T15 Powder
T15 powder is a tungsten carbide-cobalt cemented carbide powder that provides an exceptional combination of hardness, strength, and toughness. It contains a high percentage of tungsten carbide along with 15% cobalt as the binder phase.
Low MOQ
Provide low minimum order quantity to meet different needs.
OEM & ODM
Provide customized products and design services to meet unique customer needs.
Adequate Stock
Ensure fast order processing and provide reliable and efficient service.
Customer Satisfaction
Provide high quality products with customer satisfaction at the core.
share this product
Table of Contents
Overview of T15 Powder
T15 powder is a tungsten carbide-cobalt cemented carbide powder that provides an exceptional combination of hardness, strength, and toughness. It contains a high percentage of tungsten carbide along with 15% cobalt as the binder phase.
Key properties and advantages of T15 powder:
T15 Powder Properties and Characteristics
Properties | Details |
---|---|
Composition | 85% WC with 15% Co binder |
Density | 13.0-14.5 g/cc |
Particle shape | Rounded, multi-faceted |
Size range | 0.5-15 microns |
Hardness | 88-93 HRA when sintered |
Transverse rupture strength | 550-650 MPa |
The ultrahard tungsten carbide particles held together in a cobalt matrix make T15 ideal for the most extreme wear and abrasion conditions across industrial, mining, and construction sectors.
T15 Powder Composition
Typical composition of T15 cemented carbide powder:
T15 Powder Composition
Component | Weight % |
---|---|
Tungsten carbide (WC) | 84-86% |
Cobalt (Co) | 14-16% |
Carbon (C) | 0.8% max |
Oxygen (O) | 0.5% max |
Iron (Fe) | 0.3% max |
Nickel (Ni) | 0.3% max |
- Tungsten carbide provides extreme hardness and wear resistance
- Cobalt acts as tough and ductile binder holding WC particles together
- Carbon and oxygen present as impurities
- Trace iron, nickel from raw materials
The optimized WC-Co ratio provides the best combination of hardness, fracture toughness and impact strength needed in wearing applications.
T15 Powder Physical Properties
T15 Powder Physical Properties
Property | Values |
---|---|
Density | 13.0-14.5 g/cc |
Melting point | 2870°C (WC) and 1495°C (Co) |
Thermal conductivity | 60-100 W/mK |
Electrical resistivity | 25-35 μΩ-cm |
Coefficient of thermal expansion | 4.5-6.0 x 10^-6 /K |
Maximum service temperature | 500°C in air |
- Very high density enables use in compact, miniaturized components
- Very low CTE reduces thermal stresses and distortion
- Can withstand continuous service up to 500°C
- Good thermal conductivity reduces temperature gradients
These properties make T15 suited for severe abrasion and repeated impact force conditions experienced in mining, drilling, and construction environments.
T15 Powder Mechanical Properties
T15 Powder Mechanical Properties
Property | Values |
---|---|
Hardness | 88-93 HRA |
Transverse rupture strength | 550-650 MPa |
Compressive strength | 5500-6200 MPa |
Fracture toughness | 10-12 MPa.m^1/2 |
Young’s modulus | 550-650 GPa |
Impact strength | 350-900 kJ/m2 |
- Extreme hardness provides wear and abrasion resistance
- Very high compressive strength withstands crushing forces
- Reasonable fracture toughness and impact strength
- Hardness and strength determined by WC particle size and distribution
This exceptional combination of hardness, strength and toughness makes T15 suitable for the most severe impaction, abrasion and gouging wear conditions.
T15 Powder Applications
Typical applications of T15 tungsten carbide-cobalt powder include:
T15 Powder Applications
Industry | Example Uses |
---|---|
Mining | Rock drill bits, grit blasting nozzles |
Construction | Demolition tools, rock crushers |
Manufacturing | Forming dies, metal drawing parts |
Oil and gas | Stabilizers, downhole motors |
General | Cutting and machining tools |
Some specific product uses:
- Percussive rock drilling bits, mine boring tools
- Highly abrasive slurry pump parts like shafts, impellers
- Extrusion dies for brick and ceramic manufacturing
- Wear-resistant components in sandblasting equipment
- Cutting blades, knives, saw teeth needing extreme hardness
T15’s unparalleled hardness and wear performance make it the top choice for equipment used in the most severe impaction-abrasion conditions across industrial sectors.
T15 Powder Specifications
Key specifications for T15 cemented carbide powder:
T15 Powder Standards
Standard | Description |
---|---|
ISO 513 | Classification and application of cemented carbides |
ASTM B276 | Cobalt-tungsten carbide powders and hard metals |
JIS G 4053 | Sintered hard metals |
GB/T 4661-2006 | Chinese standard for cemented carbides |
These define:
- Chemical composition – Co and WC content
- Carbide grain size and powder particle size distribution
- Required mechanical properties
- Acceptable impurities
- Approved production methods like carburization and reduction-diffusion
Meeting these specifications ensures optimal combination of hardness, strength and toughness for maximum wear performance.
T15 Powder Particle Sizes
T15 Powder Particle Size Distribution
Particle Size | Characteristics |
---|---|
0.5-2 microns | Ultrafine grade provides superfinish |
0.5-5 microns | Submicron range enhances toughness |
3-15 microns | Most commonly used size for optimal properties |
- Finer powders increase hardness and finish
- Coarser powders improve fracture strength and impact resistance
- Particle size distribution is optimized based on service conditions
- Both crushed and sintered carbide powders used
Controlling particle size distribution and morphology optimizes final component properties and performance.
