta phase and improves workability
- Other elements limited as impurities
The optimized Ti-Al-V ratios provide an exceptional combination of strength, ductility, fracture toughness, and fatigue strength.
Ti6Al4V Powder Physical Properties
Ti6Al4V Powder Physical Properties
Property | Values |
---|---|
Density | 4.43 g/cc |
Melting point | 1604-1660°C |
Thermal conductivity | 6.7 W/mK |
Electrical resistivity | 170 μΩ-cm |
Coefficient of thermal expansion | 8.4 x 10^-6 /K |
Maximum service temperature | 400°C |
- Low density compared to steels
- High melting point enables use at moderately elevated temperatures
- Low thermal conductivity requires design considerations
- High electrical resistivity suitable for corrosion resistant fasteners
- CTE lower than steels and nickel alloys
These properties make Ti6Al4V well suited for many lightweight structural applications across industries.
Ti6Al4V Powder Mechanical Properties
Ti6Al4V Powder Mechanical Properties
Property | Values |
---|---|
Tensile strength | 950 – 1050 MPa |
Yield strength | 860 – 950 MPa |
Elongation | 10 – 18% |
Hardness | 330 – 380 HB |
Modulus of elasticity | 110 – 120 GPa |
Fatigue strength | 400 – 500 MPa |
- Excellent combination of high strength and reasonable ductility
- Strength exceeds other titanium grades like commercially pure titanium
- Hardness higher than unalloyed titanium
- Outstanding fatigue life makes it suitable for cyclic loading applications
The properties make Ti6Al4V suitable for demanding applications requiring high specific strength and fatigue resistance.
Ti6Al4V Powder Applications
Ti6Al4V powder is used widely across industries:
Ti6Al4V Powder Applications
Industry | Uses |
---|---|
Aerospace | Structural airframe parts, engine components |
Biomedical | Orthopedic and dental implants |
Automotive | Connecting rods, valves, springs |
Chemical | Tanks, vessels, heat exchangers |
Consumer | Sporting goods, watch cases, cellphone bodies |
3D Printing | Aerospace and medical components |
Some specific product applications include:
- Bone plates, joint replacement implants
- Airplane and helicopter structural components
- Automotive engine valves and connecting rods
- Chemical equipment like pipes, pumps, valves
- Sporting goods including golf clubs and bicycle frames
- Additive manufacturing of lightweight structures
Ti6Al4V provides the best strength-to-weight ratio and biocompatibility for critical structural parts across these demanding sectors.
Ti6Al4V Powder Specifications
Key specifications and standards for Ti6Al4V powder:
Ti6Al4V Powder Standards
Standard | Description |
---|---|
ASTM F2924 | Additive manufacturing Ti6Al4V alloy |
ASTM F3001 | Specs for gas atomized Ti alloy powder for AM |
AMS 4954 | Composition limits of Ti-6Al-4V powder for additive manufacturing |
ASTM B348 | Specs for Ti and Ti alloy powders |
ASTM F1472 | Wrought Ti6Al4V alloy for surgical implants |
These define:
- Chemical composition ranges
- Required mechanical properties
- Powder production method – inert gas atomization
- Impurity limits like O, N, C, Fe
- Particle size distribution and morphology
- Testing methods to verify powder quality
Certified Ti6Al4V powder meeting these specifications ensures optimal properties and performance for different applications across industries.
Ti6Al4V Powder Particle Sizes
Ti6Al4V Powder Particle Size Distribution
Particle Size | Characteristics |
---|---|
15-45 microns | General purpose size range |
45-100 microns | Optimized for cold spraying |
5-25 microns | Finer sizes used in laser AM processes |
- Finer powder provides higher resolution and surface finish
- Coarser powder suits high deposition rate methods like cold spraying
- Size range tailored based on production method used
- Spherical morphology maintained across size ranges
Controlling particle size distribution and morphology is critical for high powder packing density, flowability, and final part properties.
Ti6Al4V Powder Apparent Density
Ti6Al4V Powder Apparent Density
Apparent Density | Details |
---|---|
Up to 60% of true density | For spherical powder morphology |
2.6 – 3.0 g/cc | Improves with greater packing density |
- Higher apparent density improves powder flowability and die filling efficiency
- Values up to 65% are possible with optimized spherical powder
- High apparent density minimizes press cycle time
Maximizing apparent density allows efficient automated powder pressing and sintering to full density.
Ti6Al4V Powder Production Method
Ti6Al4V Powder Production
Method | Details |
---|---|
Gas atomization | High pressure inert gas breaks up molten alloy stream into fine droplets |
Vacuum arc melting | High purity input materials refined and melted in vacuum |
Multiple remelts | Improves chemical homogeneity |
Sieving | Classifies powder into different particle size fractions |
- Gas atomization with inert gas produces clean, spherical powder
- Vacuum processing minimizes gaseous impurities
- Multiple remelts improve uniformity of composition
- Post-processing allows particle size distribution control
Automated methods combined with stringent quality control result in reliable and consistent Ti6Al4V powder suitable for critical applications.