T15 Powder Production Method
T15 Powder Production
Method | Details |
---|---|
Carburization and reduction-diffusion | Produces fine spherical powders |
Crushing sintered material | Lower cost, irregular angular particles |
Milling | Ball milling used for particle size reduction |
Spray drying | Granulation and spheroidization process |
Degassing | Removes gaseous impurities |
- Spherical powder morphology provides high packing density
- Crushed powders have lower production cost
- Milling, spray drying used for particle size control
- Degassing optimizes powder purity and sintered microstructure
Automated, high volume production processes result in consistent feedstock optimized for part performance.
T15 Powder Pricing
T15 Powder Pricing
Factor | Impact on Price |
---|---|
Powder grade | Higher purity grades cost more |
Particle size | Ultrafine powder is more expensive |
Order quantity | Price decreases with larger volumes |
Production method | Complex methods increase cost |
Packaging | Special bags or cans increase cost |
Indicative Pricing
- T15 spherical powder: $45-60 per kg
- T15 crushed powder: $35-45 per kg
- Large volume pricing can be 20-30% lower
Pricing depends on powder characteristics, production method, order size, packaging and lead time.
T15 Powder Suppliers
T15 Powder Suppliers
Company | Location |
---|---|
Sandvik | Sweden |
Kennametal | USA |
H.C. Starck | Germany |
Jingdong New Material | China |
Zhuzhou Cemented Carbide Group | China |
Toshiba Materials | Japan |
Selection factors:
- Powder grades and particle morphologies
- Production capacity and lead times
- Technical expertise and customer service
- Sampling, testing and quality control procedures
- Pricing levels and payment terms
- Compliance with international material standards
T15 Powder Handling and Storage
T15 Powder Handling
Recommendation | Reason |
---|---|
Use PPE and ventilation | Prevent exposure to fine particles |
Avoid ignition sources | Powder can combust if overheated in air |
Follow safe protocols | Reduce health and fire hazards |
Use inert atmosphere | Prevent oxidation during powder processing |
Store sealed containers | Prevent contamination or absorption |
Storage Recommendations
- Store in stable containers and ambient temperatures
- Limit exposure to moisture, acids, chlorine
- Avoid cross-contamination from other powders
Proper precautions preserve powder purity and prevent safety issues during handling and storage.
T15 Powder Inspection and Testing
T15 Powder Testing
Test | Details |
---|---|
Chemical analysis | Verifies composition using ICP, EDX, or XRF |
Particle size distribution | Laser diffraction or sedimentation analysis |
Powder morphology | SEM imaging of particle shape |
Apparent density | Measured as per ASTM B212 standard |
Tap density | Density measured after mechanical tapping |
Hall flow rate | Determines powder flowability |
Testing ensures powder meets required chemical composition, particle characteristics, morphology, density specifications, and flowability per relevant standards.
T15 Powder Pros and Cons
Advantages of T15 Powder
- Exceptional hardness, wear resistance, and strength
- Withstands high compression without fracturing
- Good fracture toughness and impact resistance
- Dimensional stability under heavy loads
- Resists deformation at elevated temperatures
- Enables smaller, lighter components
Limitations of T15 Powder
- Difficult to machine after sintering
- Not suitable for dynamic bearing applications
- Relatively brittle behavior
- Oxidation at high temperatures without resistance coatings
- Higher raw material costs than steel powders
- Requires specialized experience for optimal use
Comparison With Tungsten Carbide-Titanium Carbide-Tantalum Carbide
T15 vs WC-TiC-TaC
Parameter | T15 | WC-TiC-TaC |
---|---|---|
Hardness | 88-93 HRA | 92-96 HRA |
Fracture toughness | 10-12 MPa.m^1/2 | 8-9 MPa.m^1/2 |
Strength | Very high | Extremely high |
Cost | Moderate | Very high |
Corrosion resistance | Fair | Excellent |
Applications | General wear parts | Extreme abrasion and corrosion |
- WC-TiC-TaC has slightly higher hardness and strength
- T15 provides significantly better fracture toughness
- WC-TiC-TaC offers excellent corrosion resistance
- T15 is more cost effective
- WC-TiC-TaC for more critical, expensive applications
T15 Powder FAQs
Q: What are the main applications of T15 tungsten carbide cobalt powder?
A: Main applications include mining tools like drill bits, rock crushers, and dredging equipment; construction tools like demolition and pulverizing equipment; dies, drawing parts, extrusion tooling; abrasion resistant components; and general cutting and machining tools.
Q: Why is cobalt used as the binder in tungsten carbide grades?
A: Cobalt provides good corrosion resistance, high strength and toughness, and facilitates liquid phase sintering of the tungsten carbide particles during densification to achieve full density and optimal properties.
Q: What heat treatment is used for T15 tungsten carbide cobalt parts?
A: T15 does not require post-sintering heat treatment. The liquid phase sintering process allows achieving full density and the desired properties during powder consolidation itself.
Q: How is T15 tungsten carbide cobalt powder produced?
A: Main production methods include carburization and reduction-diffusion to make spherical powders or crushing and milling sintered tungsten carbide material into irregular particles. These powders are then blended with cobalt powder in the desired ratio.
About Met3DP
Product Category
HOT SALE
CONTACT US
Any questions? Send us message now! We’ll serve your request with a whole team after receiving your message.
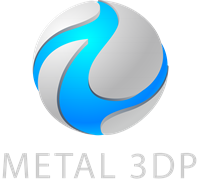
Leading provider of additive manufacturing solutions headquartered in Qingdao, China.
COMPANY
PRODUCT
cONTACT INFO
- Qingdao City, Shandong, China
- info@metal3dp.com
- amy@metal3dp.com
- +86 19116340731