Ti6Al4V Powder Pricing
Ti6Al4V Powder Pricing
Factor | Impact on Price |
---|---|
Purity grade | Price increases for higher purity |
Particle size | Ultrafine powder more expensive |
Order quantity | Price reduces for bulk orders |
Production method | Use of multiple remelts increases cost |
Packaging | Argon filled cylinders cost more |
Lead time | Faster delivery times increase price |
Indicative Pricing
- Ti6Al4V for medical applications: $150-250 per kg
- Ti6Al4V for industrial applications: $100-150 per kg
Significantly lower pricing applicable for bulk order quantities in the tons range.
Ti6Al4V Powder Suppliers
Ti6Al4V Powder Suppliers
Company | Location |
---|---|
AP&C | USA, Canada |
Carpenter Additive | USA |
Met3DP | China |
TLS Technik | Germany |
Sandvik Osprey | UK |
Tekna | Canada |
Key selection factors:
- Range of purity grades and particle sizes offered
- Powder quality and consistency from batch to batch
- Production capacity and lead times
- Compliance with medical and aerospace standards
- Pricing levels based on order volume
- Technical expertise and customer support
Ti6Al4V Powder Handling and Storage
Ti6Al4V Powder Handling
Recommendation | Reason |
---|---|
Avoid inhalation | Due to risk of lung tissue damage from fine particles |
Use protective mask | Prevent accidental ingestion |
Handle in ventilated areas | Reduce airborne particle suspension |
Ensure no ignition sources | Powder can combust in oxygen atmosphere |
Follow anti-static protocols | Prevent fire from static discharge while handling |
Store sealed containers in cool, dry area | Prevent moisture pickup and reactivity |
Although Ti6Al4V powder is relatively inert, recommended precautions should be taken during handling and storage to preserve purity.
Ti6Al4V Powder Inspection and Testing
Ti6Al4V Powder Testing
Test | Details |
---|---|
Chemical analysis | ICP spectroscopy used to verify composition |
Particle size distribution | Laser diffraction used to determine size distribution |
Apparent density | Measured using Hall flowmeter as per ASTM B212 |
Powder morphology | SEM imaging to check particle sphericity |
Flow rate analysis | Using Hall flowmeter funnel |
Tap density test | Density measured after mechanically tapping powder sample |
Testing ensures the powder meets the required chemical composition, physical characteristics, morphology, density, and flow specifications per applicable standards.
Ti6Al4V Powder Pros and Cons
Advantages of Ti6Al4V Powder
- Excellent strength-to-weight ratio
- High fatigue strength and fracture toughness
- Outstanding corrosion resistance
- Good ductility and formability
- High biocompatibility for medical uses
- Cost-effective compared to other titanium alloys
Limitations of Ti6Al4V Powder
- Moderate high temperature oxidation resistance
- Lower strength than some titanium alloys
- High reactivity requires inert processing atmosphere
- Difficult to machine in fully sintered state
- Limitations in welding the alloy
- Toxicity concerns about vanadium element
Comparison With Ti64 and Ti Grade 2 Powders
Ti6Al4V vs. Ti64 and Grade 2 Powder
Parameter | Ti6Al4V | Ti64 | Ti Grade 2 |
---|---|---|---|
Aluminum | 6% | 6% | – |
Vanadium | 4% | 4% | – |
Strength | 950-1050 MPa | 950-1050 MPa | 420-550 MPa |
Ductility | 10-18% | 10-18% | 15-30% |
Cost | Moderate | Moderate | Low |
Uses | Aerospace, medical | Aerospace, automotive | Industrial, consumer |
- Ti6Al4V and Ti64 have virtually identical properties
- Grade 2 Ti provides better ductility but lower strength
- Ti6Al4V preferred for critical structural parts needing high strength
Ti6Al4V Powder FAQs
Q: What are the main applications of Ti6Al4V powder?
A: The main applications include aerospace structural components, biomedical implants like hip and knee joints, automotive parts like valves and connecting rods, chemical process equipment, and consumer products like sports equipment and watch cases.
Q: Why is Ti6Al4V the most popular titanium alloy?
A: Ti6Al4V provides the best all-round combination of high strength, low density, fracture toughness, corrosion resistance, bio-compatibility, weldability, and moderate cost.
Q: What precautions should be taken when working with Ti6Al4V powder?
A: Recommended precautions include using protective gear, handling in inert atmosphere, avoiding ignition sources, controlling static charges, using non-sparking tools, and storing sealed containers in a cool, dry place.
Q: How does vanadium affect the properties of Ti6Al4V alloy?
A: Vanadium acts as a beta stabilizer which improves workability. It also contributes to precipitation hardening which imparts strength and high temperature creep resistance to the alloy.
About Met3DP
Product Category
HOT SALE
CONTACT US
Any questions? Send us message now! We’ll serve your request with a whole team after receiving your message.
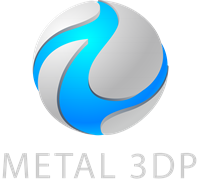
Leading provider of additive manufacturing solutions headquartered in Qingdao, China.
COMPANY
PRODUCT
cONTACT INFO
- Qingdao City, Shandong, China
- info@metal3dp.com
- amy@metal3dp.com
- +86 19116340731